
Sometimes business leaders focus more on revenue growth and may overlook the less-obvious costs in their business. One such cost is the inventory carrying cost.
One of the priciest under-the-radar outlays, the inventory carrying costs are expenses that build over the years until the inventory is sold to a new buyer. And we’ll be honest figuring out the inventory carrying cost entirely on your own can sometimes be challenging.
Therefore, in this blog, we will talk all about inventory carrying costs and get into the depts of it to make things easier for you! From discussing its definition to figuring out how to calculate it correctly, we’ve covered most things.
What is Inventory Carrying Cost?
Inventory carrying cost, also known as holding cost, refers to the total expenses a company incurs to store and manage its unsold inventory. These costs are typically expressed as a percentage of the total inventory value and are calculated using the following formula:
Inventory Carrying Cost (%) = (Total Holding Expenses / Total Inventory Value) × 100
On average, inventory carrying costs fall between 20% and 30% of the total inventory value, although this can vary depending on the industry and size of the business.
Why It Matters:
- Strategic Insight: Knowing the carrying cost percentage helps businesses identify areas for improvement, evaluate whether inventory levels are optimized, and adjust processes accordingly.
- Financial Impact: For retailers, inventory and its related costs often make up a large portion of current assets on the balance sheet. Efficient inventory management can directly reduce these expenses.
- Cash Flow Management: Carrying costs tie up capital that could otherwise be used elsewhere in the business. High inventory levels can lead to cash flow constraints and reduce investment flexibility.
- Business Valuation: In public companies, investors and analysts closely track inventory carrying costs. Trends over time, and comparisons with industry peers, can provide insights into operational efficiency and cost control.
10 Components of Inventory Carrying Cost
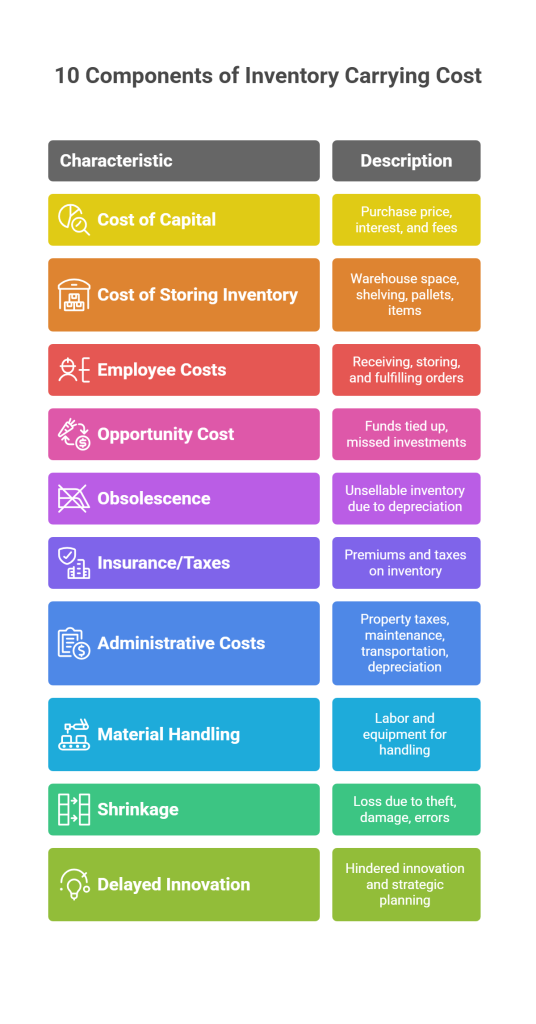
1. Cost of Capital
This encompasses the purchase price of inventory plus any interest or fees if the business borrowed money to acquire it. Tying up capital in inventory can strain cash flow and increase the need for additional capital.
Strategies to reduce this cost include improved forecasting leading to more strategic purchasing and negotiation for lower purchase prices.
2. Cost of Storing Inventory
Warehouse or store space is valuable, with average costs around $6.53 per square foot. Third-party logistics (3PL) providers may charge based on shelving, pallets, or items, making it easier to calculate this expense. Optimizing warehouse layout and storage methods can lower these costs, potentially allowing for downsizing to smaller facilities.
3. Employee Costs
This covers labor expenses related to tasks like receiving, storing, and fulfilling orders. Warehouses can enhance productivity by organizing popular items near packing stations or integrating automation. Experimenting with picking methods and utilizing software for efficient pick paths can mitigate rising labour costs.
4. Opportunity Cost
Overspending on inventory ties up funds that could be invested elsewhere, potentially in more lucrative opportunities. This cost underscores the importance of efficient inventory management to allocate resources effectively.
5. Obsolescence
Inventory that becomes unsellable due to depreciation adds to carrying costs. Minimizing obsolete inventory involves strategies like discounting, donations, or selling to liquidators before it loses all value.
6. Insurance/Taxes
Insurance premiums and taxes increase with higher inventory levels, necessitating careful inventory management to minimize these expenses.
7. Administrative Costs
These include property taxes, maintenance, transportation, and depreciation, which escalate with larger inventory holdings.
8. Material Handling
Labour and equipment costs associated with handling inventory contribute to overall expenses. Reducing the need for machinery or maintenance through streamlined inventory management can lower these costs.
9. Shrinkage
Loss of inventory due to theft, damage, or errors leads to increased expenses. Implementing measures like employee training, vendor communication, and frequent inventory counts can mitigate shrinkage.
10. Delayed Innovation
Excessive focus on managing excess inventory may hinder innovation and strategic planning. Optimizing inventory levels frees up resources for research and development.
Inventory Carrying Cost Formula
Regularly assessing inventory carrying costs is essential for businesses to ensure that holding expenses remain proportionate to inventory value. This analysis helps in identifying when process and practice reevaluation is necessary.
To calculate inventory carrying costs, sum up expenses such as capital, storage, labor, transportation, insurance, taxes, administrative costs, depreciation, obsolescence, and shrinkage over a year. Then, divide this total by the annual inventory value and multiply the result by 100 to obtain a percentage.
Inventory Carrying Costs = (Total Expenses) / (Total Annual Inventory Value) x 100
For a quick estimate of carrying costs, dividing the total annual inventory value by four can provide a rough estimate.
Inventory Carrying Cost Example
As autumn fades, Boutique Treasures finds itself with two brimming warehouses of winter garments, prompting a closer examination of the expenses tied to maintaining such inventory while preparing for the arrival of spring collections.
The breakdown of expenses includes storage costs amounting to ₹10,000, labor expenses totalling ₹2,000, ₹3,000 earmarked for shipping, ₹2,000 allocated for insurance, and an additional ₹1,000 covering shrinkage and depreciation. This totals up to inventory carrying costs of ₹18,000, against an inventory value of ₹75,000.
Using the formula:
Inventory Carrying Costs = (Total Expenses) / (Total Annual Inventory Value) x 100
We calculate:
₹18,000 / ₹75,000 x 100 = 24%
Thus, Boutique Treasures’ inventory carrying costs stand at 24%.
5 Ways to Reduce Inventory Carrying Cost
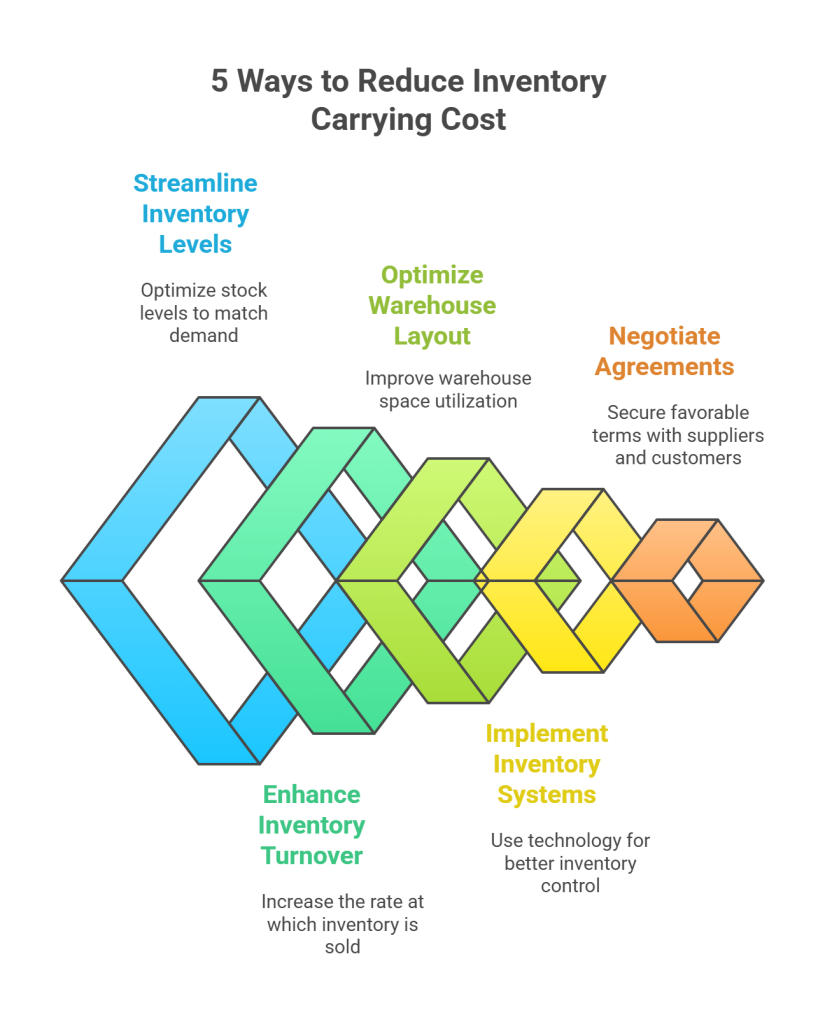
Companies have various strategies at their disposal to trim inventory carrying cost, many of which require minimal time and effort. Here are some smart approaches to spending less on inventory storage:
1. Streamline Inventory Levels
While the just-in-time inventory strategy has faced scrutiny, companies often hold excess stock or inappropriate products. Start by monitoring inventory key performance indicators (KPIs) to assess each SKU’s relevance and quantity requirements. Accurate forecasting coupled with software that triggers reorder alerts can strike an optimal balance, ultimately saving money.
2. Enhance Inventory Turnover
Accelerating the sell-through rate reduces the time items spend on shelves, thus lowering holding costs. Evaluate products monthly to ensure they meet expected turnover rates, adjusting inventory levels accordingly. Effective forecasting mitigates excess inventory risks, while promotions and bundling can help move slow-moving stock.
3. Optimize Warehouse Layout
Redesigning warehouse space can significantly reduce holding costs. Utilize containers for efficient storage, install vertical shelving, or centralize popular items to minimize labor and storage expenses. Such adjustments can also enhance inventory visibility, curbing capital, depreciation, and insurance expenses.
4. Implement Inventory Management Systems
Investing in technology like perpetual inventory systems provides real-time visibility, enabling informed decision-making. Warehouse management systems (WMS) improve fulfillment and shipping efficiency, further reducing costs.
5. Negotiate Agreements
Renegotiating contracts with suppliers and customers can mitigate holding costs. Ensure contracts assign responsibility for risks and costs appropriately. Manufacturers can specify maximum holding times with penalties for exceeding them, while retailers can negotiate terms to avoid unnecessary early possession of seasonal items.
By adopting these strategies, companies can effectively cut down on money going into your inventory, enhancing overall financial efficiency.
Conclusion
As we dive into the nuances of running a successful business, it’s crucial to address the often-overlooked aspect of inventory carrying costs. Here at Qodenext, we understand the challenges that come with managing these expenses.
With our expertise and innovative solutions, we help businesses navigate the complexities of inventory management, ensuring they thrive in today’s competitive landscape.
So, as we explore the intricacies of inventory carrying cost, remember: understanding and managing these expenses effectively can make all the difference in the success of your business.
FAQs: Inventory Carrying Cost: What It Is & How to Calculate It
1. How can I avoid carrying costs?
You can streamline inventory levels, enhance turnover, optimize warehouse layout, implement inventory management systems, and renegotiate agreements with suppliers and customers.
2. What is the general carrying cost of an inventory?
The general money typically ranges between 20% to 30% of the total value. However, this percentage can vary depending on factors such as industry, business size, turnover ratio, and storage requirements.
3. Does higher carrying cost harm the business now?
Yes, higher prices can harm the business by tying up capital, reducing cash flow, increasing storage expenses, and impacting profitability. It can also lead to obsolescence, shrinkage, and decreased competitiveness in the market.
4. What is the inventory carrying cost benchmark?
It varies across industries and businesses. However, it is commonly used as a reference point to evaluate the efficiency of management practices. Typically, businesses aim to keep these within a certain percentage of the total inventory value, with lower percentages indicating more efficient management.
5. Why is inventory carrying cost important for businesses?
It helps businesses understand the true cost of holding inventory and identify opportunities to improve cash flow and operational efficiency.
6. What is a good inventory carrying cost percentage?
While it varies by industry, most businesses aim to keep carrying costs between 20% and 30% of total inventory value.
7. How do carrying costs affect profitability?
Higher carrying costs eat into profit margins by increasing overhead, especially if inventory turnover is low.
8. How often should inventory carrying cost be reviewed?
It’s best to review it quarterly or annually to adjust inventory practices and avoid excess costs.
9. What tools help track inventory carrying costs?
Inventory Management Systems (IMS), ERP software, and warehouse management tools provide real-time insights into inventory levels and associated costs.