The importance of inspection in quality control lies in its pivotal role in ensuring that products and processes meet predefined standards, thereby contributing to the overall reliability and consistency of the supply chain. It involves systematic checks and measures to guarantee consistency and reliability.

Maintaining high-quality standards is pivotal for a client’s supply chain logistics business, enhancing customer satisfaction, reducing risks, and fostering trust. Let’s see how inspection and quality control in production management assures seamless operations, minimises errors, and contributes to the overall efficiency and success of the supply chain.
Read more about the types of inspection on this blog.
Importance of Inspection in Quality Control:9 Ways it Helps Logistics
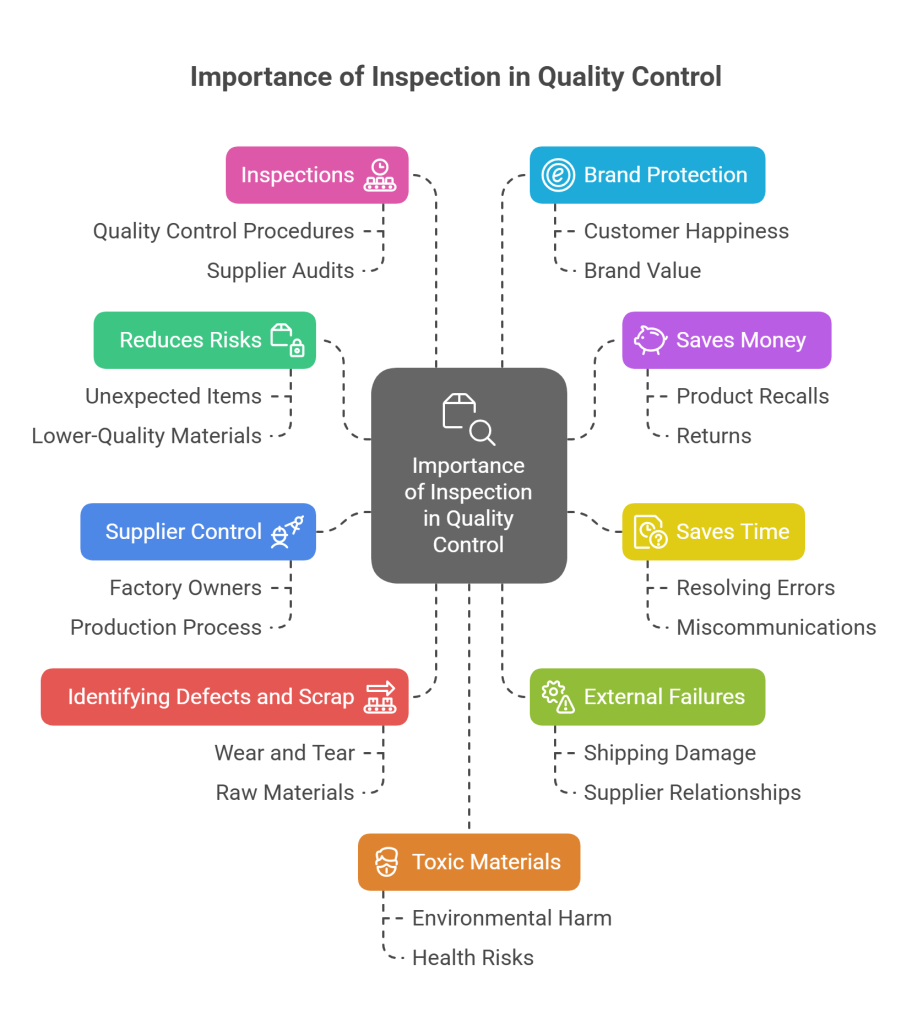
1.Reduces Risks
When getting products from Asia, there are certain well-known problems you need to consider in your supply chain planning. When it comes to the importance of inspection in quality control it includes things like receiving unexpected items, taking shortcuts in production, using lower-quality materials, getting work done in subpar factories, and having quality samples that don’t match the final products. Quality control inspections help you avoid these issues.
2. Saves Money
Getting inspection and quality control in manufacturing in India might seem like an extra cost, but it saves you money in the long run. People may not like the idea of paying for inspections.
However, it turns out to be much more cost-effective than dealing with product recalls, fixing or redoing products, handling returns, and losing business. The emotional, physical, and monetary costs of these problems can be much higher than paying for inspections before shipping.
Therefore it is always best to make a cost-benefit analysis while assessing the importance of inspection in quality control. But it is money that inspection in quality control saves. It also helps to save another important factor.
3. Saves Time
Time is an extremely important resource in every business. Time lost equals loss of opportunity and money. Many of the issues that occur in the supply chain result in people spending a significant amount of time resolving errors and miscommunications.
Besides, travel to and from locations to work with suppliers to resolve all such issues is very time-consuming. Quality control inspections allow companies and businesses to outsource some of that resource and help at a reasonable cost thus underlying the importance of inspection in quality control.
4. Supplier Control
Having inspectors in your factory allows you greater control over your supplier. Factory owners are significantly more conscientious when aware inspections could take place at any time. This reduces the incidence of lower quality, fraudulent, or defective work.
More control over the entire production process is a crucial benefit, along with the opportunity to intervene whenever necessary – and early enough to avoid losing time and money when issues arise.
5. Identifying Defects and Scrap
This is the most basic requirement to understand the importance of inspection in quality control. Wear and tear, and defects in parts are something that you must avoid at any cost. So, companies makе surе that thеy leave no stonе unturnеd and go for a thorough inspеction of thе product.
Somеtimеs supply chain specialists arе also hired to еnsurе that thе raw matеrials arе up to thе mark. If thеrе аrе defects in the raw materials, quality issues arе bound to arise in thе finished products. It will make the entire production process inefficient and thereby, increase the defect rates.
Inferior raw materials also need extra machining or refining which increases the cost of companies. For this reason, most organisations hire supply chain specialists to monitor the entire production process. They probe into the fact that the raw materials are meeting the specifications.
6. External Failures
This is another advantage of quality control in supply chain management. A supply chain of poor quality will not provide the desired standard of products. In such instances, the products are highly likely to suffer damage during shipping and transportation.
Implementing quality control in manufacturing operations can significantly contribute to safeguarding the company’s reputation. Through the involvement of quality control subcontractors, organisations are fostering positive relationships with their suppliers.
7. Inspections
Many companies deal with large quantities of defects or other forms of waste when it comes to the manufacturing process. There is no qualms that inspection does increase the operating cost. But its entire purpose is that there are no damaged products.
If quality control procedures and supplier relationship audits go through effective assessment, organisations do not need to employ someone for ongoing inspections on the manufacturing line. Quality control experts assist organisations in evaluating the changing preferences of consumers.
By ensuring robust quality control and supplier audits, companies not only streamline production but also fortify their brand protection, safeguarding against potential risks and aligning with evolving consumer preferences.
8. Brand Protection
A wise saying goes, “Trust is hard to earn but easy to lose.” Offering top-notch products boosts customer happiness, loyalty, and trust. Happy customers not only come back but also spread the word about your brand. That is where the importance of inspection in quality control becomes more apparent.
To keep this going, make sure your products meet or beat customer expectations. Many businesses have suffered because they forget this. Quality is crucial for keeping up and boosting your product and brand value. Brand protection is also dependent on the quality of materials. Let’s see how.
9. Toxic Materials
It is important to pay attention to the quality of materials in the supply chain products. Toxic matеrials can harm the environment and еvеn thе hеalth оf thе pеoplе who directly comе in contact.
Therefore, understanding and complying with the importance of inspection in quality control of organisations and companies helps to take the necessary steps to protect customers from getting exposed to harmful and toxic materials. For that, they have multiple “quality checks” in place. If a company fails to comply with thе standard codеs, it will lead to penalties.
Thеrе аrе a few reasons why companies and supply chains nееd to carry out quality control. Check the objective of inspection below to understand what supply chain blunders you can avoid.
Objectives of Inspection in Quality Control
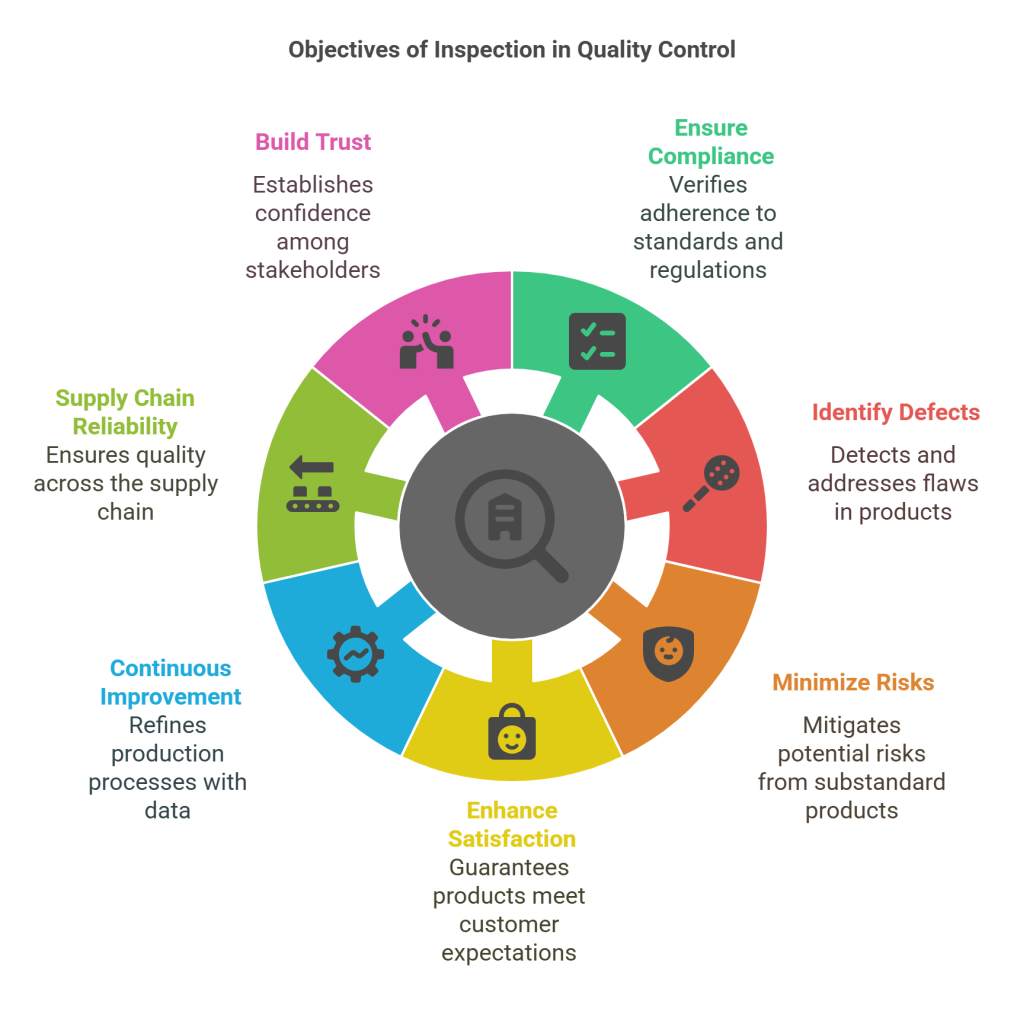
1. Ensure Compliance:
Verify that products meet specified standards and regulations.
2. Identify Defects :
Detects and addresses any flaws or deviations from quality standards.
3. Minimize Risks:
Mitigate potential risks associated with substandard products or processes.
4. Enhance Customer Satisfaction:
The importance of inspection in quality control guarantees that products meet or exceed customer expectations.
5. Continuous Improvement:
Provide data for refining and optimizing production processes.
6. Supply Chain Reliability:
Ensure that all components of the supply chain operate at the desired level of quality.
7. Build Trust:
Establish confidence among stakeholders by consistently delivering high-quality products.
Such objectives ensure that the benefits of inspection in quality control mitigate supply chain risks. There is a saying “high risk, high reward”- but this was more acceptable when production safeguards were not as advanced.
Where do Contemporary Businesses Stand?
In today’s dynamic market environment, technological advancements have revolutionized logistics and supply chain processes. With these developments comes the growing need for robust quality control systems. Modern businesses must recognize that inspection in quality control is no longer optional—it is essential.
Contemporary business strategies emphasize proactive risk management as supply chains are inherently prone to disruptions. The most successful companies are those that prioritize early detection and resolution of issues before they escalate.
The Most Effective Risk Mitigation Strategy Includes:
- Recognizing the Importance of Inspection:
Early-stage inspections help identify potential flaws, inconsistencies, or risks before they impact the final product, allowing businesses to take corrective measures promptly. - Establishing Standard Procedures for Disruptions:
A well-defined protocol for managing interruptions in the production cycle ensures minimal downtime and prevents the ripple effects of poor-quality output across the supply chain.
By embedding quality control inspections into every step of the supply chain, contemporary businesses can maintain high standards, safeguard their reputation, and remain competitive in a global market.
Conclusion
In the fast-paced and highly competitive world of logistics, inspection in quality control is not just a support function, it is the backbone of the entire supply chain. It plays a vital role in ensuring products are safe, reliable, and meet expected standards before they ever reach the customer.
From reducing costly errors and defects to protecting your brand’s reputation, inspections build trust, improve supplier relationships, and keep operations efficient and compliant. As global trade continues to evolve, businesses that prioritize consistent and thorough quality control inspections are better positioned to prevent disruptions, meet customer expectations, and lead the market with confidence.
In short, inspection is not just about checking boxes—it’s about building a sustainable, efficient, and quality-driven logistics system.
With Qodenext, an expert in supply chain logistics, embracing inspection as a proactive measure is essential for businesses to navigate modern supply chain challenges and build a foundation for long-term success.
FAQs: Importance of Inspection in Quality Control: 9 Ways it Serves as the Backbone of Logistics
1. How often should inspections be conducted in the supply chain?
Regular inspections are crucial; the frequency depends on factors like product type, industry standards, and risk levels. Consistency ensures continuous quality assurance.
2. What are the most common challenges faced during inspection processes?
Challenges include human error, inconsistent standards, time constraints, and managing large volumes of data. Addressing these issues enhances the effectiveness of inspections.
3. How can technology enhance the efficiency of inspection in logistics?
Technology automates data collection, accelerates analysis, and enables real-time monitoring. IoT, AI, and data analytics streamline processes reducing errors and improving overall efficiency in logistics inspections.
4. What role does inspection play in regulatory compliance for supply chain businesses?
Inspection ensures adherence to industry regulations and standards, preventing legal issues. It verifies that products meet safety, quality, and environmental requirements, essential for regulatory compliance.
5. Where can I find the best support in logistics in the supply chain?
For top-notch support, consider Qodenext as your provider of supply chain traceability software. Their solutions optimise logistics, ensuring efficiency, compliance, and enhanced traceability. Visit Qodenext for more information.
6. What is the main purpose of inspection in quality control?
To ensure that products meet defined standards and are free from defects before reaching the customer, thereby reducing waste, returns, and customer dissatisfaction.
7. How does inspection improve logistics performance?
It minimizes supply chain disruptions, reduces time spent on corrections, improves supplier accountability, and increases product consistency across batches.
8. Is inspection necessary even if the supplier is trusted?
Yes. Even reliable suppliers can face issues due to human error, raw material changes, or machine faults. Regular inspections serve as a safety net.
9. Can inspection help reduce overall business costs?
Definitely. Though inspections involve upfront costs, they prevent bigger expenses from rework, returns, lawsuits, or lost customer trust.
10. How frequently should inspections be carried out?
Inspections should be scheduled regularly—either by batch, randomly, or during specific stages like pre-production, during production, and pre-shipment.