The automotive manufacturing supply chain is prone to various risks. At different stages and durations, companies inevitably face bottlenecks or challenges that disrupt the flow of operations.
These recurring inefficiencies disrupt the entire supply chain. For example, a neglected stamping machine can cause shipping delays, while rushing testing may result in defective products, wasting resources and straining customer relations.
While bottlenecks vary between companies, certain challenges are common across the automotive sector. In this post, we’ll explore these frequent bottlenecks and recommend essential strategies that every automotive company should adopt.
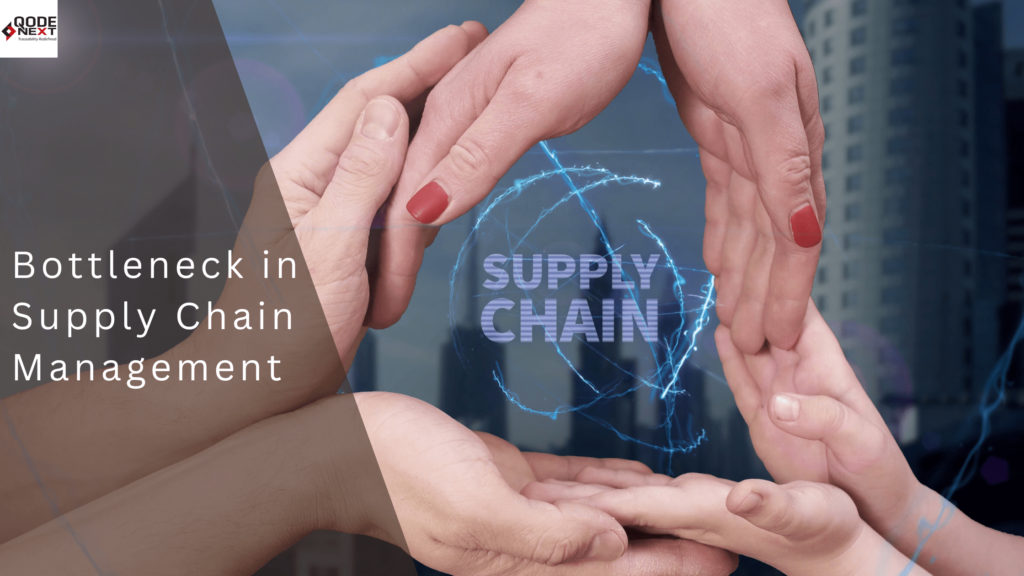
What is a Bottleneck in the Supply Chain Management?
Bottlenecks occur when certain activities slow down production, extend waiting times, and hinder overall productivity. These inefficiencies reduce operational effectiveness and often drive up product costs.
Bottlenecks restrict a company’s potential and delay project timelines. They are frequently caused by outdated systems or software, but can also stem from employee performance, poor organization, inadequate planning, communication breakdowns, or supplier-related challenges.
How to Eliminate Bottleneck in Supply Chain Management?
One thing is clear: your industrial data holds valuable stories waiting to be uncovered, but how can we make sure to control them?
Highlight and Eliminate Wasteful Processes to Boost Productivity
Operational bottleneck in supply chain management often stem from inefficient industrial processes, leading to various forms of waste. Remarkably, unpredictable bottlenecks can cost trillions of dollars in lost productivity each year, with nearly 40% of industrial output wasted before it even reaches customers.
Recognizing this waste is the first step towards its elimination. By utilizing your existing data, you can focus on identifying these bottlenecks and allocate the necessary resources to address them effectively.
It’s time to shine a light on your operational data, providing operations managers with a comprehensive view that integrates enterprise-wide systems.
This holistic perspective enables them to detect, trace, and eliminate waste-inducing bottlenecks in the supply chain, driving KPI-led operations on both micro and macro levels while reducing the need for labour-intensive manual efforts.
Categorize Bottlenecks for More Effective Maintenance
Bottlenecks can arise from various root causes on the shop floor, including random downtime, processing time variations, and other supply chain variables. Multiple bottlenecks can coexist within the production system, manifesting at different intervals.
What complicates matters is that while these bottlenecks may appear equal at first glance, their true nature can vary significantly. To enhance maintenance and improve production activities, it’s crucial to identify these bottlenecks and understand their specific characteristics.
For instance, to expedite order shipments, it’s essential to discern whether your bottlenecks are tied to labour, technology, or processes. Insights drawn from machine data can help operations managers swiftly identify and diagnose bottlenecks, enabling timely decision-making for their resolution.
Inconsistent, poorly timed, incomplete, and redundant data can lead to inaccuracies, which can hinder effective management.
Plan and Forecast Maintenance to Mitigate Unexpected Losses
Unplanned machine downtime can create a substantial impact on profitability. Studies show that the average manufacturer experiences around 800 hours of downtime annually—equating to more than 15 hours per week—with costs potentially reaching $22,000 per minute of downtime. When this unplanned downtime recurs, the losses can be catastrophic.
Traditionally, demand estimation has been crucial in supply chain management, but businesses often respond to demand fluctuations by overstocking, leading to increased operational and storage costs.
Operations managers need to leverage data to develop intelligent algorithms for accurate planning and forecasting, ensuring achievable output and improvement potential. Enhanced demand forecasting can reduce costs, while machine learning facilitates real-time analytics, allowing supply chain management to be more efficient without missing out on demand.
Cultivate a Holistic View for Real-time Decision-Making
Abrupt bottlenecks anywhere along the production line can strain resources and challenge operations managers’ decision-making capabilities. The real challenge lies in ensuring that the data driving supply chain decisions is clean, relevant, and accurate.
To address this, decision-makers should strive to create a comprehensive view of all data sources, understanding how they integrate and interact within supply chain processes.
By harnessing real-time machine data and employing analytical techniques such as data visualization and root-cause analysis, these bottlenecks can be anticipated and targeted effectively.
Insights gained from these data application techniques can significantly enhance real-time decision-making. One practical step is to establish a centralized supply chain collaboration system that connects all enterprise systems into a unified network.
This approach ensures that KPIs and other essential data are readily accessible at all levels of supply chain operations, enabling quicker evaluations of the supply chain as a whole or in its individual components, all while maintaining high confidence in the accuracy and timeliness of the data.
Bottleneck in Supply Chain Management During the COVID-19 Pandemic
The economic challenges brought on by the pandemic have shown us the need to quickly find and fix problems in the supply chain. As we work to solve these issues, we often discover that fixing one bottleneck just leads to another.
Some major bottlenecks that have come up during the COVID-19 pandemic include:
- Travel restrictions that require different ways to transport goods.
- Closed or limited borders.
- Uneven distribution of shipping containers.
- Lack of cargo space at ports.
5 Examples of Bottlenecks in Supply Chain Management Disruptions
From production delays to having too much or too little stock, bottlenecks can cause you to lose time, money, and reputation, as well as affect product quality for you and your customers.
Typically, bottlenecks in the automotive supply chain happen due to a few main issues:
Unchecked Processes and Workflows
A company’s manufacturing process is the base for all workflows. Without careful monitoring of the entire process—from design to production to delivery—companies may face problems like:
- Product recalls
- Defects in final products
- Loss of customer trust
- Damage to brand reputation
One well-known example is the 2016 Toyota vehicle recall. Due to issues with faulty fuel tanks and airbags, Toyota had to recall 3.37 million cars, which cost the company a lot and hurt its brand image.
Although fixing and rechecking manufacturing processes can be expensive and take time, having quality checks can help avoid even bigger costs in the future.
Still trying to bounce back from recent global supply chain issues? Download “The Complete Guide to Supply Chain Optimization” to learn how to boost your efficiency.
Shortage of Skilled Workers
The pandemic created a shortage of skilled workers, including engineers and technicians, a problem that existed even before the pandemic. The ongoing shift to digital technology in the industry is a big reason for this shortage.
As technology changes, workers need to learn new skills. According to a Deloitte article, manufacturers might face a shortage of up to 2.1 million jobs between 2020 and 2030 if workers don’t adapt.
Old Machinery
New manufacturing equipment can be very costly, which often leads companies to put off buying it, even when it’s needed. However, using old machinery can lower product quality, increase service costs, and decrease productivity.
Modern machinery helps manufacturers design, test, and evaluate products to meet high standards. If buying new equipment isn’t an option, regular maintenance can help keep old machines running longer and prevent bottlenecks.
Lack of Automation and Technology
Automation in machines and software makes repetitive tasks easier with little human input. For example, robotic welding is an automated process that only needs a human-made plan to work, leading to more accurate parts.
Unfortunately, many companies still use manual processes that could be automated, making them prone to mistakes and slowing down production.
Poor Forecasting
Effective forecasting is essential for different parts of manufacturing, such as buying materials, managing stock, and mitigating risks. A common problem with forecasting happens when demand is miscalculated.
Having too much inventory might mean sales forecasts were too low while having too little suggests the opposite. The right automation software can improve forecasting by looking at past data, sales trends, and future needs, helping you keep the right amount of stock.
FAQ: Role of Bottleneck in Supply Chain Management
What are the advantages of bottlenecks?
Bottlenecks can highlight weaknesses in processes, prompting improvements. They also encourage efficient resource allocation, prioritize tasks, and foster teamwork, ultimately enhancing overall supply chain performance when addressed properly.
What causes bottlenecks in supply chain management?
Bottlenecks in supply chain management are often caused by inefficient processes, equipment failures, labour shortages, poor forecasting, and limited resources. External factors like transportation issues and demand fluctuations also contribute.
Can bottlenecks be fixed on a budget?
Yes, bottlenecks can often be addressed on a budget by optimizing existing processes, implementing regular maintenance, improving communication, training staff, and leveraging technology for better data analysis and forecasting.
Conclusion
Addressing bottleneck in supply chain management is essential for improving efficiency and profitability in the automotive industry. By adopting smart strategies and partnering with us at Qodenext, you can streamline your operations and create a smoother production flow! Strengthen your business with satisfied customers and a thriving business.