Running a warehouse is no mean feat. You need to ensure your business is connected to different channels, which requires an organized system of storage, tracking, and warehouse waste management. By increasing value and reducing the time required to perform tasks, companies transform their business operations.
Disposing waste and recycling materials is crucial to keep your warehouse clean and sustainable. This blog will identify the different types of waste in the warehouse, including tips to dispose of your trash responsibly.
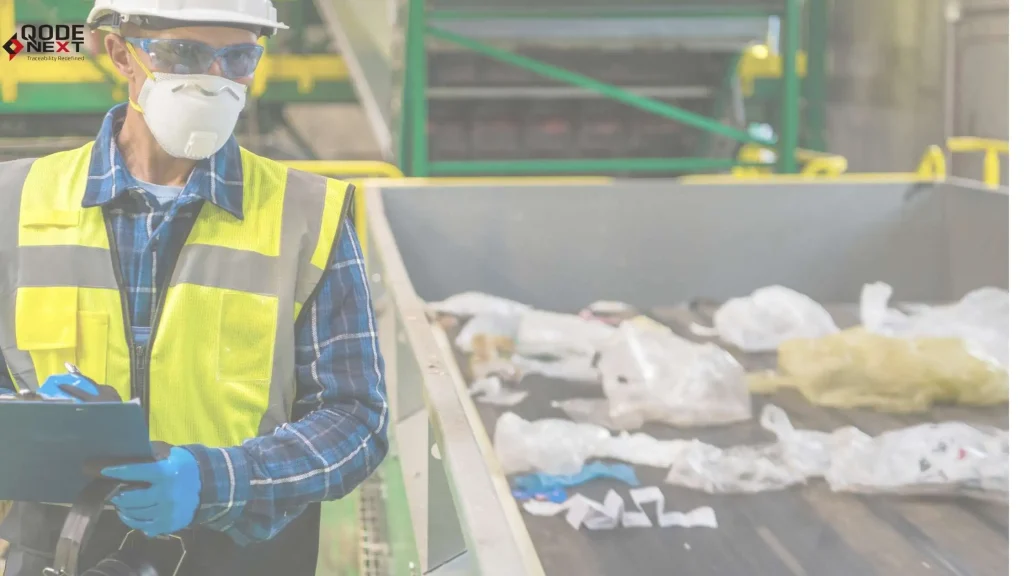
The Importance of Warehouse Waste Management
Managing warehouse waste goes beyond basic trash removal. It involves examining inefficiencies that may go unnoticed but contribute to increased costs, wasted time, and energy.
Companies that successfully implement warehouse waste management plans often see improvements in employee productivity, operational efficiency, and sustainability. Additionally, reduced waste means lower disposal costs and a smaller environmental footprint—an increasingly significant factor in modern business practices.
9 Waste Types and How to Remove Them
Let’s examine the most common waste types in warehouses and the strategies you can use to reduce them effectively.
1. Inventory Waste
Inventory waste occurs when excess or obsolete inventory takes up valuable warehouse space. This can happen due to inaccurate forecasting, over-ordering, or lack of proper stock rotation.
Solution: Adopt Just-in-Time (JIT) inventory practices to maintain optimal stock levels, reducing excess. Regularly conduct warehouse waste management audits to identify and phase out slow-moving items. Leveraging warehouse management systems (WMS) can aid in accurate forecasting and demand planning, minimizing inventory waste.
2. Motion Waste
Motion waste refers to unnecessary movement by employees to perform their tasks, often due to poor layout or inefficient processes.
Solution: Optimize your warehouse layout to reduce motion waste. Place frequently accessed items closer to shipping and receiving areas. Implement pick-to-light systems to direct employees to the items’ exact locations, reducing time spent searching.
3. Transport Waste
Transport waste results from unnecessary movement of goods within the warehouse. Frequent handling and transportation increase the risk of damage, misplaced inventory, and delays.
Solution: Reduce internal transportation by arranging stock zones strategically based on demand frequency. Implement cross-docking practices, where incoming goods are directly transferred to shipping, minimizing internal movement and handling.
4. Overprocessing Waste
Overprocessing waste happens when unnecessary steps are included in processes, such as redundant inspections or extra packaging.
Solution: Standardize and streamline your processes to eliminate extra steps. Assess each stage in the workflow for necessity and remove redundant processes. Using automation, such as automated sorting systems, can ensure efficiency without over-processing.
5. Defect Waste
Managers should include defect errors in warehouse waste management strategies. Processing, labelling, or packaging can lead to wasted resources and time as items need to be reworked or discarded.
Solution: Implement quality control systems at critical points within the workflow. Training employees on proper handling and processing techniques also reduces errors. Regular audits of equipment and systems ensure sustainable supply chain standards.
6. Waiting Waste
Waiting occurs when workers are idle due to delays in other processes or equipment issues. This form of waste disrupts workflow and productivity.
Solution: Coordinate tasks efficiently to reduce downtime. Use predictive maintenance to keep equipment operational and minimize unexpected breakdowns. Ensuring that materials and tools are available when needed prevents idle time.
7. Space Waste
Unused or inefficiently used warehouse space leads to higher operational costs and limits expansion potential.
Solution: Implement vertical storage solutions, such as high-rack shelving or mezzanine floors, to maximize floor space. Regularly review layout plans and reorganize as necessary to ensure space is utilized optimally. Employ a WMS to track available storage capacity and assign it effectively.
8. Energy Waste
Energy waste is often overlooked but can be a significant cost contributor in warehouse operations. Poorly insulated facilities, outdated lighting, or inefficient machinery increase energy usage.
Solution: Conduct an energy audit to identify inefficiencies. Replace old equipment with energy-efficient models, install LED lighting, and implement smart climate control systems. Small adjustments like switching off lights in unoccupied areas or optimizing temperature settings can also reduce waste.
9. Packaging Waste
Warehouses can generate large amounts of packaging waste, especially in facilities with high shipping and receiving volumes. Excessive use of materials increases costs and environmental impact.
Solution: Adopt sustainable packaging practices, such as using reusable or recyclable materials. Assess your packaging standards to eliminate unnecessary material and reduce sizes where possible. Training employees to follow optimized packaging methods ensures consistency.
Next, let’s explore the best practices for waste disposal warehouses.
Best Practices for Warehouse Waste Management
Implementing effective warehouse waste management requires ongoing effort and commitment. Here are some practical tips for long-term success:
- Leverage Data Analytics: Use data analytics to monitor performance and identify waste-prone areas. Regular data reviews allow for continuous improvement in waste management.
- Embrace Automation: Automated systems help reduce human errors, speed up operations, and minimize waste. Consider using robotic solutions for repetitive tasks like picking and sorting.
- Promote a Lean Culture: Encourage a lean mindset among employees. Regular training and awareness programs on waste reduction help create a proactive, lean logistics culture.
- Implement a Continuous Improvement Program: Establish a Kaizen or 5S program that continuously assesses warehouse practices, ensuring a consistent focus on waste reduction.
- Measure and Reward Success: Track waste management goals and reward employees who contribute positively. This can motivate the entire team to adopt best practices in waste reduction.
FAQs – Warehouse Waste Management
What are the most common types of waste in warehouses?
The most common types of waste in warehouses include inventory waste, motion waste, transport waste, overprocessing waste, defect waste, waiting waste, space waste, energy waste, and packaging waste. Addressing these can significantly improve efficiency and reduce costs.
How can I measure waste in my warehouse?
You can measure waste by tracking key performance indicators (KPIs) such as inventory accuracy, order fulfilment time, and defect rates. Regular audits and using warehouse management software also help identify and quantify waste.
How to reduce waste in a warehouse?
Automation can reduce errors, improve process efficiency, and minimize waste. Automated systems like pick-to-light, automated guided vehicles, and robotic sorting reduce the need for manual intervention and streamline workflows.
How does lean methodology apply to warehouse waste management?
Lean methodology focuses on removing waste and optimizing processes. In warehouses, it means eliminating activities that don’t add value, such as excess inventory, unnecessary movements, and over-processing. Implementing lean practices like Kaizen and 5S helps create a culture of continuous improvement.
What role does a WMS play in reducing warehouse waste?
A WMS helps track inventory, manage orders, and optimize space, reducing inventory and motion waste. It offers actionable insights to warehousing staff, helping them make timely decisions to reduce waste.
Why is space management important in warehouse waste management?
Inefficient use of space leads to higher costs and limits warehouse expansion. Effective space management, like using vertical storage and rearranging layouts, maximizes available space, reduces clutter, and improves operational flow.
Is sustainable packaging necessary for reducing warehouse waste?
Sustainable packaging reduces environmental impact and lowers material costs. Using recyclable or reusable materials in packaging decreases waste, promotes sustainability, and often aligns with customer expectations for eco-friendly practices.
Conclusion
Warehouse waste management is difficult due to their enormous scale of operations. Fortunately, implementing the above solutions will ensure your warehouse is efficient and well-maintained. Limit your processes and only use what is necessary to strike a fine balance between quality and efficiency. Need help optimizing your entire supply chain operations? Join forces with Qodenext to solve your supply chain bottlenecks.