
In an ecommerce warehouse, things are moving all the time – literally. Finished products and raw materials go on quite the physical journey before they are packed in orders, changing hands many times and traveling through multiple warehouse stations or locations.
How those materials are physically moved is a key to a safe, speedy, and efficient warehousing operation. If materials are handled in the proper ways and using the proper equipment, it’s much easier to keep normal processes running smoothly. But if your warehouse material handling is sloppy or hazardous, it can impact warehouse efficiency and productivity.
In this article, we’ll dive deep into warehouse material handling and the role it plays in your ecommerce supply chain.
What is Material Handling?
Material handling is the movement of materials and goods from one location to another. It includes protecting, storing, and controlling the materials, from manufacturing to distribution.
Material handling can be used across industries, but is typically utilized in warehousing, where goods need to be securely stored, retrieved, and shipped.
Material handling equipment utilizes manual, semi-automated, and automated equipment to assist the movement and storage of materials within the warehouse.
What Is Warehouse Material Handling?
Warehouse material handling refers to the movement, storage, protection, and control of materials throughout the supply chain.
Any time materials in a warehouse (such as raw materials or finished inventory) are physically moved – including during manufacturing, procurement, receiving, storage, fulfillment, shipping, and last-mile delivery – warehouse material handling is involved.
Proper warehouse material handling ensures that raw materials and products are carefully and efficiently transported where they need to go, so that a business can speed up its supply chain, minimize errors, and reduce waste.
Why Does Warehouse Material Handling Matter?
Material handling directly impacts productivity in warehouses, manufacturing plants, and distribution centers. An inefficient facility causes errors and delays, eroding customer loyalty and making it easier for your competition to snatch away business.
Something else that’s interesting? Effective material handling isn’t only about sorting your goods into unit loads. Successful businesses invest time into monitoring and improving their material handling system in order to protect:
- The integrity of their goods
- The productivity of their retail warehouse, 3PL warehouse, distribution center, or manufacturing plant
- The physical and mental health of their workers
When a shipment arrives, a good material handling process ensures goods get from the dock to the appropriate rack in good time. It also accounts for proper control of materials. You can mitigate theft, damage, and spoilage with a material handling process that limits access to certain parts of your warehouse to particular employees.
Finally, proper material handling allows warehouses to store goods in an organized manner that makes it easy to pick and pack inventory for outgoing shipments.
Warehouse Material Handling Principles
Consider following these principles to ensure safe, efficient and cost-effective material handling. They’re based on factors like the material type and nature, distance covered, storage requirements and equipment availability.
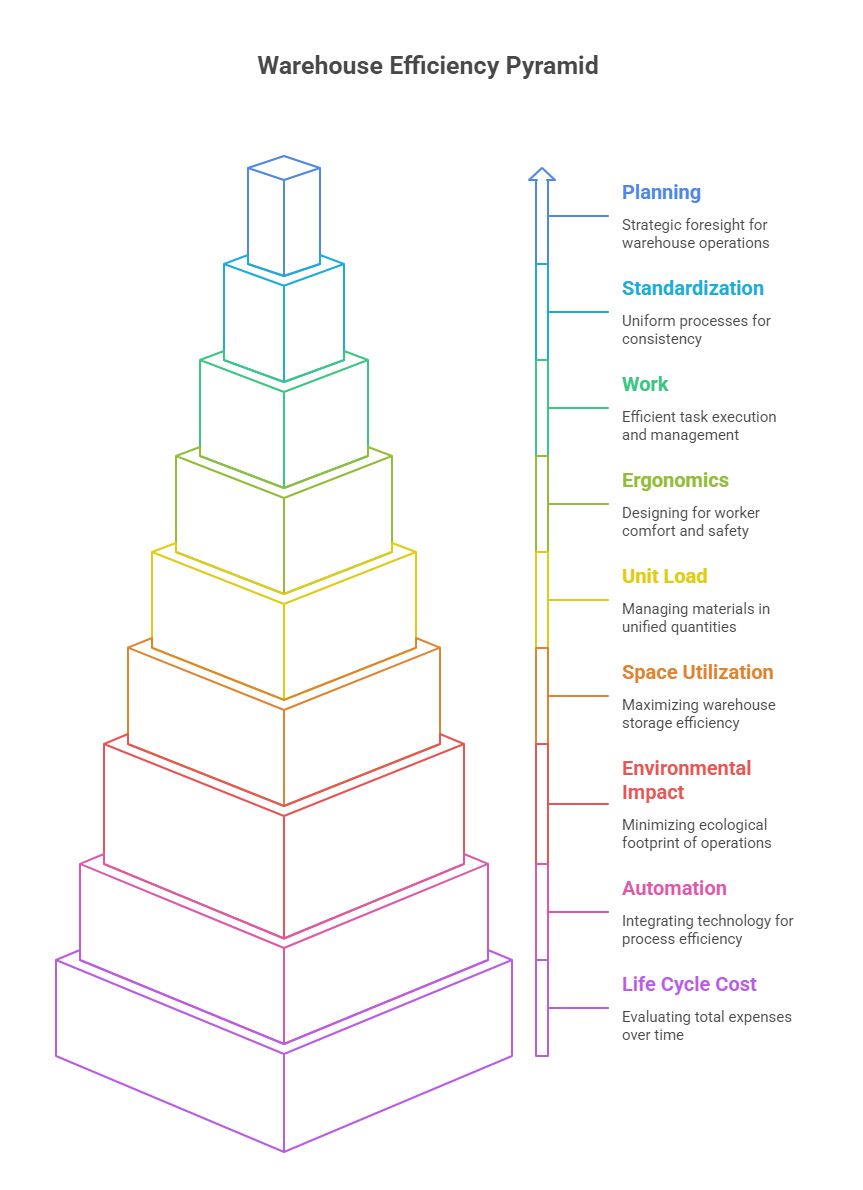
Planning: Assess the materials, equipment and labor required to handle operations. Effective planning reduces operational costs and increases efficiency. The planning phase also includes developing strategies to optimize resources and minimize waste.
Standardization: Handle materials with consistent methods, procedures and equipment. This strategy simplifies the handling process, reduces errors and improves efficiency. It also reduces accidents and injuries caused by unfamiliar or inconsistent handling practices.
Work: Design workstations and handling equipment to minimize worker injury or strain.
Ergonomics: Ergonomics reduces fatigue, improves productivity and prevents work-related injuries.
Unit Load: Forklifts and pallet jacks minimize handling time and labor costs. They consolidate products into a single unit load to reduce damage during handling and transportation.
Space Utilization: Effective space utilization can reduce additional storage space, minimize handling time and improve material flow.
System: Coordinate material movement and processes (receiving, storage, inspection, production, packaging, shipping and transportation) to form an integrated, cohesive system.
Environmental Impact: Implement sustainable practices and use of environmentally-friendly materials and equipment to minimize the impact of material handling operations.
Automation: Increase efficiency, reduce labor costs and improve safety by reducing the need for manual handling via automation.
Life Cycle Cost: Analyze equipment life cycle costs by considering factors such as upfront, maintenance, repair and replacement costs.
The Role of Warehouse Layout
For your material handling equipment to work efficiently, you need a revision of the layout. The layout will affect your material handling systems, and it can be the difference between a messy warehouse and an efficient warehouse.
Poor layout design increases the risk of injury, and motion waste, and introduces bottlenecks. Redesigning the layout can streamline the processes, improve the employees’ mental and physical health, and decrease worker movements.
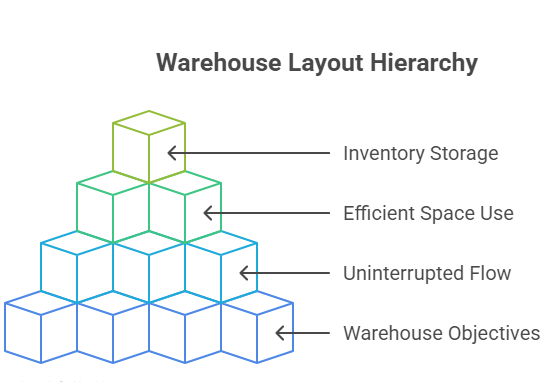
1. Warehouse Objectives
Before changing the layout of your warehouse, you ought to know your goals or priorities. Some of the goals might focus more on inventory management, while others might improve materials packing and picking. After zeroing in on your goals, you can thoughtfully structure the layout of the warehouse.
2. Uninterrupted Flow
A good layout should not interfere with the flow of goods. All operations ought to keep on moving, and all the equipment should be functional. The storage of materials and products ought to be well thought out to boost their accessibility.
3. Efficient Use of Space
Even with a small room as your warehouse, you can design the layout to meet all your needs. That is, get to know the different storage options without wasting any space. The equipment, too, ought to work hand in hand with the available space and layout.
4. Inventory Storage
Never overload a facility. Calculate the available inventory to know whether it can fit in your warehouse. Poor inventory management and storage will affect material handling and increase injuries. It takes more time for the workers to move the products around the warehouse.
You must understand how long you’ll store the inventory and the amount available. It ensures that you’ll easily come up with smart decisions on the different storage options.
Warehouse Material Handling Benefits
From preventing workplace injuries to saving money, effective material handling systems can provide numerous benefits:
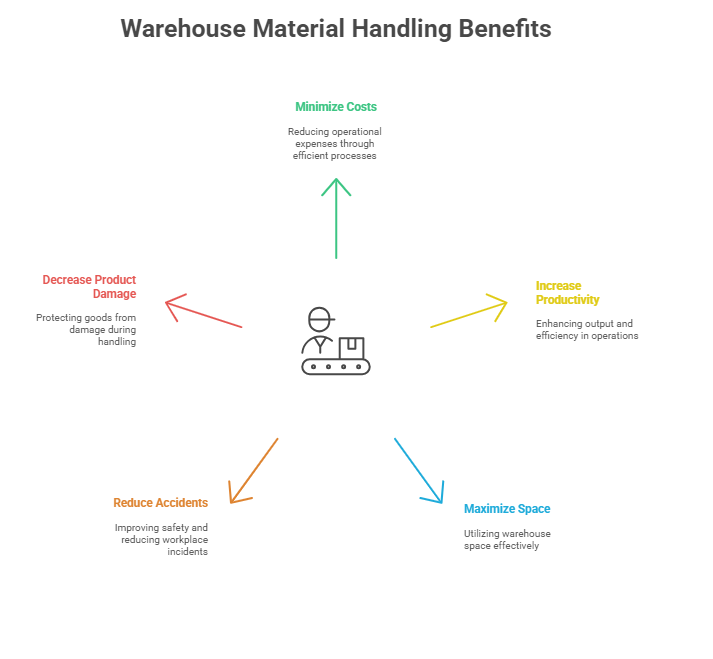
1. Minimize Costs
Streamline material handling to reduce manual touches on equipment. Use optimal storage space to avoid the need for additional storage facilities and associated costs. It organizes materials efficiently to store more goods in the same amount of space while reducing overall storage costs.
It cuts down on transportation costs by optimizing the material flow required to transport materials.
2. Increase Productivity
Efficient material handling systems optimize inventory management and reduce the inventory required for storage. They also reduce the time and labor required for each production cycle to improve efficiency. Regular maintenance and inspections allow businesses to identify risks and avoid equipment breakdowns.
They automate certain processes to minimize injuries and reduce the labor needed to remove materials.
3. Maximize Space
Mezzanines, pallet racks and tall storage facilities help maximize vertical storage space. Plan proper storage areas by identifying the best locations for materials and optimizing storage layout.
It analyzes material flow, identifies high-traffic areas and designs storage systems accordingly.
4. Reduce Accidents
Automated material handling systems such as conveyor belts and robotic systems reduce the need for manual labor to move heavy loads. Proper material storage and organization reduce accidents caused by tripping, slipping or falling objects. It also minimizes the risk of musculoskeletal injuries and physical strain.
5. Decrease Product Damage
Protective wrapping, pallets and containers can prevent damage during handling, stacking and transport. Train workers to use appropriate lifting techniques to avoid product dropping or mishandling. Use appropriate equipment, such as forklifts, conveyors and hoists, to reduce extensive product damage.
Conclusion
Warehouse material handling is a critical aspect of warehouse management, and efficient equipment utilization can improve the productivity and profitability of warehouse operations. With the right equipment and a well-organized warehouse layout, businesses can streamline their material handling processes, reduce errors and maximize space utilization.
However, warehouse management software integration is necessary to achieve optimal efficiency, in today’s digital age. It can help automate and optimize warehouse operations, provide real-time inventory tracking and streamline order fulfillment processes.
Get you warehouse material handling in order with the help of Qodenext.
FAQ: Warehouse Material Handling
1. How can businesses determine the right balance between manual and automated material handling processes in their warehouses?
Businesses can look at productivity metrics, equipment utilization, and accuracy rates over time to determine whether their operations would benefit from manual handling processes, automated handling processes, or a combination of both.
2. Are there any warehouse material handling trends or innovations that businesses should be aware of in order to stay competitive?
To stay competitive, businesses should keep track of automated material handling technologies as they continue to develop, as well as strategies for optimizing warehouse layouts.
3. How can warehouse management systems help improve material handling efficiency and accuracy?
Warehouse management systems can provide better visibility into warehouse operations, increased inventory control, and improved labor management, which will eventually improve the efficiency and accuracy of material handling.
4. What is the warehouse handling process?
The warehouse handling process is a series of steps that manage goods from arrival to dispatch. It includes receiving and inspecting shipments, storing and organizing inventory, picking and packing orders, shipping products, and ongoing inventory management to ensure accuracy and efficiency.
5. What material handling equipment is commonly used in a warehouse?
Common material handling equipment in warehouses includes forklifts, pallet jacks, order pickers, conveyor belts, robotic picking systems, automated guided vehicles (AGVs), cranes, and hand trucks. These tools help move, store, and protect goods efficiently while reducing manual labor and improving safety.
6. What is manual handling in a warehouse?
Manual handling in a warehouse refers to the physical movement of goods by hand or bodily force, such as lifting, lowering, pushing, pulling, or carrying items. It is necessary in many warehouse tasks but poses risks of injury if not performed correctly. Proper training and ergonomic practices are essential to minimize these risks.
7. What are the types of warehouses?
Types of warehouses include distribution centers, fulfillment centers, cold storage warehouses, bulk storage warehouses, cross-docking/transloading centers, public warehouses, private warehouses, and cooperative warehouses. Each type is designed to meet specific needs related to product type, supply chain strategy, and industry requirements.
8. Why is inventory management important in a warehouse?
Inventory management is important because it ensures that the right products are available in the right quantities at the right time, preventing stockouts and overstock situations. Accurate inventory tracking supports efficient operations and timely order fulfillment.
9. How does a Warehouse Management System (WMS) contribute to warehouse operations?
A WMS streamlines processes and improves efficiency by automating tasks such as inventory tracking, order picking, and reporting. It helps reduce errors, optimize space usage, and ensure timely order fulfillment.
10. What are the key functions of a warehouse?
Key functions include receiving and unloading goods, storing and organizing inventory, picking and packing orders, shipping and delivery, inventory management and control, and maintaining warehouse cleanliness and safety.