Efficient inventory management is the cornerstone of successful businesses, enabling them to optimize resources, enhance customer satisfaction, and boost profitability. Among the various strategies employed, ABC analysis stands tall as a powerful tool for categorizing inventory items based on their value and impact.
However, as with any methodology, it is vital to recognize the limitations of ABC analysis to make informed decisions and avoid potential pitfalls. In this blog post, we delve into the world of ABC analysis, exploring its significance in inventory management while shedding light on its inherent limitations. By understanding both the merits and constraints of ABC analysis, businesses can effectively harness its power and transform their supply chain operations for sustained success.
What Is ABC Analysis? Limitations of ABC Inventory Analysis.
ABC analysis, also known as the Pareto analysis or the 80/20 rule, is a widely used technique in inventory management and supply chain optimization. It classifies items or products into three categories based on their value or importance.
These categories are A, B, and C, with A items being the most critical and C items being the least critical. ABC analysis helps businesses prioritize their inventory management efforts and allocate resources efficiently.
Classification Criteria:
ABC analysis classifies items based on a specific criterion, typically the monetary value, sales volume, or profitability. The criterion chosen should reflect the importance of the item to the business.
Category A (High-Value Items):
- Category A consists of the most valuable items in terms of monetary value, sales volume, or profitability. These items usually account for a significant portion of the total value or volume. Businesses need to closely monitor and manage these items to avoid stockouts and ensure customer satisfaction.
Category B (Moderate-Value Items):
- Category B includes items that have moderate value or volume but are not as critical as Category A items. These items are important but not as essential for the overall success of the business. Adequate inventory levels and monitoring are necessary, but they may not require the same level of attention as Category A items.
Category C (Low-Value Items):
- Category C consists of low-value or low-volume items that have minimal impact on the business. These items typically have a low contribution to overall sales or profitability. While it’s important to maintain an adequate stock of Category C items, excessive attention or resources are not warranted.
Resource Allocation:
ABC analysis helps businesses allocate their resources effectively by focusing on the items that have the greatest impact. It enables them to prioritize their inventory management efforts, such as forecasting, purchasing, and storage, based on the category to which each item belongs.
In summary, ABC analysis is a valuable technique for inventory management and resource allocation. It helps businesses prioritize their efforts, optimize inventory levels, and ensure that critical items receive the necessary attention while minimizing unnecessary expenses on less important items.
Different Types of ABC Classification
ABC classification is a popular technique used in inventory management to categorize items based on their relative importance or value. It helps businesses prioritize their inventory control efforts and allocate resources effectively. There are several types of ABC classification, each with its own focus and criteria for categorization.
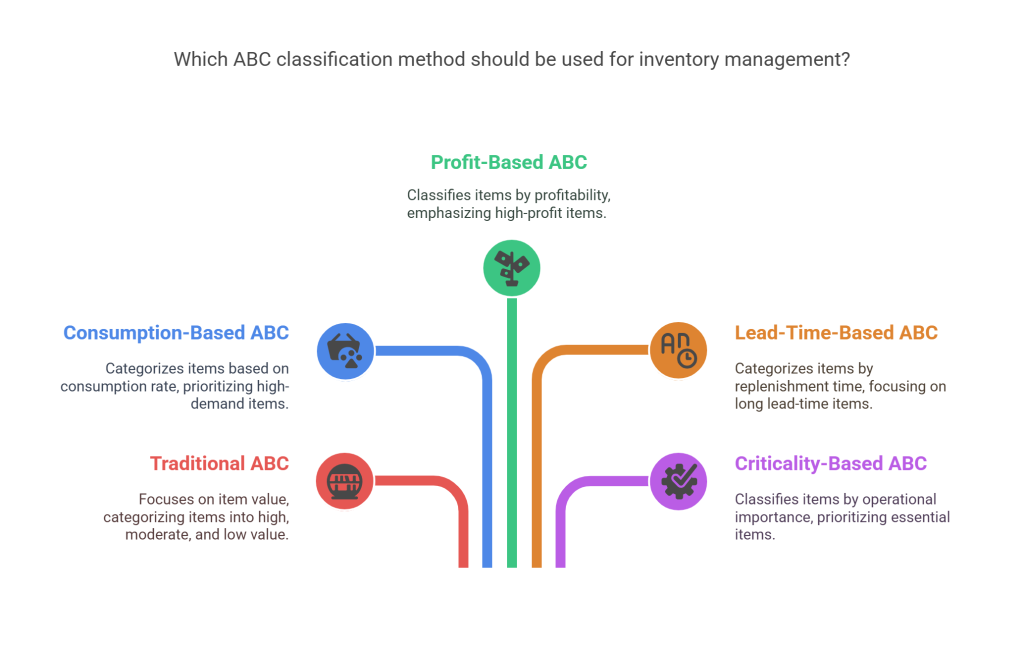
1. Traditional ABC Classification:
This method divides items into three categories: A, B, and C. Category A includes high-value items that contribute to a significant portion of the total inventory value but represent a small fraction of the total items. Category B consists of moderately important items, while Category C comprises low-value items that make up a large portion of the total inventory but contribute less to the overall value.
2. Consumption-Based ABC Classification:
In this approach, items are categorized based on the rate of item consumption or demand. Category A includes high-consumption items, while Category C consists of low-consumption items.
3. Profit-Based ABC Classification:
In this classification, items are categorized based on their profitability or contribution to the organization’s profits. Category A includes high-profit items, while Category C comprises low-profit items.
4. Lead-Time-Based ABC Classification:
This method categorizes items based on the time required to replenish their stock. Category A includes items with the longest lead times, which require careful planning and monitoring. Category C consists of items with short lead times that can be easily replenished.
5. Criticality-Based ABC Classification:
This classification considers the criticality or importance of items in the production or service process. Category A includes critical items that are essential for operations and require close attention. Category C comprises non-critical items that have less impact on operations.
These various types of ABC classifications provide businesses with different perspectives to manage their inventory effectively. By understanding the characteristics and significance of each item, companies can allocate their resources, optimize stock levels, and enhance overall operational efficiency.
Examples of ABC Analysis
ABC Analysis is a valuable technique utilized in inventory management to prioritize items based on their value and significance. By categorizing inventory items into three groups, namely A, B, and C, businesses can allocate their resources more efficiently. The following are the top 5 examples of ABC Analysis:

Example 1:
In a retail store, A-category items might include high-value products with high sales volumes, such as electronics or luxury goods. B-category items could consist of moderately priced items with moderate sales volumes, such as clothing or household appliances. C-category items might encompass low-value items with low sales volumes, like stationary or small accessories.
Example 2:
In a manufacturing plant, A-category items could be critical raw materials or components that are required for the production of high-demand products. B-category items might include less critical materials or components with moderate demand. C-category items could encompass non-essential materials or components with infrequent usage.
Example 3:
In a hospital, A-category items might be life-saving drugs or medical supplies required for emergency situations. B-category items could include medications or supplies needed for routine treatments. C-category items might consist of non-essential supplies, such as office stationery or administrative materials.
Example 4:
In a warehouse, A-category items could be fast-moving consumer goods (FMCG) that have high demand and quick turnover. B-category items might include goods with moderate demand and turnover, such as seasonal products. C-category items could encompass slow-moving or obsolete inventory that requires close monitoring and potential clearance strategies.
Example 5:
In a restaurant, A-category items might be premium ingredients used in signature dishes or high-margin menu items. B-category items could include standard ingredients used in regular menu items. C-category items might consist of non-perishable or low-value items like condiments or disposable utensils.
These examples illustrate how ABC Analysis helps businesses focus their attention on high-value items (A-category) while minimizing the resources allocated to low-value items (C-category), ultimately enhancing operational efficiency and maximizing profitability.
Limitations of ABC Analysis
ABC analysis has a few limitations. It relies heavily on historical data and may not accurately predict future patterns in dynamic business environments. It also overlooks the interdependencies between different inventory items and fails to consider factors beyond value or importance.
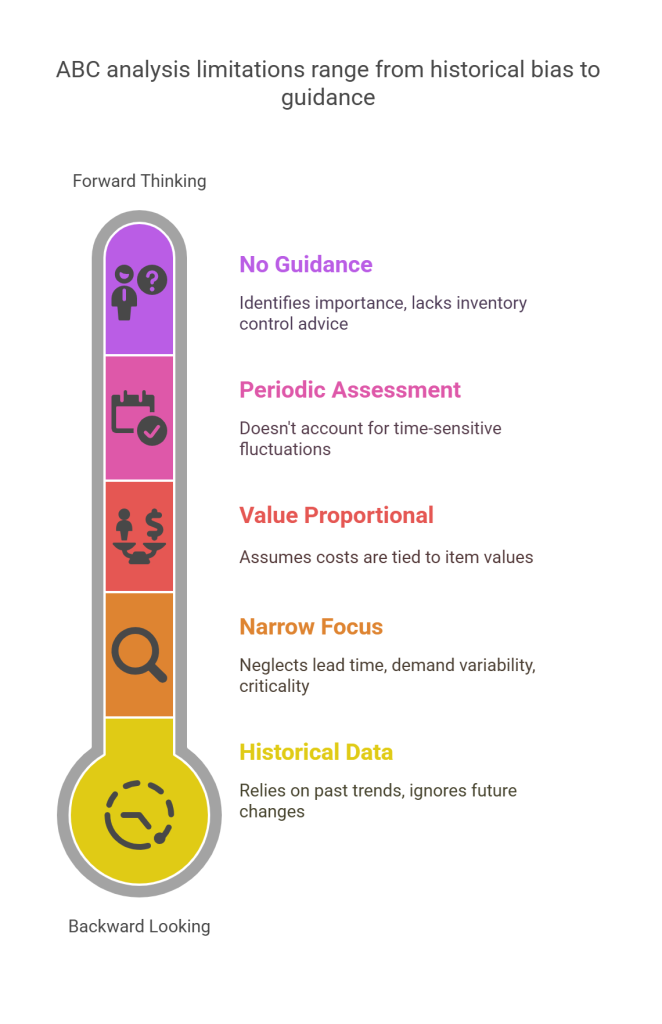
Additionally, it assumes consistent demand and doesn’t account for fluctuations or supply disruptions. To ensure effective inventory management, ABC analysis should be supplemented with other techniques and considerations. Listed below are some of the limitations of ABC Analysis.
1. Historical Bias:
ABC analysis heavily relies on historical data, assuming that past trends will continue to hold true in the future. However, this assumption may not always be accurate, especially in rapidly changing industries or during unpredictable events such as economic crises or natural disasters.
2. Single Criterion:
ABC analysis categorizes items based on a single criterion, typically monetary value. This narrow focus neglects other important factors such as lead time, demand variability, or item criticality, which can lead to oversights and inaccurate classifications of items.
3. Lack of Guidance:
While ABC analysis classifies items into categories, it does not provide specific guidance on how to handle each category. It merely identifies the relative importance of items without addressing the best practices for inventory control, leaving the decision-making process up to the manager’s discretion.
4. Cost Assumption:
ABC analysis assumes that inventory costs are directly proportional to item values. However, this assumption may not always hold true. Some high-value items might have low carrying costs, while low-value items may have significant holding costs due to factors like storage requirements or obsolescence.
5. Time Sensitivity:
ABC analysis typically relies on periodic assessments of item value, which may not account for time-sensitive fluctuations. Items may shift between categories over time, leading to inconsistencies and the need for frequent reassessment.
Inventory analysis, ABC analysis, ABC analysis for inventory management, ABC analysis cost accounting, ABC analysis graph, ABC analysis advantages and disadvantages, ABC analysis in financial management, ABC analysis material management, ABC analysis diagram, inventory analysis method, ABC analysis steps.
It’s important to consider these limitations when using ABC analysis and supplement it with other techniques or approaches to achieve a more comprehensive and robust inventory management strategy.
Conclusion
ABC analysis is a valuable inventory tool that helps businesses focus on what matters most—high-value items—while optimizing stock and reducing costs. However, it has limitations like historical bias and a narrow focus. To overcome these, businesses should pair ABC analysis with modern tech solutions.
By incorporating ABC analysis along with other techniques and considerations, businesses can develop a comprehensive inventory management strategy. They can leverage the insights provided by ABC analysis while taking into account the limitations and supplementing it with additional approaches to achieve accurate and effective inventory management.
However, Qodenext offers a solution to these challenges. By automating the ABC analysis process and providing real-time data insights, Qodenext enhances inventory management efficiency.
FAQs
1. How often should ABC analysis be performed?
ABC analysis should be reviewed periodically—typically quarterly or biannually—to account for changes in sales trends, demand patterns, or new product introductions.
2. Can ABC analysis be applied to services, not just physical products?
Yes, ABC analysis can be adapted to services by analyzing factors like service cost, frequency of use, or customer value, helping allocate resources to high-impact services.
3. What tools can be used to perform ABC analysis?
Businesses can use Excel, ERP systems, or inventory management software like Qodenext’s solutions, which offer automated ABC classification and real-time tracking.
4. What’s the difference between ABC analysis and XYZ analysis?
While ABC analysis focuses on the value or impact of items, XYZ analysis considers the variability of demand. Both are often used together for more robust inventory planning.
5. How does ABC analysis support cost reduction?
By identifying high-priority items, ABC analysis helps reduce overstocking, minimize holding costs, and streamline procurement, resulting in significant cost savings.
6. Is ABC analysis suitable for all industries?
Yes, ABC analysis is flexible and can be used in various industries such as retail, manufacturing, healthcare, and logistics to optimize inventory control and resource allocation.
7. How is ABC analysis different from Just-In-Time (JIT) inventory?
ABC analysis categorizes inventory based on value, while JIT focuses on minimizing inventory levels by receiving goods only as needed. They can complement each other for efficient inventory strategies.
8. Can ABC classification change over time?
Absolutely. An item’s classification can shift as demand, price, or business priorities change. Regular reviews help maintain accurate categorization.
9. What are the main data points needed to conduct ABC analysis?
Typically, you’ll need item names, annual consumption values, unit costs, and total consumption value to classify inventory into A, B, or C categories.
10. What are the risks of misclassifying items in ABC analysis?
Misclassification can lead to poor inventory decisions—like overstocking low-priority items or understocking high-value items—resulting in lost sales or increased holding costs.