Everyone is well aware of the disruptions the COVID-19 pandemic has instigated since Q1 2020. The resiliency of the legacy procedures and systems has been tested to the core, and the operational gaps have been blown open. In all sincerity, the impact on the supply chain is nothing short of being downright dreadful.
But this has also ushered in an overhaul of the supply chain framework. Organisations now seem to be strategically and purposefully investing in enabling redundancy and flexibility – thanks to forward-facing ideologies, proactive methodologies, and an eye to learn.
Undoubtedly, product traceability across the value chain has driven this change. And while it’s the core of optimising the creation and distribution of resources, its value has only recently been magnified.
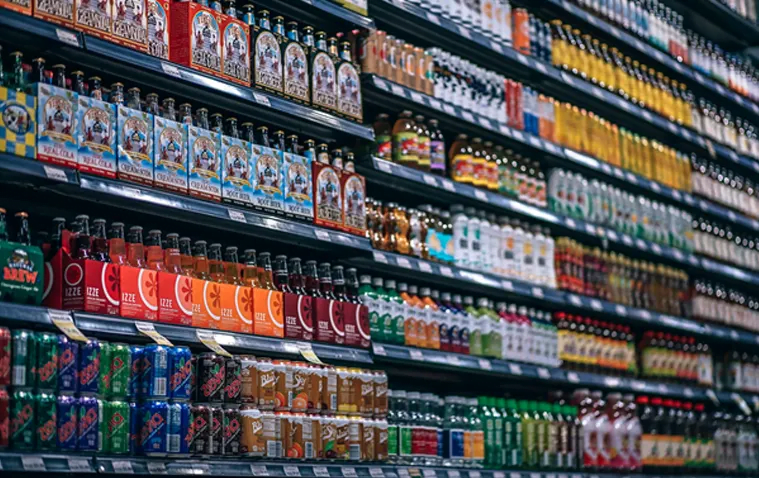
For instance, throughout the pandemic, traceable systems have constrained microbial growth in the FMCG industry. The ability to monitor and identify product temperature and the product source in the first place has prevented the contamination of food products across their sustenance in plants, warehouses, transportation, and retail stores.
Thus, it’s fair to say that traceability is not just limited to plant operations but spans the entire value chain. It makes it easy to put objectivity first and keep the consumers and vendors unassailable by monitoring the product’s viability against standards and regulations.
Starting Off: Traceability in Plants
At the beginning of 2021, Nestlé Prepared Foods recalled “762,615 pounds of pepperoni hot pocket products” due to contamination. The recall was affirmed after determining that glass and plastic had contaminated them.
Such recalls, unsurprisingly, incur wastage and material costs, as well as customer-service expenses, not to mention the hit-to-reputation. And even if the damage is reasonably limited, the repercussions can be widespread, revealing that there is no standard protocol for ensuring the safety of products.
Hence, fostering a proper traceability system at the plant level is worth its weight in gold. This can help identify the source of the contamination/defects, streamline the elimination of waste, and validate the product against the quality standards.
Storing the Products: Traceability in Warehouses
More than 11,000 supply chain disruptions were recorded in 2021 – up from 6192 in 2020. In this wake, companies have been forced to reconfigure their storage facilities to prevent interruption and customer dissatisfaction. But even under ideal conditions, these new warehouse facilities can only stand up for weeks before becoming overcrowded.
This is because there are limited places available for storage. Even if some companies have increased the height of their distribution centres, it’s unlikely that they can accommodate all the same. So, it’s imperative to identify the most appropriate storehouses to invest in.
But more importantly, it’s crucial to have a standardised dispatching method for optimised inventory and intelligent job allocation. Traceability in the warehouses, therefore, takes the form of system-integrated supply chain management. It helps reduce wastage and drive dispatch movement courtesy of insights into replenishment.
Transporting the Products: Traceability in Logistics
Logistics is often plagued with inefficiencies, leading to overextended delivery schedules and retailer dissatisfaction. For instance, the docking stations integral to transporting products are not always up for grabs. It’s disconcerting that retailers are forced to wait for hours/even days as a result.
The situation becomes even more complicated when a load is to be dispatched across multiple stations. The time wasted in waiting and transferring shipments can’t be quantified (remains unbilled). What’s more, it doesn’t help that the freight carriers often take longer than expected to provide shipment confirmation.
So, it’s imperative to identify the best-suited transportation workflows for delivery and the associated loading and replenishment. This entails standardising the transportation process, tracking driver timeliness, implementing intelligent scheduling at docking stations, and reducing documentation headaches — all possible through product traceability at the logistics front.
The Final Assembly Unit: Traceability in Retail Stores
It’s common knowledge that retail stores are as much reliant on a supply chain as vendors and customers. With inconsistent and infrequent shipments, retailers are forced to change their front-end exhibitions and clock substantial expenses. In other words, retail store supply chain complications can inflict a substantial financial burden on an organisation.
The problem compounds when it comes to administering the safety (for let’s say, food items), monitoring compliance, and identifying the source of product variations. In the worst scenario, a faulty product can spoil the reputation of an entire brand.
All these hurdles can be overcome if retailers can precisely track and control their inventory, thus reducing wastage and directing the movement of products to an optimal location. Furthermore, with traceability, they can ensure that the delivered products are devoid of fraudulent alterations and up to par with the quality standards. This also proves beneficial in consumer-facing endeavours, such as marketing, packaging, and advertising.
What Next? Traceability Across the Value Chain
With the growing promise and prominence of traceability solutions and systems, we are seeing a shift from plant-centric monitoring to end-to-end supply chain management. This bodes well with the practices concerning recalls, product audits, and batch compliance.
Hence, the next logical step is to establish a system-level traceability model for each value chain level. This means a more centralised approach to tracking, verifying, and validating the products. And ultimately, it also means a more thorough and transparent process when it comes to managing quality standards and certifications.
No doubt, traceability is a continuous and evolving process. But with the right strategy, you are bound to see long-term benefits in terms of revenue generation, productivity, and responsiveness.
All in all, achieving traceability means reaping a higher appreciation from customers and vendors alike.