Warehouses store goods, but locating a specific item can be time-consuming and inefficient without an organized system, often requiring a manual search through multiple stockrooms.
This is where a Warehouse Management System (WMS) becomes invaluable. A WMS helps streamline inventory management by maintaining detailed records of all products and their exact locations within the warehouse.
With this system in place, businesses can quickly and accurately locate products without the need for extensive manual searching, significantly reducing effort and improving overall efficiency.
This guide will highlight the key benefits of a WMS, explore its different types, and show how it can transform your inventory management, simplifying operations, reducing errors, and making your life easier.
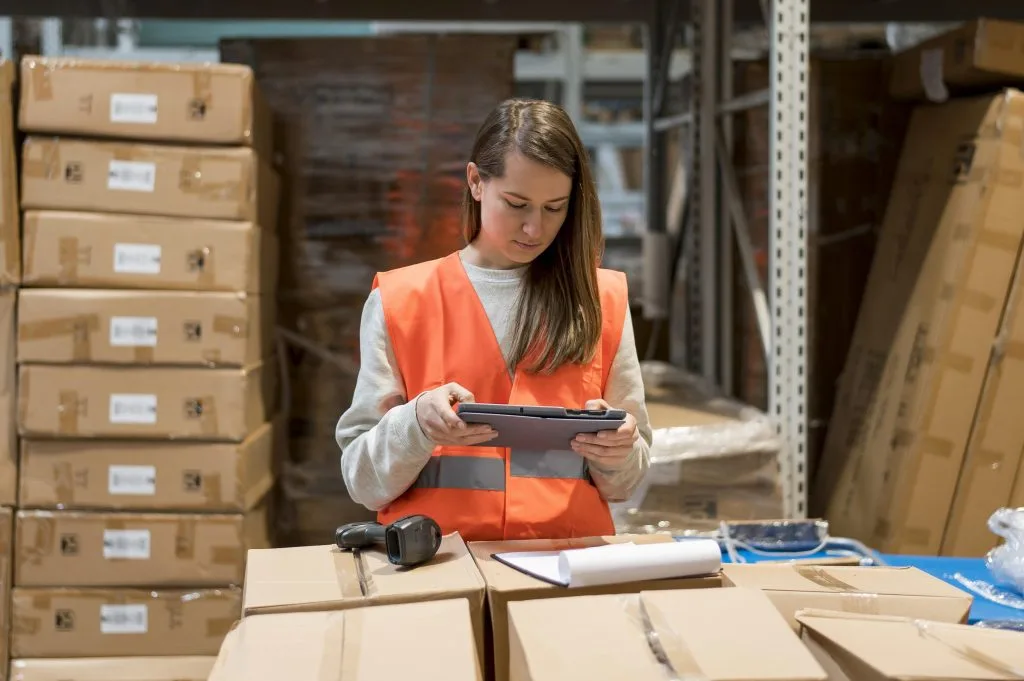
Meaning of Warehouse Inventory Management System
A Warehouse Inventory Management System (WMS) is a software solution designed to optimize and automate various operations within a warehouse, distribution, or fulfillment center. It streamlines processes like receiving, storage, inventory control, order picking, packing, shipping, labor management, and interfaces with automated handling equipment.
While both inventory and warehouse management deal with stock, inventory management offers a broader perspective, focusing on overall stock levels and their status. It provides valuable data to assess sales trends, profit margins, and holding costs, whereas warehouse management zooms in on the specifics of stock movement and execution.
Importance of Warehouse Inventory Management System:
Here are five reasons to consider using a Warehouse Management System:
Inventory Control and Management
A Warehouse Management System (WMS) helps manage inventory by reducing stock levels, improving order fulfillment, and speeding up order processing. It allows you to track every item in detail, ensuring accuracy in stock levels and orders.
With real-time updates, WMS provides quick and accurate information, helping businesses meet customer demands. Distributors and wholesalers always know what’s in the warehouse, where it’s located, and when it needs to be restocked.
Customer Service and Tracking
The warehouse is key to providing a great customer experience. Ensuring products are in stock and orders are fulfilled correctly is essential for good service. WMS improves picking accuracy, so orders are correct from the start.
It also simplifies the organization and tracking of shipments. Worker tasks, shipment routes, and stock movements are automated, leading to more accurate deliveries and happier customers.
Company Productivity
Your warehouse affects your company’s productivity. A Warehouse Management System makes operations more efficient, consistent, and controlled by helping move goods quickly through the warehouse. Workers can achieve more in less time with the right tools and processes.
Return on Investment
The right WMS can increase sales and profits not just by selling more, but by selling faster and more accurately, which makes customers happy. It also helps your team handle more orders in less time with fewer errors, leading to fewer customer issues and less support needed.
Warehouse Management Vs Inventory Management
Inventory Management
Inventory management can be defined as the process of overseeing and controlling the procurement, storage, sale, and disposal or use of goods to ensure that the right product is available at the right place, at the right time, in the right quantity, and for the right customer.
It involves managing stock levels to meet demand and avoid shortages or overstocking, ensuring that products meet specific requirements such as color, size, and functionality. Essentially, inventory management focuses on optimizing the availability of goods while balancing cost efficiency and customer satisfaction.
Inventory is a modern necessity for businesses, much like how a car or truck carries a spare tire to avoid being stranded during a puncture. Similarly, companies maintain inventories of raw materials and finished goods to ensure smooth operations without delays.
Inventories are essential for any physical distribution system, as products cannot be distributed without stock. However, carrying inventory comes with costs and investments, and it directly impacts transportation and logistics costs. For instance, if a company’s inventory policy requires maintaining large stocks, it may opt for Full Truck Load (FTL) shipments to optimize transportation efficiency.
Warehouse Management
Warehouse management systems (WMS) are designed to oversee the movement of goods and labor within a warehouse or fulfillment center. Basic WMS tools handle tasks like picking, packing, and shipping, while advanced systems also manage inventory, demand planning, labor, and other supply chain operations.
A robust warehouse management system can enhance workflow efficiency, reduce errors, lower error-related costs, and accelerate order fulfillment times. However, adopting and operating a WMS can be both time-intensive and expensive. This involves significant upfront investment in hardware, extensive training, and recurring monthly maintenance costs.
Earlier warehouse management system versions were simpler, primarily focusing on tasks such as locating stored products. Modern systems, however, are highly sophisticated and may require a dedicated team to operate and fully utilize their features.
If you work with an experienced 3PL for your shipping and logistics needs, they are likely equipped with a warehouse management system and can manage it to optimize the movement of your products within their facility.
Inventory Control
- Core Questions in Inventory Control:
Inventory control system focuses on three main questions: whether an item should be stocked, when to reorder it, and how much to order, with the last two being more critical as they directly affect stock levels and operational efficiency.
- Avoiding Over or Understocking:
Proper inventory control ensures that no item is overstocked or understocked, as both scenarios can lead to unnecessary costs or missed sales opportunities.
- Stock Levels Align with Business Policies:
General stock levels should align with the company’s sales and production policies, just as product specifications align with technical requirements.
- Deficiency and Out-of-Stock Levels:
The deficiency level indicates insufficient stock to meet needs, requiring faster procurement methods. The exhaust bin level, or out-of-stock point triggers emergency restocking measures.
- Buffer Stock Importance:
Buffer stock acts as a reserve to meet immediate demand if fresh supplies are delayed. Orders are placed through normal channels as inventory approaches this level to prevent stockouts.
Role of Warehouse Inventory Management in the Supply Chain
Inventory Balances Supply and Demand
Inventory exists across the supply chain to manage the mismatch between supply and demand. For example, manufacturers produce in large batches for cost efficiency, while retailers hold stock to meet anticipated customer needs.
Key Roles of Inventory
Inventory enhances responsiveness by ensuring products are readily available for customers and optimizes costs by leveraging economies of scale in production and distribution.
Impact on Responsiveness
Inventory levels directly affect supply chain responsiveness. High inventory improves responsiveness (e.g., customers immediately finding desired products in-store), while low inventory leads to delays, such as waiting weeks for production and delivery.
Relationship Between Inventory and Flow Time
Inventory impacts material flow time—the duration from when materials enter the supply chain to when they exit. Lower inventory levels reduce flow time, improving supply chain efficiency.
FAQ: Warehouse Inventory Management System (IMS):
What are the limitations of warehouse inventory management?
It can be limited by factors such as inaccurate inventory tracking, storage space constraints, high operational costs, complex software systems, and human error. These challenges can impact efficiency, accuracy, and costs.
What are the reasons for holding inventory in a warehouse?
Warehouses hold inventory to ensure products are available when needed, buffer against supply chain disruptions, reduce lead times, and take advantage of bulk purchasing. This also helps maintain a steady production flow and meet customer demand.
What is EOQ in warehouse inventory management?
EOQ (Economic Order Quantity) is a formula used to determine the optimal order size that minimizes total inventory costs, including holding and ordering costs. It helps balance inventory levels and reduce storage and ordering expenses.
Conclusion
A warehouse inventory management system is essential for optimizing warehouse operations, improving efficiency, and reducing errors. By implementing an advanced WMS, businesses can streamline inventory tracking and enhance customer satisfaction. To ensure seamless integration and growth, consider leveraging solutions like Qodenext for tailored inventory management that meets your evolving needs.