Does your business use an inventory management system?
Are you always sure to have the right products on hand when needed?
For any business, keeping track of inventory, updating records, and analyzing the data to monitor profits, needs, and sales is crucial. For small businesses, having an effective inventory management system can be a game-changer in staying on top of sales and demand.
Are you losing sales because items are out of stock?
Are you wasting money on excess inventory?
An inventory management system helps you keep a tight rein on your supply, allowing you to optimize inventory levels and manage them efficiently, saving both time and money.
Regular evaluation of your inventory management practices is key to ensuring your business stays on the right track for success.
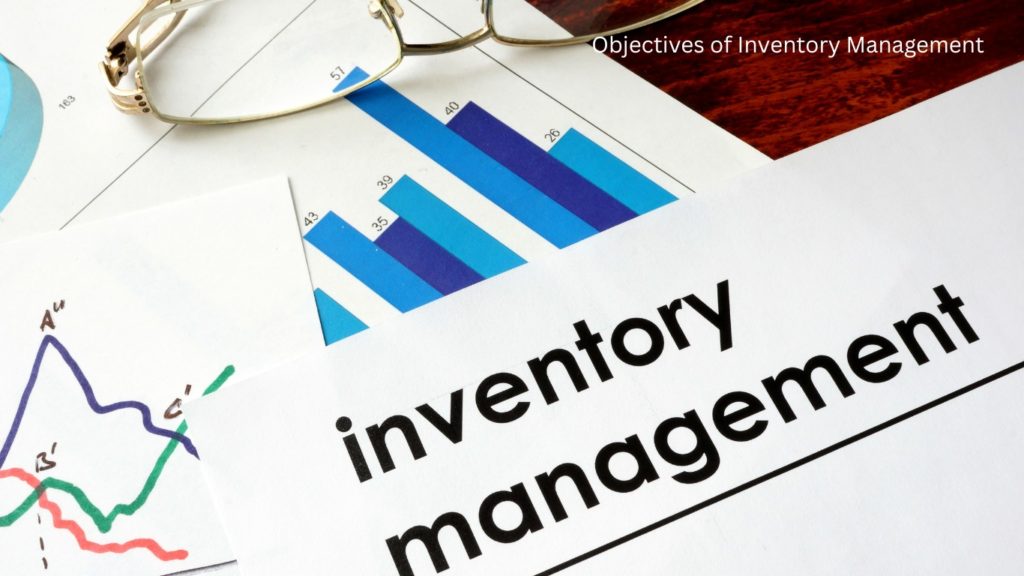
What is Inventory Management?
Inventory management is a method for systematically organizing and handling goods, inventories, and noncapitalized assets based on their type and placement.
Inventory refers to any item a business holds for resale or repair.
Effective inventory management encompasses ordering, storing, and utilizing stock. This includes sourcing raw materials, components, and finished products, as well as managing their warehousing and processing within the company.
Before inventory can be recorded on the balance sheet, it must be physically counted to ensure accuracy.
Objectives of Inventory Management
Operational and financial goals are important when managing inventory. The operational goal is to keep enough inventory on hand to meet customer demand, while the financial goal is to reduce extra stock and unnecessary costs.
To achieve these goals, inventory management helps streamline operations. Some key reasons for using an inventory management system are:
Making Sure Materials Are Available
The primary purpose of inventory management is to ensure all necessary materials are available when the production team needs them. This prevents production delays or slowdowns caused by missing supplies. Keeping extra stock of important items ensures smooth operations.
Improving Customer Service
Without a proper count of what’s in stock, fulfilling orders can be challenging. To meet customer demands, the right products must be available at the right time. Maintaining enough finished products ensures timely order fulfillment, enhancing the company’s reputation.
Reducing Wastage and Loss
Inventory management helps prevent loss due to misplaced or wasted items and reduces the risk of theft. Keeping track of goods minimizes the chances of loss and waste, especially when handling large quantities. The goal is to keep waste within acceptable levels, whether during storage or production.
Keeping Enough Stock
From raw materials to finished products, having enough stock ensures that customer orders are met without compromise. This steady supply means the production team doesn’t have to worry about running out of essentials.
Saving on Storage Costs
Managing inventory control levels carefully avoids overstocking, which reduces unnecessary storage costs. When too much stock is ordered without a clear need, companies may end up paying for extra storage space that isn’t necessary.
This not only increases the cost of storing the goods but can also lead to waste if items expire or become obsolete before they are used or sold. By carefully managing inventory levels, businesses can reduce the amount of unnecessary stock, ensuring they have just enough to meet demand without paying for excess storage.
Inventory management systems help forecast future demand based on past sales, enabling companies to order the right amount of stock and avoid piling up unused items. This minimizes expenses related to warehouse space, utilities, insurance, and other costs associated with storing extra inventory.
Additionally, efficient storage management also ensures that goods are well-organized and easily accessible, saving which and labor. Proper labeling and tracking of products can reduce the time spent searching for items and lower the chance of misplaced goods, further enhancing overall efficiency.
Lowering Inventory Costs
Regular purchases can help businesses secure discounts or other benefits, reducing the overall cost of goods. When companies purchase inventory in bulk or on a regular basis, they can often negotiate better prices with suppliers. Suppliers may offer discounts, lower shipping costs, or provide other incentives for larger orders or long-term purchasing agreements.
This allows companies to reduce their per-unit cost, which in turn improves profit margins. Additionally, by analyzing sales data, businesses can optimize their purchasing schedules. Instead ofRather than buying stock when it’s running low, companies can plan ahead and take advantage of seasonal discounts, promotions, or bulk purchase opportunities.
Having a well-organized inventory management system means that businesses can order only what they need when they need it, preventing them from tying up money in excess stock that sits unused for long periods.
Moreover, managing inventory properly reduces the risks of over-ordering or under-ordering, both of which can be costly. Over-ordering results in unnecessary storage and potential waste, while under-ordering can lead to stockouts, forcing businesses to rush orders at higher prices or risk losing sales.
Boosting Sales
Inventory management also helps track product sales. By analyzing sales trends, businesses can identify slow-moving items and remove them, optimizing product offerings for better performance.
By monitoringkeeping track of inventory levels, businesses can analyze which products are selling well and which are moving slowly. This information allows businesses to make informed decisions about restocking, promotional efforts, and discontinuing underperforming items.
Proper inventory planning also allows businesses to avoid stockouts, which can result in missed sales opportunities and damage customer loyalty if their needs aren’t met promptly.
Types of Inventory Management Techniques
Just-in-Time (JIT)
Just-in-time means companies only order what they need when they need it, so they don’t have to store a lot of extra stuff.
Benefits: JIT helps save money on storage because you don’t need big warehouses. It also reduces waste and keeps cash free for other things.
Example: Toyota uses JIT for car production. They make cars based on real orders, so they don’t have too many extra cars sitting around, saving. This saves them a lot of money.
Challenges: JIT needs everything to run smoothly. If there’s a delay in getting supplies or a sudden change in demand, it can cause significant issues.
ABC Analysis
ABC Analysis divides inventory into three groups. ‘A’ items are expensive but sell slowly. ‘B’ items are in the middle, and ‘C’ items are cheap but sell fast.
Benefits: This method helps companies focus on important items without losing track of the smaller ones, . It making stock management stock easier.
Example: In pharmacies, expensive ‘A’ drugs don’t sell as often but are essential to have on hand. Therefore, they ensure these are always in stock.
Challenges: You need to keep an eye on how things change. Over time, sales patterns and the value of products may shift.
(First-In, First-Out)
FIFO means using or selling the oldest stock first, which is perfect for items that can go bad.
Example: Grocery stores use FIFO for things like fruits and veggies. This way, they sell older items first, so nothing spoils.
Benefits: FIFO is great for reducing waste, It ensuring that products are used or sold before they expire.
Challenges: When prices are rising, using FIFO could lead to higher taxes, as you’re selling the cheaper, older stock first.
FAQ: Objectives of Inventory Management: Complete Guide:
What are the limitations of inventory management?
It can be limited by inaccurate demand forecasting, high storage costs, stockouts, excess inventory, and complex supply chain dynamics, leading to inefficiencies and lost sales.
Can inventories be managed in the ABC analysis under a budget ?
Yes, ABC analysis can be applied under a budget by prioritizing high-value items (A category) for closer monitoring, while less critical items (B and C) receive proportionate attention.
How can inventory levels be maintained?
They can be maintained through regular monitoring, accurate demand forecasting, timely reordering, safety stock maintenance, and adopting technology like ERP systems for real-time inventory tracking.
Conclusion
Understanding the objectives of inventory management is crucial for optimizing stock levels, reducing waste, and boosting profitability. By implementing the right strategies, businesses can meet customer demand while minimizing costs. For advanced inventory solutions, maybe consider Qodenext! We have innovative tools to streamline processes, ensuring efficient and profitable operations.