
Let’s imagine you’ve placed an online order for your favorite bag, and you are monitoring its path from the warehouse to your home, eagerly awaiting its arrival. Have you ever thought about how the magic works behind the scenes? It’s the order fulfillment action!
The fast and effective delivery of your goods is guaranteed by the back-end procedures. It’s a well-oiled operation from selection and packaging to shipping and delivery. But what is order fulfillment? Fasten your seatbelts, for we are about to delve into the exciting realm of shipping your orders from the warehouse straight to your door!
What is Order Fulfillment?
This involves a series of steps involving the receipt of an order, its processing, and distribution to the end user. With it, all e-commerce businesses are held together since they want to ensure that customers receive exactly what they ordered at the agreed time. It is the process of the flow and delivery of your product from the warehouse to your home.
The Order Fulfillment Process
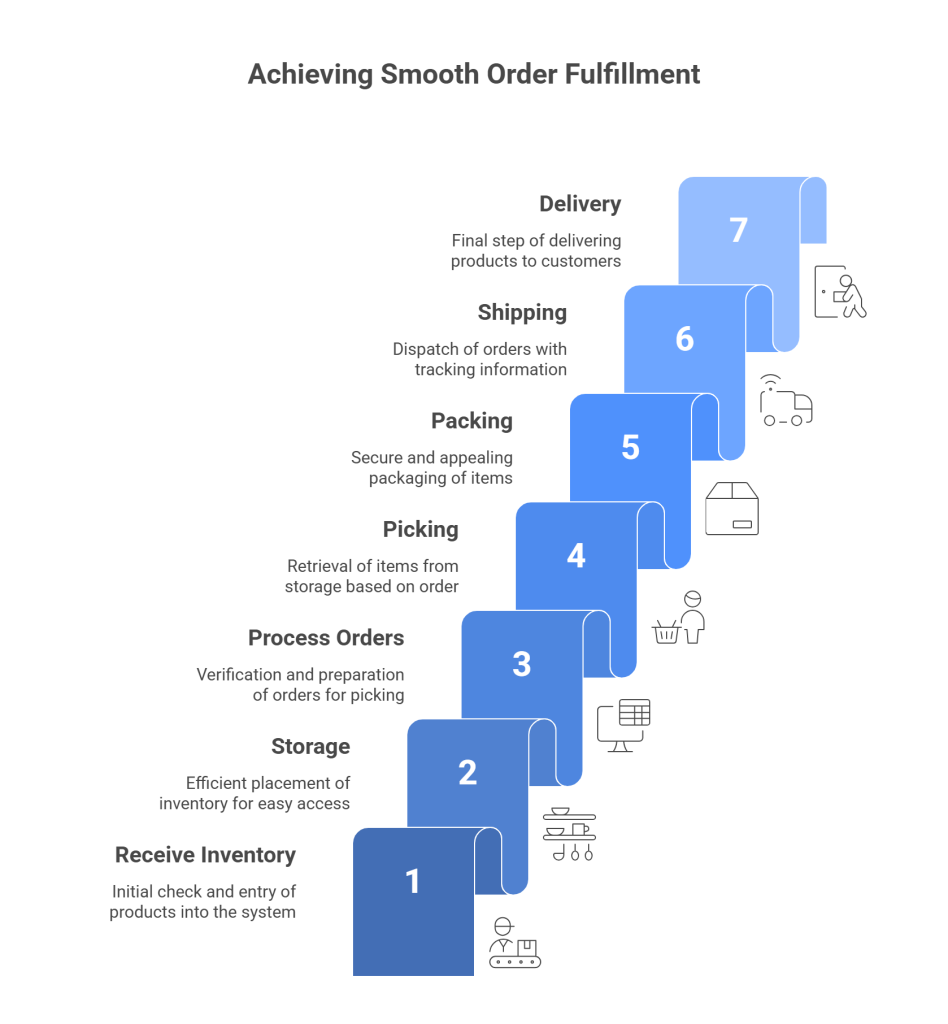
Well, what then could be the formula for smooth and effective orders? Okay, let’s just evaluate it step by step.
1. Receiving Inventory
The process begins with the receiving of the products. As the stocks are received in the warehouse they are counted and checked for quality, then they enter into the inventory system. By doing this, you can ensure everything is ready before orders start coming in.
2. Storage
After the check involving inspections and audits of the inventory, it is placed in particular areas within the warehouse. Ideally, storage should be dealt with efficiently to enhance the rate of picking and also curtail errors.
3. Processing Orders
Once a customer orders, a set of processes begins. Order information is checked, payments are made and a pick ticket is created. This ticket informs the warehouse team which stock items to pick and correctly pack for the final destination.
4. Picking
This process of picking orders starts in a warehouse by retrieving the items from the shelves based on the ticket. In order to ensure correct products are chosen every time, speed and precision are essential.
5. Packing
The collected items are then packed properly to be shipped on the next course of the supply chain. Remember packaging is not simply placing goods in a container, it means guaranteeing your product isn’t damaged during transportation and creating an exciting experience that makes the customer want to open the package.
6. Shipping
After packing the order is shipped by courier service or a shipping company. This step involves the creation of shipping labels, order status changes, and notification of tracking info to the customer.
7. Delivery
The last action involves the delivery of the specific product relevant to the identified problem. The shipping carrier then brings a package to the door of your customers. Order completion is incurred when the ordered items are delivered to your buyer.
How to Improve Order Fulfillment Process?
After going over the fundamentals, let’s discuss how to improve the order fulfillment procedure. In the realm of online shopping, precision, and quickness may either make or ruin your business.
1. Make Inventory Management More Streamlined
A seamless order fulfillment process starts with efficient inventory management. Here’s how to do it correctly:
- Automate Inventory Tracking: Monitor stock levels in real-time with software. This lessens the likelihood of overstock and stockouts.
- Arrange Your Storage Facility: Place popular things in places where they are easily accessible and establish a system of clear labeling. Having a neatly arranged warehouse expedites the selection process.
2. Streamline the Ordering Process
Accuracy and speed of fulfillment can be greatly increased with effective order processing.
- Put Order Management Systems (OMS) to Use: Order processing is automated by an OMS, which decreases human error and boosts productivity.
- Establish Clear Protocols: Ensure your group processes orders according to a set procedure; this reduces misunderstandings and mistakes.
3. Boost the Effectiveness of Picking and Packing
Picking and packing are labor-intensive processes where little adjustments can result in significant impact.
- Put in place a pick-to-light system: this system can help you speed up the processes and reduce errors by using lights to direct pickers to the appropriate goods.
- Educate Your Group: Frequent training guarantees that your team can manage the process effectively and is knowledgeable about current best practices.
4. Pick Reputable Shipping Companies
The last challenge in the order fulfillment process is shipping. Selecting trustworthy partners guarantees precise and on-time delivery.
- Negotiate Rates: To get the best bargain, compare rates offered by several carriers. Your profit margins may increase with lower shipping expenses.
- Provide a Range of Shipping Choices: Provide customers options to improve their experience, such as regular or expedited shipment.
5. Interact with Your Customers
The experiences of your customers or clients are improved and confidence is developed when they are kept informed throughout the order fulfillment process.
- Notify your customers: When their order has been received, processed, and dispatched let them know by sending them an order confirmation and updates.
- Give tracking details: Permit clients to follow their orders in real-time. This raises contentment and lowers anxiety.
Order Fulfillment Example
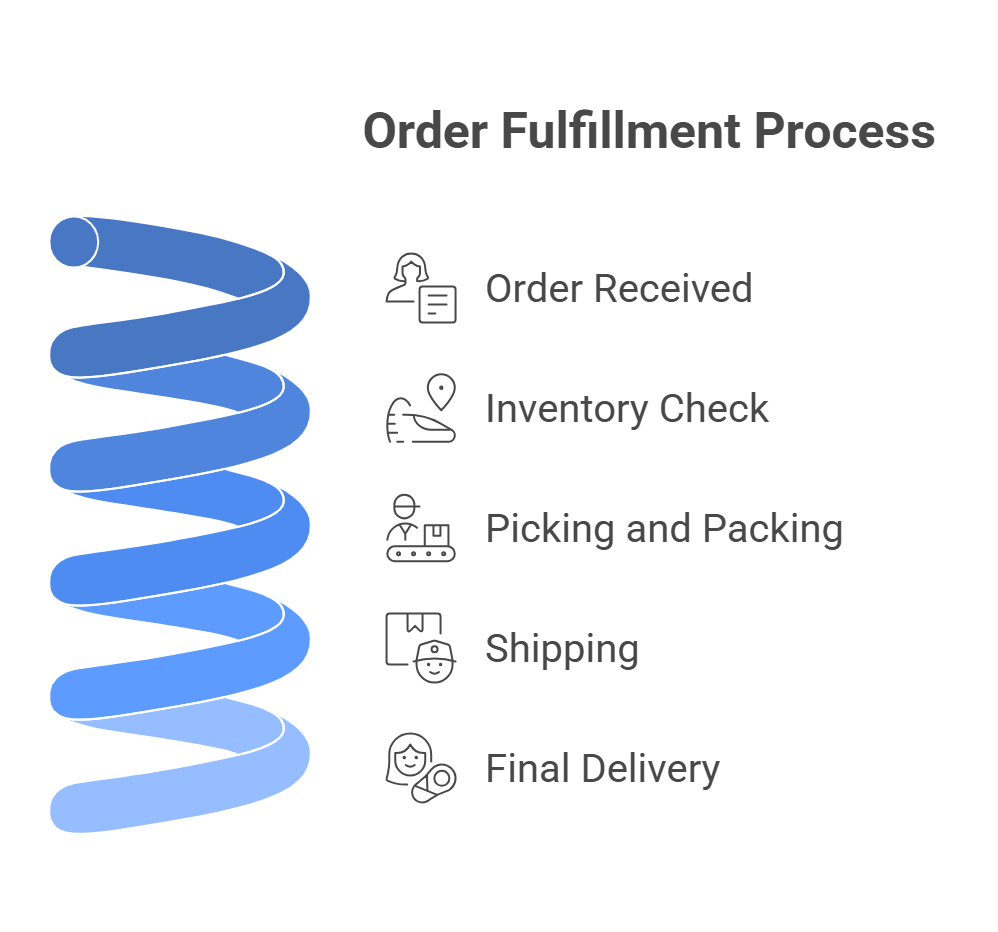
To understand how order fulfillment works in real life, let’s walk through the journey of a customer named Mary—a regular online shopper who just bought a new pair of shoes.
Step 1: Order Received
Mary places her order through an e-commerce website. Within seconds, the platform’s order management system gets to work. It confirms her purchase details and securely processes her payment. Everything is smooth and automatic.
Step 2: Inventory Check
Now, behind the scenes, the system checks if the shoes Mary ordered are available in the warehouse. Once confirmed, a picking ticket is generated and sent to the warehouse team, signaling them to prepare the order.
Step 3: Picking and Packing
At the warehouse, the team uses a smart pick-to-light system to quickly find the exact pair of shoes from the shelves. This system lights up the right location, helping staff avoid mistakes and save time. Once the shoes are picked, they’re carefully packed in a sturdy box, with protective wrapping to make sure nothing gets damaged in transit. A shipping label is added, and the package is ready to go.
Step 4: Shipping
The order is handed over to a delivery partner, like FedEx, Delhivery, or Blue Dart. As soon as the shoes are on their way, Mary receives an email with a tracking link so she can follow her package in real-time—from warehouse to doorstep.
Step 5: Final Delivery
A few days later, Mary hears the doorbell ring—it’s her package! She opens the box to find her shoes in perfect condition, neatly packed just as she expected. Thanks to a well-managed fulfillment process, Mary’s shopping experience is fast, reliable, and stress-free.
Why This Matters
This example shows how each step in the order fulfillment process—from order confirmation to final delivery—plays a key role in keeping customers happy. When done right, it leads to faster shipping, fewer errors, and a great overall experience that keeps people like Mary coming back for more.
Conclusion
Success in your e-commerce business depends on how much you know what order fulfillment is and how you can handle the entire process. Every stage, from obtaining inventory to delivering the finished product, should be done perfectly to guarantee your client’s pleasure.
Thus, let’s remember, that each time you order any item from an online store, there is a complex chain of work and interactions that go on behind the scenes.
This is a highly organized sphere ensuring efficiency, accuracy, and dedication with one only objective in mind: to deliver customers what they requested on time. Cheers to your shopping!
FAQs: What is Order Fulfillment? Process and Strategies
1. What is order fulfillment?
Order fulfillment is the complete process that starts when a customer places an order and ends when the product is delivered to their door. It involves receiving inventory, processing the order, picking, packing, shipping, and final delivery.
2. Why is order fulfillment important for e-commerce businesses?
Order fulfillment ensures customers receive exactly what they ordered on time. Efficient fulfillment builds customer trust, improves satisfaction, reduces errors, and keeps businesses competitive in the fast-paced e-commerce market.
3. What are the main steps in the order fulfillment process?
The key steps include receiving inventory, storing products, processing orders, picking items from the shelf, packing goods securely, shipping the package, and finally delivering it to the customer.
4. How can businesses improve their order fulfillment process?
Improvement can come from automating inventory tracking, organizing warehouses efficiently, using order management systems, implementing pick-to-light technology, training staff regularly, and choosing reliable shipping partners.
5. How does pick-to-light technology enhance picking accuracy?
Pick-to-light systems guide warehouse workers with lights that indicate exactly where items are placed, speeding up picking and greatly reducing errors by ensuring the right products are selected every time.
6. What role does customer communication play in order fulfillment?
Keeping customers informed sends order confirmations, shipping updates, and tracking information. This transparency enhances their experience, reduces anxiety, and increases customer loyalty.
7. What challenges do businesses face in order fulfillment?
Common challenges include inaccurate inventory management, errors during picking and packing, shipping delays, and coordinating multiple steps without mistakes—each of which can hurt customer satisfaction.
8. How can technology help streamline order fulfillment?
Tools like barcode scanners, inventory management software, automated picking systems, AI, and data analytics help speed up processes, minimize human error, and provide real-time visibility into orders.
9. What’s the difference between order processing and order fulfillment?
Order processing deals with confirming order details and payment, while order fulfillment covers the entire workflow from taking the order, packaging the product, shipping, and delivery to the customer.
10. Can you give a simple example of the order fulfillment process?
Sure! Imagine Mary ordering shoes online. Her order is received and payment confirmed, the warehouse team picks and packs the shoes, ships the package via a courier, and Mary receives it at her doorstep—all tracked step-by-step to ensure accuracy and speed.