More than 100 million foodborne ailments are contracted in India each year. Regrettably, 120,000+ annual deaths are directly attributed to these illnesses. The COVID-19 pandemic has furthered the already escalating demographic-driven pressure of the increasing population.
Unsurprisingly, food safety risks are a constant concern for companies in the FMCG sector, with the potential for broad financial and reputational consequences. The conventional methods of monitoring and responding to food safety challenges are no longer adequate given the rapid growth in global sourcing networks, brand proliferation, and consumer demand for transparency.
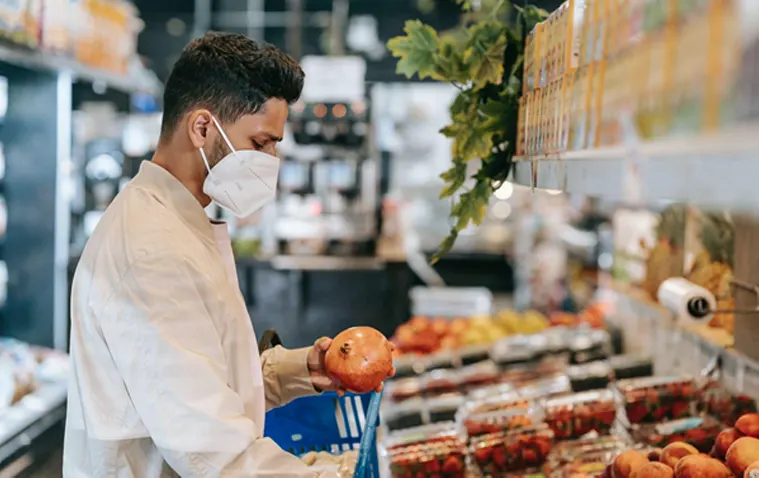
And while transparency in supply chains has been a buzzword of late, the seemingly proactive traceability measures fall short in one or the way. For instance, they:
- Do not provide the ability to move with agility and speed in case of a crisis
- Do not support collaboration with suppliers and logistics providers to give timely, actionable data to aid in decisions, pinpoint areas of concern and mitigate risks
- Do not facilitate end-to-end visibility into the full journey of the consumer product
As a result, organisations face the challenge of operating in a ‘fog’ of information and lack the capabilities to take action – certainly a hapless position to be in any time, but especially during a crisis (COVID serves as a genuine example).
So, the notion of granular monitoring of the supply chain through real-time visibility, coupled with end-to-end collaboration in response to an issue is fundamental and not a theoretical construct.
Along those lines, below are some high-tech ways in which companies can provide greater visibility and response agility into their supply chains for addressing and alleviating food safety challenges.
Digitising the Vendor Portal
From a grander perspective, there are several reasons why the vendor end, i.e., the component level, should be digitised. They pertain to the need to amalgamate the source production data — mapping the journey from farm to production, accessing the vendor plant capacities and qualities, vendor material sourcing action plans, and comprehending and improving the vendor production plan.
All in all, the idea is to provide a much more comprehensive view of the vendor’s end of the supply chain, thus, paving the way for real-time visibility into the vendor’s product material flow, logistics GPA, material sourcing plans, etc.
Overcoming challenges in this regard would entail attaining the same level of granularity across all the internal systems (i.e., ERP, CRM, etc.) that would be required to support this enhanced visibility into the real-time data.
Tracking Plant's Production for Agile Crisis Management
From ensuring compliance to providing a means of quality assurance, tracing the plant’s production process can benefit companies in several ways. This translates to, for instance:
- Providing information on any contractual limitations that may exist with respect to the vendor’s production capabilities and/or capacities
- Validating the ingredients in terms of the quality and integrity of the raw materials to mitigate the risk of contamination
- Verifying packaging specifications to minimise potential product safety hazards and lowering the probability of a product being recalled
- Recording production or test batch data to improve vendor production plan
Visualising the Warehousing and Transportation of Goods
The pipeline models, which provide an end-to-end visualisation of the transportation process, are becoming increasingly popular and afford companies with a dynamic and real-time picture of the movement and location of their goods.
For example, Qodenext’s warehouse and logistics solution for FMCGs:
- Automates GRN and warehouse replenishment processes
- Reduces inventory wastage through the use of intelligent routing
- Leverages intelligent job allocation and intelligent scheduling to optimise warehouse usage and improve the efficiency of the delivery cycle, respectively.
- Helps visible monitoring of transportation activities to minimise risk, improve control, reduce the turnaround time, and increase client satisfaction.
Digitising the Retail Portal
Much like vendor’s side digitisation, there are several reasons why companies should digitise their retail portal – e.g., real-time visibility into the product materials supply chain, synchronisation of the inventory with the vendors’ end, and other like functionalities like:
- Monitoring the food safety conditions at the retail stores
- Identifying and tracking shelf-life of product materials
- Leveraging the product information to market the same to the consumers
- Improving the retailers’ merchandising and pricing decisions, among many others.
Ensuring Traceability
With the use of the right solutions, all the above initiatives can be championed by organisations to ensure high-grade traceability in their supply chains. Here, traceability refers to the capability of:
- Tracking the origin of raw material and knowing the source product batch information
- Having an active channel of communication with all vendors and suppliers for fostering transparency into the entire supply chain
- Isolating the supply chain risks and any potential contamination quickly
- Allowing companies to distribute information fast, to the right people, in the right manner to facilitate quick decision-making and reduce downtime
- Making corrective decisions for product recalls, including the cost involved in executing them
The Bottom Line
Food safety is a critical aspect of the food industry. And, with the advent of advanced technologies, companies have several technologies at their disposal to bolster their capabilities in assuring that food safety risks are minimised within their supply chains.
At Qodenext, we deliver seamless traceability solutions solution to enable FMCG companies to:
- Quantify and qualify the quality of raw materials
- Track the products at every stage of the supply chain for optimum product quality and safety
- Reduce the need for product recalls
- Prioritise the risks of product recalls with respect to their overall risk profile
- Prioritise the focus areas for supply chain management
Altogether, these digitisation efforts streamline the traditional supply chain operations and equip FMCG companies with superior flexibility and agility to evolve and provide a much safer product to their customers.