Efficient order fulfillment is undoubtedly the backbone of a successful business. Amongst the various processes within the bustling warehouse, some processes, such as order picking, stand as the fundamental process.
But what is warehouse order picking? Why is it necessary? What makes it such an important component of supply chain management? This comprehensive guide is to help you explore all the crucial details which you must know about warehouse order picking. Let’s get started!

What Is Warehousing Order Picking?
As the name suggests, warehouse order picking refers to pulling and selecting the products ordered by customers from the warehouse. The warehouse is the heart of the entire supply chain. While the warehouse is flooded with different varieties of products in enormous amounts, the supply chain is flooded with orders received from customers.
This process is a pivotal step of the entire supply chain because it involves retrieving the right order from the right storage location among all warehouse operations. Once the orders are received from the customers, it’s first organized and processed on the basis of their priorities and estimated delivery deadlines.
Order picking is closely tied to other warehouse processes, such as putaway, where products are stored in optimal locations for easy retrieval, and warehouse rack labelling, which ensures pickers can quickly locate items. Then, these orders are picked at the right time and further processed until they reach the customers. It’s the initial step of order fulfillment and directly impacts customer satisfaction and the overall effectiveness of the warehouse operations.
Various Methods of Warehouse Order Picking
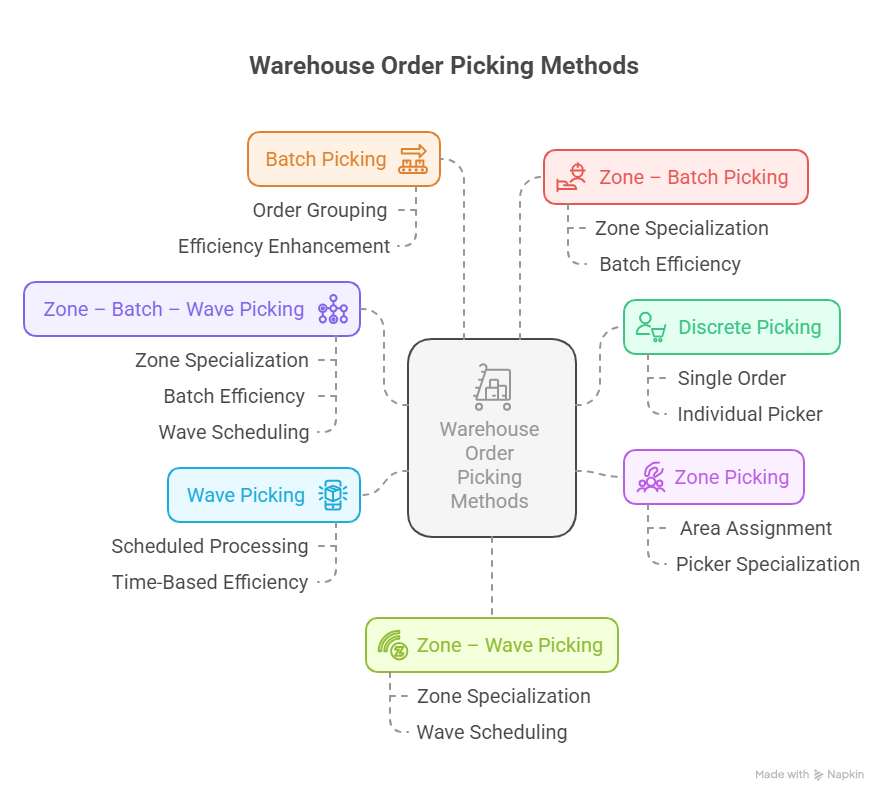
Warehouse order picking methods is a hectic process demanding time, effort, and care. A slight mistake can create a lot of havoc, thus leading to negative customer feedback. Here are various ways of warehouse order picking, which make the cumbersome process systematic and organized.
1. Discrete Picking
Also known as single order picking, this manual order picking method is ideal for warehouses which are either small or have low order volume. In this method, one order is picked up at a time. It’s time-consuming yet easy to do. However, it’s the most preferred warehouse order-picking method.
2. Zone Picking
As simple as it sounds, zone picking involves pickers being assigned to a particular part of the warehouse. It’s mostly used in large warehouses with a wide variety of products. This method divides the entire warehouse into small zones, and a picker is assigned specifically to each zone. The picker is solely responsible for picking orders within that specific zone only.
This method is known to improve the productivity and efficiency of pickers by minimizing congestion and reducing the workload to only one specific zone.
3. Wave Picking
In this process, all the orders are organized and categorized into waves based on their scheduled routine. Items within a particular wave have some common factors, such as shipping dates, items, warehouse zone, customer, etc.
Each wave is allowed a picker. It allows simultaneous picking for multiple orders, improving efficiency and reducing redundant travel.
4. Batch Picking
In this method, multiple orders with similar items are grouped together. The orders are batched on the basis of common factors such as similar SKUs, product type, or customer. Pickers fulfill all the orders simultaneously, optimizing the picking route and reducing travel time.
Besides being effective and efficient, it’s also budget-friendly as it reduces the costs associated with labor and other related operations.
5. Zone – Batch Picking
This hybrid warehouse order-picking process is a combination of zone and batch-picking methods. Much like zone picking, it involves the division of the warehouse into zones comprising a particular category of orders. However, in the picking process, pickers process a batch of similar orders at the same time by picking the same SKU for multiple orders simultaneously.
6. Zone – Wave Picking
The zone-wave picking method involves pickers responsible for picking specific items during each wave within a particular warehouse zone. It’s ideal for large warehouses with significantly high and diverse product varieties and receiving enormous orders.
7. Zone – Batch – Wave Picking
Wave picking Combining the benefits of the three most popular warehouse order-picking processes, this is an advanced method of picking up multiple orders from an organized warehouse quickly and accurately.
Imagine the warehouse is divided into different areas, or “zones,” and each zone has its own picker. Instead of picking one order at a time, the picker grabs items for several orders, like putting them into groups, known as “batches.”
Then, these batches are picked during specific time intervals called “waves.” This method helps save time and makes order picking more efficient, as the picker stays in their assigned zone, gathers items for multiple orders at once, and follows a schedule to get things done faster.
Should You Go for an Automated Warehouse Picking System?
All the above-discussed warehouse order-picking methods are manual. This means that they are time-consuming and demand manual labor. Well, do you think today’s technological innovations can also automate this cumbersome task?
Well, here is where an automated warehouse order-picking system comes into the picture. But what is it?
An automated warehouse order-picking system is a business solution that automates the order-picking process within a warehouse with the help of robotics, conveyor systems, sensors, and software. It reduces human labor and maximizes efficiency and accuracy. Automation also integrates seamlessly with broader warehouse operations and can significantly increase warehouse capacity without expanding your physical footprint.
Now, what benefits does this automation bring over manual warehouse order-picking methods? Here’s a list of the benefits it offers.
- Starting off with the speed, it’s no doubt that automated systems work way faster than humans. It’s because automated systems can work around the clock without fatigue and breaks. This, in turn, reduces the time taken for order fulfillment which ultimately improves customer satisfaction.
- The accuracy of automated systems with robots is quite high. Automating the warehouse order-picking process reduces the errors that come along with human labor.
- Automated systems can make better use of vertical space in the warehouse setup, allowing for higher-density storage and potentially reducing the overall warehouse footprint.
- The best part about automated warehouse picking systems is that they are flexible and versatile. Users can easily scale it up or down according to their business needs.
- With automation handling heavy lifting and repetitive tasks, the risk of employee injuries due to manual handling is reduced, creating a safer work environment.
Thus, automating the warehouse order-picking process is a great way to maximize productivity, efficiency, and accuracy while reducing manual labor and the chances of errors and injuries associated with it.
Do you want to revolutionize warehouse operations by automating the order-picking process? Worry not because we bring you QodeNEXT and its unique solutions, which are tailored to meet your unique needs, thus taking your business’s productivity and efficiency to the next level. Unlock the full potential of your business with QodeNEXT’s comprehensive suite of hardware and software solutions. Go check out QodeNEXT’s services now!
FAQs: Picking Process in Warehouse
1. What is warehousing order picking?
Warehouse order picking refers to the process of pulling, selecting the products ordered by customers from the warehouse.
2. What are the various methods of warehousing order picking?
There are 7 most common methods of warehousing order picking, namely, discrete picking, zone picking, wave picking, batch picking, zone- batch picking, zone – wave picking, zone – batch – wave picking.
3. What is batch picking?
In the batch-picking method, multiple orders with similar items are grouped together. The orders are batched on the basis of common factors such as similar SKUs, product type, or customer. Pickers fulfill all the orders simultaneously, optimizing the picking route and reducing travel time.
4. What is discrete picking?
Also known as single order picking, discrete picking is a manual order picking method that is ideal for warehouses which are either small or have low order volume.
5. What is an automated warehouse picking system?
An automated warehouse order-picking system is a business solution that automates the order-picking process within a warehouse with the help of robotics, conveyor systems, sensors, and software.
6. What factors should be considered when choosing a picking method?
When selecting a warehouse picking method, consider factors such as order volume, product characteristics, warehouse layout, and workforce skills. The right method should align with your business goals and operational requirements. Consulting with industry experts can also help ensure you make the optimal choice for your facility.
7. How does warehouse order picking impact customer satisfaction?
The accuracy and speed of the picking process directly influence how quickly and correctly customers receive their orders. Errors or delays in picking can lead to incorrect shipments and late deliveries, resulting in negative customer feedback. Efficient picking processes help maintain high service levels and improve overall customer satisfaction.
8.What are the main challenges in manual warehouse picking?
Manual picking can be time-consuming and physically demanding, often leading to fatigue and errors. Workers may need to travel long distances within the warehouse, increasing the risk of mistakes and injuries. Additionally, as order volumes grow, manual processes may struggle to keep up with demand, impacting efficiency.
9.How does automation improve the warehouse picking process?
Automation introduces robotics, conveyor systems, and intelligent software to handle repetitive and heavy tasks. This leads to faster order fulfillment, higher accuracy, and reduced labor costs. Automated systems can also operate continuously without fatigue, making them ideal for high-volume operations.
Wrapping Up
Warehouse order picking is the crucial and most intricate process which directly impacts order fulfillment. While a variety of methods are available for doing the same, it’s also important to choose the right one suited to your business and warehouse needs.
Before choosing any method, make sure to count for factors such as order volume, product characteristics, warehouse layout, and workforce skills. You may also consult experts to help you choose the best one.
If you still feel stuck or want to get started on exploring any of these amazing technologies, get in touch with us at QodeNEXT now! We are here to help you make the best choice to manage your fleet and optimize your process!