In the fast-paced world of modern business, where agility and efficiency are paramount, lean supply chain management emerges as a strategic approach that goes beyond mere cost-cutting.
This blog will delve into the intricacies of what is lean supply chain management, exploring its principles, benefits, and implementation strategies, and providing a roadmap for businesses aiming to optimize their supply chain processes.
Let’s begin by breaking down the key principles of lean supply systems.

Principles of Lean Supply Chain Management:
Waste Elimination: Lean principles focus on eliminating waste in all forms—be it excess inventory, unnecessary transportation, or inefficient processes.
Continuous Improvement (Kaizen): A culture of continuous improvement encourages small, incremental changes to enhance efficiency over time.
Pull System: The supply chain operates on a pull system, responding to actual demand rather than pushing products into the market.
1. Value Stream Mapping:
Visualizing Processes: Value stream mapping involves visualizing the entire process from supplier to customer, identifying areas for improvement and waste reduction.
Streamlining Workflows: By streamlining workflows, businesses can optimize processes, reduce lead times, and enhance overall efficiency.
2. Inventory Management:
Just-In-Time (JIT) Inventory: Lean supply chains aim for JIT inventory, minimizing excess stock and holding costs.
Demand-Driven Replenishment: Systems are designed to replenish inventory based on actual demand, avoiding overstock or stockouts.
For a deeper understanding of how lean principles compare with other methodologies, check out our detailed discussion on Lean vs Agile, which highlights the strengths and weaknesses of each approach and helps you decide the best fit for your business.
Components of Lean Principles
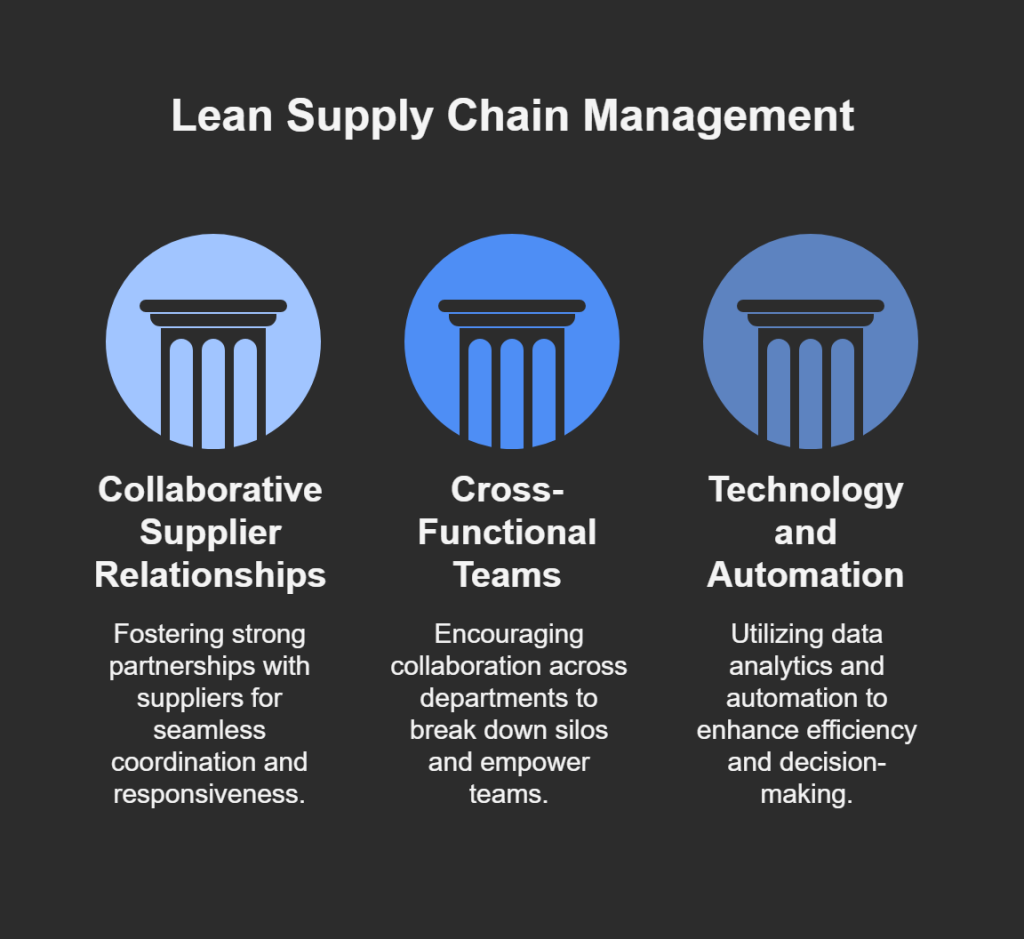
1. Collaborative Supplier Relationships:
Lean supply chain management fosters collaborative relationships with suppliers, creating a network that responds effectively to changes in demand.
Integrating suppliers into the planning process ensures seamless coordination and reduces the risk of disruptions.
2. Cross-Functional Teams:
Breaking Silos: The supply chain management encourages cross-functional collaboration, breaking down departmental silos for a more integrated and responsive approach.
Empowering Teams: Empowered teams are essential for driving continuous improvement and innovation within the supply chain.
3. Technology and Automation:
Data-Driven Decision Making: Leveraging data analytics and real-time information enables informed decision-making, contributing to lean practices.
Automation for Efficiency: Implementing automation technologies streamlines repetitive tasks, reducing errors and enhancing overall efficiency.
Benefits of Lean Supply Chain Management
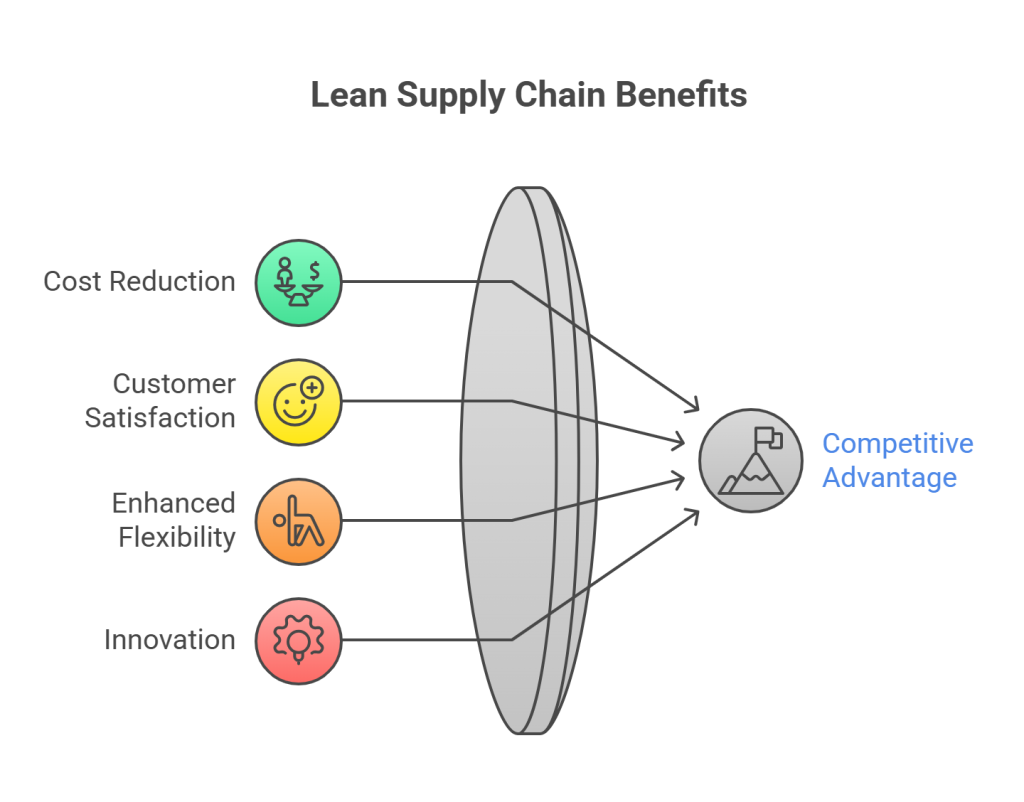
1. Cost Reduction:
Lower Holding Costs: By reducing excess inventory and adopting JIT principles, this type of supply chain management contributes to lower holding costs.
Operational Efficiency: Streamlined processes and reduced waste lead to operational cost savings.
2. Improved Customer Satisfaction:
Faster Lead Times: Lean supply chains often result in faster lead times, ensuring that products reach customers promptly.
Higher Quality Products: The focus on continuous improvement enhances product quality, contributing to customer satisfaction.
3. Enhanced Flexibility:
Adaptability to Changes: Lean supply chain management fosters adaptability, allowing businesses to respond swiftly to changes in customer demand or market trends.
Scalability: Lean principles make supply chains more scalable, accommodating growth without significant disruptions.
4. Competitive Advantage:
Market Responsiveness: The ability to swiftly respond to customer demands and market changes provides a competitive advantage in dynamic industries.
Innovation: Lean supply chains encourage a culture of innovation, positioning businesses as industry leaders.
Disadvantages of Lean Supply Chain Management
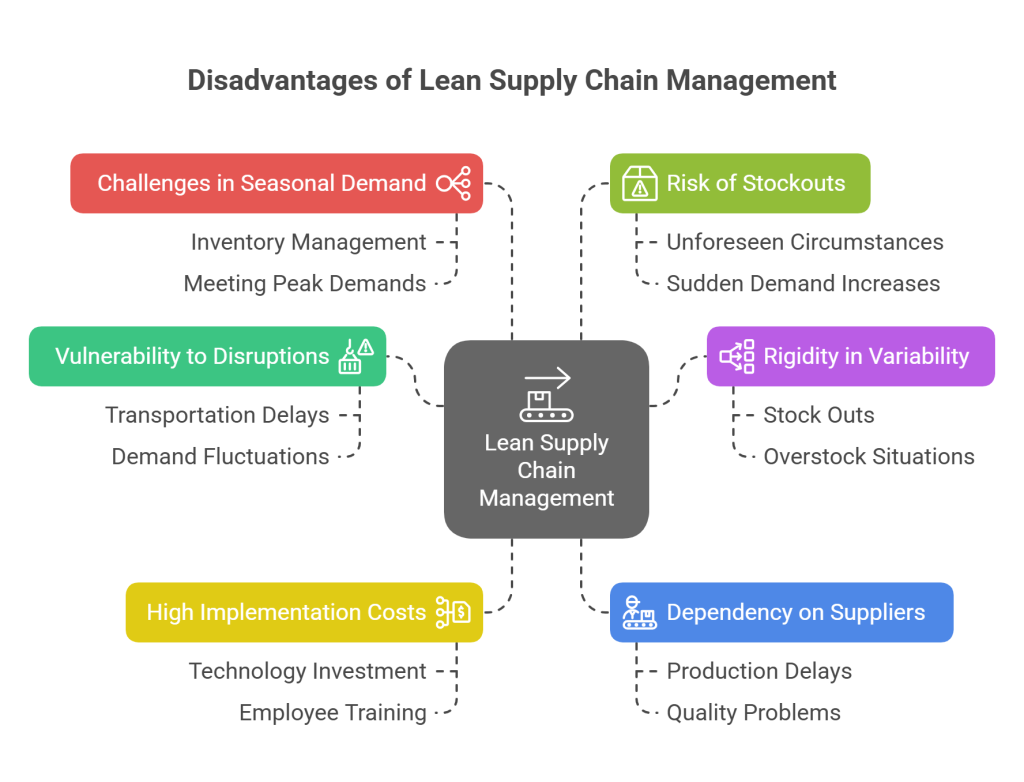
While lean supply chain management offers numerous benefits, it’s important to acknowledge that this approach may not be suitable for every business or situation. Here are some potential cons and challenges associated with lean supply chain management:
1. Vulnerability to Supply Chain Disruptions:
Lean supply chains typically maintain minimum inventory levels. While this reduces holding costs, it leaves businesses more vulnerable to disruptions in the supply chain, such as delays in transportation or unexpected demand fluctuations.
2. Rigidity in High-Variability Environments:
Less Adaptive to Variability: In industries characterized by high demand variability or frequent changes in customer preferences, the rigid nature of lean supply chains may struggle to adapt quickly, leading to potential stock outs or overstock situations.
3. High Initial Implementation Costs:
Investment in Technology and Training: Implementing lean practices often requires substantial upfront investments in technology, employee training, and process redesign. Small or resource-constrained businesses may find it challenging to make this initial investment.
4. Dependency on Supplier Performance:
Supplier Reliance: Lean supply chains depend on reliable and efficient suppliers. If suppliers face issues such as production delays or quality problems, it can disrupt the entire supply chain, affecting the downstream processes.
Challenges in Managing Seasonal Demand in Lean Supply Chains
Lean supply chains are built for efficiency, minimizing waste and reducing inventory levels. However, they can become vulnerable in industries with fluctuating or seasonal demand. Below are key challenges businesses face in such scenarios:
1. Difficulty in Seasonal Industries
Industries with significant seasonal fluctuations often struggle to align lean principles with demand peaks. Rigid inventory and production systems may not scale quickly enough, leading to missed opportunities or excess inventory after the season ends.
2. Risk of Stockouts
Lean supply chains maintain low safety stock levels to reduce holding costs. While efficient, this increases the risk of stockouts during sudden demand surges or supply disruptions—impacting revenue and customer satisfaction.
3. Inflexible Procurement and Supply Agreements
Long-term contracts or fixed sourcing models may hinder the ability to respond to changing seasonal needs. Lack of flexibility in procurement can lead to delays or an inability to secure enough inventory during peak periods.
4. Greater Impact from Forecasting Errors
Lean systems depend heavily on accurate demand forecasting. Any error, especially during high-demand seasons, can result in significant inventory shortfalls or overstock, both of which are costly.
5. Production Bottlenecks
Lean manufacturing setups are typically optimized for steady, consistent output. During seasonal peaks, these systems may lack the agility to scale up production rapidly, leading to delays or missed deadlines.
6. Extended Lead Times
Global sourcing in lean systems can result in longer lead times. In seasonal industries, delayed shipments can cause inventory shortages during critical sales periods, affecting performance and profitability.
Lean Supply Chain – A Detailed Guide with Examples
Lean logistics is a critical component of lean supply chain management. It focuses on optimizing transportation, warehousing, and distribution to eliminate waste and improve flow. By streamlining logistics processes, companies can reduce costs, improve delivery times, and enhance overall supply chain performance
1. Procter & Gamble (P&G):
Industry: Consumer Goods
Overview: P&G has embraced lean supply chain principles to streamline its operations. The company collaborates closely with suppliers, implements demand-driven replenishment, and uses technology for real-time data visibility. These strategies have enabled P&G to reduce lead times, improve inventory turnover, and enhance overall supply chain responsiveness.
2. McDonald’s Corporation:
Industry: Fast Food
Overview: McDonald’s employs lean principles in its supply chain to ensure the consistent and timely delivery of ingredients to its restaurants worldwide. The company utilizes a just-in-time inventory system to minimize holding costs and waste. Additionally, McDonald’s has established strong relationships with suppliers to maintain quality standards and reduce supply chain disruptions.
3. General Electric (GE):
Industry: Industrial Manufacturing
Overview: GE has implemented lean supply chain practices to optimize its manufacturing processes. The company focuses on reducing lead times, improving product quality, and enhancing efficiency through continuous improvement initiatives. GE’s lean approach has led to significant cost savings and improved competitiveness in the industrial sector.
4. Boeing:
Industry: Aerospace and Defense
Overview: Boeing has integrated lean principles into its production processes to streamline aircraft manufacturing. By adopting a just-in-time approach and minimizing work in progress, Boeing has achieved cost efficiencies and improved production flow. Lean practices are crucial in an industry where precision, reliability, and cost control are paramount.
5. Nike:
Industry: Sportswear and Apparel
Overview: Nike employs lean supply chain management to respond quickly to changing consumer preferences and trends. The company collaborates closely with suppliers, utilizes technology for demand forecasting, and emphasizes a flexible production model. Nike’s lean supply chain allows it to bring new products to market swiftly and efficiently.
6. H&M:
Industry: Fashion Retail
Overview: H&M embraces lean principles to maintain a fast and responsive Supply Chain Agility in the fashion industry. The company focuses on reducing lead times, minimizing excess inventory, and adopting sustainable practices. By staying agile and responsive, H&M can quickly adapt to evolving fashion trends and consumer demands.
These examples demonstrate that supply management strategies are not limited to a specific industry but can be successfully applied across diverse sectors.
Irrespective of the industry, the principles of waste reduction, continuous improvement, and customer-focused strategies remain fundamental to achieving operational excellence and competitive advantage.
Now, let’s address the frequently asked questions for supply chain management.
FAQs – Lean Supply Chain Management
1. What is the primary goal of lean supply chain management?
The primary goal is to eliminate waste, streamline processes, and create an efficient, customer-centric supply chain that responds to actual demand.
2. How do lean supply chains differ from traditional supply chain management?
These supply chain management focuses on waste elimination, continuous improvement, and value creation, while traditional approaches may prioritize cost-cutting without a holistic view of the entire supply chain.
3. Can lean principles be applied to all industries?
Yes, lean principles are adaptable and have been successfully implemented across various industries, including manufacturing, healthcare, and services.
4. Is technology integration essential for implementing lean supply chain management?
Technology, including data analytics and automation, enhances the effectiveness of supply chain management but isn’t a strict requirement. However, it significantly contributes to achieving optimal results.
5. How can businesses measure the success of their supply chain management?
Key performance indicators (KPIs) such as lead times, inventory turnover, and customer satisfaction metrics can be used to measure the success of lean supply chain management.
6. What tools are commonly used in lean supply chain management?
Common tools include Value Stream Mapping (VSM), 5S methodology, Kanban systems, root cause analysis (like the 5 Whys), and Total Productive Maintenance (TPM). These tools help identify inefficiencies and drive continuous improvement.
7. How does lean supply chain management support sustainability goals?
By reducing excess inventory, minimizing waste, and improving transportation efficiency, lean practices contribute to sustainability by lowering carbon emissions, reducing energy usage, and promoting resource optimization.
8. What role does employee training play in lean supply chains?
Employee training is crucial for successful implementation. Teams must be trained in lean principles, process improvement, and collaboration to actively contribute to continuous improvement and operational efficiency.
9. Can lean supply chains scale with growing businesses?
Yes, lean supply chains are designed for flexibility and scalability. With the right systems in place, businesses can adapt to increased demand, market changes, and expansion while maintaining efficiency.
Conclusion
In the pursuit of operational excellence, lean supply chain management emerges as a guiding philosophy, providing businesses with a roadmap to efficiency, customer satisfaction, and competitiveness. By embracing the principles, businesses can create a supply chain that not only meets the demands of today but also adapts to the challenges and opportunities of tomorrow.
If you are looking for a strategic way to thrive in a dynamic and evolving marketplace, look no further than Qodenext for a one-stop solution to all your supply chain problems.