Efficient warehouse management is essential for any business dealing with inventory and order fulfillment. One crucial element in this process is the picking list, a document that helps warehouse staff accurately and efficiently collect the right products for customer orders.
In this guide, we’ll explore what a packing list is, why it matters, the different types, how to create one, best practices, and the challenges businesses face in optimising their picking process.
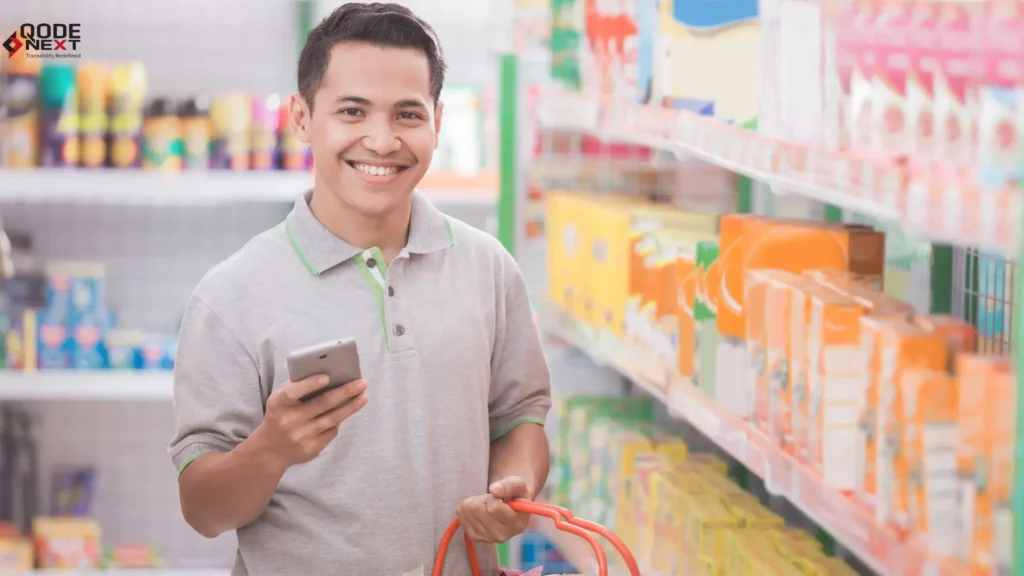
What is a Picking List?
A packing list is a document or digital record used in warehouses and fulfillment centers to guide staff in selecting the correct items for customer orders. It contains essential information such as product names, SKUs, quantities, storage locations, and order details.
The primary purpose of a fulfillment list is to ensure efficiency, accuracy, and speed in the order fulfillment process, reducing errors and improving customer satisfaction.
Why is a Picking List Important?
A well-organised packing list helps businesses in several ways:
- Reduces Picking Errors: Ensures that the right products are selected, minimizing returns and customer complaints.
- Enhances Warehouse Efficiency: Streamlines the movement of workers, reducing unnecessary steps and delays.
- Improves Order Accuracy: Reduces mismatched orders, leading to higher customer trust and satisfaction.
- Saves Time and Labor Costs: Optimizes the picking process, allowing staff to complete more orders in less time.
- Facilitates Inventory Control: Helps track inventory levels and restock items before they run out.
Types of Picking Lists
Different warehouse operations require different order packing lists based on product volume, storage layout, and fulfillment methods. Here are the most common warehouse pick list examples:
1. Single Order Warehouse Picking List
This type of packing list is used for one order at a time. It is ideal for small businesses or warehouses with low order volumes.
- Best For: Small eCommerce businesses and stores with minimal stock.
- Pros: Simple and straightforward, reduces confusion.
- Cons: Can be inefficient for high-volume order fulfillment.
2. Batch Picking List
A batch picking list allows workers to pick multiple orders at the same time, optimizing their movements within the warehouse.
- Best For: Warehouses handling multiple small orders daily. Barcode readers can enhance batch picking. Their working process is effective and fast.
- Pros: Reduces travel time and improves efficiency.
- Cons: Requires proper sorting after picking.
3. Zone Picking List
In this method, the sorting list is divided based on warehouse zones, with workers assigned to specific areas. Each picker gathers products from their designated zone before passing the order along.
- Best For: Large warehouses with complex inventory structures.
- Pros: Increases efficiency and prevents worker congestion.
- Cons: Requires coordination between pickers in different zones.
4. Wave Picking List
Wave picking combines batch and zone picking by organizing orders into waves. It helps optimize picking schedules based on priority orders, shipping deadlines, or inventory availability.
- Best For: High-volume fulfillment centers with tight shipping schedules.
- Pros: Maximizes efficiency and reduces congestion.
- Cons: Requires advanced warehouse management systems (WMS).
How to Create a Picking List
Creating an effective packing list involves structuring it to reduce errors and optimize efficiency. Here’s what should be included:
Essential Elements of a Packing List
- Order Number – A unique identifier for tracking orders.
- Product Name & Description – Clear product details to avoid confusion.
- SKU (Stock Keeping Unit) – A unique product identifier to streamline inventory tracking.
- Quantity – The number of units required per item.
- Warehouse Location – Specifies where the item is stored (aisle, shelf, bin number).
- Priority Status – Identifies urgent or time-sensitive orders.
- Special Instructions – Notes on fragile items, packaging requirements, or other specifics.
Steps to Generate a Picking List
- Receive Customer Orders: Orders are placed via an eCommerce platform or ERP system.
- Sort by Picking Method: Decide whether to use single, batch, zone, or wave picking.
- Optimize Picking Routes: Use a warehouse management system (WMS) to determine the most efficient picking path.
- Print or Digitize the Packing List: Distribute the packing list to warehouse staff via paper or digital devices.
- Pick, Verify, and Pack: Staff picks items, checks for accuracy, and forwards them for packing and shipping.
Best Practices for an Efficient Packing List Process
- Use Barcode Scanning: Reduces human errors and speeds up verification. The working process of barcode readers is highly technical and complex.
- Organise Inventory Logically: Store frequently picked items near packing stations.
- Leverage Technology: A WMS can automate packing list generation and route optimisation.
- Train Warehouse Staff: Proper training ensures accuracy and efficiency.
- Monitor Picking Performance: Track key metrics like error rates and pick times to improve processes.
Challenges in Managing Packing Lists
Even with an efficient order list, businesses face challenges in order fulfillment. Here are some common issues:
1. Picking Errors
Mistakes in selecting items lead to incorrect shipments and customer dissatisfaction. Solution: Implement barcode scanning and double-check orders before shipping.
2. Inefficient Warehouse Layout
A poorly organised warehouse increases picking time. Solution: Optimize inventory placement based on order frequency.
3. Lack of Real-Time Inventory Updates
Outdated inventory data results in picking unavailable items. Solution: Use a WMS for real-time stock updates.
4. High Labor Costs
Manual picking is labor-intensive. Solution: Automate where possible and streamline picking routes.
5. Overstock or Stockouts
Inaccurate picking lists can lead to inventory imbalances. Solution: Implement predictive analytics for demand forecasting.
FAQs – Picking List
What is a packing list used for?
A packing list is used in warehouses to help workers accurately select and retrieve items for customer orders, reducing errors and increasing efficiency.
How does a packing list improve order fulfillment?
By organising products based on SKUs, quantities, and locations, a packing list ensures quick and accurate order picking, reducing delays and mistakes.
What is the difference between a fulfillment list and a packing list?
A packing list is used for retrieving items from storage, while a packing list details what’s included in a shipment and is used for customer reference.
How can I automate my packing list process?
You can use a warehouse management system (WMS) or an ERP system to generate, manage, and optimise packing lists for efficiency.
Can small businesses benefit from a packing list?
Yes! Even small businesses can reduce errors and streamline fulfillment by using a simple packing list for inventory management.
Conclusion
A picking list is an essential tool for improving warehouse efficiency, ensuring accurate order fulfillment, and enhancing customer satisfaction. By choosing the right type, implementing best practices, and leveraging technology, businesses can optimize their picking process and reduce errors.
If you manage an eCommerce store or a large warehouse, investing in an automated order system will help streamline operations and improve your bottom line. Contact Qodenext today for a hassle-free guidance.