
Backorders — an inconvenience in our gotta-have-it-now world. Faced with an out-of-stock notification, many consumers will simply click over to a competitor’s site. For some retailers, the answer is to use backorders, where a desired item that is still in production but currently out of stock is promised to ship in a set timeframe.
The customer gets the item, the retailer makes the sale. Win/win.
Backorders can be tricky, though. If you end up being unable to fulfil the order, the customer may be more irritated than if you had just marked the item as out of stock. And, managing backorders can be a headache for finance and logistics teams.
So are backorders right for your business? Maybe. Let’s find out.
What Is Backorder?
An item on backorder is an out-of-stock product that is expected to be delivered by a certain date once it is back in stock. Businesses will often still sell products on backorder with the guarantee to ship them to the buyer once their inventory has been replenished.
Backordering an item means the shopper can buy the item now and receive it at a future date when the item is in stock and available. When an order contains a backordered item, it can’t be packed and shipped immediately given the lack of physical inventory at the time.
If there are other items in the same order that are in stock, the order may be split and shipped at different times, with the back-ordered items being shipped at a later date.
How Backorders Work
When a company takes orders — and potentially payments — for products that are not in stock, it is accepting backorders.
Once backorders are accepted, the inventory management system converts them to purchase orders and sends them to the appropriate internal department, vendor or distributor. Customer service teams should provide buyers with an estimate of when they can expect their orders and how payment will be handled.
Retailers may choose to have the supplier drop ship items directly to customers, or the retailer may take delivery of the items, translate the backorders to sales orders and ship the items to customers after charging the customer’s account, if applicable.
For a limited number of SKUs at a manageable volume, this is not an overly complex process. Problems mount, however, when the number or quantity of back ordered products multiply or when retailers have a lot of manual order processes and must match each purchase order with a current sales order when completing the fulfilment process.
What causes backorders?
Several internal and external factors can cause backorders, including:
1. Supply chain issues
Even now, many supply chains are still experiencing or recovering from disruptions that originated during the COVID-19 pandemic lockdowns and have been exacerbated by environmental factors and global conflicts. Such supply chain issues can delay the production, transportation, or delivery of goods and affect your ability to fulfil orders on time.
2. Fluctuations in demand
Backorders may be caused by unusual demand for a particular product. Everything from a marketing campaign going viral to an extreme weather event could generate an unplanned spike in demand.
3. Inventory management
How you choose to manage inventory can influence backorders. If you keep minimal inventory or run a dropshipping business, you will likely have to manage and fulfil backorders as a tradeoff for low to zero warehouse costs. You might prefer to keep extra stock, also known as safety stock, as a way to cushion your orders from supply chain disruptions and demand shifts.
Backorder vs. out-of-stock
Inventory management plays a pivotal role in customer satisfaction, revenue generation, and brand loyalty. Two important terms often encountered in retail and eCommerce are “backorder” and “out-of-stock.” While they may seem similar, they have distinct meanings and impacts. Understanding the difference between them—and knowing how to manage both—is essential for any business.
Backorder vs. Out-of-Stock: Understanding the Difference
1. Backorder
A backorder occurs when a product is currently unavailable but will be restocked at a known future date. Customers are allowed to place orders in advance and receive the product once it becomes available. Retailers accept orders with the promise of later fulfillment, offering clarity on estimated shipping dates.
In practice:
- “Item will ship in 2 weeks”
- “Your order will be fulfilled within 10 business days”
- Customers still have the ability to purchase the item ahead of time
This implies temporary unavailability—there is certainty and confidence in restocking the item soon.
2. Out-of-Stock
An out-of-stock item means that the product is currently unavailable with no specific restocking date provided. This may be due to supply chain issues, product discontinuation, or unpredictable manufacturing delays.
In practice:
- “This item is currently unavailable”
- No purchase option is available on the site
- The future availability is unknown or indefinite
Out-of-stock status may be temporary or permanent, but customers cannot complete a purchase or rely on a timeline for fulfillment.
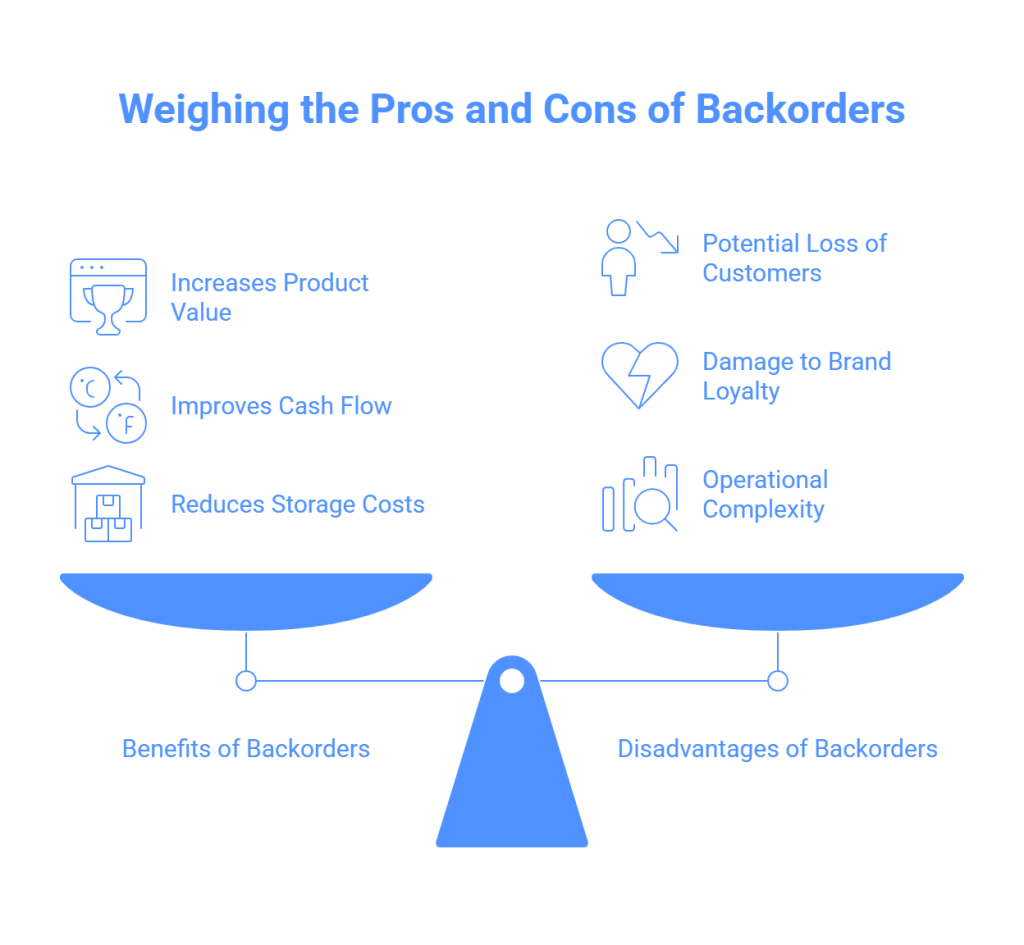
Benefits of Offering Items on Backorder
While backorders require careful logistics and communication, they offer several advantages when handled properly:
1. Increases Product Value and Demand
Backorders can reflect high demand, which in turn enhances product perception, desirability, and brand equity. When customers see an item still being offered despite temporary unavailability, they perceive it as worth waiting for.
2. Improves Cash Flow
Allowing customers to purchase products on backorder means the business receives revenue before stock is replenished. This enables better cash flow management and allows capital to be allocated toward other initiatives (e.g., marketing, tech upgrades).
3. Reduces Storage and Warehousing Costs
Since backordered items are often shipped immediately upon receipt, they may bypass storage altogether. This method helps minimize inventory holding costs and reduces delays from warehouse-to-door processes.
Disadvantages of Backorders
Despite their benefits, backorders also present specific risks and operational challenges:
1. Potential Loss of Customers
Not all buyers are willing to wait. Impatient customers may cancel their orders to seek alternatives from competitors, leading to lost sales opportunities and reduced customer satisfaction.
2. Damage to Brand Loyalty and Market Share
Repeated backorder notices or long delays can erode customer trust. When customers experience fulfillment issues frequently, they may switch to more reliable brands, resulting in a loss of market share.
3. Operational Complexity
Managing payments, updating customer information, and responding to delays becomes more involved with backorders. Late updates, expired cards, or missed fulfillment schedules can increase customer service workload and hurt company reputation.
Practical Tips to Minimize Backorders
While backorders can’t always be avoided, businesses can reduce their frequency and impact by following these best practices:
1. Maintain Communication with Supply Chain Partners
Develop and maintain proactive relationships with your vendors, manufacturers, and logistics providers. Regular check-ins help you:
- Understand lead times
- Track manufacturing delays
- Adjust your estimated delivery timeline to reflect reality
Real-time collaboration improves forecast accuracy and keeps customers informed.
2. Review Sales Trends and Customer Demand Data
Using historical sales data and seasonal analysis helps predict future demand more accurately. For instance, back-to-school items typically spike in the fall. Anticipating such trends helps ensure you’re well-stocked during peak seasons.
Consider investing in:
- Market research tools
- Customer analytics platforms
- Sales forecasting software
This predictive approach leads to smarter procurement and lower instances of backorders.
3. Calculate Reorder Points (ROP) for Each Product
An ROP (Reorder Point) is the inventory threshold that triggers a new purchase order. It helps ensure stock replenishment is timely and proactive.
How to calculate ROP:
To set smart reorder points, account for:
- Lead time demand: The number of units sold during lead time
- Safety stock: Extra inventory kept to mitigate demand or supply variability
Formula:
ROP = Lead Time Demand + Safety Stock
Setting product-specific ROPs helps ensure you never fall below necessary quantities for fulfillment, significantly minimizing the risk of backorders.
Understanding the difference between backorder and out-of-stock isn’t just about wording—it shapes how businesses manage customer expectations, inventory flow, and operational efficiency.
An out-of-stock status, by contrast, might indicate uncertain or unavailable products, potentially leading to revenue and loyalty loss. A product on backorder still provides buyers with confidence and clarity, encouraging continued purchases.
Conclusion
Backorders can be both a blessing and a curse for businesses. On one hand, they indicate high demand for a product, which is great for sales and revenue. However, backorders can also lead to customer dissatisfaction if not managed properly. Businesses need to understand the causes, advantages, and disadvantages of backorders to effectively prevent them or minimize their impact.
By implementing strategies such as effective inventory management, clear communication with customers, and proactive measures to prevent stockouts, businesses can navigate the challenges of backorders and maintain customer satisfaction.
So, whether you’re a business owner or a customer waiting for an item on backorder, understanding the ins and outs of backorders is key to ensuring a smooth shopping experience. Need a helping hand? Qodenext can lend you that.
FAQ: What Is Backorder?
1. What is a backorder?
A backorder refers to an item that is currently not available in stock but is expected to be restocked and shipped at a later date. Customers can still purchase the item during this time, and the order will be fulfilled once inventory is replenished.
2. What is a partial backorder?
A partial backorder occurs when a customer places an order containing multiple items, but only some of them are in stock. Businesses may choose to either split the shipment—sending the available items immediately and shipping the remainder later—or hold the entire order until it can be fulfilled in full.
3. What does “rolling backorder” mean?
A rolling backorder typically describes a backordered item that does not have a fixed delivery date. Instead, it uses a flexible timeframe or rolling estimate for when the product may become available, giving retailers more leeway in managing supply uncertainty.
4. Can backorders be avoided entirely?
While it’s not always possible to eliminate backorders, businesses can minimize their occurrence by maintaining higher inventory levels, using safety stock, improving demand forecasting, and choosing not to allow backorder purchases once stock runs out.
5. What is the difference between a backorder and an out-of-stock item?
The key difference is that a backordered item is expected to return to stock by a known date and can still be purchased, while an out-of-stock item is unavailable for purchase and has no estimated restocking date. Backorders come with a future promise, while out-of-stock status does not.
6. Are backorders risky for customer satisfaction?
Yes, if not carefully managed. Customers may become frustrated if their expectations aren’t met, especially if delays go uncommunicated. However, with proactive communication and accurate delivery estimates, many buyers are willing to wait for high-demand products.
7. Why do backorders happen?
Backorders may occur due to supply chain disruptions, unexpected demand surges, insufficient inventory planning, or lean inventory models like just-in-time systems or dropshipping. Even well-prepared businesses can face backorders during peak seasons or global supply crises.
8. How should businesses manage backorders effectively?
To manage backorders well, businesses should maintain clear communication with customers, provide estimated delivery windows, automate inventory tracking, and identify reorder points for timely restocking. Offering alternatives or partial shipments can also help reduce dissatisfaction.
9. What are the advantages of offering backorders?
Backorders can boost revenue by allowing sales to continue despite temporary stockouts. They also help improve cash flow by capturing payments earlier and reduce storage costs, as items can be shipped directly to customers upon arrival without warehousing.
10. What are the disadvantages of backorders?
Backorders come with their challenges, including the risk of customer cancellations, damage to brand reputation, and operational burdens like customer service follow-ups, payment updates, and fulfillment complications. Poorly managed backorders can result in lost business and long-term customer churn.