In thе supply chain logistics, it is very important to еnsurе that thе products are safe and intact еvеry stеp of thе way. Sincе thе products go through various stagеs in thе supply chain, thеrе is always thе possibility of damagе or even getting lost.
To ensure optimum quality and that they reach the consumers on time, supply chain experts need to perform inspections. For this, there are two processes: inspection and testing. But what is the difference between inspection and testing in quality control? Find out below.

What is the Difference between Inspection and Testing in Quality Control?
Inspection involves visually examining products for defects, while testing employs systematic methods to assess functionality or performance. Inspection is subjective, focusing on appearance, while testing is objective, assessing specific criteria to ensure product quality and compliance.
To understand this difference between inspection and testing in quality control more vividly, let’s take a look at each of them in detail.
Inspection Procedure in Quality Control
Quality inspеction rеfеrs to thе еvaluating thе quality of a product or sеrvicе during thе production stagеs. This process ensures that the final product meets the required spеcifications and standards. This is an important step in the supply chain process for it helps to identify and correct any defects or issues before the product reaches the customers.
For instance, suppose you run a manufacturing company that produces electronic devices. Throughout the production process, the role of inspection in the quality control team is to meticulously inspect each device.
This will ensure they are devoid of defects like faulty wiring, cracked screens, and malfunctioning buttons. Know the difference between inspection and testing in quality control as you see the stages of inspection.
7 Stages Of Inspection in Quality Control
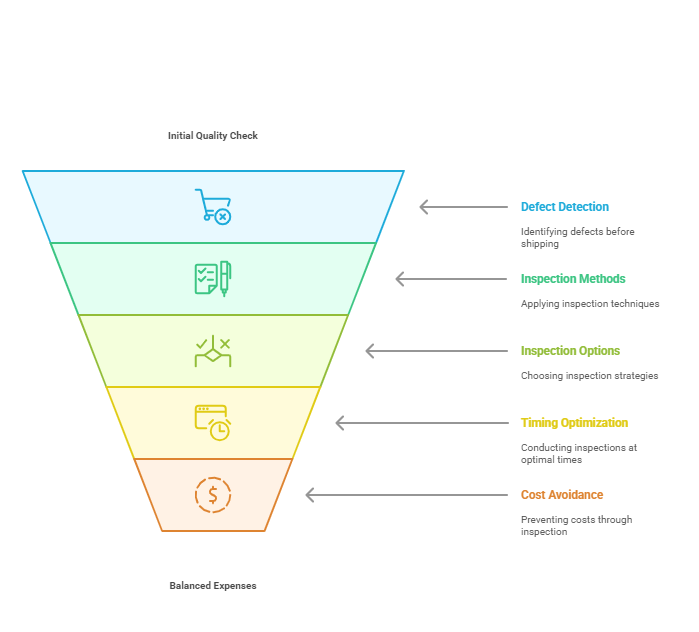
1. Ensuring Quality Control
Product inspection is a critical step in the manufacturing process, primarily conducted at the manufacturing facility. This phase involves comprehensive scrutiny of goods, focusing on their appearance, construction, and functionality, all crucial aspects evaluated before export.
2. Crucial Role of Detecting Defects Before Shipping
Detecting quality defects before shipping is paramount to facilitate timely corrections by the supplier. The difference between inspection and testing in quality control ensures this practice is essential in preventing significant damages and customer dissatisfaction upon receipt of the products.
3. Methods Employed by Quality Inspectors
Quality inspectors employ various tools, such as checklists and sampling methods like Acceptance Quality Limit (AQL), to assess products against specified criteria. These evaluations determine whether the products meet the required standards, leading to a clear pass or fail status.
4. Options for Conducting Product Inspections
Companies have three primary options for product inspections. Firstly, they can hire a third-party inspection company or maintain a full-time inspection team. The third way is to conduct inspections personally or through a representative. Each option comes with its pros and cons. The choice depends on the specific needs of the business.
5. Optimal Timing for Inspection: Pre-Shipment Inspection
Another major difference between inspection and testing in quality control is the timing of the checks. The ideal timing for product inspection is usually before shipment, commonly referred to as pre-shipment inspection. This strategic step identifies any discrepancies or defects and addresses them before the products reach the customers.
6. Importance of Pre-Shipment Inspection in Cost Avoidance
Consider the scenario of selling floral shirts where packaging and descriptions indicate a floral design. However, customers receive striped shirts, leading to the potential need for replacements or refunds.
This difference between inspection and testing in quality control highlights the avoidable cost and underscores the immense value of pre-shipment inspection. This practice reveals packaging errors before distribution.
7. Balancing Expenses with Mistake Prevention
While the implementation of pre-shipment inspection incurs appraisal costs for the business, these expenses play a crucial role in preventing costly mistakes. The upfront investment in quality control ultimately safeguards the business from potential financial setbacks and customer dissatisfaction.
While the inspection process is extensive, another process testing is equally important. Testing of the products is important before it reaches the hands of the consumers to ensure they are safe. However the testing process is extensive as well, so let’s see the difference between inspection and testing in quality control.
Testing Procedure for Quality Control in Supply Chain
Product testing is like lab testing but the former one is for supply chains to assess the quality and condition of the products in circulation. The products undergo the tests at a certified lab.
However, there are some exceptions where companies and supply chain logistics experts carry out on-site testing. So, let’s see what are the objectives of quality control and pre-shipment inspection in exporting.
How Do Supply Chains Conduct Product Testing
Supply chain experts usually do quality testing at each step of the manufacturing process. They will test the raw materials first, pulling samples from the manufacturing line and testing the finished product.
Running testing at various stages of manufacturing helps to identify exactly where the production problem is (if there is one). In this way, the experts can take remedial steps to prevent its recurrence in the future.
That is the difference between inspection and testing in quality control. So, when it comes to product testing, there are specific purposes. See them below.
Purpose of Product Testing: 3 Reasons for Doing It
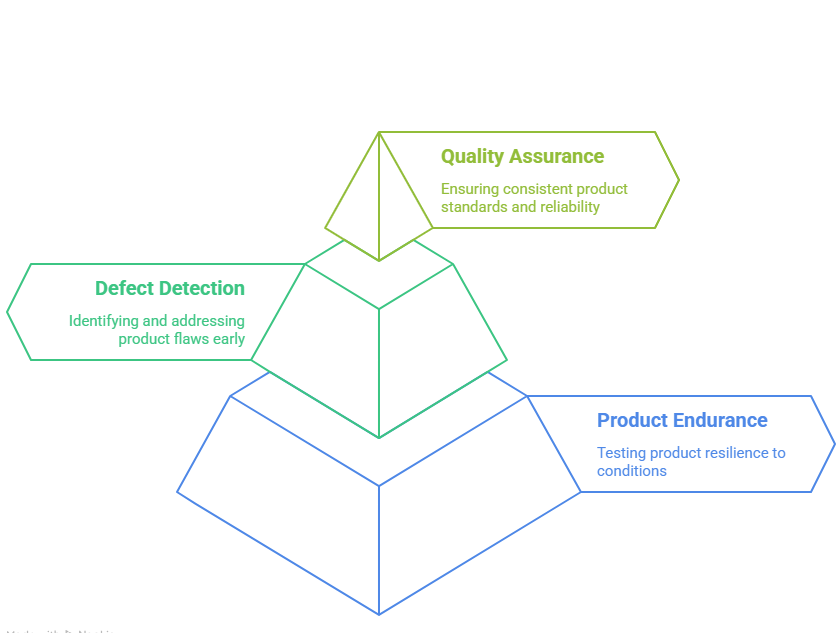
1. What Can Your Products Endure
Stress testing should be a key part of checking a product to see what kinds of pressures it can handle. This includes things like temperature, weather, pressure, or other tough conditions.
By doing stress tests, makers can simulate real-life situations that their product might encounter over its lifetime. They can do so without having to wait for the product to naturally age. This is the difference between inspection and testing in quality control.
For instance, if a product is regularly exposed to chemicals, it could dеvеlop corrosion over time. To prеvеnt this, manufacturers should tеst thе product with corrosivе matеrials, such as saltwatеr, to sее how it rеsponds.
2. Catch Product Defects Early
Knowing how long your product will last is crucial for customers to get their hands on it. Testing bеforе use is really important to make surе customers arе happy and thе product works properly.
In bigger situations, defects in a product could lead to serious injuries. To keep users safe and maintain your company’s good name, it’s vital to reduce the chance of defects by testing products.
3. Quality Assurance
You have to ensure that the products meet specific standards. This is one of the standard procedures that highlights the difference between inspection and testing in quality control. There are certain requirements that many products need to meet before supply chains have the green signal to distribute them and consumers can buy them.
Such a checkpoint is very crucial in an industry like the medical industry. This industry uses products like o-rings and seals in medical devices. Such components need to undergo testing and proper sanitation checks.
Conclusion
Understanding the difference between inspection and testing in quality control is vital in quality control. The meticulous stages of inspection, complemented by testing, minimise risks and enhance supply chain efficiency. Technology integration, balanced inspection and testing, and adherence to industry standards are key to maintaining a seamless and effective quality control system in supply chain logistics. Consult Qodenext for more expert tools and process integration to streamline your supply chain logistics
FAQs: Inspection and Testing in Quality Control
1. Why are both inspection and testing important in supply chain logistics?
Inspection and quality testing ensure a comprehensive approach to quality control, addressing both product integrity and performance through inspection and testing, respectively. There is a difference between inspection and testing in quality control. This balance minimises the risk of defects and enhances overall supply chain efficiency.
2. Can a company solely rely on either inspection or testing for quality assurance in logistics?
An exclusive reliance on either inspection or testing may leave gaps in quality assurance. A synergistic approach, leveraging the strengths of both, is best for a more robust quality control system.
3. How can technology enhance inspection and testing processes in the supply chain?
Technology, such as automation and data analytics, can streamline inspection and testing, improving accuracy and speed. Integration of IoT devices and AI-driven systems can provide real-time insights, enabling quicker decision-making and proactive quality management.
4. How to tell if a company’s quality control processes need reevaluation?
Warning signs include an increasing number of defects, customer complaints, or disruptions in the supply chain. Regularly monitoring key performance indicators related to quality can help identify areas for improvement and optimization.
5. How can companies stay updated on evolving industry standards for quality control?
Engaging in industry forums, attending conferences, and subscribing to reputable publications are effective ways to stay informed. Collaborating with industry peers and participating in continuous education programs can also provide valuable insights into emerging trends and best practices.
6. What is inspection and testing?
Inspection and testing are important steps to make sure products or services meet quality standards. Inspection means carefully looking at or checking products to find any problems or defects. Testing involves using tools or techniques to check if the product works properly and is safe to use. Together, these processes help catch issues early and ensure the final product is reliable and meets customer expectations.
7. How can businesses improve their quality control systems?
Businesses can improve quality control by setting clear standards and making sure inspections happen at every important stage of production. Training workers to identify problems quickly and using data to track quality helps reduce mistakes. Using technology and encouraging teamwork also make quality control more effective. Regularly reviewing and improving the system ensures products stay consistent and customers stay happy.
8. What is inspection quality control?
Inspection quality control is the process of checking products or materials to make sure they meet specific quality requirements. It involves looking for defects, measuring, and testing products during different stages of production. This helps catch problems early, maintain consistent quality, and avoid sending faulty products to customers. It’s a key part of managing overall product quality.
9. When should inspection take place during the supply chain process?
Inspection should happen at several points in the supply chain. First, raw materials should be inspected before production starts to avoid problems later. Then, inspections during production help catch defects early. Before shipping, a final inspection ensures finished products meet quality standards. Sometimes, inspection also happens during packing or loading to make sure everything is correct and safe. This step-by-step inspection helps maintain quality from start to finish.