Inventory discrepancy refers to the situation when there is a mismatch between the recorded inventory records and the number of items in your inventory. It usually occurs due to data entry, theft, misplacement, or damage.
Even though such discrepancies are common, they can negatively affect profit. That’s why it’s important to have a system that tracks records and enhances your inventory reconciliation process.
When inventory mismatches occur, you risk order delays, frustrated customers, and lost sales—or costly overstocks that waste money and warehouse space.
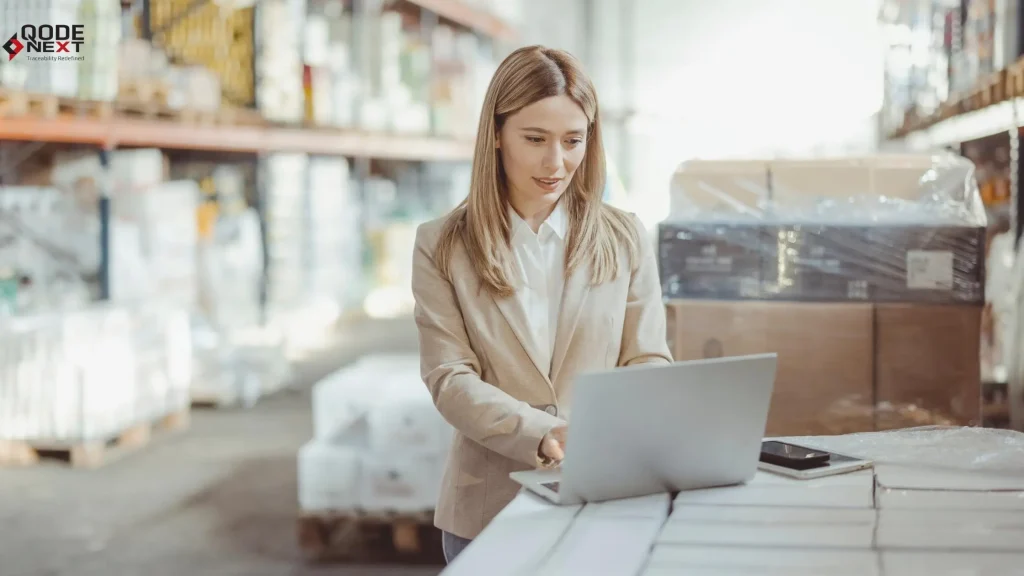
5 Causes of Inventory Discrepancy
Inventory discrepancies are common, but some significant reasons are causing it. When you understand the exact reasons, it gets easier for you to take preventative measures to stop waste and save money. Here are some of the common causes of discrepancies in inventory:
1. Inventory Shrinkage
Inventory Shrinkage is caused by accounting errors, theft, or fraud. To reduce the risk and prevent it, you need to implement loss-prevention tactics. These could include employee training and better warehouse security.
2. Lost Inventory
Human errors can lead to the loss or misplacement of physical inventory. This can occur during the warehouse receiving or fulfilment process.
There are a number of reasons for it- maybe the inventory had the wrong labels, or it was stored in an incorrect location, or maybe because of a mistaken SKU. Sometimes the suppliers can even dispatch the wrong quantity of products.
To prevent inventory discrepancy, establishing a rigorous warehouse receiving process is essential. The warehouse management system can track inventory using barcodes. You can track the item across the supply chain and storage and see if it matches the purchase order as it leaves inventory.
3. Poor Returns Management
Reverse logistics is as important as the initial fulfilment and last-mile delivery processes. If you see a spike in inventory discrepancies, it might be due to poor return management.
Sometimes returned items get damaged in transit or you need to dispose of them. Tracking how returns are handled—whether restocked, donated, or disposed of—significantly reduces inventory discrepancies.
4. Bad or Outdated Technology
For businesses that want to scale quickly, old technologies do more harm than good. So, they need to update the technology they use. Outdated inventory tracking systems mean more manual processes, thus consuming more time.
This is why you need an automated inventory management system which ensures real-time inventory tracking.
5. Poor Training of Employees
If your employees lack proper training on how to receive, store manage, and even track inventory, more discrepancies will occur. Having the right technology in place is crucial, but if your employees are not trained to use it, it will cause more errors and risks.
So, training them is important to ensure straightforward processes and workflows to help employees manage high volumes of inventory.
Now let’s see how to prevent an inventory discrepancy.
Preventing Inventory Discrepancy with 5 Tips
Here are the best practices you must implement. These will improve accuracy and optimise operations for better efficiency and customer satisfaction.
Here’s how ecommerce and 3PLs can reduce inventory loss due to damage:
- Perform regular physical inventory checks to ensure accuracy.
- Use omnichannel inventory systems with real-time updates.
- Streamline procurement to prevent overstocking.
- Analyze sales trends to avoid dead inventory buildup.
- Apply quality controls like barcode scanning and RFID tracking.
- Invest in advanced warehouse management system (WMS) software.
- Train warehouse staff to reduce picking, packing, and shipping errors.
Here are some of the inventory discrepancy investigation practices to implement:
1. Regularly Conduct Inventory Counts
You must have regular inventory counts at intervals. When you conduct these counts, you physically count every item in stock and compare it against what you have in the records.
To make it easier, use inventory software with automatic and real-time updates that can integrate with your sales and shipping systems. In case you find any discrepancies, you can mend them quickly.
You can also do quick routine checks for errors in receiving, picking, packing, or recording inventory. Therefore, it’s best to take corrective actions to ensure greater accuracy.
Maintaining accurate inventory records is important as it reduces the likelihood of stockouts or overstocking, improves order fulfilment accuracy, and thus enhances business continuity. It also prevents revenue loss owing to shrinkage or incorrect inventory levels.
2. Choose Robust Inventory Management Systems
Advanced inventory management software provides many features like real-time inventory tracking, automated replenishment, barcode scanning, and integration with e-commerce platforms and other systems.
Such software helps to reduce discrepancies by giving you accurate and up-to-date stock levels across multiple locations and channels.
With real-time tracking and monitoring inventory movements, identifying differences and reconciling records is easier; barcode scanning, and automated processes streamline operations, thus reducing manual errors and improving data accuracy.
With this software, you can make more data-driven decisions, like demand forecasting and reducing the risk of inventory issues.
3. Strict Quality Control Processes
Rigorous quality control, which instils best practices for receiving incoming shipments, storing, picking, packing, and shipping inventory, and conducting quality inspections while verifying inventory accuracy helps to ensure accurate counts of all incoming inventory. Also, inspecting inventory for damages or defects and recording issues in software for record-keeping is best.
Take corrective actions as you identify the discrepancies immediately. You can initiate investigations, contact the suppliers for resolution, or directly update the inventory records,
Strict receiving and quality control processes can help your team maintain data integrity, upholding several quality service standards. This also minimises the likelihood of shipping defective or incorrect products, improving customer satisfaction and reducing potential returns.
Let’s see another tip to prevent inventory discrepancy.
4. Adopt an Advanced WMS Software
A robust WMS must-have features like barcode scanning, real-time tracking and automated workflows and real-time visibility into stock levels, RFID tracking and storage locations, and visibility into warehouse movements.
Using a WMS for 3PL inventory management helps you better meet your customer expectations with timely order fulfilment. With features like barcode scanning, automated workflows, and detecting anomalies from the point of receiving to shipping, you have better accuracy.
5. Train Your Warehouse Staff
One of the best ways to ensure there is minimal to zero inventory discrepancy is by training your staff. For inventory loss prevention, your staff must know the proper ways to handle inventory, have accurate data entry, and adhere to standard operating procedures that equip them to perform roles efficiently.
It instills a culture of attention to detail and accountability. Thus, it reduces errors in receiving, picking, and shipping processes. Raining your staff can help to maintain high performance standards. This enhances the overall performance and service quality.
FAQs: How to Identify Inventory Discrepancy and 5 Tips to Fix It
How to calculate inventory loss?
Accurate inventory records signify a healthy supply chain. Running regular inventory checks and keeping consistent details about your inventory is crucial if you want to avoid any major inventory discrepancies.
Also, partnering with a 3PL helps you to reduce risk as they take care of the storage and fulfilment process. At the same time, you have full visibility into inventory levels in real-time.
What is an example of inventory discrepancy?
Let’s take an example where you sell sneakers. Your system shows you have 400 units of sneakers in your warehouse that have not been ordered yet by the time the first quarter of the given year ends.
But when you do a physical inventory count, you see you have 375 units of sneakers, not 400. This is what a discrepancy in inventory looks like.
How to reduce discrepancies in your inventory?
Minimise inventory discrepancies by implementing real-time tracking systems, conducting regular audits, training staff on accurate data entry, automating inventory updates, and integrating inventory management software for seamless operations and reporting.
Conclusion
Any inventory discrepancy can significantly impact your profits, operations, and customer satisfaction. To prevent these issues, focus on advanced inventory management solutions, quality control, and staff training.
With the help of Qodenext’s solutions, you can streamline processes, improve accuracy, and reduce errors.