Shipping labels are the backbone of efficient logistics.
They serve as navigators, ensuring the smooth movement of packages through intricate global networks. However, even minor mistakes, like incorrect addresses, missing packaging details, or failure to comply with regulations, can create significant disruptions.
These errors not only lead to delays and increased costs but can also jeopardize customer relationships and overall business success.
In this blog, we’ll uncover the most common mistakes made during shipping label preparation, analyze their consequences, and provide actionable solutions to help streamline your shipping process.
By addressing these issues head-on, you can enhance efficiency and keep your customers satisfied.
Let’s dive right in.
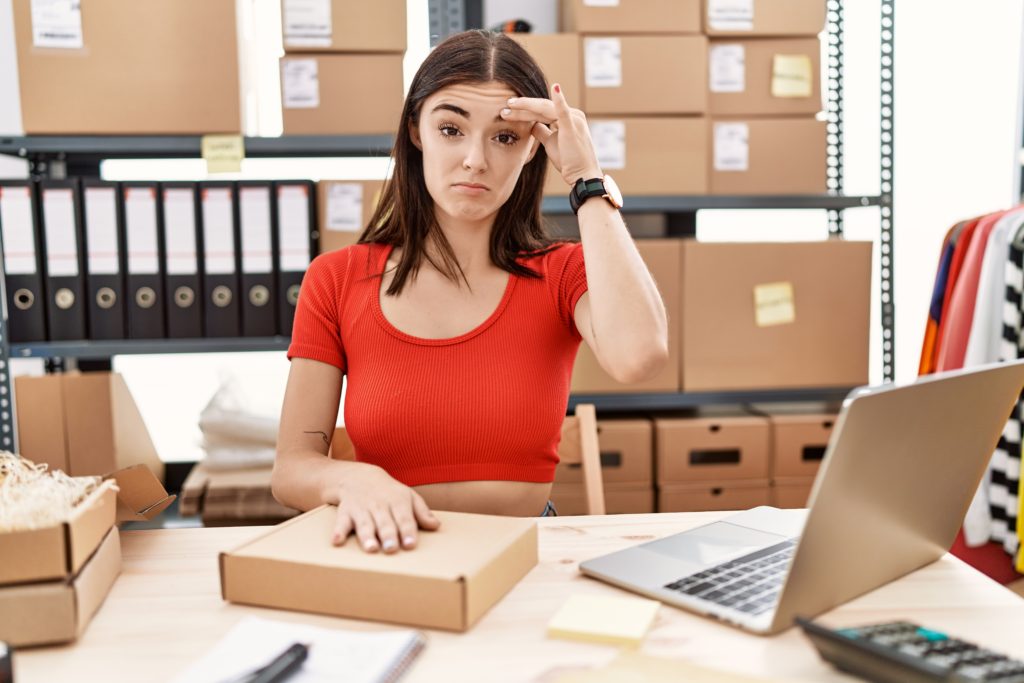
Why Are Having Accurate Shipping Labels Important?
Before we dive into the common mistakes made with shipping labels and how to fix them, let’s first discuss why having accurate shipping labels is so important.
Accurate shipping labels are vital for several key reasons:
1. Streamlined Logistics
- Shipping label stickers include all the necessary information for transporting, handling, and delivering packages.
- When labels are accurate, they help ensure that goods are directed correctly through complex logistics networks, minimizing the chances of delays or misdirection.
2. Regulatory Compliance
- Various industries have specific regulations regarding the shipping of goods, especially for hazardous materials like chemicals, food products, and international trade.
- Accurate labeling is essential to meet these regulations and avoid legal issues or rejected shipments.
3. Cost Efficiency
- Mistakes on shipping labels can lead to extra expenses, such as return shipping fees, costs for resending items, and lost productivity.
- By ensuring labels are accurate, businesses can reduce these financial burdens and ensure shipments reach their intended destinations on the first attempt.
4. Customer Satisfaction
Timely and accurate deliveries are crucial for maintaining customer trust. Errors in shipping labels can result in delays or lost packages, which can significantly impact the overall customer experience.
5. Reduced Risk of Loss and Theft
- Proper labeling includes important details like addresses, tracking codes, and barcodes that help track the shipment’s journey.
- Accurate and comprehensive labels can help lower the chances of packages being lost or stolen during transit.
Top Shipping Label Errors and How to Correct Them
Now, let’s get into the frequent shipping label errors, their effects, and practical ways to resolve them, ensuring a seamless delivery process.
1. Improper Printer Settings or Incorrect Label Size
A common issue arises from using the wrong printer settings or label sizes, leading to misaligned labels or missing key details. Mistakes like these can affect all types of labels, from automatic shipping labels to E Ink shipping labels and RFID shipping labels.
Solutions and Preventative Measures:
- Optimize Printer Settings: Make sure your printer settings match the label type, selecting appropriate modes for thicker or specialty labels.
- Use the Correct Label Size: Confirm the label size required by your shipping carrier to avoid sizing errors that can affect scanning, especially with RFID or E Ink shipping labels.
- Test Before Printing: Run test prints on standard paper to check alignment and size before printing on your actual labels.
By addressing these common issues, you can prevent errors and ensure smoother deliveries with all types of shipping labels.
2. Labels That Fail to Stick Properly
Labels not adhering correctly to packages is a common issue, often caused by factors like poor adhesive quality, unclean surfaces, or using label materials unsuitable for the package. Learning how to stick shipping labels properly is key to avoiding this problem.
When labels come off during transit, the risk of packages becoming lost or undeliverable rises sharply. This can disrupt deliveries and negatively affect customer satisfaction.
Solutions and Preventative Measures:
- Choose High-Quality Labels: Always opt for labels with strong adhesive properties that work well with your packaging material, whether it’s cardboard, plastic, or another surface.
- Prepare the Surface: Before applying the label, make sure the package surface is clean, dry, and free from dust, grease, or debris. A smooth and flat surface ensures maximum adhesion.
- Use the Right Label Material: Select label materials suitable for the package’s surface texture and the conditions it may face during shipping, such as moisture or temperature fluctuations.
By ensuring your shipping labels stick properly, you can reduce the risk of delivery disruptions and enhance customer satisfaction.
3. Incorrect or Misinformation
One of the most common mistakes in shipping labels is omitting essential details or including incorrect information, such as wrong addresses, inaccurate weights, or improper service codes.
These errors can cause packages to be delayed or sent to the wrong destination. In some cases, carriers may also charge extra fees for correcting or rerouting shipments.
Solutions and Preventive Measures:
- Double-Check for Accuracy: Before printing, thoroughly review all details, including addresses, package weight, and any relevant shipping codes or instructions, to avoid errors.
- Use Carrier Address Validation Tools: Many shipping carriers offer tools to verify addresses against postal service databases. These tools can help catch and fix mistakes before the label is printed.
- Follow Correction Procedures: If a label is printed with incorrect or missing information and the package is already in transit, contact the carrier as soon as possible. Most carriers can update shipping details during transit, though it may come with an additional fee.
4. Improper Label Placement
Placing shipping labels on package seams, edges, or uneven surfaces can compromise the label’s readability and durability. This makes it difficult to scan barcodes, which can result in delays or misdelivered shipments.
Solutions and Prevention:
- Optimal Placement: Choose the largest, flattest surface on the package for the label to ensure strong adhesion and easy visibility for scanners.
- Avoid High-Risk Areas: Steer clear of placing labels over seams, edges, or corners, as these spots are prone to damage and can affect the label’s durability.
- Prepare the Surface: Before applying the label, make sure the area is clean, dry, and free of debris to ensure the label sticks securely.
5. Insufficient Packaging for Weather Conditions
Failing to use waterproof or weather-resistant labels for shipments exposed to elements like rain, snow, or humidity can compromise the label’s durability.
Exposure to harsh weather can make labels unreadable, erasing vital shipping details and barcodes. This can hinder tracking and lead to misdeliveries, delays, or lost shipments.
Prevention and Solutions:
- Use Weather-Resistant Labels: Choose labels specifically designed to endure challenging weather conditions. These labels are made from water-repellent and tear-resistant materials, ensuring the information stays intact.
- Evaluate Shipping Conditions: Before shipping, assess whether the package will face exposure to adverse weather. This will help in selecting the right label material for the journey.
- Add Extra Protection: For extreme conditions, use additional protective measures such as plastic sleeves or waterproof packaging to keep the label and the package secure.
6. Issues with Color and Print Quality
Inconsistencies in color and image resolution can affect the uniformity of shipping labels. This not only impacts how the brand is represented but also compromises functional elements like barcode readability.
Prevention and Solutions:
- Utilize Professional Printing Services: For important shipments, especially those that represent your brand to customers, consider using professional label printing software, such as BarTender, or rely on printing services. These options are designed to ensure high color accuracy and quality standards.
- Invest in Quality Printing Equipment: If printing in-house, invest in high-quality thermal printers that excel in color reproduction and can produce clear, high-resolution images. Regular maintenance of these printers is essential for maintaining consistent performance.
- Follow Standardized Color Codes: Use standardized color codes, such as Pantone, for branding elements to achieve uniformity across all printed materials, including shipping labels.
- Conduct Pre-Printing Checks: Before finalizing a batch of prints, perform tests to compare the output with your brand standards. Adjust printer settings as needed to ensure that the colors and resolution on the labels align with your specifications.
FAQs: Common Shipping Label Errors: A Guide to Avoiding Costly Mistakes
Is it possible to reuse a shipping label for another package?
No, a shipping label cannot be reused for a different package. Each label is unique and contains specific information and tracking numbers that are designated for the original shipment.
What should you do if the shipping label is damaged?
If your shipping label is damaged, it’s best to print a new label. Ensure that the new label includes all the necessary information, such as the correct address, tracking number, and barcode, to avoid delivery issues.
What are the consequences of having a missing barcode on a shipping label?
A missing barcode can hinder the tracking of your package, resulting in delays or misdelivery. Always ensure that barcodes are clearly printed and not obstructed by any other information.
How can I track the status of a shipment with a shipping label?
You can track the status of a shipment by using the tracking number provided on the shipping label. Enter this number on the carrier’s website or app to view real-time updates on your package’s location and delivery status.
Conclusion
Creating and using shipping labels is an important part of the logistics and delivery process. It’s crucial to ensure that the information on the labels is accurate, meets international standards, and is produced with good quality to prevent issues that could cause delivery delays, extra costs, or unhappy customers.
By following the strategies discussed for common mistakes, businesses can achieve a smoother delivery process and keep their supply chain running smoothly.
We hope this article has given you helpful insights into improving your shipping label practices to meet your logistics needs effectively.