E-commerce requires space for storing, packaging, and shipping inventory. Many new business owners start by using their home office or garage, but as they grow, outsourcing fulfillment to a third-party logistics partner, such as a warehouse or fulfillment center, becomes essential.
“Warehouse” and “fulfillment center” are frequently used interchangeably.
However, they serve distinct roles in order fulfillment. While both types of facilities are crucial and share similar functions, their purposes and benefits differ significantly. To fully understand how they differ, it’s important to examine their specific functions and goals.
In this blog, we will explore the differences between fulfillment centers and warehouses, highlighting their unique capabilities and benefits to provide a clearer picture of how they compare.
Let’s take up each option individually so that you can easily figure out which shipping solution works best for your business.
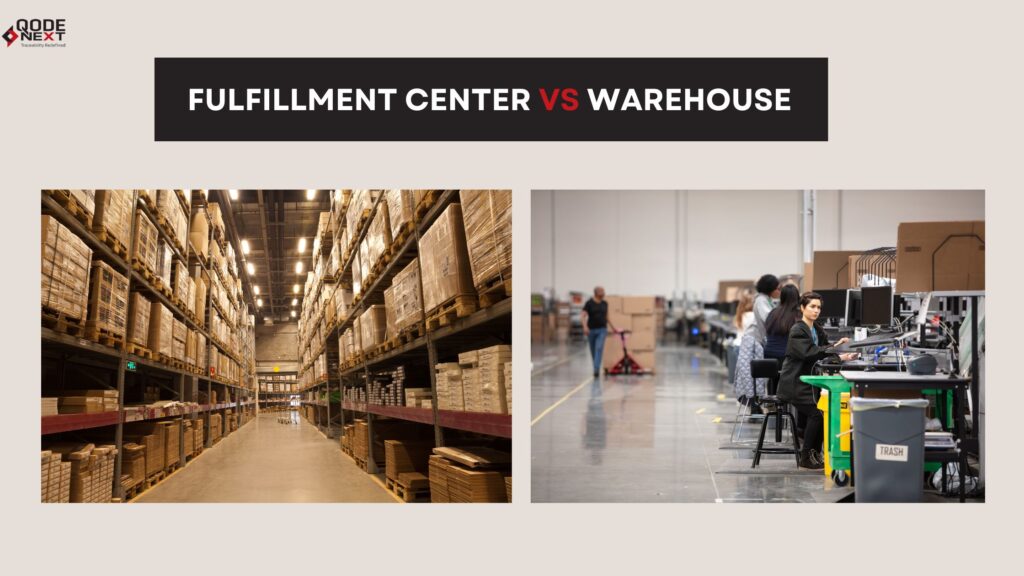
How Would You Define A Warehouse?
When you picture a warehouse, you probably imagine a vast space with towering shelves and forklifts zipping around to pick up or move products.
That’s spot on!
A warehouse is a large building where finished goods are stored until they’re sent to their final destination, such as retailers, wholesalers, or distribution centers. Warehouse sizes can vary widely, typically ranging from 10,000 to 100,000 square feet, and they play a crucial role in supply chain management.
The design and function of a warehouse depend on the type of inventory it stores. According to the objectives of warehousing, there are six different types of warehouses.
Various Types Of Warehouses
- Private Warehouse
- Public Warehouse
- Automated Warehouse
- Climate-Controlled Warehouse
- On-demand Warehouse
- Distribution Center
What is fulfillment center then? Well, let’s find out.
How Do You Define a Fulfillment Center?
A fulfillment center might look like a warehouse and also store goods for different companies, but that’s where the similarities end.
While warehouses are designed to store products for extended periods, fulfillment centers typically handle fast-moving items that are frequently shipped out. The primary role of a fulfillment center is to get products to customers or end-users as quickly as possible.
Fulfillment centers work with retailers, e-commerce companies, and others to handle both B2B and B2C orders, ensuring goods reach their final destination efficiently.
For instance, when you order a new pair of shoes online, they’re likely shipped from a fulfillment center rather than a warehouse. A large shoe retailer might store extra stock in a warehouse and periodically send it to a fulfillment center for quicker distribution.
There’s also something called a 3PL fulfillment center.
A fulfillment center that is operated by a 3rd Party Logistics provider (3PL) is called a 3PL fulfillment center. It offers inventory storage along with a range of other services like freight transportation, cross-docking, customer service, and, most importantly, fulfilling orders.
How Do Fulfillment Centers Operate?
Here’s a simple breakdown of how a fulfillment center works:
Receiving and Storing Inventory
Products from suppliers or manufacturers arrive at the fulfillment center in bulk. These items are scanned into the system and stored in specific locations within the center.
Inventory Management
The center tracks inventory levels for each product, ensuring they have enough stock to meet demand without overstocking. Many fulfillment centers use advanced software to monitor inventory in real-time.
Order Processing
When a customer places an order, the center picks the items from storage, packs them securely, and prepares them for shipping.
Shipping
The packaged order is labelled and handed over to a carrier like FedEx, UPS, or a local courier, which then delivers it to the customer.
Returns Management
Fulfillment centers also handle returns. If a customer sends something back, the center processes the return, checks the condition of the item, and restocks it if it’s still in good shape.
Fulfillment Center vs Warehouse: What’s The Difference?
At first glance, you might notice that a fulfillment center might seem similar to a warehouse, but they actually serve different purposes.
So, what sets a fulfillment center apart from a warehouse in terms of how they operate? Let’s find out with the help of these key differences.
1.Goals
Warehouse
- A warehouse is primarily focused on the safe and efficient long-term storage of inventory, often keeping products for several months or even up to a year.
- They typically store a limited range of inventory types for extended periods, ensuring that items are securely housed until they are needed.
Fulfillment Center
- A fulfillment center, on the other hand, is all about speed and efficiency in processing orders.
- These centers are designed to move products quickly, usually storing inventory for only a few months at most.
- Their operations are streamlined to fulfill orders as fast as possible, prioritizing quick turnaround times over long-term storage.
2.Storage
Warehouse
- Warehouses are designed for long-term storage, often holding large quantities of inventory that may not be needed right away.
- Products stored in warehouses are not accessed frequently, making it ideal for keeping surplus inventory or items that are only in demand during certain seasons.
Fulfillment Center
- Fulfillment centers, on the other hand, focus on short-term storage, with the primary goal of quickly moving products in and out.
- Inventory is constantly flowing through these centers, ensuring that products don’t sit idle for too long.
3.Operations
Warehouse
- In a warehouse, inventory typically arrives and leaves on large shipping pallets. Most of the logistical operations here revolve around handling freight carriers or sometimes working with intermodal providers.
- The primary focus is on storing goods and managing bulk shipments, often for longer periods.
Fulfillment Center
- Fulfillment centers, on the other hand, receive inventory in palletized shipments but ship out products in smaller, parcel-sized packages.
- These centers are designed to quickly pick, pack, and ship orders directly to customers, often holding inventory for only a short time.
- E-commerce retailers, like Amazon, rely on a network of fulfillment centers and delivery stations to efficiently manage and expedite shipping, enabling fast delivery.
4.Customers
Warehouse
- Warehouses typically cater to business-to-business (B2B) clients.
- Their primary role is to store large quantities of goods that are distributed in bulk to other businesses, retailers, or distribution centers.
Fulfillment Center
- Fulfillment centers are mainly designed to handle direct-to-consumer (D2C) and online orders, commonly referred to as e-commerce or business-to-consumer (B2C) operations.
- Some fulfillment centers also serve a dual purpose, managing both retail and online orders for various brands.
5.Pickups
Warehouse
- Since items are stored for extended periods, pickups are scheduled less frequently and offer less flexibility in terms of shipping options.
- While this can be cost-effective for shipping multiple items to a single address with a common delivery date, it doesn’t typically meet the demands for fast shipping to various locations.
Fulfilment Center
- In a fulfillment center, inventory flows more continuously, starting as soon as an order is placed.
- This means that shipping companies must pick up packages more frequently to ensure timely delivery to customers.
- Some carriers might have set pickup schedules, while others could arrange daily pickups based on the seller’s needs and the types of shipments being sent.
Choosing the Right Solution for Your Business
Before coming to a conclusion you need to take the following points into consideration:
Understand the Purpose
Warehouses and fulfillment centers serve different roles. As a business owner, it’s important to choose the right option based on your needs. A fulfillment center offers full operational integration, allowing you to reach a wider network and maintain high customer satisfaction, whereas a regular warehouse is more suited for long-term storage.
Value of Consolidated Services
Unless your goal is simply to store products for an extended period, a fulfillment center’s comprehensive services are typically more beneficial. These centers handle everything from inventory management to order processing and shipping, making them a more versatile solution.
Limitations of In-House Fulfillment
Managing fulfillment in-house can limit your flexibility. Relying on just one or two locations restricts your ability to optimize for fast shipping, which can negatively impact the customer experience. It’s harder to scale and adapt quickly to changing demands.
Need for Flexibility
In today’s market, the ability to adapt and respond quickly to customer needs is crucial. Customers expect fast, free shipping, and a traditional warehouse setup often can’t provide the level of speed and flexibility required to meet these expectations in the long term.
FAQs: Fulfillment Centers Explained: How They Differ from Traditional Warehousing
Do fulfillment centers handle inventory management?
Yes, fulfillment centers do manage and sort inventory, keeping track of stock within the warehouse. However, their primary focus is on efficiently processing and shipping orders to customers as quickly as possible.
What is the best example of an online fulfillment center?
The best example of an online fulfillment center is Amazon Fulfillment. When a customer places an order on Amazon, the fulfillment center picks, packs, and ships the items directly to the customer, often with expedited shipping options.
How much square footage do you need for a fulfillment center?
The required space will depend on your growth plans and the nature of your business. You’ll want to avoid moving into, renting, or leasing a space that you’ll quickly outgrow.
Conclusion
In short, fulfillment centers and traditional warehouses have different roles. Fulfillment centers are all about quickly processing and shipping orders, offering flexible and fast delivery. Warehouses, on the other hand, focus more on long-term storage and don’t prioritize fast shipping.
If you want to improve how you handle orders and boost customer satisfaction, QodeNext can help. They offer customized solutions to streamline your operations, making sure you have the right setup to match your growth and business needs.