Trucks play a crucial role in transporting finished goods and raw materials to and fro. It’s common to witness at least a hundred to thousand trucks in a plant on a normal day. With so many trucks entering and exiting the plant throughout the day, companies have difficulty managing them. A few challenges that truck drivers and companies face at the plant include lack of space to accommodate all the trucks, limited weighbridges, manual paperwork, long waiting hours, and slow traffic movement.
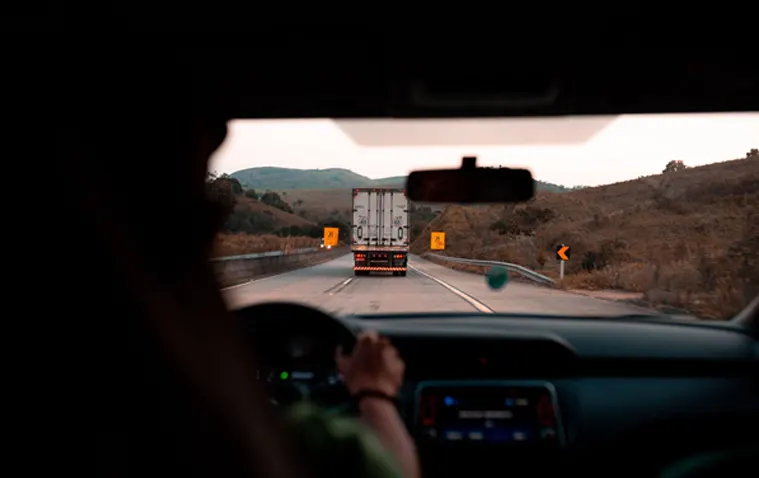
Time is crucial in businesses. Even a minor delay could disrupt the supply-chain process. Companies could incur heavy losses and have to pay for overtime labor and other operational delivery. Streamlined truck management can also help in enhancing the truck driver’s experience within the plant.costs. Modernizing truck management is the only way to avoid additional costs and ensure timely
Let’s look at what companies can do to improve the experience and the entire logistical process.
How to Improve Trucker’s Experience
IoT-enabled situational awareness
Truck drivers are often clueless about the status of their position in the queue or the status of their load. They have to rely on the plant’s staff for information and follow-up with them repeatedly to know the status. Drivers do not get personal time-off as they have to wait in the queue for their turn. One way to address this is through IoT-enabled situational awareness. Take the example of our client’s plant. Almost 200 trucks from different locations enter and exit the plant every day. To streamline the process and enhance the driver’s experience, we implemented an IoT-based situational awareness solution at the plant. The solution included digital signage and automated announcement systems across the plant. The signage displayed the status and the truck’s position in the queue, while the announcement system played automated, personalized messages for truckers and staff based on their location, situation, and process. The real-time automated information deliveries helped the client streamline operations, reduce follow-ups and coordination between the staff and drivers, and gave drivers some respite from waiting in the long queue. Companies can consider using such solutions to manage the plant’s traffic efficiently.
Entry and exit management
According to a survey, 41% of respondents cited manual operations as their biggest concern in yard management. Truck drivers are held up with unnecessary manual paperwork at the entrance and exit, which leads to delays and errors if the information is incorrectly transferred to the system. To improve accuracy and reduce the waiting time, companies can implement RFID antennae at the plant’s entry and exit gates. So, when the truck enters the plant, the staff at the gate will register the driver and truck’s details and provide them with a permanent RFID tag. If the truck is already registered, the staff can validate the details on their system. As the truck moves, the RFID tag is read and logged. Once the loading/unloading is completed, the truck passes through the exit gate, where the RFID antenna reads the tag and logs the truck’s movement. By automating the entry and exit procedures, companies can save the driver’s time, ensure timely delivery, and track the truck’s movement in real-time.
Weighbridge automation
Typically, weighbridges are managed by the plant staff manually. The manual process is time-consuming, inefficient, and could be prone to errors and even malpractices. Busy plants can take more time and lead to traffic. Weighbridge automation can improve the overall process. Weighbridge automation can be integrated with the company’s internal software systems to efficiently manage the data and accounting. The weighing process is directly done under CCTV surveillance. So, there is minimal scope for fake weighing or double weighing of the vehicle and almost zero chances of disputes or misunderstanding. The real-time measurement also removes the need for someone to be physically present to measure. This can help companies save overhead expenses and enable the drivers to save time. It improves the overall transparency in the process.
Bay allocation
The trucks need to be allocated a bay for loading and unloading. However, drivers are often unaware of bay availability due to a lack of visibility. The truck drivers have to wait for long hours to get a free bay. They end up wasting their productive hours. With so many trucks entering the plant, the staff also faces difficulty managing bay allocation and scheduling the truck to report to the designated bay. There’s even more confusion when too many trucks enter at the same time because there’s no visibility on available bays. This issue can be resolved with automated bay allocation. When a truck enters the plant, the entry procedures are completed or validated, and a bay is allocated. When the truck approaches the bay, the RFID antenna monitors the timing and alerts the driver if the truck passes the time limit. This saves the driver’s time and expedites the loading/unloading process.
Conclusion
Trucks help in effectively transporting raw materials and finished goods. As companies expand their footprint to geographies, they need to invest in intelligent systems to streamline the logistics, reduce waiting time, and reduce overhead expenses. They need to ensure that every process – right from the truck’s entry to weighing, bay allocation, and exit is managed efficiently. QodeNext’s TiTo helps companies sequence the events from entry to exit and record consignment information digitally using intelligent tags, IoT-based sensors, weighbridge automation, etc. We have helped some of the best companies to automate their truck management initiatives and improve their ROI. To know more about QodeNext TiTo solution, contact us.