Are you struggling to keep track of your inventory and production processes? Do you find yourself constantly running out of essential materials or overstocked on others? If so, you may want to consider utilizing a bill of materials (BOM) in your inventory management system.
A BOM is a comprehensive list of all the components and raw materials needed to produce a particular product. By creating a BOM, you can easily identify what items are needed, how much of each is required, and the cost associated with producing the final product.
In this blog, we’ll dive into the benefits of using a BOM in your inventory management system and provide expert tips for creating and utilizing one effectively.
So, let’s get started.
What Is a Bill of Materials?
An Overview. A Bill of Materials (BOM) is a comprehensive list of all the materials, components, and sub-assemblies required to manufacture a product. It serves as a central reference point for all the materials and parts needed to build a product, including their quantities, specifications, and sources.

The components of a BOM typically include:
1. Part number:
A unique identifier for each item in the BOM.

2. Description:
A detailed description of the item, including its material, dimensions, and other attributes.
3. Quantity:
The amount of each item required to build a single unit of the product.
4. Unit of measure:
The unit used to measure the quantity of each item (e.g., each, box, pound).
5. Source:
The supplier or manufacturer from whom the item will be sourced.
6. Cost:
The cost of each item, which is used to calculate the total cost of the product.
Types of BOM
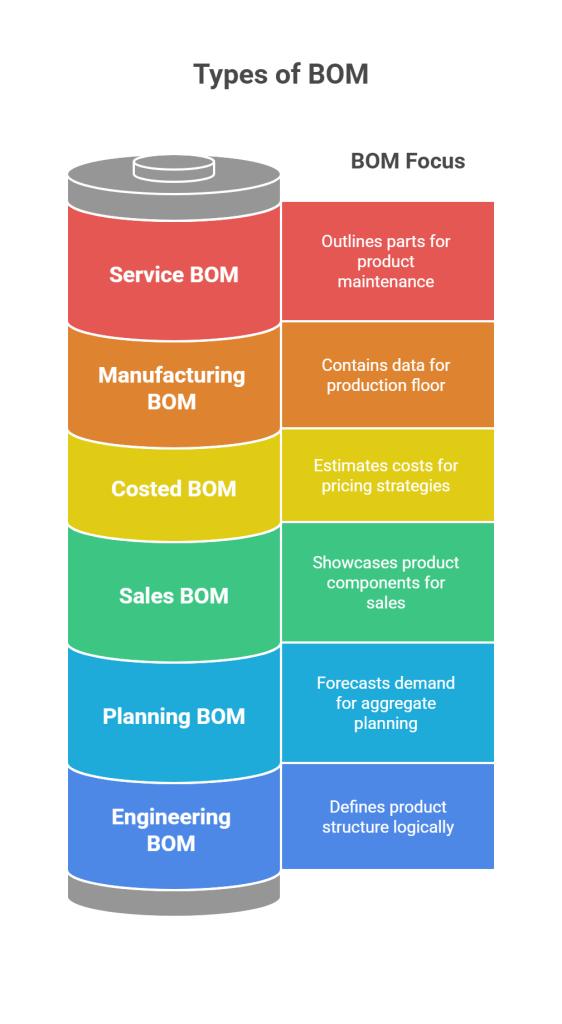
A Bill of Materials (BOM) is a comprehensive list of raw materials, components, assemblies, and sub-assemblies required to manufacture or assemble a product. BOMs play a crucial role in various stages of a product’s lifecycle, from design and production to sales and service. Below are the primary types of BOMs used across industries, along with their specific purposes:
1. Engineering BOM (EBOM)
The Engineering BOM is created during the product design and development phase. It defines the product structure as envisioned by the engineering team, including functional components and specifications.
- Used by design engineers.
- Typically created within CAD (Computer-Aided Design) or product lifecycle management (PLM) systems.
- Focuses on how the product is logically structured.
2. Manufacturing BOM (MBOM)
The Manufacturing BOM is used on the production floor and contains all materials, components, assemblies, and subassemblies required to manufacture the finished product.
- Used by production and operations teams.
- Includes additional data such as part numbers, quantities, and assembly instructions.
- Links directly to ERP systems for order processing and material tracking.
3. Sales BOM (SBOM)
A Sales BOM is prepared from a sales and marketing perspective and is used to showcase the end product along with its components.
- Useful in product configuration and quotations.
- Helps sales teams understand how items are bundled or packaged.
- Common in make-to-order businesses or products sold as kits.
4. Service BOM
The Service BOM outlines the components and replacement parts required for the repair, servicing, or maintenance of a product.
- Used by after-sales support and service departments.
- Helps in streamlining maintenance schedules and repair operations.
- Ensures parts availability in service depots or field operations.
5. Costed BOM
A Costed BOM adds an additional layer by including detailed cost information for each component.
- Used by finance and procurement teams to estimate the cost of goods sold (COGS).
- Facilitates pricing strategies, budgeting, and profitability analysis.
- Important for evaluating cost-saving opportunities or comparing suppliers.
6. Planning BOM
The Planning BOM is used for forecasting and planning purposes rather than actual production.
- Helps balance supply with anticipated demand.
- Involves setting up phantom items or product families for aggregate planning.
- Valuable in high-mix, low-volume manufacturing environments or seasonal industries.
BOM in Inventory Management
In inventory management, a Bill of Materials is essential for tracking the usage of components and raw materials during production. It ensures procurement and stock control teams are aware of which materials are required, in what quantities, and at what time. Here’s how BOM supports inventory functions:
- Tracks material requirements for each product or assembly.
- Triggers procurement when inventory levels fall below the reorder point.
- Enables accurate reservation of stock, preventing shortages during manufacturing cycles.
- Supports inventory optimization by reducing excess stock and carrying costs.
By maintaining accurate and up-to-date BOMs, manufacturers can achieve improved production planning, inventory accuracy, and on-time delivery, thereby streamlining the entire manufacturing and supply chain process.
By using a BOM, manufacturers can improve their production planning, reduce waste and errors, and optimize their inventory levels, ultimately leading to cost savings and improved efficiency.
Importance of Bill of Materials in Inventory Management
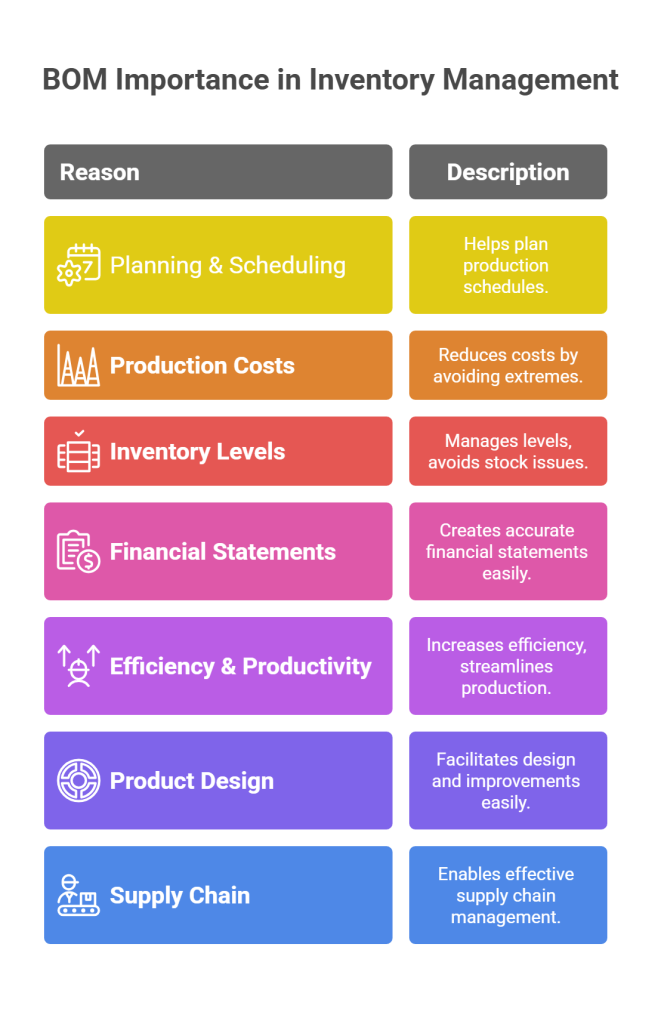
A Bill of Materials (BOM) is a detailed inventory that specifies all the necessary ingredients, intermediate parts, and constituent elements essential for the production of a final product. It serves as a vital document for manufacturers and is instrumental in the success of inventory management. Below are some of the reasons why a Bill of Materials is crucial in inventory management:
Helps in planning and scheduling production: A BOM provides a clear breakdown of all the components and raw materials required for a product. With this information, manufacturers can plan production schedules, ensuring that all the necessary components and raw materials are available at the right time. This helps in reducing production downtime and ensures that manufacturing processes are streamlined.
Reduces production costs: A BOM helps in reducing production costs. By knowing exactly what components and raw materials are required for a product, manufacturers can avoid overstocking or understocking. This ensures that only the necessary materials are purchased, thereby reducing inventory carrying costs.
Helps in managing inventory levels: A BOM helps in managing inventory levels. It provides manufacturers with a clear view of the components and raw materials required for a product, enabling them to keep track of inventory levels accurately. This helps in avoiding stockouts or overstocking, which can negatively impact production schedules and increase inventory carrying costs.
Helps in creating accurate financial statements: A BOM is essential for creating accurate financial statements. By tracking the cost of each component and raw material, manufacturers can accurately calculate the cost of producing a finished product. This information is instrumental in creating accurate financial statements, which are essential for decision-making and strategic planning.
Increases overall efficiency and productivity: A BOM increases overall efficiency and productivity. By streamlining production processes, manufacturers can reduce production time, reduce costs, and ensure that products are produced to a high quality. This, in turn, can increase overall efficiency and productivity, leading to higher profits and business growth.
Facilitates product design and improvement: A BOM is a valuable tool in product design and improvement. By providing a detailed breakdown of all components and raw materials, manufacturers can identify which parts of the product are driving the costs and which ones can be optimized to reduce costs. It also allows manufacturers to evaluate the impact of making changes to the product design, such as using alternative materials or components, on production costs and inventory levels.
Enables effective supply chain management: A BOM is crucial for effective supply chain management. By providing a detailed list of all components and raw materials required for a product, manufacturers can communicate their needs to suppliers accurately. This ensures that the right materials are delivered at the right time and in the right quantities, reducing delays in production and avoiding stockouts.
All in all, we can say that a BOM is a crucial document for manufacturers and inventory managers. It helps in planning and scheduling production, reduces production costs, manages inventory levels, creates accurate financial statements, and increases overall efficiency and productivity.
Tips for Creating an Effective Bill of Materials
Creating an effective bill of materials (BOM) is crucial in ensuring a smooth manufacturing process. A BOM is a comprehensive list of all the components, subassemblies, and raw materials needed to manufacture a product. It serves as a guide for purchasing, planning, and production, helping manufacturers maintain consistency, avoid delays, and reduce costs. Here are some tips on how to create an effective BOM:
Be thorough and accurate: It is essential to be comprehensive and accurate when creating a BOM. Every component, sub-assembly, and raw material that goes into the product should be included. Additionally, the quantities needed for each item should be specified, along with any relevant information such as size, weight, or color. Accuracy is vital to ensure that the production process runs smoothly and that the final product meets the desired specifications.
Standardize naming conventions: When creating a BOM, it is essential to use a consistent naming convention for each component. This helps avoid confusion and errors, ensuring that everyone involved in the manufacturing process understands exactly what each item is. For example, if a specific type of screw is called “bolt” in one BOM and “screw” in another, it can create confusion and delays during production.
Include supplier information: It is important to identify the suppliers for each component in the BOM. Knowing the supplier ensures that the necessary components are available when needed. Additionally, including supplier information allows foreasier communication and coordination with vendors, streamlining the supply chain and reducing delays.
Review and update regularly: A BOM is a dynamic document that should be reviewed and updated regularly to ensure its accuracy. As the manufacturing process evolves, updates to the BOM are often necessary. Additionally, changes in the availability or pricing of components may require updates to the BOM to ensure cost-effectiveness and timely production.
Use BOM management software: Utilizing BOM management software can streamline the BOM creation process, reducing errors and ensuring consistency. BOM management software can automate the process of creating, updating, and maintaining BOMs, reducing the time and effort required. Furthermore, software can ensure that BOMs are standardized, with a consistent format, naming convention, and information structure, reducing confusion and errors.
Conclusion
This blog highlights the importance of Bill of Materials (BOM) in inventory management, its types, and tips for managing them effectively. To optimize the process, businesses can use inventory management software solutions by Qodenext, that offers real-time tracking, BOM management, and automated replenishment.
By implementing such software solutions, businesses can streamline their operations, save time, reduce costs, and improve product quality. Contact Qodenext today to learn more about their inventory management software solution and improve your business’s inventory control.
FAQs – Bill of Materials (BOM)
1. What is a Bill of Materials (BOM)?
A Bill of Materials (BOM) is a detailed list of all the raw materials, components, subassemblies, and quantities required to manufacture a product. It serves as a blueprint for procurement, production planning, and inventory management, ensuring all necessary parts are available for efficient and accurate product assembly.
2. What are the key components of a BOM?
The essential components of a BOM include the part number, description, quantity required per product unit, unit of measure, supplier/source for each item, and cost. These elements allow manufacturers to track materials, control inventory, and calculate product costs effectively.
3. What are the different types of BOMs?
There are several types of BOMs, each serving a unique purpose:
- Engineering BOM (EBOM): Created by the design team to specify how a product is engineered.
- Manufacturing BOM (MBOM): Used in production to guide the assembly process.
- Sales BOM (SBOM): Helps in displaying bundled products or kits to customers.
- Service BOM: Used for maintenance and repair purposes.
- Costed BOM: Includes detailed cost information for each item.
- Planning BOM: Used for forecasting and planning material requirements.
4. Why is a BOM important in inventory management?
A BOM plays a critical role in inventory management by providing a clear list of required components, allowing businesses to plan procurement, avoid stockouts, minimize excess inventory, and align stock levels with production schedules. It supports accurate forecasting, efficient production, and real-time inventory control.
5. How does a BOM reduce production costs?
By outlining exact materials and quantities needed, a BOM helps manufacturers avoid over-ordering or under-ordering. This ensures optimal inventory levels, lowers carrying costs, reduces waste, and allows bulk purchasing where appropriate—all of which contribute to lower production costs.
6. How often should a BOM be reviewed or updated?
A BOM should be updated regularly, especially when changes are made to the product design, material availability, pricing, or supplier relationships. Regular reviews help maintain accuracy in production, cost estimation, and inventory planning.
7. What is a Costed BOM, and why is it useful?
A Costed BOM includes the cost for each listed item, allowing manufacturers to estimate the total production cost. It’s used by finance teams to calculate cost of goods sold (COGS), assist in budgeting, set product pricing, and identify areas for cost savings.
8. What are some best practices for creating an effective BOM?
To create an effective BOM, ensure it’s comprehensive and accurate, use standardized naming conventions, include supplier and sourcing information, review it regularly, and use BOM management software to automate and streamline the process. These practices help improve accuracy, reduce delays, and enhance workflow efficiency.
9. Can BOM software make BOM management easier?
Yes, BOM management software automates many aspects of BOM creation, maintenance, and version control. It reduces manual errors, maintains data consistency, supports real-time updates, and integrates with inventory and production systems for better control and visibility.
10. How does a BOM contribute to better supply chain management?
A BOM enhances supply chain efficiency by clearly outlining material requirements, enabling businesses to communicate needs accurately with suppliers. This helps reduce lead times, improve vendor coordination, avoid delays in production, and ensures just-in-time inventory availability.