Imagine waking up to your manager rushing to you, complaining about insufficient raw materials or finished products in your inventory. This would be your worst nightmare, right? Did you just realize that inventory is your business’s most important and largest asset? This nightmare wouldn’t have pathed into your business if you focused better on inventory management. That’s why FIFO full form -First in First out inventory management is very important.
Well, you’re not the only one ignoring the importance of inventory management. But how do you manage your inventory? Which inventory management method do you use? You must have heard of the term “First Come, First Serve.” An inventory management method known as First In First Out (FIFO) is similar to that. Do you wish to explore more about FIFO?

What Is First In First Out (FIFO)?
First In, First Out (FIFO) is an inventory management method wherein the products are dispatched from the inventory based on their date of entry into the inventory. This means that the goods which arrive first in the inventory also leave the inventory first and vice versa.
Besides the inventory management method, it’s also used to value a business’s inventory. In inventory management, FIFO ensures that the products are dispatched fresh, reducing their chances of getting wasted or expired in the inventory.
It’s mostly used in industries with products that come with short shelf life, such as food and beverages, pharmaceuticals, electronics, cosmetics, and apparel.
Not just this, it’s also ideal for businesses which have a periodic inventory system wherein the stocks are counted physically at the end of each period. It’s also useful for businesses that deal with international clients. It’s because it’s one of the few accepted and approved methods under International Financial Accounting Standards (IFRS).
It’s not ideal for industries and businesses which sell large ticket items or items with fluctuating prices. Amongst all the other inventory management methods, it’s the simplest one, which is more product-oriented than customer-oriented.
How Does FIFO Work?
The basic principle of the First In First Out (FIFO) inventory system is to sell or use the oldest items before restocking the new ones to replace them. To ensure this, the oldest items are placed in the front face of the inventory, leaving the backspace for the new incoming inventory items.
For businesses using the FIFO inventory management system, it’s highly essential to have a record of the inventory items based on their entry and exit dates. This facilitates the entire process, thus reducing the chances of discrepancies.
While small businesses with limited products in the inventory can do this record-keeping manually, medium and large-scale businesses may go for inventory or warehouse management software. These software automate the entire record-keeping process and provide real-time data and statistics as needed. Some of these software also come with built-in features that help you analyze the inventory inflow and outflow, thus providing valuable insights.
Advantages Of FIFO
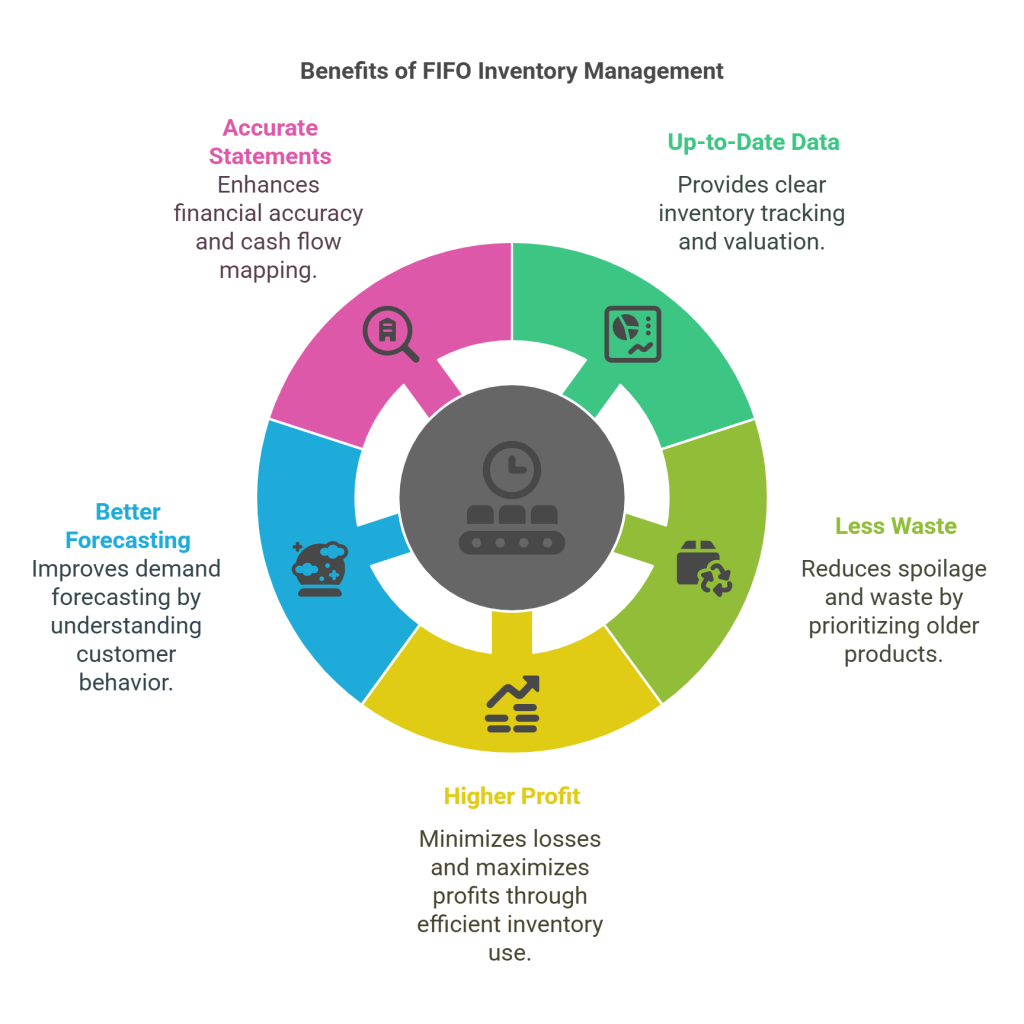
What advantages does the FIFO inventory management system bring to your business? Read on to explore!
1. Up-to-Date Inventory Data
With the FIFO inventory management system, you’ll always have a clear picture of all your inventory along with their entry, expiration and exit dates. Moreover, you can also easily track your products and their location in the supply chain. As an inventory valuation method, it provides the most accurate analysis of a business’s inventory value.
2. Less Waste Production
The First In First Out (FIFO) inventory management system ensures that the oldest products are used up or sold first compared to newer ones. This reduces the chances of expired products in the inventory itself, thus preventing spoilage and reducing waste production.
3. Higher Profit
In the FIFO inventory management method, managers can keep their COGS low. Moreover, it reduces the chances of inventory spoilage and obsolete items in the supply chain, thus minimizing losses and maximizing profits.
4. Better Demand Forecasting
In the FIFO system, you are always aware of the number of products in your inventory and their expiration dates. This way, you don’t end up overstocking products. You can restock the products anytime you want and are always ready to meet the consumer’s demand on time. It also helps you understand and analyze the customer behavior towards your products, thus lesson to better demand to forecast.
5. Accurate Financial Statements
You would be surprised to know that the First In First Out (FIFO) inventory management system is one of the most efficient ways to accurately map a company’s finances and cash flow. Right from inventory to other core areas, you can have a truer picture of costs associated with various segments of your business.
Do you want to integrate advanced business solutions into your business? Worry not because we bring you QodeNEXT and its unique solutions tailored to meet your unique needs. It has a comprehensive suite of hardware and software solutions which will take your business’s productivity and efficiency to the next level. Go check out QodeNEXT’s services now!
Disadvantages Of FIFO
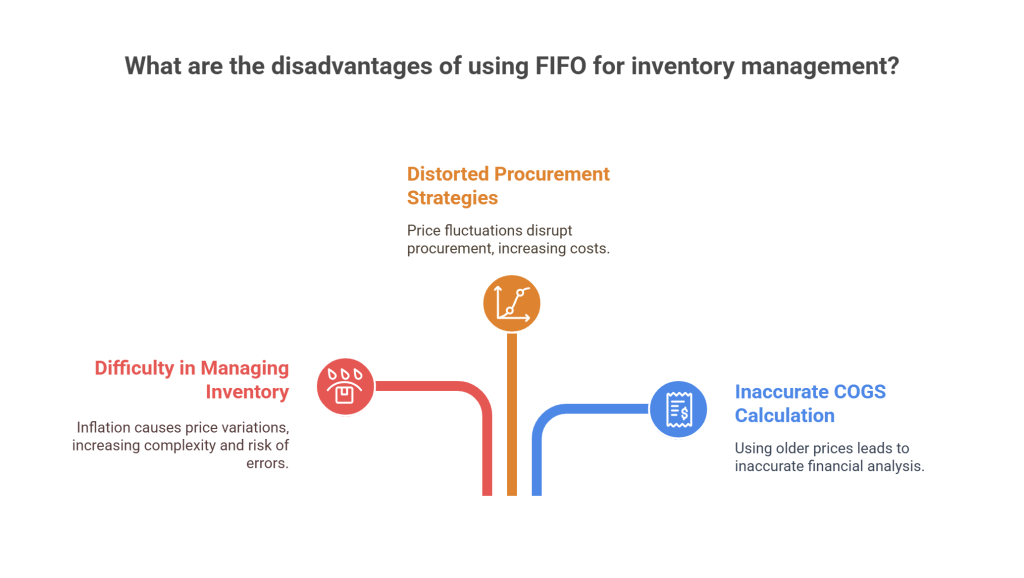
Just like a coin has 3 sides, this inventory management system also comes with some disadvantages. Let’s look into them one by one.
1. Difficulty in Managing Inventory
With the rising inflation rates, it’s quite common to have inventory batches of the same product with slight variations in prices. This makes the entire inventory management quite complex. Moreover, it also increases the risks of human errors.
2. Distorted Procurement Strategies
Imagine you purchased a bunch of inventory at a specific price. Suddenly, the prices of the products spike up or fall significantly. Wouldn’t this screw up the entire inventory management? This will force the team to adjust procurement processes by spreading purchases over time. They would have to increase the total ordering costs to mitigate the impact of outdated cost data.
3. Inaccurate Cost of Goods Sold (COGS) Calculation
FIFO has this thing where it calculates COGS based on older inventory prices. That might seem like no big deal, but imagine this: it’s like trying to figure out how much you spent on groceries last month by using prices from last year’s grocery store receipts. It’s not going to give you the clearest picture of what’s really going on right now in your wallet, right? The same happens with FIFO, which can lead to distorted financial analysis.
How Can You Implement a FIFO Inventory Management System in Your Business?
With many other inventory management systems available in the market, such as Last In, First Out (LIFO), we recommend you go for the FIFO full form- first in first out inventory management. It aligns with the special international standards and is ideal for most products, including the time-sensitive and perishable ones.
If you’re looking forward to implementing a FIFO inventory management system in your business, here are some strategies to simplify the process for you:
- Organize your entire inventory right from the SKU using various labels such as expiration date etc. This improves the traceability and visibility of your inventories, thus making it easier for pickers to pick them and reducing the number of misplaced, lost, or out-of-date products.
- Go for gravity carton flow racks that ensure fresh items are picked from the rear. With these cartons, you can pick products even while you’re restocking.
- Don’t forget to include sequencing in the process. This fastens up the process by categorizing and arranging the items before they’re taken for production.
Conclusion
In addition to FIFO full form – first in first out inventory management You’ll find a bunch of other inventory management methods for your business. However, you should take time to evaluate their features, advantages, and disadvantages before settling on the best one suited for your business needs. You may also take help from experts in choosing the best system.
If you need any help or assistance, check out our indispensable solution, QodeNEXT. Please feel free to contact us now to help you make the best choice to manage your fleet and optimize your process!
FAQs: FIFO Full Form
1. What is FIFO?
FIFO full form is an inventory management method wherein the products are dispatched from the inventory based on their date of entry into the inventory.
2. What’s the basic principle of FIFO?
The basic principle of the First In First Out (FIFO) inventory system is to sell or use the oldest items before restocking the new ones to replace them.
3. What are the advantages of FIFO?
FIFO provides real-time inventory data, helps reduce waste by ensuring older stock is used first, and improves overall inventory management, leading to higher profitability. It also supports accurate financial reporting and better demand forecasting.
4. What are the disadvantages of FIFO?
FIFO can be challenging to manage in large-scale operations, may lead to skewed procurement decisions, and often results in less accurate cost of goods sold during inflation. This can make costing and pricing decisions less reliable.
5. Which inventory management method should you use?
We would recommend you go for the First In, First Out (FIFO). It not just aligns with the special international standards but is also ideal for most products, including the time-sensitive and perishable ones.
6. Is FIFO suitable for all types of businesses?
FIFO is best suited for businesses dealing with perishable or time-sensitive goods such as food, cosmetics, and pharmaceuticals. However, it may not be ideal for businesses dealing with large-ticket or non-perishable items where prices fluctuate significantly.
7. How is FIFO different from LIFO?
FIFO (First In, First Out) dispatches the oldest inventory items first, whereas LIFO (Last In, First Out) dispatches the most recently added items first. FIFO provides better inventory freshness, while LIFO may result in lower tax liabilities during inflation.
8. Does FIFO help in maintaining compliance with accounting standards?
Yes, FIFO is widely accepted under International Financial Reporting Standards (IFRS) and is often preferred by auditors and financial analysts for its transparency and consistency in valuing inventory.
9. Can FIFO be implemented manually or is software required?
Small businesses with limited inventory can implement FIFO manually using clear labeling and stock rotation. However, for medium and large-scale businesses, using inventory management software or WMS is highly recommended for accuracy, real-time tracking, and efficiency.