Because of the current crises, freezer warehouse operators must find new ways to do things, as old methods won’t work anymore. They face challenges like high energy bills, a lack of skilled workers, and the need to use space well for future growth.
To address these problems, companies should consider using semi- or fully-automated systems for storage and shipping. This can help reduce energy costs and lessen the need for skilled workers. Additionally, investing in new technology can also make operations more efficient and easier.
Factors like utility costs, labor expenses, and government regulations regarding handling perishable goods can greatly affect profits and make running the business more complex. This article discusses the common challenges faced by cold storage warehouse and suggests simple solutions to overcome them.
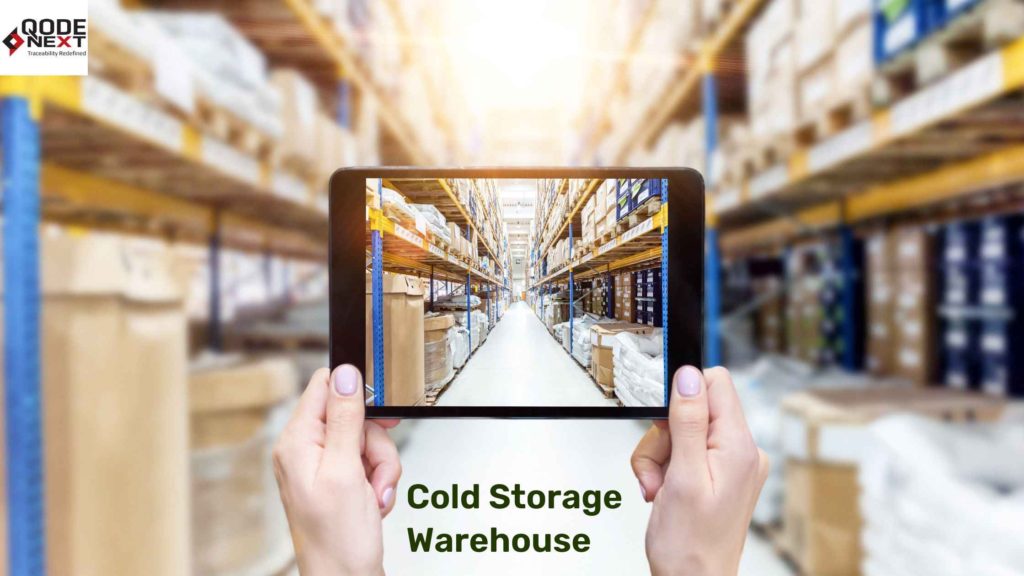
What is a Cold Storage Warehouse?
Cold storage warehouses maintain low temperatures using HVAC cooling systems and insulation. While insulation helps reduce heat transfer, similar to how it works in homes, the cooling process is more complex.
The process involves a coolant that circulates through pipes and components, alongside compressors, condensers, receivers, separators, and evaporators. The coolant, usually made from anhydrous ammonia, moves through the system, where the compressor increases its pressure and temperature.
Next, condenser then removes heat from the coolant, turning it from gas to liquid. The receiver stores this high-pressure liquid and regulates the system’s pressure, while the separator adjusts the coolant flow before it reaches the evaporator.
Finally, the evaporator brings cold air into the warehouse, cooling the space and preserving the stored goods. This continuous cycle keeps temperatures between -122.8°F and 70°F, depending on the business’s needs.
6 Challenges Faced by Cold Storage Warehouses
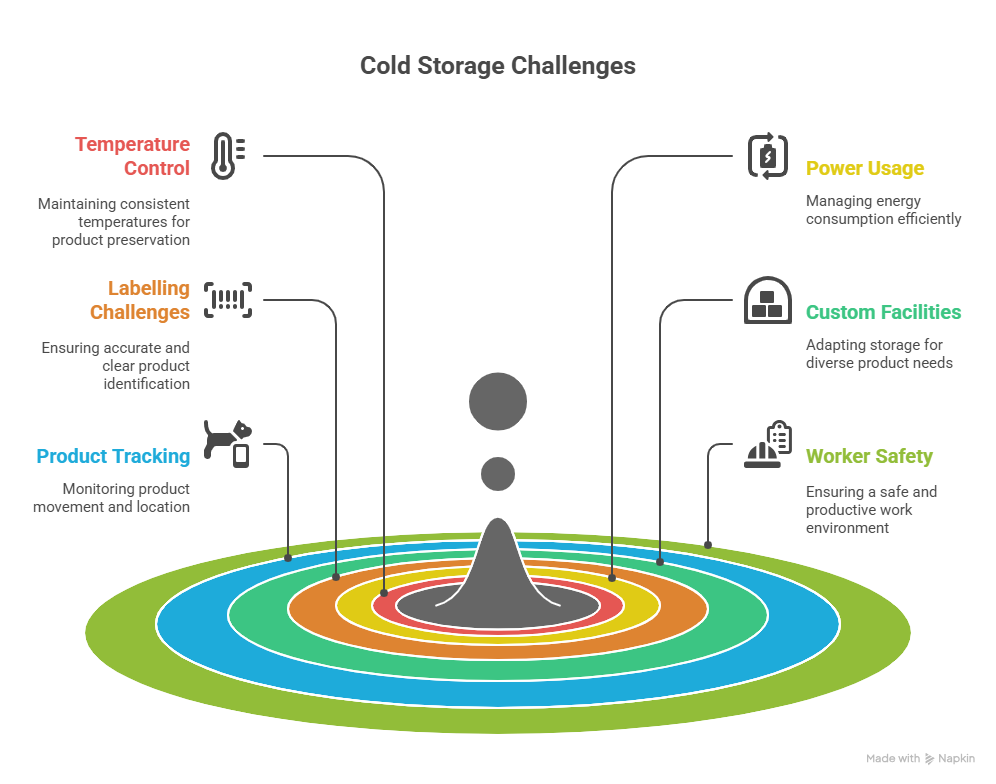
1.Temperature and Humidity Control
Chilling larger areas can sometimes be less efficient than smaller ones. Cold storage facilities, especially those designed for high-density storage, aim to maximize space. When a door is opened, warm air enters the temperature-controlled areas.
Every time a product is taken out of the freezer, it warms up, which can raise the temperature slightly when it’s returned. This change can affect product quality due to moisture buildup. Seasonal temperature changes can also lead to spoilage.
2.Power Usage
In cold chain logistics, running cold storage facilities requires a lot of electricity since they operate 24/7. With energy costs always increasing, keeping power consumption low is a major concern. Maintaining stable temperatures and protecting frozen goods demands significant energy for refrigeration, especially in larger warehouses.
3.Labelling Challenges
Labels for products and racks in cold storage need to be different from regular labels. They must be made from materials that can withstand low temperatures, as the cold can affect the quality of the labels, adhesive, and ink.
Poorly made labels might curl, crack, or freeze, leading to misidentified products. To tackle these issues, facilities need reliable barcode labels suitable for cold environments. They also have to decide between magnet or adhesive labels based on specific warehouse conditions.
4.Custom Facilities for Different Products
A big challenge in cold storage is meeting the different needs of customers. Various products require different temperatures in the same warehouse. For instance, fresh produce may need to be stored at 55°F, meat at 28°F, and ice cream at -10°F. This complexity requires facilities to be customized to handle specific storage needs.
5.Product Tracking
Knowing where products are located in the warehouse or during transit is crucial for cold storage operations. Each pallet must be tracked by its expiry date, freezing temperature, and freezing date, along with any rules that apply.
Some items, like fresh produce, may need extra controls for things like humidity or carbon dioxide, making accurate records important. Implementing a complete tracking system for inventory can be a significant challenge.
6.Worker Safety and Productivity
The human element is also important in the cold storage industry. Workers face challenges related to labour and productivity, as they must bundle up to stay warm. Those handling cleaning, maintenance, and machine operations are at risk for cold-related illnesses like the flu and bronchitis, as well as other accidents.
Warehouses need to provide special equipment and protective clothing, like gloves and goggles, to help keep workers safe and comfortable.
4 Solutions for Cold Storage Warehouses
1.Temperature and Humidity Control
Cold room services often accommodate various products, requiring distinct units for each type. It’s essential to regulate the temperature in every section of the cold storage unit.
For instance, you can enhance temperature management by using a modular insulated wall system to create barriers between different zones. These plastic modular curtains, resembling shower curtains, can be easily deployed and redeployed, allowing you to separate the warehouse into specific temperature zones as needed.
2.Adopt Technology
Using technology like automated storage systems, advanced cooling systems, and energy-saving cooling solutions can make cold storage more efficient. To make better use of space and reduce labour, add automation wherever you can. This can help lower energy costs by reducing mistakes and cutting down the need for workers. For example, using automated palletizers and depalletizers lets you run operations with fewer staff, speeding up loading and unloading.
3.Maintain Records
Since products in a cold warehouse are sensitive to temperature changes, it’s important to keep a close eye on your inventory. Use temperature sensors to accurately track temperature, set off alarms, and catch any issues early. Modern software can help you scan pallets and keep precise records in your database.
4.Right Equipment
You need special equipment for the different areas in your cold storage facility, like computers, forklifts, sensors, and scanners. Make sure your workers have personal protective gear like insulated coats, pants, and gloves.
Ensure that your equipment has large buttons that can be easily pressed while wearing gloves. Industrial racks should be strong enough to handle cold conditions and consider using batteries with higher voltage to meet your needs.
Conclusion
To sum it up, dealing with the challenges of cold storage warehouses is important for smooth operations and the safety of everyone working there. By improving efficiency and lowering costs, we can create a better work environment.
If you need help, think about working with Qodenext. Together, we can make your cold storage warehouse a more efficient and successful place. Let’s work towards a better future together!
FAQ: X Cold Storage Warehouse Challenges and their Solutions
1.How dangerous is prolonged exposure in a cold storage warehouse?
Prolonged exposure to cold storage can lead to cold-related illnesses like hypothermia and frostbite. Workers may also experience fatigue, reduced concentration, and an increased risk of accidents.
2.Which factors affect a cold storage warehouse?
Factors affecting cold storage warehouses include temperature fluctuations, humidity levels, energy consumption, product labelling, facility layout, workforce efficiency, and adherence to health and safety regulations for perishable items.
3.Is a cold storage warehouse eco-friendly?
Cold storage warehouses can be eco-friendly if they use energy-efficient equipment, renewable energy sources, and sustainable practices. However, their high energy consumption can pose environmental challenges if not managed properly.
4.What types of labels are suitable for cold storage product identification?
Labels made from durable materials like laminated vinyl or polyester with adhesives designed for low temperatures are best. Barcode and magnetic labels that withstand cold and moisture ensure accurate tracking.
5.How can cold storage warehouses customize facilities for multiple temperature zones?
Modular insulated wall systems, such as plastic curtains, can divide warehouses into different temperature zones, enabling tailored environments to store diverse products at their optimal conditions.
6.What role does inventory tracking play in cold storage management?
Accurate tracking of product location, expiry dates, and storage conditions using temperature sensors and barcode or RFID scanning improves product quality control and compliance with regulations.
7.How can worker safety be ensured in cold storage environments?
Providing insulated protective clothing, gloves, goggles, equipment with user-friendly controls, regular safety training, and health monitoring helps protect workers from cold-related risks.
8.What technologies help monitor temperature and detect issues early in cold storage?
Temperature sensors integrated with alarm systems and modern inventory management software that logs and analyzes data enable real-time monitoring and prompt corrective actions.