Without appropriate strategies, managing an overflow warehouse can be challenging. When businesses grow and consumer demand changes, there is a need for additional warehouse space to accommodate excess inventory, which makes an overflow warehouse setup critical. These venues may go wayward if not effectively managed, resulting in operational ineptitude and inflated expenditure.
This guide will discuss practical solutions for storing and managing an overflow warehouse to maximize your space and help increase efficiency. These tips will help whether you’re experiencing peaks of activity at certain times of the year, in a growing business, or simply moving to a larger space.
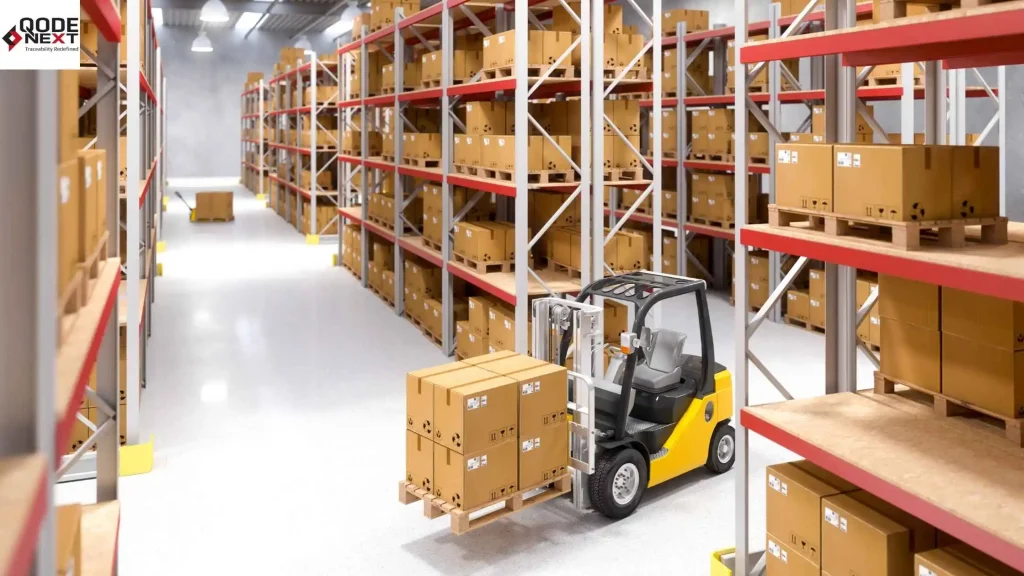
What Is an Overflow Warehouse?
An overflow warehouse is a secondary storage facility that is used when your primary warehouse space is full. It’s a crucial component of a logistics strategy for companies facing excess stock, seasonal inventory, or rapid growth. For many companies, these buildings are makeshift solutions, but they require the same kind of organization and planning as front-line warehouses.
Some of the most important characteristics of these warehouses are:
- Temporary warehousing for surplus products
- Assist with seasonal demands like holiday inventory.
- Flexibility to adapt to the evolving market landscape.
Importance of Efficient Overflow Warehouse Management
The management of these warehouses is essential for the operation’s flow and to decrease costs. Badly managed warehouses cause delays, lost inventory, and increased costs. Here are a few ways that you can organize your overflow facility:
- Stop inventory loss with improved tracking.
- Increased order accuracy and improved customer satisfaction
- Minimize operational costs through better space and process optimization.
Here, we will discuss the best tips to help your overflow warehouse run smoothly and efficiently.
5 Tips to Manage Overflow Warehouses
A clear strategy is needed for an efficiently run overflow warehouse. Here, we’ll present five tactics that can help you optimize storage, enhance operations, and lower costs.
1. Space Optimization Techniques
Optimizing space is imperative in an overflow warehouse. When square footage is limited, you need to get as much use out of every square inch of your facility as possible. Now, for some methods to get better use of the space:
- Vertical Storage Systems: Use tall storage racks to maximize vertical space. Pallet racks, mezzanines, and automated vertical lifts increase storage space astronomically.
- Dynamic Slotting: Organize based on demand Inventory that is in high demand needs to be stored in locations a lot easier to get to, while items that move less can be stored higher and/or further back.
- Maximize Aisle Space: Decrease aisle widths yet compliance safe; allows more convenient storage.
- Modular Storage Solutions: Implement adjustable racks and bins to handle different product sizes.
➤ Pro Tip: A well-organized warehouse layout can increase storage efficiency by 50% and lower the time and labor required for inventory retrieval.
2. Choose the Best Warehouse Location
Where to have your warehouse is a big deal when it comes to how effective it will be for you. Generally, if the location is not well chosen, it leads to increased transportation costs along with delayed delivery. When choosing a location, however, keep these factors in mind:
- Proximity to Distribution Centers: An overflow warehouse located closer to your main facility or distribution centers minimizes transit times and costs.
- Accessibility: Look at both the ease of access by major highways and well-developed transport systems to the warehouse.
- Scalability: Select a place that will grow with you. When there is space available, it is easier to expand operations to satisfy increased demand.
Case Study: A retailer with seasonal demand spikes selected a warehouse site within 10 miles of their primary facility, achieving a 20% decrease in transportation costs during the holiday peak.
3. Developing inventory storage solutions
You also want to know that your overflow warehouse is running well and that inventory is being managed smartly. Here are a few of those solutions, in practice:
- Just-In-Time (JIT) Inventory: Align inventory with demand to minimize overstock. JIT approach reduces storage costs and prevents any stoppage in sales.
- ABC analysis: Classifying inventory according to importance. High-value items (A) should get more attention than low-value items (C). It is a very helpful way to direct storage and retrieval.
- FIFO and LIFO Methods: If applicable to your industry, use FIFO (First In, First Out) or LIFO (Last In, First Out) methods to manage inventory turnover efficiently.
- Digital Inventory Tracking: Choose ERP (Enterprise Resource Planning) or WMS (Warehouse Management System) to receive actual quantities of inventory, which reduces a lot of manual errors and also provides better visibility.
➤Pro Tip: A good WMS can help automate reordering processes so that your overflow warehouse doesn’t become overstocked or under-stocked.
4. Making the Most of Storage Racks
Storage racks play an important role in every warehouse. They don’t just organize inventory, but maximize storage capacity as well. Here’s how to use them to your advantage:
- Pallet Racking: For heavy and bulky items, pallet racking systems allow for easy access and efficient storage.
- Drive-In Racks: Drive-in racks facilitate high-density storage by enabling forklifts to move input directly into inventory and minimizing aisle space.
- Cantilever Racks: Due to their lack of horizontal beams, cantilever racks accommodate irregularly shaped items (such as pipes or furniture).
- Labeling and Categorization: Use clear labels on storage racks to simplify retrieval and reduce mistakes.
5. Using Technology to Become More Productive
So here’s how technology can transform the way you manage your overflow warehouse. Here are several innovations to consider:
- IoT-Enabled Tracking: Implement IoT sensors to keep track of inventory levels and the movement of items across the supply chain.
- Automated pick and pack lines: This will reduce manual labor to a great extent and speed up your operations.
- Data analytics: Use analytics tools to analyze trends, improve workflows, and make decisions based on data.
- Barcode and RFID Systems: Use barcode and RFID systems to streamline inventory tracking and improve accuracy.
Case Study: To illustrate, a company leveraging RFID technology reported a 30% decline in picking errors and a 25% enhancement in order fulfillment times.
Frequently Asked Questions: Overflow Warehouse
Do you have common practices for how to maximize the storage space in an overflow warehouse?
The ideal approach would be the implementation of vertical storage systems, compact aisle designs, and modular solutions to maximize the available space.
How can I determine a site for my overflow warehouse?
Choose a location near distribution centers, transportation hubs, and customer clusters to reduce transit times and costs.
What inventory management systems are ideal for it?
WMS and ERP software are great for making inventory count and optimizing efficiency.
What are affordable storage options?
Some common kinds of low-cost and efficient storage for overflow warehouses are adjustable racks, pallet systems, and vertical lifts.
So how does technology enhance its function?
Automation, IoT devices, and RFID systems improve accuracy, speed, and productivity to decrease operational expenses.
Conclusion
Using an overflow warehouse effectively is a critical necessity for businesses that are growing, have seasonal demand, or need to manage their inventory effectively. A well-designed warehouse will not only avoid hampering your procedures but also enhance your output. Due to the following aspects, you can design your warehouse better. Space Optimization, Location, Smart Inventory Solutions, Storage Racks & Technology.
Ready to enhance your warehouse management? Contact QodeNext today to explore tailored solutions for your business!