
Inventory management is a hectic task and boxes, shipping materials, and packaging items have to be arranged in a symmetrical order to keep track of incoming and outgoing boxes. Warehouse racking systems directly impact the efficiency of your order management.
While storage cabinets, totes, and shelves are needed to pick and store boxes, warehouse racks streamline the workflow of your inventory staff. In this article, let’s take a closer look at racking systems and their role in faster order fulfilment, worker safety, and installation costs.
Warehouse Racking – What is it and the Different Types
Storage racking systems play a critical role in distribution centre infrastructure. They are designed to store products in an organised manner to maximise space and resource allocation. These accessible metal racks store pallets in multiple horizontal rows, stacked on top of one another.
Here are the key features to consider:
1. Load Capacity –
They are designed meticulously to hold heavy loads for different pallet sizes.
2. Linear and Non-Linear Placement –
Utilising the capacity, the racks allow vertical and horizontal product stacking as per the height of the warehouse.
3. Seamless Accessibility –
The warehousing staff can easily access and pinpoint the package location using forklifts.
4. Modularity –
User-friendly and modular racks allow quick customization and reconfiguration based on storage needs.
Next, let’s understand the different types of racking systems.
6 Types of Warehouse Racking
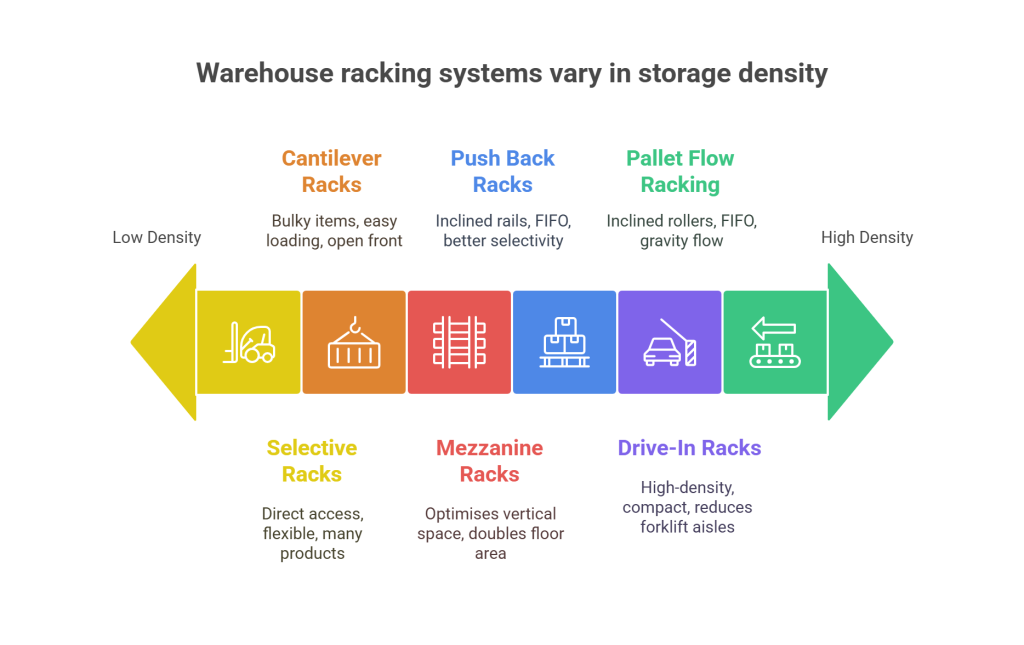
A Quality racking system uses handling equipment that supports both light and heavy loads. Here are different types of racks for faster load management.
1. Selective Racks
The most common type of warehouse racking system, selective storage racks, allow direct access to unit loads. You can select, store, and unload items directly without any barrier restriction. Furthermore, they are flexible, easily adaptable, and compatible with forklifts.
This loading system is suitable for companies storing many products in their warehouses.
2. Drive-In, Drive Through Racks
Do you have lesser storage and warehouse utilisation? Drive-in Drive-through racking is a high-density storage solution maximising space and warehouse height by reducing the forklift operating aisles.
Single entry point and cost-effective for large volumes of multiple products, drive-in drive-through allows compact racking for effective space utilisation. The first load is the first to be cleared in drive-through racking while drive-in racking deals with the last load to be cleared at the top.
3. Push Back Racks
Pallets are loaded from the front and pushed back on inclined rails. Such racking systems stack pallets in a single line and each subsequent pallet pushes the previous one back.
They offer better selectivity and storage density than drive-in racks, but are costly and harder to implement than selective racks. Push-back racks are perfect for First-in-First Out(FIFO) inventory management reducing stockout risk.
4. Cantilever Racks
These racks are specialised warehouse storage systems designed to handle bulky items that are not easily stored on traditional pallets. There are arms adjusted up and down the columns to accommodate items and flexible storage requirements.
The open-front design allows easy loading and unloading and simplifies inventory organisation keeping items off the floor.
5. Pallet Flow Racking
Pallet flow racking systems, also known as gravity flow racks, use inclined rollers or wheels to allow pallets to move forward when one is removed. This system is ideal for first-in, first-out (FIFO) inventory management, ensuring that older stock is used before newer stock.
6. Mezzanine Racks
Mezzanine floor racking lets you optimise the vertical warehouse space by doubling or tripling the floor area. This allows you to increase space without building expansion.
Benefits of Warehouse Racking Systems
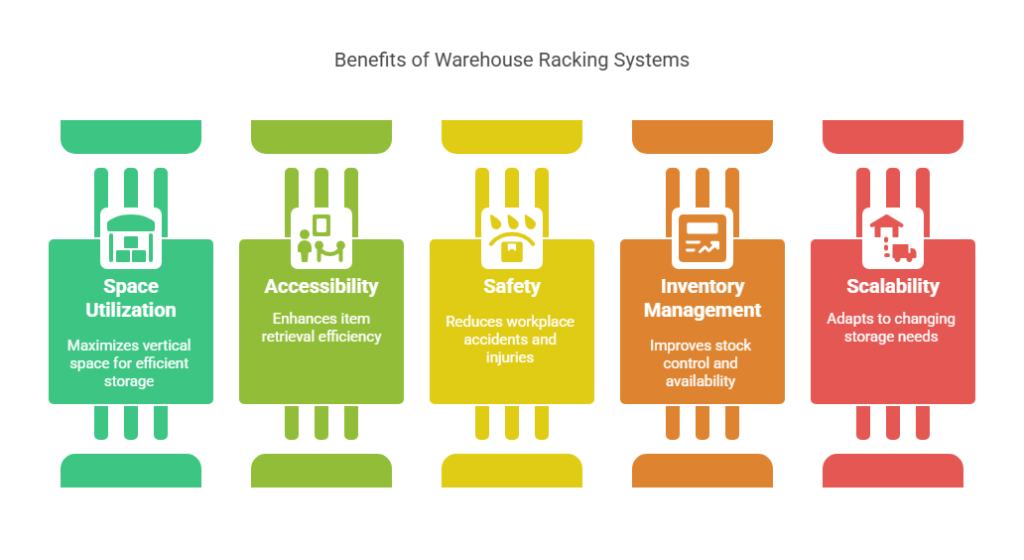
Implementing racking systems offers numerous benefits, including:
1. Improved Space Utilization
High-density storage racks maximise the use of vertical space, allowing warehouses to store more products within the same footprint. This is especially important for businesses with limited floor space.
2. Enhanced Accessibility
By organising inventory in a structured manner, warehouse racking systems make it easier for workers to locate and retrieve items. This improves picking efficiency and reduces the time spent searching for products.
3. Increased Safety
Properly designed and installed warehouse racking systems improve workplace safety by securely storing heavy and bulky items. This reduces the risk of accidents and injuries caused by falling objects or unstable stacks.
4. Better Inventory Management
Warehouse racking systems facilitate better inventory control by providing clear visibility of stock levels and locations. This helps prevent overstocking and stockouts, ensuring that the right products are available when needed.
5. Scalability
These racking systems are highly scalable, allowing businesses to adjust their storage capacity as their needs change. This makes it easy to expand or reconfigure the racking system to accommodate new products or increased inventory.
Best Practices for Implementing Industrial Racking Systems
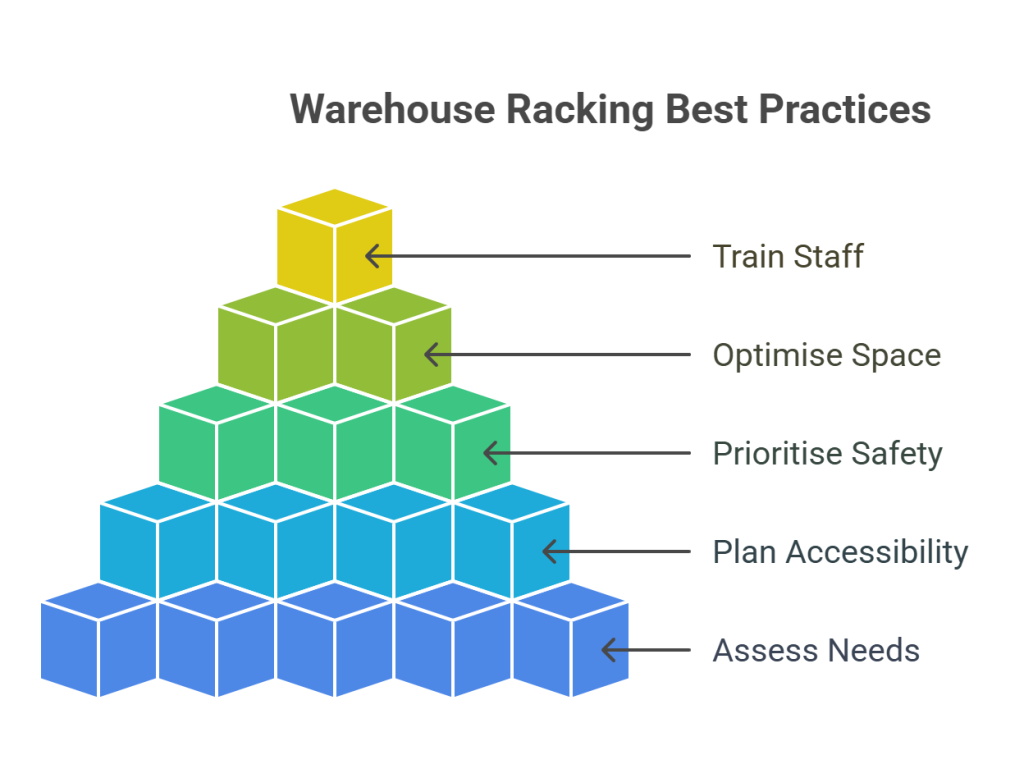
To get the most out of warehouse racking systems, consider the following best practices:
1. Assess Your Storage Needs
Before selecting a racking system, evaluate your storage needs based on the types of products you handle, their dimensions, and their weight. This will help you choose the most suitable warehouse shelving for storing goods.
2. Plan for Accessibility
Design your racking layout to ensure easy access to all stored items. Consider the flow of goods through your warehouse and the movement of forklifts and other equipment.
3. Prioritise Safety
Ensure that your racking system is designed and installed to meet safety standards. Regularly inspect the racks for signs of damage and perform maintenance as needed to prevent accidents.
4. Optimise Space Utilisation
Maximise space utilisation by using the appropriate racking system for your inventory. For example, use high-density racking systems for products with high turnover rates and selective racking for items that require frequent access.
5. Train Your Staff
Properly train your warehouse staff on the use and maintenance of the racking system. This includes safe loading and unloading procedures, weight limits, and regular inspections.
Conclusion
Warehouse racking systems are indispensable for modern warehouse management. They offer numerous benefits, including improved space utilisation, enhanced accessibility, and scalability. By understanding the different racking types and best practices, businesses can optimise their storage solutions and achieve greater operational efficiency.
Looking to streamline your supply chain visibility with advanced tracking solutions? Qodenext is your one-stop destination to fuel logistical growth.
FAQs: What are Warehouse Racking Systems?
1. What is the most common type of racking system?
The most common type of warehouse racking system is selective racking. It allows for direct access to each pallet and is highly flexible, making it suitable for a wide range of products.
2. How do warehouse racking systems improve safety?
It securely stores heavy and bulky items, reducing the risk of accidents caused by falling objects or unstable stacks. Regular inspections and maintenance further enhance safety.
3. Can warehouse racking systems be customized?
Yes, these systems can be customised to meet specific storage needs. This includes adjusting rack heights, depths, and configurations to accommodate different types of products and storage requirements.
4. What factors should be considered when choosing a rack?
When choosing a racking system, consider factors such as the types of products you store, their dimensions and weight, the available space in your warehouse, and the desired level of accessibility.
5. How often should warehouse racking systems be inspected?
These systems should be inspected regularly, ideally every month. Inspections should check for signs of damage, such as bent or cracked components, and ensure that weight limits are not being exceeded.
6. What materials are warehouse racking systems made from?
Most warehouse racking systems are made from high-strength steel to ensure durability and load-bearing capacity. They are often coated with powder finishes to resist corrosion and wear.
7. Are there specific racking systems for temperature-controlled warehouses?
Yes, certain racking systems are designed for cold storage or temperature-sensitive environments. These racks use corrosion-resistant materials and are structured to maintain airflow and support insulation needs.
8. What is the difference between FIFO and LIFO racking systems?
FIFO (First-In, First-Out) systems like pallet flow and push-back racks ensure older stock is used first, reducing spoilage. LIFO (Last-In, First-Out) systems like drive-in racks are suitable for non-perishable goods stored for longer durations.
9. How do racking systems impact order fulfillment speed?
By organizing inventory efficiently, racking systems reduce picking time and improve worker navigation, significantly increasing order processing speed and accuracy.
10. Can warehouse racking systems support automation?
Yes, many modern racking systems are compatible with warehouse automation technologies such as conveyor belts, automated guided vehicles (AGVs), and robotic picking systems, boosting productivity and reducing manual labor.