In the fast-paced world we live in, the logistics and supply chain industry has emerged as a core pillar for businesses. Third-party logistics (3PL) providers can streamline your supply chain and increase customer satisfaction, but how do you objectively assess their performance? That’s where 3PL KPIs and metrics come into play.
Monitoring key metrics gives you insights into operational efficiency, and areas of improvement, and ensures that your supply chain continues to run productively. In this guide, we’ll provide an overview of the most crucial KPIs to be aware of, discuss why benchmarking is critical, and we’ll discuss how warehouse tracking systems can help you accurately track and report on metrics.
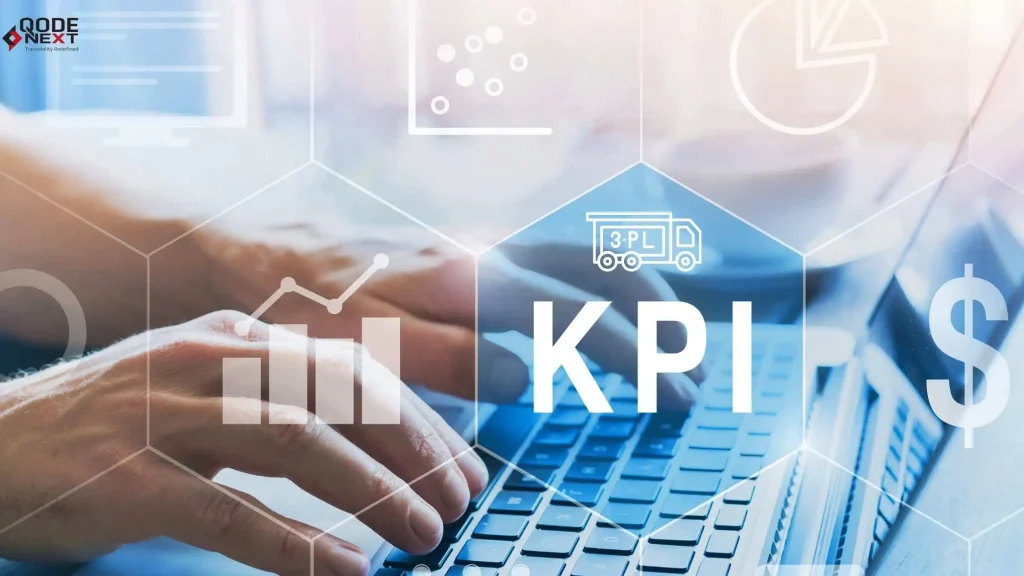
What Are 3PL KPIs?
Key Performance Indicators (KPIs) for 3PL are measurable values that help determine how efficient, reliable , and cost-effective third-party logistics providers are. Such metrics give businesses the information they require to assess how their logistics partners are performing and whether service-level agreements (SLAs) are being fulfilled.
KPIs such as order accuracy rate, on-time delivery rate, and cost per order provide a glimpse of the 3PL provider’s performance. By tracking such metrics, businesses can ensure quality and raise customer satisfaction levels.
Why Are 3PL KPIs Important?
There are multifaceted advantages of tracking 3PL KPIs and metrics:
- Enhanced Efficiency: Recognizing friction points lets you optimize processes and lower expenses.
- Improved Decision-Making: Data-driven insights enable informed decision-making for logistics strategies.
- Customer Satisfaction: By tracking metrics such as on-time delivery, customers can be confident that they receive their orders as promised.
- Cost Control: Key metrics such as cost per order illustrate areas where cash can be conserved.
- Accountability: KPIs hold your 3PL provider accountable for hitting different service-level expectations.
Without tracking these KPIs, companies face the danger of inefficiency, delayed shipments, and unhappy customers.
Top 3PL KPIs to Track
So Line here is a closer look at the most important KPIs you will track while using a 3PL provider:
1. Order Accuracy Rate
This KPI measures how accurately your 3PL fulfills orders without mistakes during picking, packing, or shipping.
- Formula: (Number of Correct Orders / Total No. of Orders Shipped) x 100
- Benchmark: From 98% to 99.9% of industry standards
- Why It Matters: When orders are filled incorrectly, it generates customer complaints, returns, and additional costs to replace the wrong items.
Tips for Improvement:
- Implement Automated Picking Systems
- Inventory audit and order processes regularly.
2. On-Time Delivery Rate
Frequency of deliveries delivered on time.
- Formula: (Orders Delivered On Time / Total Orders Delivered) x 100
- Benchmark: Above 95% is excellent.
- Why It Matters: Late deliveries damage consumer confidence and lead to lost sales.
Tips for Improvement:
- You can use predictive analytics for your delivery scheduling.
- Collaborate with dependable carriers.
3. Inventory Accuracy
Measures how closely your physical inventory aligns with the inventory in your systems.
- Formula: (Correct Inventory Count / Total Inventory Count) x 100
- Benchmark: 95% or above is considered a good accuracy score.
- Why It Matters: Bad accuracy results in stockouts, overstocking and wasted resources.
Tips for Improvement:
- Utilize RFID or barcode systems
- Conduct regular cycle counts.
4. Warehouse Utilization Rate
This metric indicates the utilization of your warehouse space.
- Formula: (Actual Occupied / Total Space) x 100
- Benchmark: Good warehouses utilize 85% of space.
- Why It Matters: 5s organizes the workplace to create more efficient, visually organized workspaces that make the most of available space, resulting in reduced costs, a higher level of cleanliness, and greater operational flow.
Tips for Improvement:
- Restructuring storage layout to minimize the delay in accessibility.
- Optimize warehouse management through WMS.
5. Cost Per Order
Monitors the overall logistics cost per order processed
- Formula: Total 3PL Costs ÷ Total Orders Fulfilled
- Benchmark: Varies by industry but should be decreasing over time.
- Why It Matters: High dollars per order can eat away at profits.
Tips for Improvement:
- Leverage your 3PL provider to get better rates.
- Batch and Ship Products Efficiently
The Importance of Benchmarking 3PL KPIs
Benchmark your metrics against industry standards and identify areas where your supply chain performs poorly. This process is critical for:
- Establish Practical Targets: You can make practical performance goals with the aid of the benchmarks.
- Identifying Weaknesses: Identify where you can improve your performance with 3PL provider
- Competitive advantage: be ahead of the competition through innovation or improving on current industry standards
Key Benchmarks to Consider:
- Order accuracy rate: 99% or higher
- On-Time Delivery Rate: 95% or more
- Inventory Accuracy: 95%-99%
- Cost Per Order: Industry-specific
If the on-time delivery metric for the industry is 95% but your 3PL provider only manages to deliver 90% of orders on-time, it’s another indication that it is time to fix the delays in their process.
The Role of Warehouse Tracking Systems in KPI Monitoring
Essential system to help you track supply chain performance KPIs accurately — Warehouse Tracking System Real-time tracking of inventory, orders, and shipments is not feasible without these systems, which use barcodes, RFID, and IoT devices.
Benefits of A Warehouse Tracking System:
- Enhanced Accuracy: Reduces human mistakes in inventory monitoring.
- Real-Time Visibility: Allows real-time data of inventory levels and status of shipments
- Quickened Decision Making: Alerts and notifications allow you to take immediate action on the issues.
- Cost Efficiency: Cuts process waste and improves effectiveness.
Key Features to Look For:
- Barcode or RFID tracking
- Integration with ERP systems
- Data visualization dashboards that can be customized
- Instant notifications for delays or discrepancies
Increasing Beyond 3PL Metrics: Supply Chain KPIs
Along with 3PL-specific metrics, companies also need to keep an eye on broader supply chain KPIs to get a fuller view of their operational efficiency.
Critical Supply Chain KPIs:
- Customer Order Cycle Time: Measures the time taken from receiving an order to delivery.
- Perfect Order Rate: What percentage of error-free and on-time orders are being delivered?
- Freight Cost Per Unit: Breaks down shipping costs on a per-unit basis for cost-saving opportunities.
- Why These Metrics Matter: These wider KPIs help you understand how your whole supply chain is functioning, not just the performance of your 3PL provider.
Frequently Asked Questions
What is a 3PL KPI?
Third-party logistics KPI is measured to analyze how well a third-party company is performing in efficiency, accuracy, and reliability.
How can I increase my order accuracy rate?
Implement warehouse management systems and barcode scanners to avoid mistakes in picking and packing.
What is a warehouse tracking system then?
A warehouse tracking system is software that tracks and monitors inventory, shipments, and order statuses in real-time while ensuring the insights you get are accurate and actionable.
Why is benchmarking important for 3PL KPIs?
Use benchmarking to evaluate your 3PL provider and compare their performance against industry performance to help you determine weaknesses and set goals for improvement.
What is a good on-time delivery?
This means that generally over 95% of the delivery must be on time; otherwise, customers are not going to receive their orders on time.
Conclusion
Measuring the correct 3PL KPIs and metrics is an absolute necessity for businesses that want to optimize their supply chain operations. Tracking order accuracy, warehouse utilization, and other KPIs helps you gain actionable insights that enable you to optimize operations, cut unnecessary costs, and increase satisfaction levels.
Are you ready to take your supply chain to the next level? Visit Qodenext to Invest in a reliable warehouse tracking system today and start achieving your logistics goals!