The warehouse receiving process replenishes the stocked inventory in the warehouse. It is the first step to delivering the ordered item to a customer. This process includes delivery, unloading, and storing ecommerce inventory in a warehouse or fulfilment centre.
A proper receiving process can make inventory management and fulfilment smoother, more efficient, and cheaper. Today, we will examine a few best practices for this receiving process in your warehouse that can enhance efficiency.
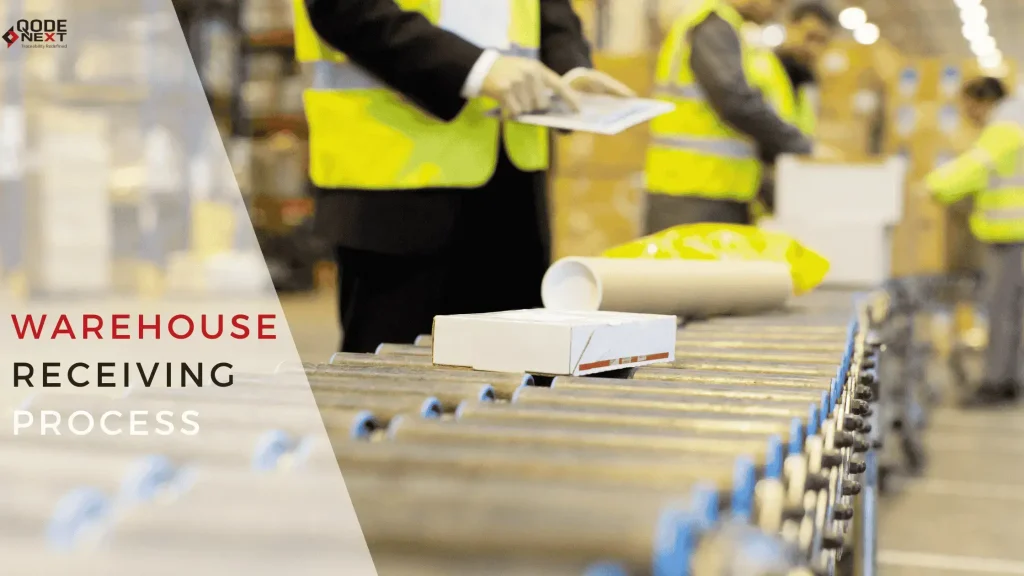
What Most Businesses Get Wrong
Warehouse receiving ensures inventory is unloaded, checked, and stored efficiently to maintain accurate stock counts. Without a clear process or checklist, businesses risk inventory errors, which can affect operations.
Staff need step-by-step resources and procedures to streamline receiving. Some operations use Warehouse Receiving Order (WRO) systems to track incoming inventory and plan capacity. If discrepancies arise, items are placed on hold as an Unidentified Receiving Order (URO). Businesses are notified to resolve issues promptly, minimising delays in processing and storage.
So, here’s how to improve the receiving process.
15 Warehouse Receiving Process Best Practices
To ensure top-notch warehouse operations, you must take a few steps to ensure the best practices. Here are a few:
1. Standardized Process
This is a consistent approach to receiving that ensures that every team member is aware of their role. It reduces the chances of any errors or oversights.
To implement this, you need a detailed receiving manual that outlines every step of the process. Conduct regular reviews and update this manual to include the changes in technology or operations.
2. Leverage Technology
Relying solely on manual processes can result in inefficiencies and costly errors is a risk in the digital world today.
How to implement it in your warehouse receiving process?
Upgrade to a powerful Warehouse Management System (WMS) like Cadre Technologies’ solution. Our platform streamlines operations by eliminating the need for separate inventory systems. Automate tasks such as inventory updates and documentation checks, while leveraging predictive analytics for smarter, data-driven decisions.
3. Continuous Training
As the warehouse industry evolves, new challenges will arise. So, it’s crucial to ensure your team stays updated regarding all the new developments. They must know all the updated software and technologies used in handling the receiving process in warehouse management.
To ensure that everyone is on the same page, conduct regular training sessions, workshops, and even webinars. Focus on areas like safety protocols, technology tools usage and more in the warehouse receiving process.
4. Vendor Collaboration
A strong relationship with suppliers can streamline the receiving process making sure there are timely shipments.
Open communication channels with vendors help. Also, schedule regular check-ins, give feedback on shipment quality, and collaborate on optimising delivery schedules.
5. Regular Audits
Even if you have the best processes in place, there is always room for improvement. Regular audits can identify the shortcomings and allow you to refine areas that need attention.
Assign a team or third-party service to conduct audits at regular intervals. With their feedback, you can refine your operations and implement new changes.
6. Quality Control Checks
Quality is as critical as quantity. Poor-quality goods can lead to customer complaints, returns, and damage to your reputation.
Create a quality control protocol to inspect random samples from received shipments for defects. Train your team to identify issues and take corrective action.
7. Prioritizing Safety
The receiving area is a hub of activity, increasing the risk of accidents. Train staff in safety protocols, including equipment use, handling hazardous materials, and emergency procedures. Conduct regular inspections to identify and resolve hazards promptly.
8. Use Inventory Management Systems
If you have an eCommerce business, then inventory management systems optimize your entire supply chain. You can automate the receiving process. All you need to do is have an inventory management system at hand and get valuable insights into inventor counts and stock levels. It also helps you to get accurate numbers for inventory accounting.
9. Monitor the Inventory Metrics
Track the important inventory metrics to optimize warehouse receiving. You can do so with the help of technology for inventory management. Some of the primary metrics include:
- Average storage cost per unit
- Total number of pallets or shelves to use
- Amount of stored inventory in each location
10. Inspect Your Inventory
To maintain a smooth warehouse receiving process flow, regular audits are necessary. This also highlights any serious inventory imbalance before it becomes unmanageable. Sending damaged inventory back costs a lot of money.
Therefore, it’s best to check each item. Using various inventory management tools, you can get real-time updates on stock levels, making tracking easier.
11. Document Verification
Also, don’t forget to double-check your documents. Ensure that the receiving inventory matches the customer’s purchasing order.
When you have a system for receiving and shipping documents, with each document having a numbering system and sequential order, it becomes easier for staff to check the paperwork thoroughly and identify missing inventory.
Apart from all of these you also need proper tech and tools to ensure a smooth warehouse receiving process. Let’s see what they are.
Tools and Tech for Efficient Warehouse Receiving Process
Integrating technology into warehouse operations is revolutionising how goods are transported, received, and stored. Here are some of the latest tech that is making this possible:
12. Warehouse Management Systems (WMS)
A Warehouse Management System (WMS) is a software solution for optimising warehouse operations.
Key Features
- Real-time inventory tracking
- Automated data entry
- Custom barcode reading
- Scheduling and inspection
- Predictive analytics
Benefits
By using a WMS, warehouses can achieve better space utilisation, and reduce manual data entry errors thus enhancing overall operational efficiency. The receiving process becomes streamlined, ensuring that goods are quickly and accurately registered into the systems. This reduces bottlenecks, guaranteeing timely order fulfilment.
13. Barcode Scanners
Essential devices that digitize barcode data for efficient processing.
Features
- Handheld or fixed devices that read barcodes and convert them into a digital format.
- Easily processed by computer systems for efficient data management.
Benefits
- Expedites the inventory counting process.
- Reduces human errors, ensuring real-time inventory updates.
- Enables accurate and faster order processing.
14. RFID Technology
Advanced technology for remote data reading and tracking via RFID tags.
Features
- RFID tags store item data and can be read from a distance.
- With RFID readers, you do not need a direct line of sight.
Benefits & Impact
- Enhances the accuracy and speed of the receiving process.
- Allows bulk reading of items for faster inventory updates.
- Reduces time for receiving shipments, streamlining operations.
15. Automation Solutions
Cutting-edge systems that streamline the warehouse receiving process with minimal manual intervention.
Features
- Includes automated conveyor systems, robotic unloaders, and sorting solutions.
- Operates with minimal human intervention for efficient goods handling.
Benefits
- Low reliance on manual labour for regular operations.
- Increases processing speed and reduces bottlenecks.
- Ensures goods are swiftly moved from docks to storage or processing areas, improving throughput.
FAQs:15 Best Practices to Elevate Your Warehouse Receiving Process
What is put away in warehouse operations?
Putaway encompasses every process- from receiving the supply from a vendor to storing it on shelves. It lasts until the orders land in your receiving dock and subsequently make their way into the warehouses. Quality and quantity checks are also a part of this process.
What does “pre-receiving” mean in a warehouse?
Business owners need to complete the receiving process before shipping any inventory. This stage oversees the receding requirements and fills out the proper documentation, labelling material and order forms that ensure the reception of new inventory by the warehouse property.
What are the common challenges of the warehouse receiving process?
Challenges like inaccurate inventory counts, miscommunication, delays, and damaged goods, you need proper documentation, inspections, and real-time inventory systems to mitigate them.
Conclusion
Optimising your warehouse receiving process is key to improving efficiency and accuracy in inventory management. Try these 15 tips for smooth efficiency.
For seamless operations, trust Qodenext for advanced solutions that streamline and automate your processes.