A built-to-suit warehouse is a custom facility for a particular business. Unlike traditional warehouses, they are built using exact standards tailored to operational, spatial, and logistical needs.
In addition to accommodating different inventory profiles and layouts, these facilities also include flexibility in design, enabling companies to manage their inventory efficiently, pick accurately, and maintain streamlined operations. Let’s explore these in detail, including their types, benefits, and more.
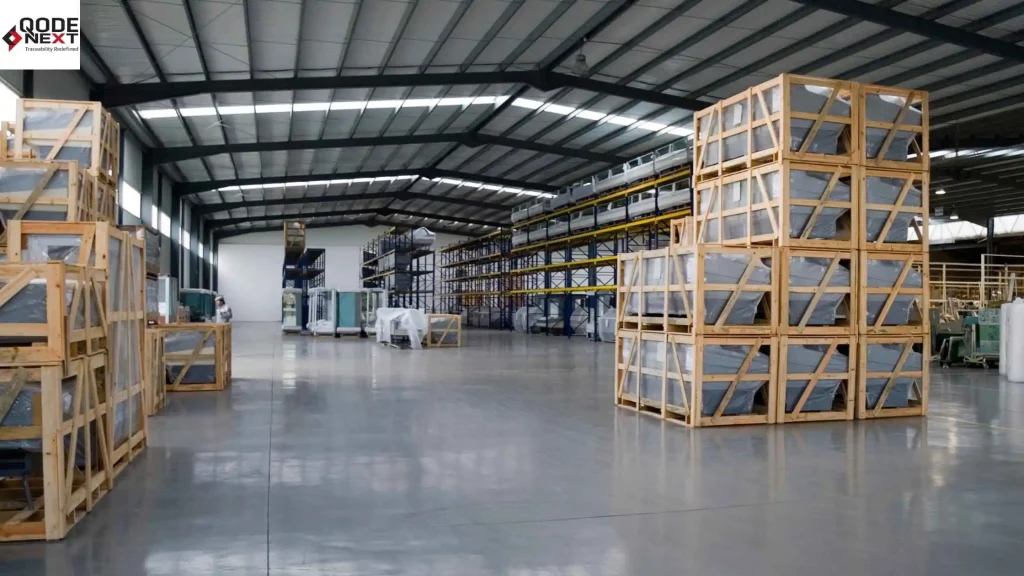
Built-to-Suit Warehouse Types
There are different types of warehouses to suit different business needs. Here are five common types:
1. Distribution Centers
Distribution centers are designed for rapid processing of goods, with a focus on an efficient layout and sophisticated material-handling systems.
2. Cold Storage Warehouses
Cold storage facilities are built with temperature-controlled zones and strong inventory management systems, so they work really well for businesses that deal with perishables.
3. High-Cube Warehouses
These warehouses also maximize vertical space with high ceilings, making them perfect for businesses with diverse product lines.
4. Cross-Dock Warehouses
Cross-Dock facilities reduce the time of storing goods, allowing the quick transfer of goods from inbound transportation to outbound transportation.
5. Automated Warehouses
Automated warehouses are powered by the latest technologies, such as robotics and AI, optimized for efficiency and minimal manual intervention.
What are the Features of Built-to-Suit Warehouses?
These warehouses have been designed with modern amenities to serve specific functions:
- Custom Layouts: Create around specific workflows in a way that bottlenecks are minimal.
- Advanced Storage Solutions: Addition and integration of pallet racking systems, mezzanines, and other space-saving technologies
- Sustainability Initiatives: Introducing green building materials, energy-efficient lighting, and solar panels.
- Integrated Technology: Leverage warehouse management systems (WMS) to improve inventory control and tracking
- Safety Features: Fire suppression systems by safety standards. Provisions for proper ventilation, and secure access.
Built-to-Suit Warehouses: How They Deliver Efficiency and Value
The concept of built-to-suit warehouses offers a wide range of strategic benefits that align with the specific requirements of companies. Adaptability to enduring asset value, such structures are changing the horizon of operational efficaciousness, and enhancing luxurious logistics. We will explore all these in detail.
1. Optimized Deployment: Customization for Fine-Tuned Operations
A key characteristic of these warehouses is that they can be tailored according to a business’s operational requirements. Unlike a generic warehouse, where square footage is wasted, these facilities optimize every inch, tailoring workflows, equipment placements, and storage systems to your goals.
A personalized approach improves productivity by minimizing the time and effort required to execute everyday tasks(such as stocking, picking, and shipping). A perishables business, for example, might need temperature-controlled areas, while an e-commerce company could require high-speed sorting systems. Customization is the key to making all the parts of a warehouse work towards operational excellence.
2. Improved inventory management and control
While managing inventory in any warehouse operation is crucial, built-to-suit warehouses take it one step further. These are further augmented with cutting-edge inventory management systems that help simplify how to control inventory in a warehouse.
Automated tracking, immediate updates, and integrated software minimize human errors, ensuring accurate stock levels and efficient replenishment. Lowering discrepancies helps businesses improve their order fulfillment rate, leading to a happier customer and less wastage.
3. Cost Efficiency and Savings
Although these kinds of warehouses might mean greater upfront costs, their longer-term economic returns speak for themselves. These facilities have emerged as some of the most energy-efficient buildings as they strive to install energy-saving fixtures such as better lighting systems, natural ventilation, and modern insulation.
The layout and process are optimized to reduce manual handling resulting in reduced labor cost. Custom workflows and advanced technology help significantly reduce operational downtimes, leading to cost savings in the long run.
4. Scalable Solution for Expanding Enterprises
As businesses expand, so does their warehousing requirement. These are scalable warehouse, meaning companies can scale up the facility’s capacity or reconfigure the layout of space as required. These types of warehouses adapt to the evolving business, whether through increased storage spaces, introducing new technology, or handling varying product lines.
Businesses no longer have to move operations to another location or upgrade their existing facilities, which consumes time as well as resources. These warehouses are guaranteed to be future-ready. Scalability is especially beneficial for transport industries that are witnessing exceptional growth (eCommerce, pharmaceuticals).
5. Improved Picking Accuracy
One of the most important operations in a warehouse is order picking, which influences the customer experience. Designed for best-in-class layouts and integrated technology to enhance picking accuracy, built-to-suit warehouses are designed for the future.
From systematic storage areas to modern warehousing management systems (WMS), these centers allow companies to find and extract products faster and more easily. Automated picking systems, barcode scanners, and RFID technology minimize errors, ensuring customers receive the right orders at the right time.
6. Reinforced Brand Identity
Warehouses are not just storage facilities; they also showcase the identity of a company’s brand. Built-to-suit warehouses present the opportunity to add branding elements to the design of the facility.
Everything from surface appearance to floor plans means that warehouse output can be designed to fit with corporate values and company image. This value is significantly higher for companies hosting clients or partners in their onsite facilities, building brand credibility and a place in their market.
7. Long-Term Value and ROI
Corners cannot be cut in the construction of the facility, and we understand this. Although the initial investment is certainly substantial to build, lease, or purchase a generic warehouse, the long-term benefits will far outweigh the cost. These facilities are designed to be extremely efficient, helping reduce long-term operating costs like energy, maintenance, and labor.
Their durability and advanced features make them less expensive to repair and replace. For businesses that aim to operate more effectively, built-to-suit warehouses can be a sound investment for long-term ROI.
The Complexity of Warehouse Management and How Built-to-Suit Warehouses Help
These warehouses help enhance warehouse management. Here’s how:
- Streamlined Operations: Eliminating unnecessary steps through server box layouts allows for better space optimization.
- Optimized Picking Processes: The design solves the challenge of warehouse picking accuracy, enabling faster order fulfillment.
- Inventory Visibility: Advanced tracking systems, often used by other logistics companies, help businesses monitor stock levels and avoid costly overstocking or stockouts.
- Improved Space Utilization: Increasing usable space with high-density storage and inventive solutions.
- Seamless Integration: Built-to-suit facilities can be designed to interface directly with existing systems so that there is no disruption.
FAQs – Built-to-Suit Warehouses
Define a built-to-suit warehouse.
A Location that is tailored to a particular business’s functional and spatial needs to improve efficiency and flexibility.
What is the difference between a built-to-suit warehouse and a regular warehouse?
Traditional warehouses are standardized, but built-to-suit warehouses are tailored to an organization’s specific requirements.
What are the main advantages of a built-to-suit warehouse?
These include increased efficiency, enhanced inventory management, improved scalability, and cost savings.
What is top-of-the-line in warehouse logistics: built-to-suit warehouses?
Automated solutions that optimize space and integrate state-of-the-art technologies for better logistics management.
Is it a capable tool for improving inventory accuracy?
Indeed, along with custom layouts and integrated WMS, the accuracy of inventory is enhanced substantially.
Are these storages for healthy living?
Many integrate green building practices, minimizing environmental impact and operating costs.
What types of industries use built-to-suit warehouses the most?
Tailored solutions provide tremendous value to e-commerce, retail, manufacturing, and logistics companies.
Conclusion
From growth to innovation, built-to-suit warehouses are the future of the logistics industry. Better inventory control to improved operational efficiency, these facilities offer a strong springboard of growth.
Presented below are the features and advantages of these systems, which can serve as an aid for a business looking to make wise decisions for effectively running a warehouse. And if you are a market player looking into built-to-suit warehouse options, make sure it fits your long-term plans and that it is equipped with the latest technology for you to keep up with the fast-paced logistics scene.
Are you facing supply chain bottlenecks? Learn how to revolutionize your logistics operations today. Reach out to Qodenext now!