As companies across different industries become more global and customer-centric, the need for real-time updates on goods transportation has become critical.
Traditionally, companies spend much of their resources and time on tracing goods’ delivery manually. Most companies have a large number of trucks moving to-and-fro from their premises. They manually verify, monitor, and sequence these trucks, making it time-consuming and inefficient.
This poses a problem because it is not time-consuming, but even a single delay in the transportation process could cause a huge impact on the supply chain and lead to severe losses. In most cases, it’s difficult to pinpoint the exact cause of the delay as it is a fragmented space, and several stakeholders are involved in the process.
However, it can be addressed by implementing smart truck management solutions. Smart truck management solutions such as traceability introduce transparency in the process. They provide real-time traceability on the supply chain. They also improve the productivity of all the stakeholders, improve the operations, enable the stakeholders to take preventive actions to minimise instances of delays and accidents, and ensure that the products are delivered on time. Let’s look at how to make truck management smarter.
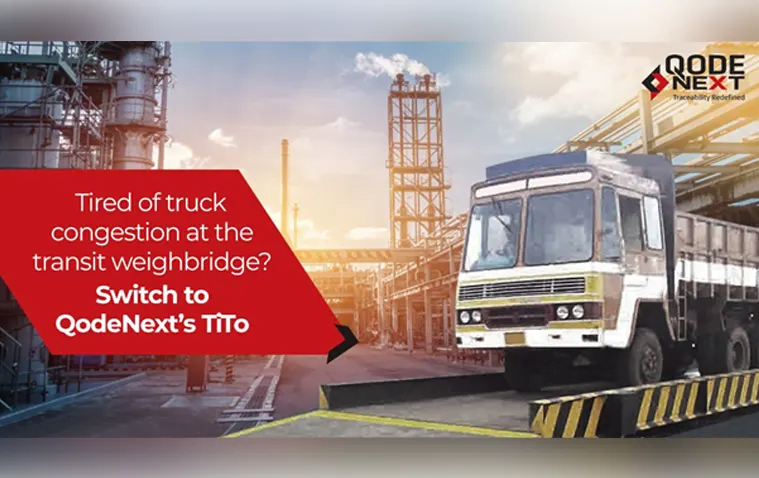
7 Ways to Make Truck Management Smarter
1. Improved tracking
Companies can use Radio Frequency Identification (RFID) to track the movement of trucks efficiently. By attaching RFID tags to every item, they can track their movement. Companies can also easily trace the goods if they are lost or stolen or defective with the help of RFID tags. The security validates the truck number and driver ID if they are already registered in the system or registers them and provides them with an RFID tag if they are new or independent trucks. Every time the truck travels through various checkpoints, an RFID reader reads the tag and uploads the details into the system. This helps in automatic check-ins and saves time on granting access or logging in the arrival or departure details.
2. Automated data entry
Paperwork is time-consuming and prone to errors. Sometimes it could also cause unnecessary delays in the check-in and check-out process, and there is a risk of incorrect data percolating through the logistics chain. By automating the data entry process, companies can save time on the arrival and departure process and ensure accuracy in data. They can also provide the truck drivers with advanced shipping notes, which can be scanned to upload the material details in the ERP. A digital record can enable companies to plan the routes and timings, make the right decisions, and track the materials’ details.
3. Trailer tracking
Trailer management is important as a lost or delayed consignment could lead to unnecessary losses to the company. Companies can use GPS to track trailers in real-time. The trailers can be fitted with in-built telematics to
- Enable real-time tracking and gain historical data of their movements
- Provide additional information such as the trailer status, location, etc.
- Check which trailers are in use, which can be leased, and which ones are underutilised
- Avoid mix-ups such as the wrong trailer delivered to wrong customers
- Save time and money on retrieving and re-routing the trailer in the right direction
4. Preventive maintenance
Unexpected repairs or breakdown of trucks could lead the company to severe losses. Trucks require regular maintenance to ensure that they function and deliver goods on time. Companies can fit the trucks with IoT-based sensors. The sensors will alert the company crew when it’s time to fix the vehicle and follow the maintenance routine regularly. It will also tell which parts require immediate replacement and ensure the overall vehicle’s health. All these measures enable the company to take preventive actions and reduce instances of unexpected breakdowns.
5. Weighbridge automation
Weighbridge automation helps in improving the overall supply chain process. Weighbridge automation can be integrated with the company’s internal software systems to manage the data and accounting efficiently. It helps in the weighing process under CCTV surveillance. So, there is minimal scope for fake weighing or double weighing of the vehicle and almost minimal chances of disputes or misunderstanding between various stakeholders. The real-time measurement also removes the need for someone to be physically present to measure the weighing spot. It also becomes possible to generate and send real-time reports on the weighbridges when demanded. All these factors enable the company to save on labour costs, win customers’ trust, and establish transparency in the process.
6. Bay allocation and bay time monitoring
Companies can use RFID to check if the truck has gone to the right loading and unloading bay. It can also be used to guide the driver to the right bay. Considering that an RFID tag is attached to the truck, the stakeholders can know when the vehicle is arriving and thus allot a free bay for loading and unloading and allocate a bay number to the driver. The RFID antenna also monitors the timing of the truck at the bay. It alerts the driver in case the truck exceeds the time limit.
7. Truck entry and exit
Technologies like RFID sensors can help companies track the truck’s movement efficiently. The RFID detectors can be placed at entry gates and exit gates of different locations. So, when the truck is about to enter, the RFID antenna placed at the entry gate reads the RFID tag and slog the details in the system for validation. Once validated, the boom barrier traffic lights get activated. Once the material is loaded or unloaded, and the truck moves out, the RFID tag is read at the exit gate, and the movement is logged.
Conclusion
As we can see, real-time traceability solutions enable smooth supply-chain management. Companies must invest in a comprehensive solution that can track the trucks and manage their movements efficiently.
At QodeNext, we offer comprehensive solutions that allow enterprises to:
- Automate truck check-in process to minimise bottlenecks at gates
- Sequence and optimise the movement of trucks to improve bay scheduling
- Enhance visibility of truck movement within the premises
- Maximise throughput capacity of trucks in a day to increase the productivity of production, dispatch, and shipment
- Reduce rental costs by improving truck turnaround time
- Decrease pilferage due to the cross-verification of the weighbridge
To know more about our truck management solutions, contact us.