Imagine, you’ve just parked in your driveway after a grocery run. Now comes the decision:
Do you bring your bags in one by one or attempt to carry them all at once to save yourself multiple trips?
If you’re leaning toward carrying them all at once, you’ve already grasped the core concept of consolidation warehousing.
Consolidation services can be a smart move for retailers and e-commerce businesses aiming to streamline their supply chain logistics and reduce transportation costs. However, it’s crucial to balance the benefits with potential risks and ensure you have a solid plan for managing a consolidation warehouse.
In this article, we’ll explore consolidation warehousing, how to determine if it’s the right fit for your business and practical tips for implementing it within your supply chain strategy.
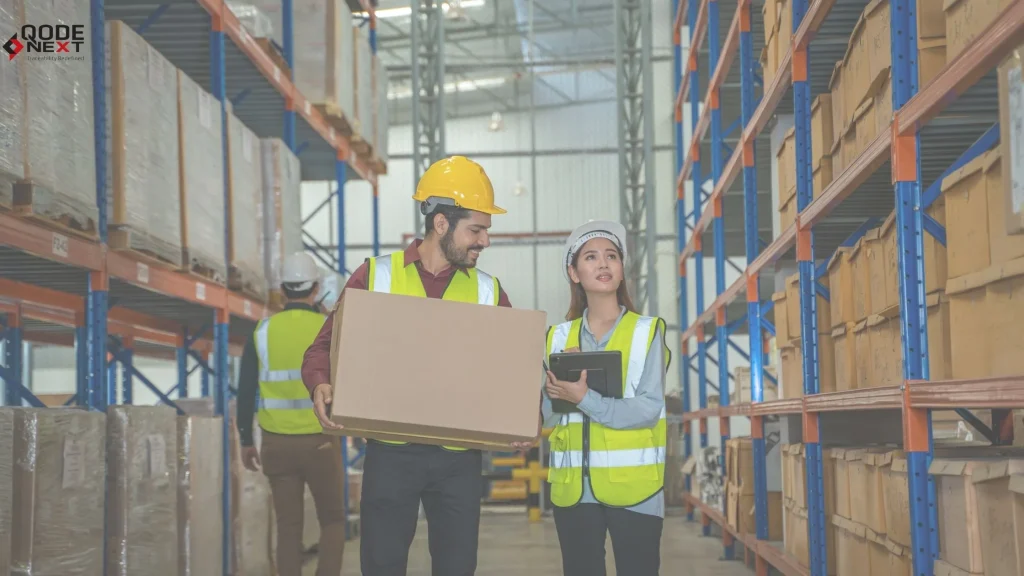
What is a Consolidation Warehouse?
A consolidation warehouse is a logistics facility designed to receive individual orders from various sources, such as other center’s, suppliers, or multiple customers, especially third-party logistics (3PL) providers. These orders are then grouped into larger shipments to streamline their transportation.
The consolidation process involves organizing and sorting the orders before they are shipped. This can be a straightforward task when dealing with full pallets, for instance, loading 33 pallets onto a single truck. However, when the unit load is in boxes and order volumes are high, the process becomes more intricate.
One of the key aims of load consolidation is to reduce transportation costs for each order. By combining multiple customers’ orders into a single shipment, the delivery expenses can be shared, allowing for full truckloads to be dispatched. This cost reduction is particularly beneficial for organizations with e-commerce channels, where customers often expect free or low-cost shipping.
With the growing prevalence of e-commerce and B2C channels, consolidation warehouses have become increasingly popular, especially in B2B sectors. Many 3PL providers now maintain consolidation warehouses near their distribution center’s, enabling them to efficiently group their clients’ orders by dispatch process or shipping route.
Consolidation Warehouse Process
Out of all the different types of warehouses, consolidation warehousing tasks take place in designated areas of the facility and are typically divided into the following stages:
Product Receipt and Sorting
In the warehouse’s docking areas, goods and materials arrive from various suppliers or customers. After verifying the accompanying documentation, items are sorted into a temporary storage zone.
Stock Storage
Once the goods are logged into the warehouse management system, operators store them according to predefined criteria and guidelines set by the logistics manager.
Product Handling
To prepare for distribution, the stock undergoes necessary processes such as weighing and packing.
Order Grouping
Goods are combined into a single batch to be dispatched as a consolidated shipment. This step also includes preparing documentation, detailing aspects like the orders and unit loads that make up the shipment.
Goods Dispatch
Once consolidated, the shipment is loaded onto the truck, either manually or automatically, for delivery to the next link in the supply chain or directly to the end customer.
The specific phases of the consolidation process can vary based on the type of warehouse, the nature of the products, and the number of orders included in the shipment.
Advantages and Disadvantages of Consolidation Warehouse
Consolidation warehousing is one of several ways to improve the supply chain. Here are some key benefits of applying best practices in warehouse consolidation:
Reduced Transportation Costs
By grouping loads together, companies can lower shipping expenses by sharing transportation costs across multiple shipments.
Improved Logistics Efficiency
Grouping orders helps increase the frequency of shipments and the number of shipping routes. It also leads to better customer service by improving the delivery process.
Optimized Storage Space
Load consolidation allows for more frequent shipments, meaning less stock is stored in the warehouse, freeing up space for other uses.
However, one of the main challenges of warehouse consolidation is the need for precise coordination between suppliers and transportation companies. Managing the high volume of orders from different customers makes this task complex.
To prevent errors, companies using warehouse consolidation need to invest more time in logistics planning, ensuring smooth coordination across all operations.
Automating a Consolidation Warehouse
The rapid expansion of e-commerce has significantly complicated order consolidation processes. This has pushed many companies to adopt industrial processes and technological automation in their warehouses and . The first step towards automating logistics facilities is often the implementation of a warehouse management system (WMS) to synchronize operations and maintain tight control over goods. Consolidation warehouses typically handle large volumes of SKUs and recipients, so a WMS plays a crucial role in real-time monitoring, guiding operators through each step based on order requirements.
Once a WMS is in place, the next phase involves analyzing which processes can be automated. In warehouses with high order density or continuous goods flow, automation is often introduced to reduce costs, streamline processes, and boost overall efficiency. Depending on the scale of operations, partial or full automation may be employed.
A key automation tool in some facilities is an automated storage and retrieval system (AS/RS), which manages the storage and dispatch of goods. AS/RS systems ensure that orders are stored, sequenced, and dispatched at the right time, contributing to smoother consolidation and shipping processes.
Another popular automation solution involves replacing manual handling equipment with roller conveyors for boxes. These conveyors continuously supply consolidation stations with stock, ensuring that goods move efficiently through the facility.
Conveyor systems can connect different areas of a warehouse, automating the supply of goods to consolidation, sorting, and dispatch zones, making the process faster and more reliable.
By automating these critical areas, businesses can achieve greater speed, accuracy, and cost-effectiveness in their logistics operations.
FAQ: Consolidation Warehouse: Role, Pros, Cons, and More
Are there any consolidation warehouse benefits?
Consolidation warehouses reduce shipping costs by combining multiple orders into one shipment, streamlining operations, enhancing delivery efficiency, and minimizing storage space requirements while optimizing supply chain management.
How to stock the inventory of a consolidation warehouse?
Inventory in a consolidation warehouse is stocked by organizing products based on demand and shipping schedules, often using a warehouse management system to track and guide inventory placement and movement.
What is the difference between consolidation and a traditional warehouse?
A consolidation warehouse focuses on combining orders for efficient shipping, while a traditional warehouse primarily stores products without prioritizing order combination or shipment optimization.
Conclusion
A consolidation warehouse can be a game-changer for businesses aiming to cut shipping costs and make their supply chain more efficient. By embracing automation, you can simplify operations and boost productivity. For reliable solutions and support, Qodenext can help guide you through your warehouse automation journey with ease.