Inventory is a crucial asset for any business that deals with physical goods. However, holding onto inventory comes at a cost—literally. Inventory holding cost is a key metric that businesses need to track to maintain profitability and efficiency.
From warehouse storage to insurance and depreciation, several factors contribute to holding costs. If left unmanaged, these costs can eat into profit margins and affect cash flow. In this blog, we’ll explore what stock holding cost is, how to calculate it, and ways to reduce it effectively.
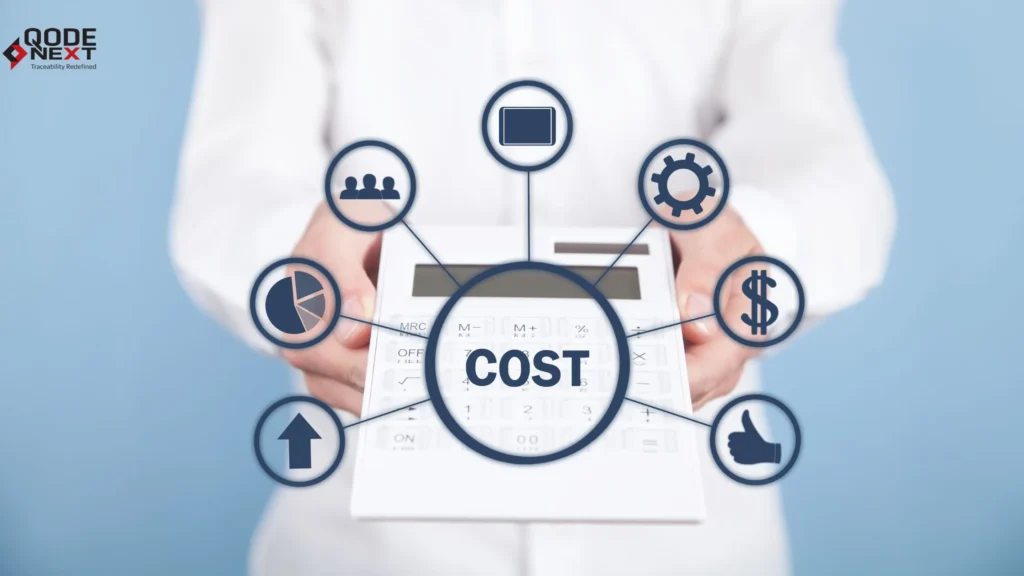
What Is Inventory Holding Cost?
Inventory cost, also known as carrying cost, refers to the expenses incurred to store and maintain unsold inventory. These costs accumulate as long as the inventory remains in stock and can significantly impact a company’s bottom line.
Holding costs typically include:
- Storage Costs – Rent, utilities, and maintenance of warehouse space.
- Depreciation & Obsolescence – The risk of inventory becoming outdated or losing value over time.
- Insurance & Taxes – Expenses for protecting inventory against theft, damage, or legal requirements.
- Capital Costs – The cost of tying up money in inventory rather than investing it elsewhere.
A high inventory holding cost can indicate inefficiencies in supply chain management, leading to increased risks and lower profits.
Inventory Holding Cost Formula
How to calculate inventory holding cost? Don’t worry, we have got your back. Use the following formula:
Annual Inventory Holding Cost Formula = Total Inventory Value × Holding Cost Percentage
Example Calculation
Let’s say a company has an inventory worth 500,000, and its holding cost percentage is 20%.
500,000 × 0.20 = 100,000
This means the company spends 100,000 annually just to hold inventory.
It’s crucial to analyze and optimize stock holding costs to improve financial efficiency.
Types of Inventory Holding Cost
Understanding the key components of warehouse holding cost helps businesses analyze where expenses are accumulating and identify opportunities for cost reduction. Below are the five primary components that contribute to the total holding cost:
1. Storage Costs
Storage costs refer to all expenses related to keeping inventory in a warehouse or distribution center. These costs are unavoidable for businesses dealing with physical goods but can be optimized through efficient warehouse management.
Key storage cost factors include:
- Warehouse Rent or Ownership Costs – Monthly rent or mortgage payments for storage space. Larger warehouses mean higher costs.
- Utilities and Maintenance – Electricity, water, heating, and air conditioning are required for storage facilities. Temperature-sensitive goods require additional expenses for refrigeration or humidity control.
- Security Measures – Surveillance cameras, security personnel, alarm systems, and access controls to prevent theft and unauthorized access.
- Storage Equipment Costs – Shelving units, racks, bins, forklifts, and conveyor belts that facilitate storage and movement.
- Packing and Handling Materials – Costs for pallets, cartons, packaging supplies, and labeling materials to organize and protect inventory.
Impact on Business:
High storage costs reduce profit margins, making it crucial to optimize warehouse space.
Inefficient storage layouts can lead to higher retrieval times, delaying order fulfillment.
Outsourcing to third-party logistics (3PL) providers can help minimize direct storage expenses.
2. Handling & Administrative Costs
This component covers labor costs associated with managing inventory and the administrative expenses of tracking stock movement.
Key handling and administrative cost factors include:
- Labor Costs for Warehouse Staff – Salaries of workers responsible for moving, picking, packing, and managing inventory.
- Inventory Management Software – Expenses related to purchasing, implementing, and maintaining ERP (Enterprise Resource Planning) systems or WMS (Warehouse Management Systems).
- Order Processing and Documentation – Costs of generating invoices, shipping labels, and maintaining records.
- Equipment Maintenance & Repairs – Regular servicing of forklifts, conveyor belts, barcode scanners, and automated storage systems.
Impact on Business:
Inefficient inventory handling can lead to increased misplacement, shrinkage, and damage.
Investing in automation (like RFID, barcode scanning, or AI-driven inventory tracking) can reduce errors and labor costs.
3. Depreciation & Obsolescence
Inventory does not always retain its value. Over time, certain products may lose their usability, relevance, or market demand, leading to depreciation and obsolescence costs.
Key depreciation and obsolescence factors include:
- Product Expiry & Spoilage – Perishable items (such as food, medicine, and cosmetics) have a shelf life, requiring timely sales to prevent waste.
- Technological Obsolescence – Electronics, fashion, and tech-related products quickly become outdated as new models enter the market.
- Seasonal Inventory Risks – Holiday-themed products, fashion trends, or limited-edition items may lose demand after a specific time.
- Inventory Deterioration – Physical degradation due to environmental factors like moisture, dust, or improper storage conditions.
Impact on Business:
- Holding inventory for too long increases the risk of obsolescence.
- Companies may have to offer deep discounts or scrap unsellable products, leading to revenue loss.
- FIFO (First-In, First-Out) inventory management helps reduce the impact of depreciation by ensuring older stock is sold first.
4. Insurance & Taxes
Businesses must insure their inventory to protect against risks such as fire, theft, natural disasters, and accidental damage. Additionally, tax liabilities on stored goods contribute to inventory holding cost.
Key insurance and tax cost factors include:
- Warehouse & Inventory Insurance – Policies covering inventory losses due to fire, floods, or theft.
- Liability Insurance – Protects businesses in case stored goods cause harm (e.g., defective products leading to legal claims).
- Property Taxes – Businesses with large warehouses may need to pay government-imposed property taxes on storage facilities.
- Customs Duties & Import Taxes – Companies dealing with imported goods must account for international trade-related tax obligations.
Impact on Business:
- Higher inventory levels increase insurance premiums since they represent a greater financial risk.
- Proper tax planning and utilizing tax exemptions can help reduce inventory holding costs.
- Storing inventory in tax-friendly locations or outsourcing storage to 3PLs can minimize direct tax burdens.
5. Opportunity Cost
Opportunity cost refers to the potential return a business loses by tying up capital in inventory rather than investing it in more productive areas like marketing, R&D, or new technology.
Key opportunity cost factors include:
- Tied-Up Working Capital – Funds locked in unsold inventory could have been used for business expansion or investments that yield higher returns.
- Missed Investment Opportunities – Companies may miss out on high-yield investment avenues due to blocked liquidity.
- Delayed Business Growth – Holding excess stock can prevent funding for new product development or market entry.
- Cash Flow Constraints – Large amounts of capital tied to inventory can affect short-term operational cash needs.
- Reduced ROI (Return on Investment) – Inventory that sits idle lowers overall returns on invested capital.
Impact on Business:
- Improving inventory turnover reduces financial drag and enhances growth potential.
- Limits flexibility to respond to market changes or invest in innovation.
- Negatively impacts profitability by lowering return on capital employed (ROCE).
- Encourages inefficient capital allocation if inventory turnover is low.
- Businesses with high opportunity costs may struggle to scale efficiently.
How to Reduce Inventory Holding Cost?
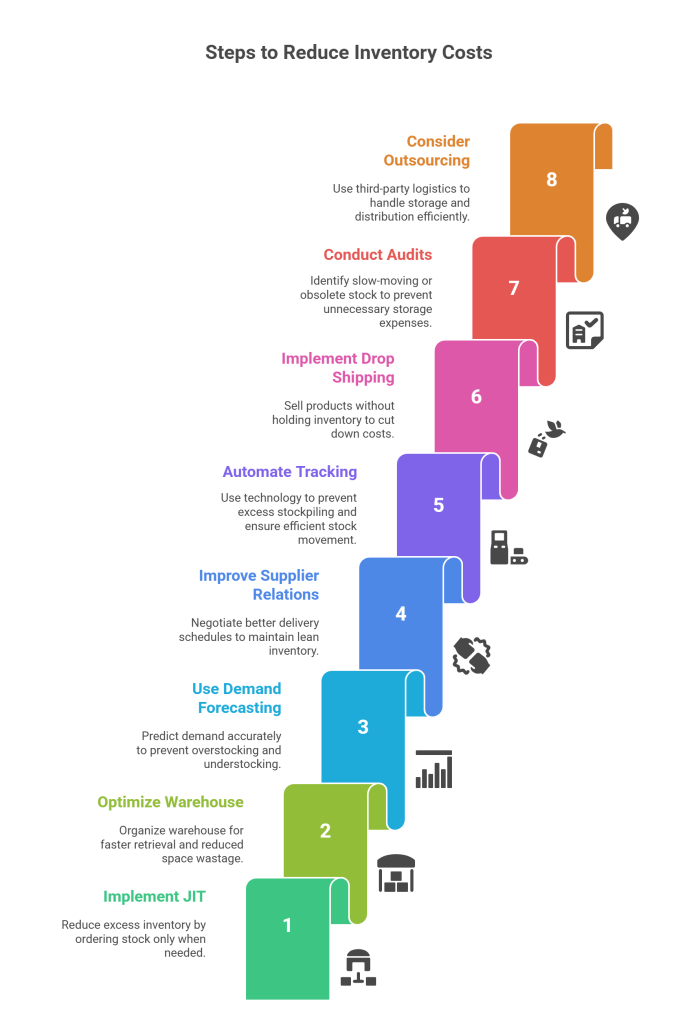
1. Implement Just-in-Time (JIT) Inventory Management
JIT reduces excess inventory by ordering stock only when needed, minimizing inventory holding cost while improving cash flow.
2. Optimize Warehouse Layout & Storage
A well-organized warehouse ensures:
- Faster retrieval times
- Reduced space wastage
- Lower handling expenses
3. Use Demand Forecasting
Accurate demand predictions prevent overstocking and understocking, reducing inventory holding cost.
4. Improve Supplier Relationships
Negotiating better delivery schedules with suppliers can help maintain lean inventory levels.
5. Automate Inventory Tracking
Using RFID, barcode scanners, and AI-powered software prevents excess stockpiling and ensures efficient stock movement.
6. Implement Drop Shipping
Drop shipping allows businesses to sell products without holding inventory, drastically cutting down inventory-holding costs.
7. Conduct Regular Inventory Audits
Frequent audits identify slow-moving or obsolete stock, preventing unnecessary storage expenses.
8. Consider Outsourcing Storage
Third-party logistics (3PL) providers can reduce warehouse costs by handling storage and distribution more efficiently.
Why Inventory Holding Cost Matters for Businesses?
- Direct Impact on Profit Margins – Higher holding costs reduce net profit.
- Cash Flow Management – Tied-up capital affects investment opportunities.
- Competitive Advantage – Lower holding costs mean more competitive pricing and better financial stability.
- Risk Reduction – Reducing storage time minimizes losses due to damage, spoilage, or obsolescence.
By controlling holding costs, businesses can increase profitability, enhance efficiency, and maintain a competitive edge in the market.
Conclusion
Understanding and managing inventory holding cost is crucial for businesses aiming to optimize efficiency and profitability. By implementing smart inventory management practices, automating tracking, and reducing excess stock, businesses can lower holding costs, improve cash flow, and stay competitive.
If you’re looking for advanced inventory solutions, Qodenext offers cutting-edge automation and traceability technologies to help businesses manage their supply chains efficiently.
FAQs – Inventory Holding Cost
1. What is the ideal inventory carrying cost percentage?
The ideal inventory cost percentage varies by industry but typically ranges between 15% and 30% of the total inventory value.
2. How does high holding cost affect a business?
High holding costs reduce cash flow, increase risks of obsolescence and lower overall profitability
3. Can automation help reduce holding costs?
Yes! AI-driven inventory management and barcode scanning reduce manual errors, improve tracking, and optimize stock levels.
4. How can businesses track their warehouse holding costs?
Using ERP systems, inventory management software, and regular audits helps track and optimize inventory holding costs effectively.
5. What is the difference between stock holding cost and ordering cost?
Stock holding cost is the expense of storing unsold inventory. Ordering cost is the expense incurred every time a business places an order (e.g., supplier fees, shipping costs).
6. How does high inventory holding cost impact profitability?
High holding costs reduce profit margins by increasing the cost per unit. They also tie up capital that could be used for growth initiatives, marketing, or technology investments.
7. How does depreciation affect inventory holding cost?
Depreciation occurs when inventory loses value over time, especially for perishable or fast-moving consumer goods. If not sold on time, this leads to markdowns, waste, or write-offs, thereby increasing holding costs.
8. Can automation reduce inventory holding cost?
Yes. Automation tools like RFID, barcode scanners, and AI-based inventory software minimize human error, improve stock visibility, and streamline warehouse operations—resulting in lower holding and labor costs.
9. What is the difference between inventory holding cost and ordering cost?
Inventory holding cost refers to expenses related to storing products. Ordering cost, on the other hand, includes the cost of placing and receiving stock—such as vendor fees, freight charges, and administrative processing.
10. Why is opportunity cost considered part of inventory holding cost?
Opportunity cost reflects the lost potential return on capital that is tied up in inventory. For example, if ₹1,000,000 is locked in inventory, that amount cannot be invested in more profitable areas like marketing, R&D, or expansion.