Inventory management is the soul of any business. Many businesses face a “tightrope” situation with their inventory management. After all, they need to balance supply and demand, ensuring you have the right products, in the right units, at the right time.
However, this does not mean that there’s no room for errors. And even if there are inventory errors, they are completely avoidable and have solutions. This means that companies can lose billions of dollars annually.
But what are these errors?
Such errors are discrepancies between the actual physical and recorded inventory levels. Incorrect accounts may occur due to operational mistakes, inventory system inefficiencies, or unforeseen events. So, let’s see how to solve inventory problems.
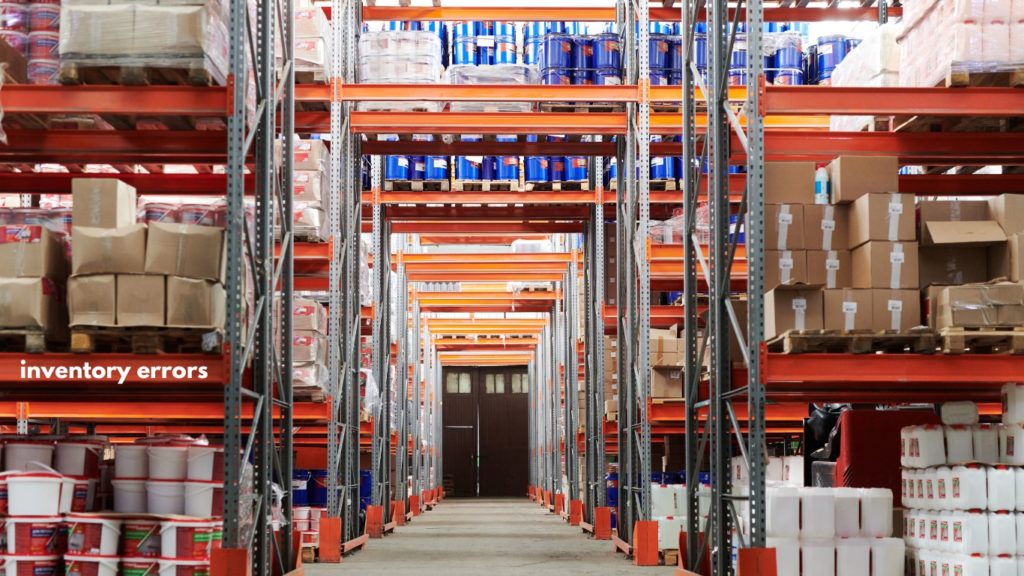
7 Common Inventory Errors
It’s human to make errors—there’s no doubt about that. Errors are always possible. However, knowing what kind of mistakes might occur can help you prepare and avoid them. Here are some of the common inventory errors:
Human Error
Humans make mistakes, and in the context of inventory, these errors can be costly. Manual processes may seem like the best way to conduct all operations. However, if you want to avoid human errors, you need to take proactive steps.
Solution
Firstly, you should double-check every time. Even if other systems have automation, it does not mean that there will be no errors. If the initial information that you input is incorrect, the entire process will be erroneous without being caught.
You can prevent these by:
- Constant education on quality control
- Automating the process
- Appoint a team to review the process before and after the automation so that you have the right numbers and data.
Apart from these, there are a few more inventory mistakes you need to know.
No Integration with Sales Channel
This is a big mistake.
In today’s era of an omnichannel retail environment, businesses sell their products via various channels, like online stores, physical stores, marketplaces, and social media.
Each of these channels has its inventory tracking systems, which can lead to discrepancies and incorrect updates across all channels. For instance, if the product is sold out on one platform but the other one is not updated, it might result in overselling.
Solution
Centralised inventory system.
Implementing an integrated inventory management system helps you to synchronise inventory levels across all sales channels in real-time. This ensures that your inventory data is accurate and up-to-date, reducing the overselling risk and meeting customer demand.
Let’s see the next set of inventory errors.
Not Analysing Data
If you use an integrated inventory management system, you must continuously pull and track data points. This can help to improve your business but only when you utilise it to the fullest.
If you’re not analyzing data weekly, you might be overlooking crucial inventory errors or successes in your workflow.
Solution
Regular data review aids inventory planning by tracking consistent orders, identifying frequently out-of-stock SKUs, and allowing you to adjust purchase orders and pricing as needed.
No Plan for Holiday Spikes in Volume
Major holidays like Christmas, Independence Day, and Memorial Day often lead to a surge in sales volume, especially when exclusive deals are offered. Even without big sales, eCommerce companies and warehouses can anticipate increased shopping during these periods.
Solution
By leveraging data and market trends, you can plan for these spikes, avoiding the inventory errors of understocking or overstocking, and ensuring a solid strategy is in place well in advance.
Here is another one of the most common inventory errors that companies face.
Failing to Count Your Inventory Regularly
Even if your warehouses have a fully automated process, it’s still advisable to do a quarterly inventory count by hand, if you can.
Some warehouses provide the staff incentive for this extra process. Numbers can be off, even if the counting process is seamless. Also, conducting a company-wide inventory count is a good way to re-analyse company inventory, especially at the start of a new quarter.
Solution
You can also compare the records on the systems to assess if there are any discrepancies. This type of quality control helps to alleviate slow-moving inventory and ensures that SKUs are in their proper places.
It also finds the gaps. With the inventory models, problems and solutions, you will easily notice when you look at the wider picture of the workflow.
Here are a few more common inventory problems.
Overstocking and Understocking
When a business has excessive inventory, that is overstocking. It blocks all valuable capital and storage space. Simultaneously, understocking is a result of insufficient inventory levels that fail to meet customer demand.
So, how can you solve such inventory management problems?
Solution
Effective Demand Forecasting. The key to managing understocking and overstocking is using sophisticated analytics and reports dashboards. This gives you a better understanding of your data. You can keep track of all upcoming events while checking on the future inventory levels.
Mishaps happen when you enter addresses incorrectly, whether by you or the customers. You can update codes in your warehouse management system to flag addresses or zip code mismatches. This ensures no incorrect address, which helps with fewer returned packages and increas customer satisfaction.
Keeping Disorganised Warehouse
Inventory errors are often caused by disorganisation in warehouses. It could lead to mishaps, miscounts, lost inventory, and unsafe conditions. Therefore, it’s crucial to have best practices early on in the warehouse organisation to solve all problems.
Solution
Implementing best practices allows warehouse employees to work faster and more efficiently, enabling them to confirm their pick slips more easily. They will also stay safe without unsecured structures, bumping into each other and messy isles because of disorganised picking.
Such measures will curb most of your inventory errors. Make sure you have stations for picking, packing, shipping, and receiving returns, make sure they support the workflow and does not work against it.
Managing excess inventory problems can not only prevent them, but you can use these mistakes as opportunities to learn. In this way, they don’t repeat, saving you time and money. Usually, making a small inventory error is easy to correct. However, it’s important to keep the processes secure, so your business does not lose money or a good reputation.
FAQs:7 Common Inventory Errors and Their Proven Solutions
What are the results of errors of inventory on the businesses’ finances?
Inventory mistakes distort a business’s financial reporting as they inaccurately reflect its assets, cost of goods sold, and revenues. This may mislead investors, affect tax liabilities, and even lead to regulatory assessment if the discrepancies are significant.
How can companies rectify errors in inventory to maintain an accurate balance sheet?
A company can do so by reassessing its physical stock and reconciling it with the documented inventory. They can adjust entries in the financial records and implement robust inventory management. This will help them avoid future mishaps.
What are the common causes of inventory mishaps?
These may include human error, theft or loss of goods, incorrect data entry, misplacing stocks, inaccurate historical data, damaging or spoiling inventory, and system errors in accounting and tracking.
Conclusion
By addressing these common inventory management errors, your business can significantly reduce losses, improve efficiency, and enhance customer satisfaction. Implementing the right solutions—like automation, data analysis, and proactive planning—will help you avoid costly mistakes and ensure smooth operations.
Regular inventory checks and a centralised system are key to maintaining accuracy. Partner with Qodenext to streamline your inventory processes, ensuring accuracy, reliability, and scalability at every step. Take control of your inventory management with inventory errors today!