Picking errors are the killers of warehouse productivity. Warehouses may know that these errors are occurring, but not all understand their implications or how to address them.
The order picking process supports the order fulfilment process. When the customer order arrives, there should be a person who will “pick” the product from the shelves so that others can package and ship it. This is such a crucial process. It constitutes approximately 55% of the warehouse’s total operating expenses. However, it can significantly impact order picking accuracy.
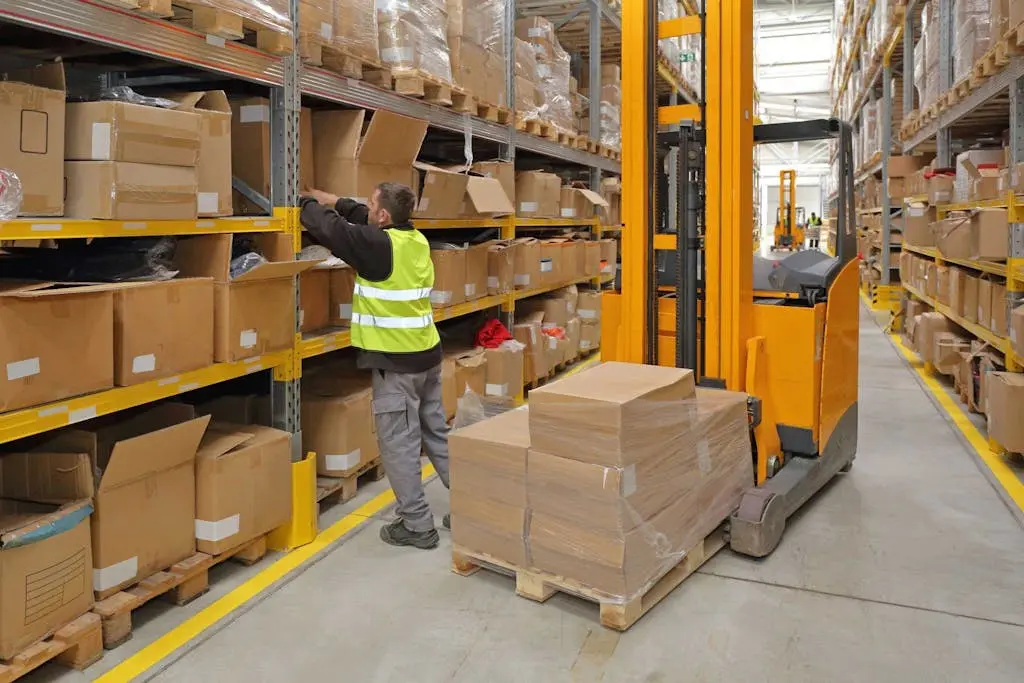
6 Strategies for Improving Order Picking Accuracy
However, humans have the potential for errors. So, here are some tips on how to improve, which will boost your bottom line and increase customer satisfaction.
Here are some of the strategies that you can implement to enhance your order picking accuracy and increase your warehouse productivity:
1.Maintain an Accurate Data Inventory
Strategies for improving the accuracy of your picking will remain ineffective if you don’t have a strong foundation that emphasises timely and accurate data. You need a process to identify products and locate them quickly with rack labels and internal signs.
You must also know how to verify in real-time that the inventory you have is located in the right place, so you don’t run out of stock or risk pulling the items from the wrong shelves.
A highly effective approach is to leverage a Warehouse Management System (WMS) combined with RFID tags. A WMS looks into all aspects of warehouse operations, which includes inventory management.
RFID tags serve as an alternative or complement to barcodes. They are encoded with unique identifiers that can be scanned remotely and in bulk.
This provides real-time inventory data, significantly reducing the risk of routine errors or mismatches.
2.Analyse Product Velocity
It’s not efficient to keep the items that do not sell very well at the front of your storage racks. When it comes to order picking accuracy, you will need to carefully analyse product velocity so you can strategically “slot” your items.
“Slotting” means the way you can locate the inventory in the picking area. Many warehouses use velocity-based slotting, which considers how frequently products leave the warehouse.
If the picker has to walk a hundred years multiple times to get the same item, then your warehouse layout lacks optimization. This will result in fatigue, and mistakes will occur.
3.Strategic Picking
Other than slotting, your picking and inventory strategies must make sense to reduce picking time and improve accuracy. For instance, when grouping similar items, it’s easier for workers to remember and collect them. This is called zoning.
As per zone policing strategies, order pickers only work in one zone. A “hot zone” in a warehouse refers to areas where the most product activity occurs. Assigning your most skilled pickers to these zones ensures greater accuracy.
Batch picking is another widely used order picking accuracy strategy to enhance efficiency and accuracy. This method works well with zone-based layouts, allowing employees to pick multiple orders from a single zone in one trip. The collected items are then sorted into individual orders afterwards.
Onto other warehouse order picking methods.
4.Leveraging the Right Technology
Not only does adopting the right warehouse technology and automation improve the profitability of your warehouse picking and packing activities, but it also reduces fulfilment errors.
Here are the technologies that are most effective in improving order picking accuracy:
- Radio Frequency Scanning Devices: As the most widely used solution in order picking, it earns its name. These handheld devices are flexible and cost-effective solutions to capture product data.
- Visual Logistics: These handheld devices display text and logistics information, which helps the workers improve the operations’ accuracy. For instance, there might be an image of the product or the bin location to use as guidance.
- Pick to Light: To improve order picking, use the ‘Pick to light” solutions. They work with the help of alphanumeric buttons and displays at storage locations. It guides the employees in picking activities.
- Voice-Directed Picking: With voice-guided picking, employees can wear Bluetooth-connected headphones that provide step-by-step audio instructions for order picking. This hands-free system ensures better accuracy, increasing efficiency.
What’s even better is that you can combine all these solutions. Thus, your workers can be more productive and save time instead of going back and forth from one location to the other.
Let’s look at a few more ways to improve warehouse picking accuracy.
5.Analyse Error Data
Even with the correct processes and technology, you may still experience a few picking errors. To enhance picking accuracy, it’s essential to have a system in place to identify and evaluate errors.
Employees must have IDs so you can determine which ones need additional training. You can also refine your warehouse organisation, change your picking strategies, or even adapt new automation technologies to enhance efficiency.
More warehouse managers understand that customer service is a major driver of their success. Also, picking errors may reduce customer satisfaction, impacting both profits and repeat business. With these best practices, you can ensure top-quality service.
Let’s see the last one of the warehouse picking strategies.
6.Use Smart Automation
When there is direct human involvement in any process, errors are likely to happen.
In the case of warehouse picking, this amounts to inefficiency. Usually, pickers spend most of their time travelling from one point to the other within the warehouse. They pick orders in that process. But this is what creates waste using excess time.
Thankfully, many technologies automate long-standing warehouse procedures. They are barcode scanners. Conveyor belts, mobile robots, and more. Their goal is to reduce the time workers spend moving the products manually. Some of the best automation solutions for warehouses enhance the work humans do rather than replace them.
So, the goal of order picking accuracy is to boost efficiency without losing the human touch.
By implementing these strategies, you will be able to achieve a warehouse that operates at a high level and conserves time while raising productivity.
FAQs: A Guide to Improving Order Picking Accuracy
What are some order picking accuracy KPIs?
Order picking accuracy KPIs include picking error rate, order accuracy percentage, mispick cost, items picked per hour, and customer satisfaction scores related to order fulfilment.
What is the order picking accuracy formula?
The formula for order picking accuracy is:
Order Picking Accuracy (%) = (Total Number of Correctly Picked Orders÷ Total Picked Orders) × 100
This measures the percentage of error-free orders.
What is the other name for order picking?
Also known as order fulfilment picking, order picking has many names. Some others are picking or stock picking in warehousing contexts.
What are some roadblocks you can face in picking?
These may include inventory inaccuracies, complex orders, inefficient layouts, human errors, peak demand pressures, and technology downtime.
Conclusion
Improving order picking accuracy is the key to enhancing warehouse efficiency and ensuring customer satisfaction. Qodenext offers high-tech solutions in the form of RFID and automation to up process quality by several notches, reduce errors, and optimise productivity.See how Qodenext can help you revolutionise your warehouse operations today!