In pharmaceuticals, food production, and various industries, product safety and quality are paramount. This pursuit led to establishing Good Manufacturing Practices (GMP), a set of principles designed to uphold stringent quality standards throughout manufacturing.
These GMP principles encompass a range of guidelines that address aspects such as cleanliness, personnel training, equipment maintenance, and documentation. This blog delves into the significance of GMP principles in maintaining the integrity of products, safeguarding consumer welfare, and fostering trust in various sectors.

What Are GMP Principles ?
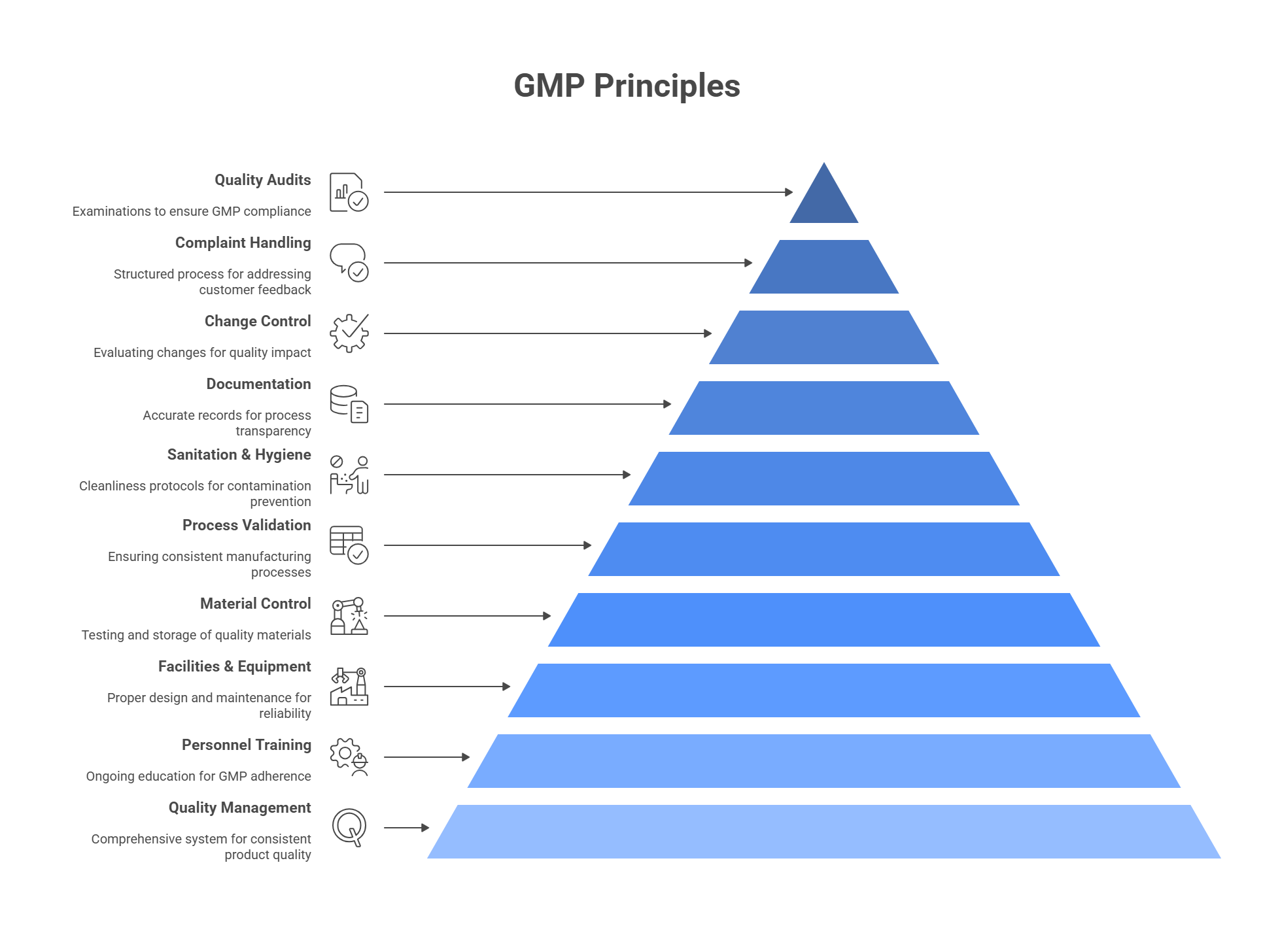
Good Manufacturing Practices (GMP) encompass principles and directives to guarantee the quality, safety, and effectiveness of pharmaceutical, food, and cosmetic items throughout their manufacturing, processing, packaging, and storage phases. These protocols are critical in upholding uniform, top-notch products that align with regulatory requisites and consumer anticipations. Some of the critical features of GMP principles include :
- Quality Management
Quality is not just an end product; it’s integrated throughout the entire manufacturing process. A comprehensive Quality Management System (QMS) governs every aspect of production. This includes establishing quality control procedures, setting specifications for raw materials and finished products, and ensuring that deviations from these standards are thoroughly investigated and addressed. A robust QMS guarantees that products consistently meet the intended quality attributes and regulatory requirements.
- Personnel Training
Training extends beyond initial orientation. It’s an ongoing process that ensures employees understand their tasks and the underlying principles of GMP manufacturing usage. Regular training sessions cover areas like Good Documentation Practices (GDP), hygiene practices, contamination prevention, and safety protocols. Well-informed employees are more likely to adhere to GMP standards and identify potential issues early.
- Facilities and Equipment
Good manufacturing practices guidelines specifiy facility design, layout, and maintenance requirements. Adequate space and ventilation prevent cross-contamination and maintain segregation of different production steps. Equipment used in manufacturing is calibrated, validated, and routinely maintained to ensure accurate and reliable results. Regular checks and maintenance schedules prevent equipment-related issues that could compromise product quality.
- Material Control
Ensuring the quality of incoming materials is a cornerstone of GMP. Raw materials are thoroughly tested, and sampling protocols are established to verify their conformity to established standards. Materials are properly stored, labeled, and tracked to avoid mix-ups. A traceable record of material usage is maintained to ensure only approved materials are used.
- Process Validation
GMP requires the validation of manufacturing processes and ongoing monitoring to ensure consistency. Process validation involves defining critical process parameters, conducting experiments, and analyzing data to establish that the operation can consistently yield products meeting predetermined specifications. Continuous process verification confirms that the process remains in control.
- Sanitation and Hygiene
The importance of cleanliness cannot be overstated in GMP. Sanitization protocols cover both personnel and facilities. Individuals must follow stringent hygiene protocols, which encompass wearing suitable attire and proper handwashing procedures. Regular cleaning and sanitization of facilities and equipment are carried out, and established measures are in a position to inhibit the proliferation of microorganisms and uphold the prevention of contamination.
- Documentation
Documentation is the backbone of GMP. Detailed and accurate records provide a transparent view of the entire manufacturing process. Batch records document every step, ensuring that processes are followed correctly. Deviations, investigations, and corrective actions are thoroughly documented, creating an auditable trail of the product’s journey from raw material to finished product.
- Change Control
Any changes to processes, equipment, or materials must be evaluated for their potential impact on product quality. Change control procedures involve risk assessment, testing, and documentation. This ensures that changes are controlled, authorized, and communicated to relevant parties. The goal is to prevent unintended consequences that could affect product quality.
- Complaint Handling
Complaints are valuable feedback mechanisms. GMP dictates that companies have a structured process for capturing, investigating, and addressing customer complaints. Complaints are tracked and tended to identify potential systemic issues. A thorough investigation helps determine whether the issue is a one-time occurrence or indicative of a more significant problem that requires corrective action.
- Quality Audits
Audits are thorough examinations of the manufacturing process to ensure compliance with GMP. Internal audits assess the company’s practices, identifying areas for improvement. External audits by regulatory agencies or third-party organizations confirm adherence to standards. Audits help maintain GMP standards, provide insights for process optimization, and demonstrate commitment to quality to regulatory authorities.
By embracing these GMP principles in a comprehensive and detailed manner, manufacturers can consistently produce high-quality products that meet regulatory requirements and consumer expectations.
Examples of GMP Practices
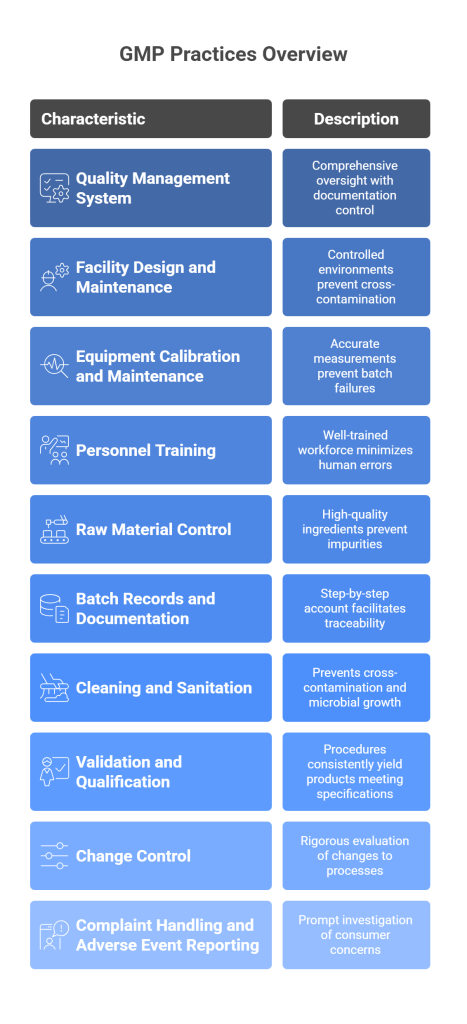
Good Manufacturing Practices (GMP) principles are essential guidelines that ensure product quality, safety, and consistency in the manufacturing process. These principles minimize risks and ensure that products meet predetermined quality standards. GMP practices encompass a wide range of activities, and here are the examples that highlight their importance:
- Quality Management System (QMS)
GMP emphasizes the establishment of a robust QMS that oversees every aspect of manufacturing. This includes comprehensive documentation control to ensure that all processes are well-documented and consistently followed. Change management protocols are crucial to assess and control any modifications to procedures, preventing unauthorized changes that could compromise product quality.
- Facility Design and Maintenance
GMP-compliant facilities are designed with careful consideration of the manufacturing processes. Cleanrooms, controlled environments, and adequate spacing between production areas are integral to preventing cross-contamination. Temperature, humidity, and pressure controls are implemented to maintain optimal conditions for product stability.
- Equipment Calibration and Maintenance
Regular calibration and maintenance of manufacturing equipment are essential to ensure that measurements and operations remain accurate. Deviations due to equipment inaccuracies can lead to batch failures, production delays, and compromised product quality.
- Personnel Training
GMP requires comprehensive training for all personnel involved in the manufacturing process. This training covers GMP principles, procedures, hygiene practices, and safety protocols. A well-trained workforce minimizes the risk of human errors that can lead to product defects.
- Raw Material Control
Rigorous control over raw materials ensures that only approved, high-quality ingredients are used. Thorough testing and qualification of raw materials prevent the introduction of impurities or substandard components that might jeopardize the final product’s integrity.
- Batch Records and Documentation
Detailed and accurate batch records provide a step-by-step account of the manufacturing process, including the use of specific materials, equipment settings, and production times. These records facilitate traceability and aid in investigating any deviations from expected outcomes.
- Cleaning and Sanitation
GMP mandates stringent cleaning and sanitation protocols to prevent cross-contamination and microbial growth. Dedicated procedures for cleaning equipment, surfaces, and production areas reduce the risk of introducing contaminants into the manufacturing process.
- Validation and Qualification
Process validation ensures that manufacturing procedures consistently yield products meeting predetermined specifications. Equipment qualification involves verifying that manufacturing equipment is properly installed, operates as intended, and maintains desired performance standards.
- Change Control
Changes to manufacturing processes, equipment, or procedures must undergo rigorous evaluation through a documented change control process. This process assesses potential impacts on product quality, safety, and efficacy before changes are implemented.
- Complaint Handling and Adverse Event Reporting
Effective complaint handling mechanisms enable prompt investigation of consumer concerns and product issues. Adverse event reporting is vital for tracking and assessing any unexpected adverse effects associated with product use, contributing to continuous product improvement and patient safety.
By incorporating these key features, GMP ensures that manufacturers adhere to standardized practices that safeguard consumer health, maintain product efficacy, and uphold the reputation of the industry. GMP principles serve as a foundation for regulatory compliance and reinforce the commitment to producing safe, reliable, and high-quality products.
Conclusion
Incorporating Good Manufacturing Practices (GMP) principles is not just a regulatory requirement but a pivotal commitment to ensuring pharmaceutical products’ safety, quality, and efficacy.
These principles encompass every facet of production, from raw materials to the final product, fostering industry integrity and safeguarding consumer well-being. As we’ve explored the significance of GMP principles in this blog, it’s evident that strict adherence is paramount.
For businesses seeking a seamless transition into GMP compliance, Qodenext stands as an invaluable partner. With their expertise in quality management systems and regulatory compliance, Qodenext empowers pharmaceutical companies to navigate the intricacies of GMP principles effectively. Take a step towards excellence; embrace GMP with Qodenext today.
FAQ’s – Good Manufacturing Practices (GMP) Principles
1. What are GMP manufacturing practices?
Good Manufacturing Practices, or GMP, are a set of quality assurance principles that ensure products like medicines, food, and cosmetics are consistently produced and controlled. These practices make sure that every product is safe, effective, and of the highest quality. They guide how companies handle raw materials, equipment, processes, and documentation to prevent errors, contamination, or mix-ups.
2. What are the key components of GMP?
The core elements of GMP include a strong quality management system, proper hygiene and sanitation, accurate documentation, validated manufacturing processes, trained personnel, well-maintained equipment, controlled environments, and systems for handling complaints or recalls. These components work together to ensure that products are consistently made to high standards.
3. Why is GMP so important in industries like pharmaceuticals and food?
GMP is crucial in these industries because they deal with products that directly impact people’s health and safety. A small mistake in manufacturing could lead to serious consequences. By following GMP, companies reduce the risk of contamination, defects, or incorrect labeling. It builds consumer trust and ensures compliance with health regulations.
4. How is GMP different from other quality standards like ISO?
GMP and ISO both aim for high product quality, but GMP is often mandatory and more focused on public health. It includes stricter controls on hygiene, cleanliness, and process validation. ISO standards, such as ISO 9001, are broader and more about general quality management, while GMP is specific to industries like pharma, biotech, and food.
5. What kind of documentation does GMP require?
GMP requires detailed and accurate documentation at every stage of manufacturing. This includes batch records, cleaning logs, calibration records, SOPs (Standard Operating Procedures), and training logs. These documents serve as proof that the correct procedures were followed and help track down the root cause if something goes wrong.
6. How often should employees be trained in GMP?
GMP training should be conducted when employees are first hired and regularly afterward—typically once or twice a year. Additional training is needed whenever new equipment, procedures, or regulations are introduced. This keeps everyone up to date and ensures that tasks are performed correctly and safely.
7. What is process validation and why does it matter?
Process validation confirms that a manufacturing process consistently produces the desired result. Before production starts, the process is tested and evaluated to ensure it meets all specifications. Ongoing validation helps maintain product quality and prevents issues from reaching the customer.
8. How do GMP audits work?
GMP audits are inspections carried out by internal teams or external authorities to check compliance with GMP standards. Auditors review records, inspect facilities, interview staff, and evaluate processes. If non-compliance is found, corrective actions must be taken. Regular audits are essential for staying compliant and ready for regulatory reviews.
9. What are some common mistakes or violations in GMP?
Common violations include incomplete or missing documentation, poor cleanliness, untrained staff, failure to investigate customer complaints, and not following validated procedures. These issues can lead to warnings, fines, or production halts. Avoiding them requires a strong quality culture and continuous oversight.
10. How can a company like Qodenext help with GMP compliance?
Qodenext supports companies with automation and technology solutions that simplify GMP compliance. Their systems help maintain traceability, ensure accurate labeling, manage inventory, and digitize records. By working with Qodenext, businesses can streamline their processes, reduce human error, and stay audit-ready at all times.