Have you ever wondered how those giant cement trucks that dot the Indian highways manage to transport millions of tons of cement to construction sites all over the country? The answer lies in the complex logistics management system that keeps the Indian cement industry running.
Logistics management is a critical concern for the industry, with the Indian cement market projected to reach 485.2 million metric tons by 2025. From raw material procurement to finished product delivery, logistics management is vital to the success of cement manufacturers.
However, with challenges such as fluctuating demand, supply chain disruptions, and transportation issues, logistics management can be a daunting task.
In this blog, we’ll explore some of the most significant logistics management challenges faced by the Indian cement industry and how a robust logistics management system can help cement manufacturers overcome these obstacles.
Let’s dive into the world of cement logistics management and discover how the industry is meeting these challenges head-on.

The Logistics Conundrum: Challenges Faced by the Cement Industry
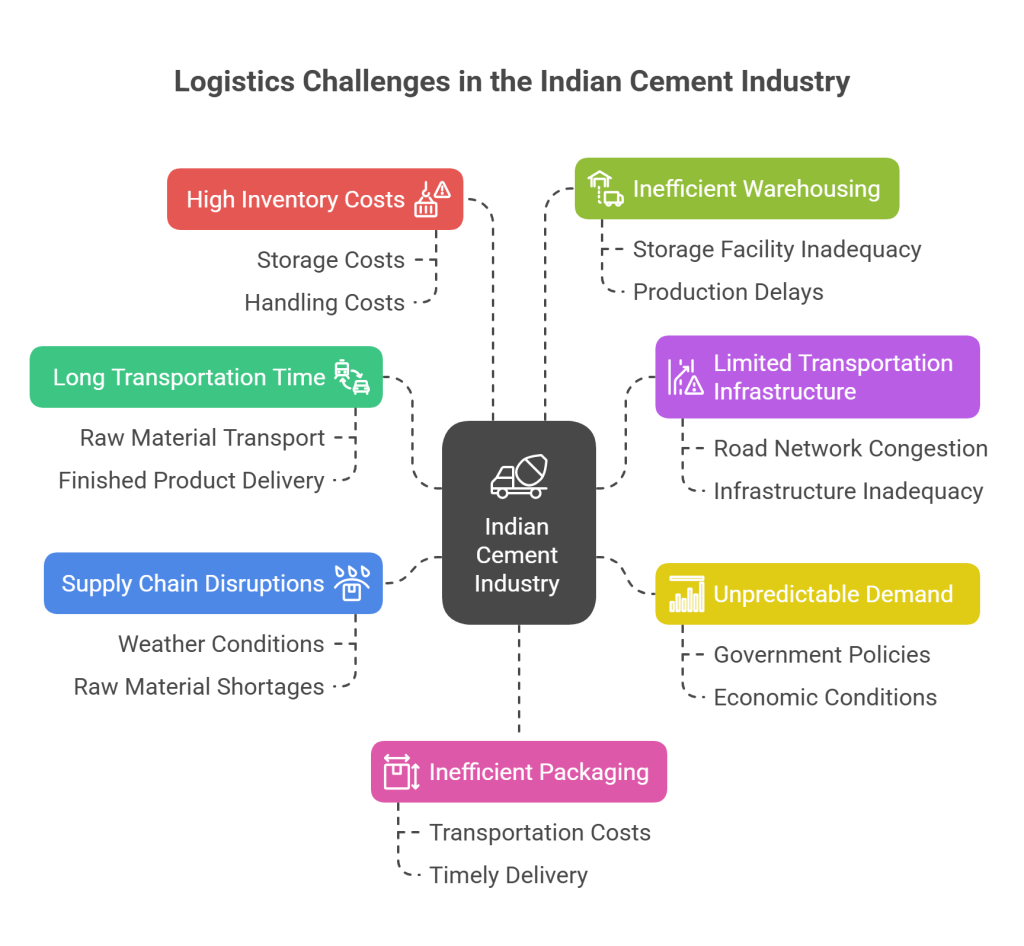
Producing over 500 million metric tons of cement per year, the Indian cement industry is one of the largest cement industries in the world.
However, the industry faces several challenges that can hinder its logistics operations. Let’s take a closer look at some of the most significant logistics management challenges faced by the Indian cement industry and discuss potential solutions.
Challenge 1: Long Transportation Time
One of the most significant logistics management challenges faced by the Indian cement industry is the long transportation time.
Cement manufacturers need to transport raw materials, such as limestone and gypsum, from mines to production plants and then transport finished products to construction sites. India’s inadequate and congested transportation infrastructure is often leading to a long transit time and higher transportation costs.
Case Study: ACC Limited
ACC Limited, one of India’s largest cement manufacturers, tackled this challenge by optimizing its logistics operations. The company implemented a fleet management system that enabled real-time tracking of vehicles and improved vehicle routing.
As a result, ACC Limited was able to reduce transit times and transportation costs.
Solutions:
- Implement a fleet management system for real-time tracking and improved vehicle routing.
- Invest in transportation infrastructure, such as better roads and rail networks, to reduce transit times.
Challenge 2: Limited Transportation Infrastructure
Another significant challenge faced by the Indian cement industry is limited transportation infrastructure. The industry relies heavily on road transportation, but India’s road network is often inadequate and congested, leading to delays and higher transportation costs.
Case Study: UltraTech Cement
UltraTech Cement, another renowned cement manufacturer in India, addressed this challenge by investing in alternative transportation methods. The company started using inland waterways to transport cement to customers, reducing transit times and transportation costs.
Solutions:
- Invest in alternative transportation methods, such as inland waterways and railways, to reduce reliance on roads.
- Work with the government to improve transportation infrastructure, such as building better roads and expanding rail networks.
Challenge 3: Unpredictable Demand
The Indian cement industry faces unpredictable demand, with the demand varying across regions and changing rapidly due to factors such as government policies and economic conditions. This unpredictability can make it challenging for cement manufacturers to plan their logistics operations effectively.
Case Study: Dalmia Bharat Cement
Dalmia Bharat Cement, a pre-eminent cement manufacturer, addressed this challenge by implementing a demand planning system. The company used data analytics to forecast demand and plan its logistics operations accordingly, reducing transportation costs and improving customer service.
Solutions:
- Implement a demand planning system using data analytics to forecast demand.
- Build a flexible supply chain that can quickly adapt to changes in demand.
Challenge 4: Supply Chain Disruptions
The Indian cement industry faces supply chain disruptions due to factors such as weather conditions, raw material shortages, and transportation delays. These disruptions can lead to production delays and higher costs.
Case Study: Ambuja Cement
Ambuja Cement, the most illustrious cement provider addressed this challenge by implementing a risk management system. The company used a data-driven approach to identify potential supply chain disruptions and developed contingency plans to mitigate their impact.
Solutions:
- Implement a risk management system using data analytics to identify potential disruptions.
- Develop contingency plans to mitigate the impact of disruptions on production and logistics operations.
Challenge 5: High Inventory Costs
Cement manufacturers need to maintain a high level of inventory to meet customer demand. However, maintaining inventory comes with significant costs, including storage, transportation, and handling.
Case Study: Shree Cement
To tackle this challenge, Shree Cement, a top cement manufacturer in India, adopted a just-in-time (JIT) inventory system. The company reduced its inventory levels by maintaining a steady flow of raw materials and finished products, reducing inventory costs, and improving operational efficiency.
Solutions:
- Implement a JIT inventory system to reduce inventory levels and costs.
- Optimize production processes to reduce waste and improve efficiency, leading to lower inventory requirements.
Challenge 6: Inefficient Warehousing
The Indian cement industry also faces challenges with inefficient warehousing. Cement manufacturers need to store large quantities of raw materials and finished products in warehouses, but inadequate storage facilities can lead to production delays and higher costs.
Case Study: Ramco Cements
Ramco Cements, another major player in the Indian cement industry, addressed the challenge by implementing an automated warehouse management system. The system enabled real-time tracking of inventory levels and improved warehouse operations, reducing storage costs and improving efficiency.
Solutions:
- Implement an automated warehouse management system for real-time tracking of inventory levels.
- Invest in better storage facilities to reduce production delays and storage costs.
Challenge 7: Inefficient Packaging and Warehousing
Cement manufacturers need to pack and store their products efficiently to reduce transportation costs and ensure timely delivery. Inefficient packaging and warehousing practices can lead to higher costs and delays.
Case Study: JK Lakshmi Cement
JK Lakshmi Cement, one of the premier cement manufacturers in India, overcame this challenge by adopting a lean warehousing system. The company optimized its packaging and warehousing operations using lean principles, reducing storage costs and improving delivery times.
Solutions:
- Implement a lean warehousing system to optimize packaging and storage operations.
- Invest in automation and technology to improve packaging and reduce storage costs.
TITO by Qodenext: The Ideal Solution for All Your Logistics Management Challenges
TITO, or Truck In Truck Out, is a revolutionary logistics management system developed by Qodenext. TITO offers a seamless and efficient solution to manage the entire logistics process, from gate-in to gate-out. This innovative solution is designed to address the key challenges faced by the Indian cement industry and other logistics-intensive businesses.
Here are some of the ways TITO can help you streamline your logistics operations and drive efficiency:
Benefits of TITO by Qodenext
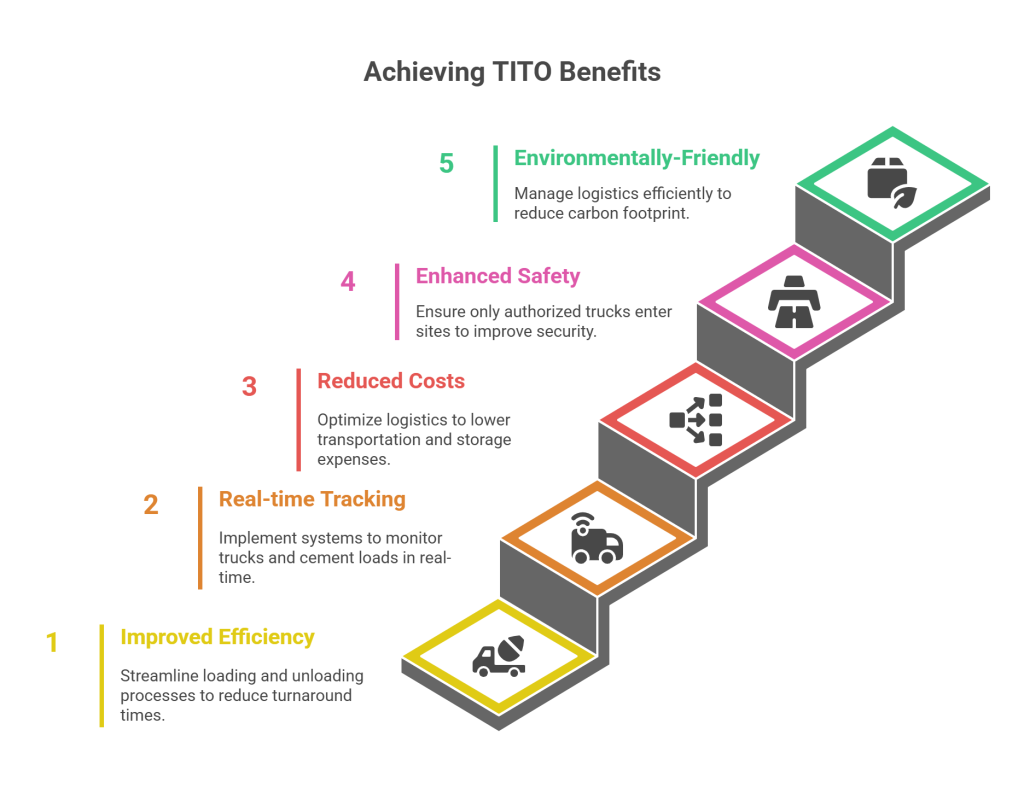
- Improved Efficiency: TITO enables seamless loading and unloading of cement at manufacturing plants and construction sites, reducing turnaround times and increasing productivity.
- Real-time Tracking: The TITO system offers real-time tracking of trucks and cement loads, providing visibility and control over logistics operations.
- Reduced Costs: By streamlining logistics operations, TITO can help reduce transportation and storage costs, ultimately leading to increased profitability.
- Enhanced Safety: TITO ensures that only authorized trucks enter manufacturing plants and construction sites, improving safety and security.
- Environmentally-Friendly: TITO’s efficient logistics management can help reduce the carbon footprint of cement manufacturing and transportation operations.
Why Choose TITO?
There are many reasons to choose TITO by QodeNext over other logistics management systems in the market.
- Proven Track Record: TITO by Qodenext has been successfully implemented by leading cement manufacturers in India, delivering tangible results.
- Cutting-Edge Technology: TITO is powered by the latest technologies, including RFID and IoT, ensuring reliability and accuracy.
- Customizable: TITO can be customized to meet the specific logistics management needs of your cement manufacturing operations.
- Support and Service: Qodenext offers comprehensive support and service for TITO, ensuring that your operations run smoothly.
Incorporating TITO into your logistics management system can revolutionize your cement manufacturing and transportation operations. Don’t let logistics management challenges hold you back – choose TITO for optimized efficiency, cost savings, and enhanced safety.
Conclusion
To stay competitive in today’s fast-paced business environment, the cement industry must address the logistics management challenges that it faces. By implementing advanced logistics management systems such as TITO, efficiency as well as productivity can be significantly enhanced in the most effective manner.
With these systems in place, companies can overcome the challenges of transportation and distribution and focus on growth and expansion. So, whether you are a cement manufacturer, supplier, or distributor, investing in an effective logistics management system is a must-have to thrive in the industry.
To know and understand more about fulfilling your logistics needs, get in touch with us now!
FAQs: Logistics Management System
1. What is a logistics management system?
A logistics management system is specialized software that helps companies smoothly manage the entire journey of goods, from sourcing raw materials to delivering finished products. It combines features like transportation, warehouse, and inventory management to make supply chain operations more efficient and cost-effective.
2. Can a logistics management system be customized for my cement company?
Absolutely! Logistics management systems can be tailored to fit your company’s unique needs. You can choose specific modules and features—like real-time tracking, demand forecasting, and risk management—that address the particular challenges your business faces.
3. Can logistics management systems integrate with existing ERP systems?
Yes, most modern logistics management systems are designed to integrate seamlessly with existing ERP (Enterprise Resource Planning) solutions. This integration ensures that your business enjoys a smooth flow of information, reducing manual work and improving operational efficiency.
4. Why is logistics management especially important in the cement industry?
The cement industry relies heavily on moving both raw materials and finished products efficiently. Given factors like bulk volume, tight deadlines, and remote construction locations, effective logistics management is crucial to control costs, reduce delays, and keep projects on track.
5. How does real-time tracking improve cement logistics?
With real-time tracking, companies can monitor their trucks, shipments, and cargo status at any moment. This visibility helps to optimize delivery schedules, quickly respond to delays, and enhance overall customer satisfaction.
6. What role does automation play in improving cement logistics?
Automation streamlines warehouse operations, speeds up packaging, and simplifies inventory management. By minimizing manual intervention, companies reduce errors, lower operating costs, and ensure products reach their destinations on time.
7. How do logistics systems help manage unpredictable demand in cement supply?
Advanced data analytics and forecasting tools within logistics systems allow manufacturers to anticipate shifts in demand. This helps them adjust production and inventory levels, so they are better prepared for market changes without incurring unnecessary costs.
8. Can logistics management systems help lower transportation costs?
Yes, they can. By optimizing vehicle routes, consolidating shipments, and automatically selecting the most efficient transportation modes, these systems help companies save money on fuel, labor, and maintenance.
9. How can a logistics system reduce supply chain disruptions?
A robust logistics management system can identify potential hazards—like weather issues or raw material shortages—and recommend contingency plans in advance. This risk-minded approach helps keep your operations running even when unexpected challenges arise.
10. Will implementing a logistics management system really make a difference for my business?
Definitely! By improving speed, accuracy, and flexibility in every aspect of logistics, such systems help your company deliver better service, cut costs, and remain competitive in a fast-paced industry. Investing in the right logistics solution is a proven way to support your long-term growth and resilience.