Rising warehouse cost jeopardies business operations. They reduce productivity, cause inventory loss, and shrink profit margins. Warehouse management is the pulse of your supply chain and requires a carefully planned strategy to cut unnecessary expenses.
Let’s understand how to reduce logistics costs to make your business competitive and recession-proof.
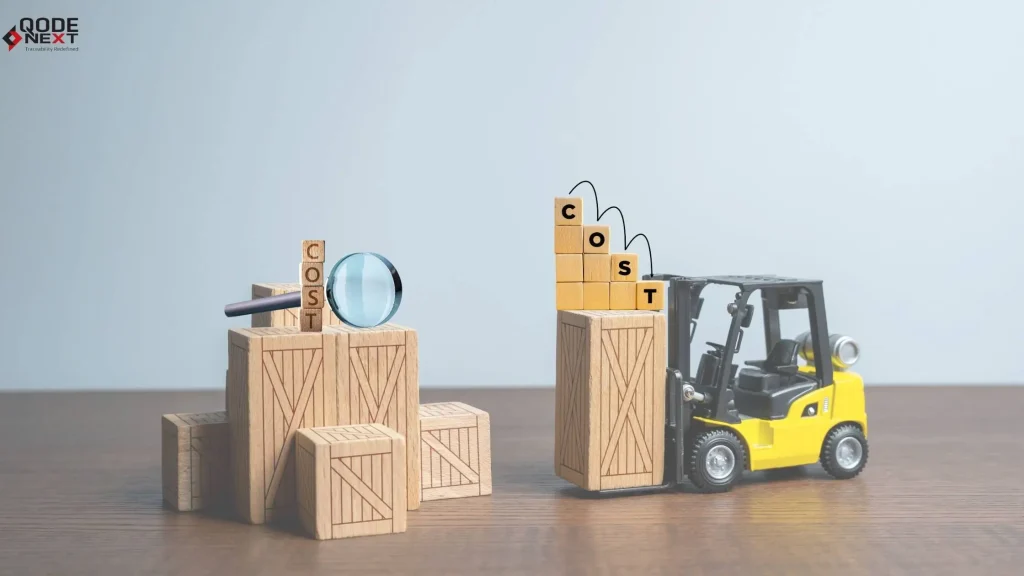
What are Warehouse Cost?
Warehouse costs refer to the expenses incurred in operating and maintaining a warehouse. These costs can include:
- Labor Costs: Salaries, wages, and benefits for employees.
- Storage Costs: Rent, utilities, and maintenance of the facility.
- Inventory Costs: Expenses related to managing and storing goods, such as warehouse insurance cost, depreciation, and obsolescence.
- Operational Costs: Day-to-day expenses like packaging, transportation within the warehouse, and energy consumption.
Effectively managing warehouse cost is vital to ensure the warehouse operates as a profit centre rather than a cost burden.
Features of a Well-Optimised Warehouse
A well-optimised warehouse operates efficiently, minimising costs while maximising productivity. Here are the key features of an optimised warehouse:
- Effective Layout Design: The warehouse layout should be designed for easy flow of goods, with clear areas for receiving, storing, picking, packing, and shipping. Efficient space utilization helps to minimize movement and streamline operations.
- Inventory Management Systems: A robust inventory management system (IMS) ensures that stock levels are accurately tracked in real time, reducing the risk of overstocking or stockouts. Utility costs for a warehouse are tracked in tools like Warehouse Management Systems (WMS) to further streamline operations.
- Automation and Technology Integration: Automated systems like conveyor belts, robotic picking systems, and barcode scanners help reduce manual labor, improve accuracy, and speed up operations. Additionally, real-time data through WMS and IoT (Internet of Things) devices provide better control and insight into warehouse performance.
- Labour Efficiency: Properly trained and well-organised staff are essential for productivity. Streamlining labour processes through training and performance tracking helps maintain high-efficiency levels.
- Safety Standards: A safe warehouse environment ensures fewer accidents, reducing downtime and injury-related costs. Proper signage, clear aisles, and safety training are crucial to reduce cold storage warehouse cost.
10 Strategies to Cut Warehousing Cost
Here are the top 10 ways to optimise your warehouse expenses.
1. Optimize Space Utilization
Space is one of the most expensive aspects of a warehouse. Poor utilization leads to unnecessary expansion or renting of additional facilities. Implement vertical storage systems like mezzanine floors or high racks to maximize cubic space.
Use slotting techniques to group items strategically based on size, weight, and demand.
Optimizing space reduces the need for larger facilities, cutting your overall warehouse cost.
2. Embrace Automation
Automation technologies can streamline operations and reduce labor costs significantly. Use Automated Storage and Retrieval Systems (ASRS) to minimize manual handling. Implement Warehouse Management Systems (WMS) to track inventory efficiently.
Deploy autonomous mobile robots (AMRs) for picking and packing tasks. While initial installation costs might be high, but automation creates substantial cost savings in the long term.
3. Improve Inventory Management
Overstocking and stockouts both contribute to unnecessary expenses. A well-organized inventory management system minimizes these risks. Use demand forecasting to stock items appropriately. Apply absolute inventory techniques to prioritise high-volume items. Conduct regular cycle counts to ensure optimal inventory collection. Efficient inventory management reduces dead weight and obsolescence.
4. Optimise Labor Productivity
Labor is often the largest yet most overlooked portion of warehouse operations. Cross-train employees to perform multiple tasks, increasing flexibility during peak seasons. Implement performance incentives to motivate workers.
Use wearable devices to track and enhance worker efficiency. Balancing labour costs with productivity ensures a more efficient and cost-effective warehouse operation.
5. Reduce Energy Consumption
Energy expenses contribute significantly to warehouse cost. Adopt eco-friendly practices to reduce logistics expenses. Install LED lights which are cost-effective and last longer than traditional bulbs.
Install motion sensors in every corner to track electrical equipment. Optimize HVAC systems to regulate temperatures efficiently. Sustainable energy practices cut costs and enhance your company’s environmental responsibility.
6. Implement Cross-Docking
Cross-docking minimizes the need for storage by transferring incoming goods directly to outbound transportation.
- Use cross-docking for high-demand items to reduce storage time.
- Partner with suppliers and customers to ensure seamless coordination.
- By reducing storage time, cross-docking directly impacts your warehouse cost, making operations leaner and more efficient.
7. Streamline Picking and Packing Processes
Picking and packing inefficiencies can increase labour costs and delay order fulfilment. Use zone or batch-picking methods to streamline warehouse workflows.
Leverage voice picking or handheld scanners to improve accuracy. Standardize packing materials to save time and reduce waste.
Streamlined picking and packing processes enhance overall warehouse productivity and reduce errors.
8. Consolidate Shipments
Consolidating shipments reduces transportation and storage costs.
- Combine smaller containers into larger packs to create optimum space.
- Work with 3PL providers who specialise in consolidated freight.
- Effective shipment consolidation leads to cost savings in storage and transportation, lowering your overall warehouse cost.
9. Use Preventive Maintenance
Unexpected equipment breakdowns can disrupt operations and increase costs. Preventive maintenance ensures equipment is functioning efficiently. Schedule regular checks for forklifts, conveyors, and other machinery. Use maintenance tools to monitor machine health in real-time. Proper maintenance minimises downtime, improving warehouse productivity and cutting operational costs.
10. Adopt Lean Warehousing Practices
Lean warehousing reduces waste in all forms, including time, space, and resources. Eliminate non-essential steps in processes like receiving, storage, and shipping. Apply the 5S methodology (Sort, Set in Order, Shine, Standardize, Sustain) to maintain organization.
Continuously analyse workflows to identify inefficiencies. Lean practices ensure a streamlined operation, significantly reducing your warehouse cost.
FAQs – Warehouse Cost
What are some hidden warehouse costs I should be aware of?
Hidden costs can include excessive overtime pay, energy inefficiencies, inventory shrinkage, and poor space utilisation. Regular audits can help identify and address these issues.
How can technology help reduce warehouse cost?
The cost of setting up a warehouse in India is significant. Technology such as Warehouse Management Systems (WMS), automation tools, and predictive analytics can improve inventory accuracy, reduce manual labour, and streamline workflows, leading to significant cost savings.
How do cross-docking and consolidation impact warehouse costs?
Cross-docking reduces storage costs by minimising the time goods spend in the warehouse, while consolidation cuts transportation expenses by combining shipments. Both strategies lead to leaner operations.
What are the risks of cutting warehouse costs too aggressively?
Over-aggressive cost-cutting can lead to insufficient labour, reduced equipment maintenance, and lower service quality, potentially affecting customer satisfaction and long-term profitability.
How much does it cost to rent a warehouse?
The average warehouse cost per square foot in India is 35-100/month, depending on the location and amenities offered.
What role does training play in reducing warehouse costs?
Properly trained staff are more efficient, make fewer errors, and operate equipment safely. Investing in regular training programs enhances productivity, minimises mistakes, and lowers labour and operational costs.
How can data analytics contribute to reducing warehouse costs?
Data analytics provide actionable insights into inventory trends, labour productivity, and operational bottlenecks. By leveraging these insights, businesses can make informed decisions to optimise processes, reduce waste, and lower warehouse costs.
Conclusion
A warehouse is the backbone of your logistics business. It’s where goods are stored, packed, and shipped for final delivery. Implementing strategies like cross-docking and real-time inventory management ensures your warehouse costs align with your business objectives.
For further assistance on supply chain optimization, contact Qodenext for personalized guidance.