In the world of managing supplies and products, “Safety Stock” is like a backup plan. Imagine you have a store, and you want to make sure you always have a popular item, like your best-selling toy. It is like having extra toys hidden away, just in case.
So, what is safety stock? It’s like a safety net for your inventory. It’s extra stuff you keep on hand to make sure you satisfy your customers if unexpected things happen. Maybe your supplier can’t deliver on time, or more people suddenly want that toy. It is there to save the day and keep your customers happy. In this easy-to-understand guide, we’ll explain why it is important, how to figure out how much you need, and why it matters for businesses.

What is Safety Stock?
It is a critical inventory management concept that acts as a buffer to mitigate the risk of stockouts due to unexpected fluctuations in demand or supply chain disruptions. It represents the extra inventory a company holds beyond its average demand to ensure product availability during uncertain times. Calculating it involves various factors, with the most common formula being:
Safety Stock = (Z-score for desired service level * Standard Deviation of Demand) + (Average Lead Time * Average Demand)
Here, the Z-score corresponds to the desired level of service, which quantifies the probability of meeting customer demand. It ensures that a company can fulfill customer orders even when actual demand exceeds expectations or when lead times are longer than anticipated.
Let’s explore the features of safety stock in detail:
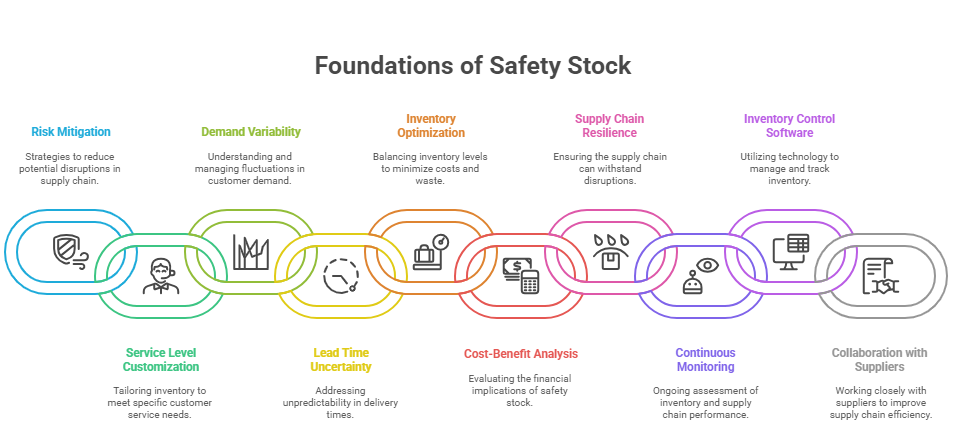
1. Risk Mitigation
This is primarily a risk management tool. It guards against the risk of stockouts, which can have severe consequences such as lost sales, dissatisfied customers, and damage to a company’s reputation. By holding extra inventory, a business hedges against the uncertainties of supply and demand, ensuring that it can meet customer needs even in adverse conditions.
2. Service Level Customization
Service level customization is about tailoring your inventory strategy to meet specific business objectives. For instance, a company may decide to maintain a 95% service level, meaning it aims to fulfill 95% of customer demand even during uncertain times. Safety stock levels are adjusted to achieve this target, allowing companies to align their inventory management with their strategic goals.
3. Demand Variability
One of the key drivers of safety stock is demand variability. This includes not only fluctuations in overall demand but also variations in the timing and size of customer orders. It accounts for seasonal demand spikes, sudden surges in popularity, or unpredictable market shifts, ensuring that products remain available when needed.
4. Lead Time Uncertainty
Lead time refers to the time it takes for a product to be replenished once an order is placed. It accommodates lead time uncertainty, which can be caused by factors such as supplier delays, shipping issues, or production disruptions. By building in a buffer, a company can handle these uncertainties without running out of stock.
5. Inventory Optimization
Effective safety stock management is part of a broader inventory optimization strategy. It involves finding the right balance between different inventory parameters, such as safety stock levels, reorder points, order quantities, and carrying costs. Striking this balance ensures that a company maintains adequate stock while keeping costs in check.
6. Cost-Benefit Analysis
Deciding on the appropriate level of safety stock requires a nuanced cost-benefit analysis. Holding too much of it ties up working capital and increases carrying costs, which can erode profitability. On the other hand, too little of it can result in lost sales, backorders, and disappointed customers. Businesses must weigh these costs against each other to determine the optimal safety stock level.
7. Supply Chain Resilience
Safety stock enhances supply chain resilience by providing a cushion against disruptions. Whether it’s a natural disaster, a sudden economic downturn, or unexpected geopolitical events, having it on hand allows a company to continue fulfilling orders even when the supply chain is under stress.
8. Continuous Monitoring
Safety stock isn’t a static value but an evolving one. It requires continuous monitoring and adjustment as conditions change. Businesses must regularly review their safety stock levels based on updated data, demand patterns, and lead time performance to ensure it remains effective.
9. Inventory Control Software
Modern inventory management often relies on sophisticated software solutions. These tools use historical data, demand forecasting algorithms, and real-time information to optimize safety stock levels. They help businesses strike the right balance between ensuring product availability and minimizing holding costs.
10. Collaboration with Suppliers
Effective safety stock management often involves collaboration with suppliers. By sharing information on demand forecasts, lead times, and inventory levels, businesses and suppliers can work together to reduce uncertainty and improve the accuracy of its calculations. This collaboration fosters a more efficient and reliable supply chain.
In essence, it is a dynamic and strategic tool that goes beyond mere stockpiling. It’s a key element of modern supply chain management, ensuring that businesses can navigate the complexities and uncertainties of today’s global marketplace while delivering consistent service to their customers.
Formula for Determining Average Maximum Safety Stock
This particular formula is most applicable in situations with short lead times, where long lead variables are not a significant factor. Its purpose is to compute the average maximum quantity of units required at any given point in time.
Safety Stock Formula for Variable Demand Scenarios
When dealing with scenarios where lead times are consistent but demand fluctuates, the safety stock formula tailored to variable demand comes into play.
Similar to the method used for calculating standard deviation, there are available online tools capable of accurately determining the average of a dataset and calculating the square root of a value. To compute the average delay, you can sum up the durations for supplier orders that exceeded the average delivery time and then divide this sum by the total number of orders that surpassed the average delivery duration.
Safety Stock Calculation for Variable Lead Times
This calculation applies in situations where demand remains stable, but lead times exhibit variability. The formula for this scenario is: Z x Average Sales x σLT. As previously mentioned, “Z” denotes the desired service level, while “σLT” represents the deviation in lead times (you can refer to the standard deviation formula for a more detailed explanation on how to compute this value).
How to Choose the Right Safety Stock Formula ?
Choosing the right safety stock formula is crucial for managing inventory effectively and ensuring you have enough stock on hand to meet customer demand while minimizing the costs associated with holding excess inventory.
There are several formulas to choose from, and the choice depends on various factors. In this in-depth and detailed explanation, we will explore these factors and guide you through the process of selecting the most suitable formula for your business needs.
Factors to Consider when Choosing a Safety Stock Formula
1. Demand Variability
Coefficient of Variation (CV)
If your demand patterns exhibit a consistent level of variability, you can use the coefficient of variation formula, which is the standard deviation of demand divided by the mean demand. A lower CV indicates more stable demand and may require less safety stock.
2. Lead Time Variability
Consider the variability in lead times for your suppliers. If lead times are consistent, it may affect the choice of formula.
3. Service Level Requirement
Determine the level of service you want to provide to your customers. A higher service level, such as 95% or 99%, will require more safety stock to ensure you rarely run out of stock.
4. Lead Time
The duration it takes for a supplier to deliver goods to your inventory plays a significant role. If lead times are longer and less predictable, you may need more safety stock.
5. Cost Constraints
Consider the cost of carrying inventory. Holding excess safety stock incurs carrying costs, such as storage, insurance, and capital costs. Balancing this against the cost of stockouts (lost sales and potential customer dissatisfaction) is critical.
6. Forecast Accuracy
The accuracy of your demand forecasts impacts the choice of formula. If your forecasts are highly accurate, you may need less safety stock to account for demand variability.
7. Demand Patterns
The nature of your demand patterns, such as seasonality or trend, can influence your choice of the formula. Different formulas may be more appropriate for specific patterns.
8. Supplier Reliability
Assess the reliability of your suppliers. If they consistently meet lead time commitments, it may reduce the need for excessive safety stock.
Now, let’s discuss some common formulas and when to use them:
Common Safety Stock Formulas and When to Use Them
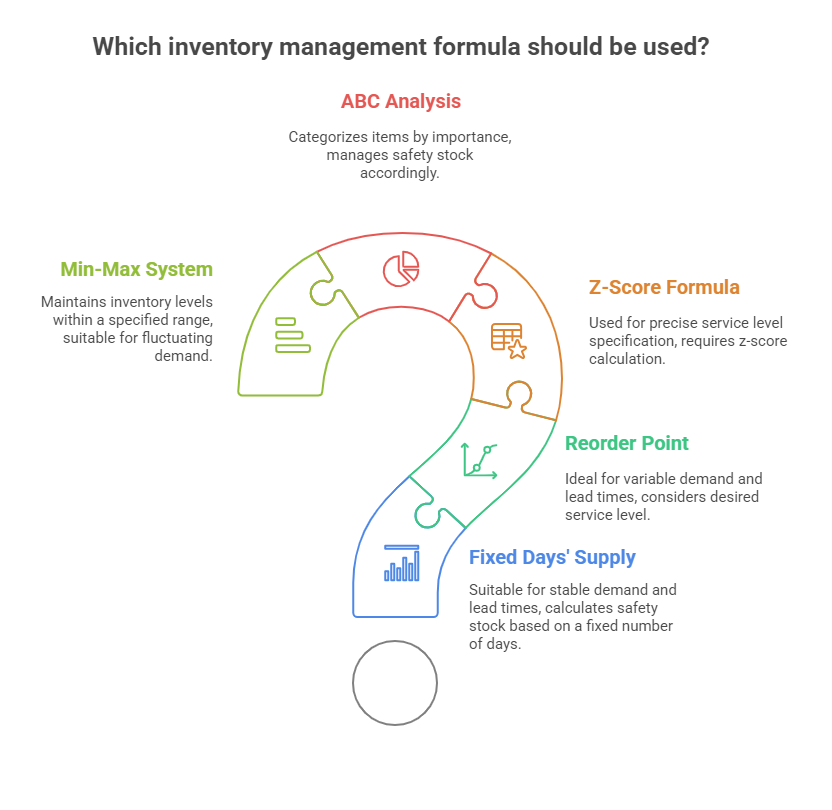
1. Fixed Days’ Supply (FDS)
Suitable for businesses with relatively stable demand and lead times. Calculates safety stock as the demand rate multiplied by a fixed number of days of supply (e.g., 7 days).
2. Reorder Point (ROP)
Ideal for businesses with variable demand and lead times.
Formula: ROP = (Demand during lead time) + Safety Stock.
It is determined based on desired service level and demand/lead time variability.
3. Z-Score Formula
Utilized when you want to specify a precise service level. Requires the calculation of z-scores and a lookup table to find the corresponding service level.
4. ABC Analysis
Useful for categorizing items by importance and managing safety stock accordingly.
High-value items may require higher stock levels.
5. Min-Max Inventory System
Appropriate for items with variable demand and lead times. Sets a minimum and maximum inventory level, reordering when stock reaches the minimum.
Choosing the right safety stock formula depends on a combination of factors specific to your business. Evaluate the factors mentioned above, including demand variability, service level requirements, lead time, cost constraints, forecast accuracy, demand patterns, and supplier reliability.
A combination of formulas may also be necessary for different products within your inventory. Regularly reviewing and adjusting your its levels is essential to optimize inventory management and meet customer demands efficiently while minimizing costs.
Why Is It Important?
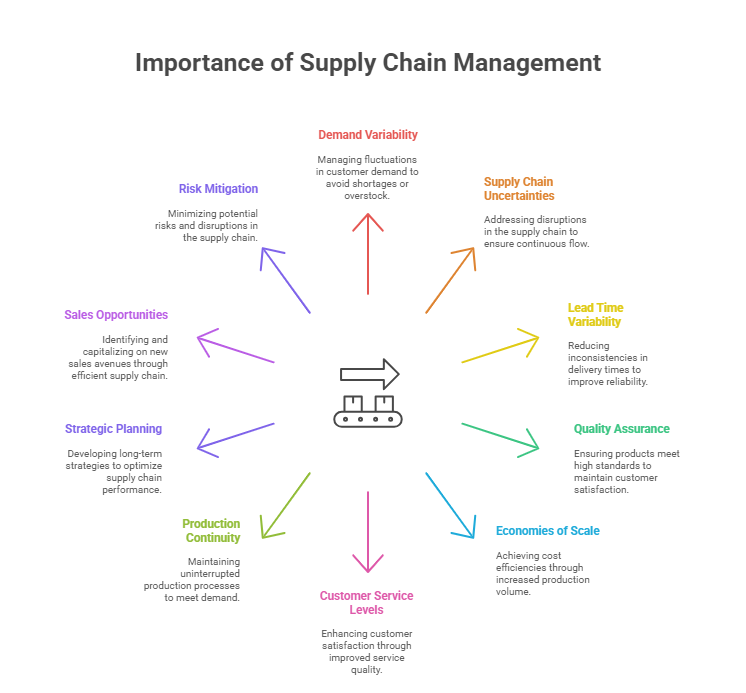
1. Demand Variability
Customer demand is rarely constant and can fluctuate due to various factors such as seasonality, market trends, promotions, or even unexpected events like a sudden surge in demand due to a viral trend on social media. Without it, businesses are at risk of stockouts when demand unexpectedly exceeds the available inventory. This can lead to lost sales, dissatisfied customers, and damage to the company’s reputation.
2. Supply Chain Uncertainties
Supply chain disruptions are commonplace and can occur due to natural disasters, transportation issues, labor strikes, or problems with suppliers. It acts as a cushion to absorb the impact of these disruptions. It ensures that businesses can continue their operations smoothly, even when faced with supply chain challenges, thereby maintaining customer satisfaction and business continuity.
3. Lead Time Variability
Suppliers may not always deliver goods on time as promised. Variability in lead times can be due to factors like shipping delays, customs clearance, or production issues at the supplier’s end. This stock bridges the gap between when an order is placed and when it is received. It prevents stock outs caused by delays in the supply chain, allowing businesses to fulfill customer orders on schedule.
4. Quality Assurance
Detailed Explanation: In industries where product quality is paramount, not all incoming inventory may meet the required standards. Some items might be subpar or defective.
Safety stock allows businesses to carefully select products from their own inventory, ensuring that only high-quality items are sent to customers. This protects the company’s reputation and reduces the risk of customer complaints or returns.
5. Economies of Scale
Ordering in larger quantities often results in lower per-unit costs due to bulk purchasing discounts, reduced shipping costs, and more efficient handling. Safety stock enables companies to take advantage of these cost savings without the fear of running out of inventory. This ensures cost-efficient operations while maintaining adequate stock levels.
6. Customer Service Levels
Meeting service level agreements and customer expectations is crucial for customer satisfaction. Stockouts or delayed deliveries can lead to customer dissatisfaction.
Safety stock prevents backorders and allows businesses to fulfill customer orders promptly. This helps maintain high service levels, enhances customer satisfaction, and fosters customer loyalty.
7. Production Continuity
In manufacturing, disruptions can occur due to equipment breakdowns, maintenance, or sudden changes in demand for components or raw materials. Safety stock ensures that production can continue even in the face of such disruptions, preventing costly downtime and ensuring a consistent supply of finished products to customers.
8. Strategic Planning
Safety stock provides flexibility for long-term strategic planning. It allows businesses to launch new products, enter new markets, or adjust production levels without the risk of immediate stockouts. This strategic flexibility enables businesses to adapt to changing market conditions and seize opportunities for growth without being constrained by inventory shortages.
9. Sales Opportunities
Unplanned sales opportunities, such as large orders from new customers or unexpected market surges, can arise. Safety stock enables businesses to respond quickly to these opportunities, fulfilling orders without delays. This can lead to increased revenue and market share.
10. Risk Mitigation
Safety stock helps mitigate financial risks associated with stockouts, excess carrying costs, and customer dissatisfaction. By reducing the impact of uncertainties in supply and demand, safety stock ensures that businesses can operate more reliably and withstand unexpected challenges, ultimately contributing to their long-term stability and success.
In summary, safety stock serves as a multifaceted insurance policy for businesses, protecting them against a wide range of operational risks and uncertainties while facilitating strategic growth and ensuring customer satisfaction. Its importance is deeply rooted in its ability to provide stability, resilience, and agility in the complex world of inventory management.
Challenges Associated with Safety Stock in Inventory Management
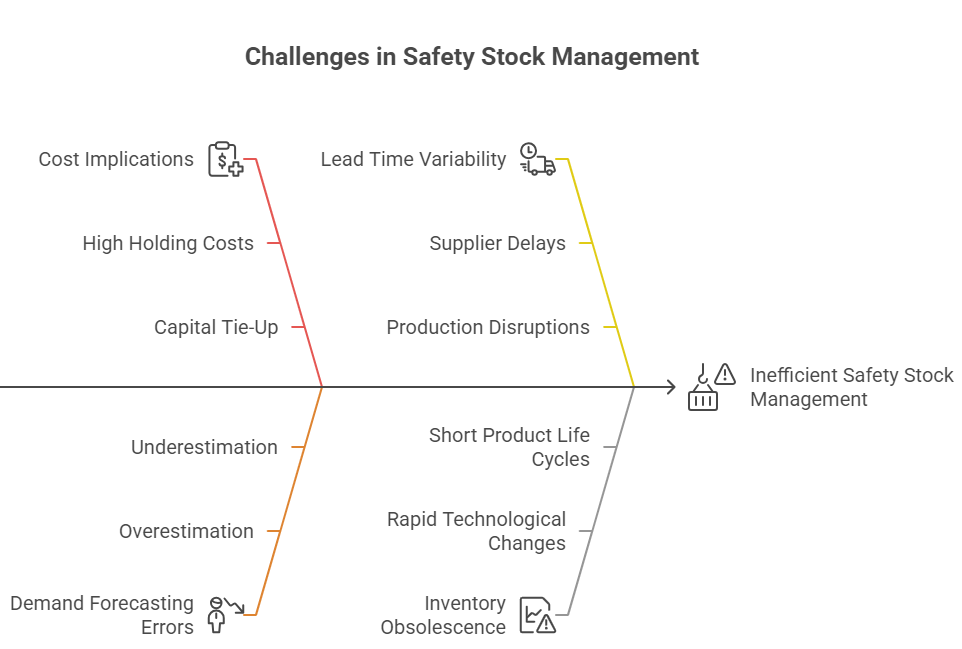
Safety stock in inventory management is a crucial buffer of extra inventory held to mitigate uncertainties in demand, supply chain disruptions, and lead time variability. While it plays a pivotal role in ensuring product availability and customer satisfaction, several challenges are associated with its management:
1. Cost Implications
One of the primary challenges of safety stock management is the cost involved. Maintaining surplus inventory ties up working capital and incurs carrying costs, including storage fees, insurance, and depreciation. Striking the right balance between having enough safety stock to meet demand fluctuations and minimizing holding costs is a delicate and ongoing challenge.
2. Demand Forecasting Errors
Inaccurate demand forecasting is a common challenge that can greatly affect safety stock levels. If forecasts are too optimistic, a company might carry excessive safety stock, resulting in high holding costs and potential obsolescence. Conversely, underestimating demand can lead to stockouts, customer dissatisfaction, and lost sales. Accurate demand forecasting becomes increasingly challenging when dealing with factors such as seasonal variations, market volatility, or abrupt shifts in consumer preferences.
3. Lead Time Variability
Safety stock is primarily designed to buffer against uncertainties in lead times, which can be caused by factors like supplier delays, production disruptions, or transportation issues. When lead times become unpredictable, maintaining the appropriate level of stock becomes more challenging. Over-relying on it to compensate for lead time variability can lead to increased holding costs and operational inefficiencies.
4. Inventory Obsolescence
Safety stock is not immune to the risk of obsolescence. Holding excess inventory for an extended period can result in products becoming outdated, especially in industries characterized by rapid technological advancements or short product life cycles. Managing obsolescence risk while still safeguarding against supply chain disruptions requires a delicate balancing act.
5. Storage Space Constraints
Businesses with limited storage capacity face an additional challenge when managing safety stock. Ensuring that there is enough space to store it while still accommodating regular inventory can be demanding. This may lead to the need for costly storage expansion or optimization solutions.
6. Supplier Reliability
The reliability of suppliers can significantly impact safety stock management. Supplier performance issues, such as inconsistent quality, delivery delays, or sudden disruptions, can necessitate larger safety stock levels to compensate for potential supply interruptions. Collaborative efforts with suppliers to improve reliability and communication are crucial in addressing this challenge.
7. Economic Order Quantity (EOQ) vs. Safety Stock
Balancing the use of safety stock with the economic order quantity (EOQ) model is a complex challenge. EOQ seeks to minimize costs by determining the optimal order quantity, while safety stock serves as a buffer against uncertainties. Striking the right equilibrium between these two inventory management approaches is essential for cost-effectiveness and operational efficiency.
8. Demand Variability
Beyond forecasting errors, the inherent variability in customer demand can pose a significant challenge. In industries with highly unpredictable demand patterns or those susceptible to external shocks (e.g., fashion, electronics, or healthcare during a pandemic), determining the appropriate level of safety stock becomes exceptionally tricky. Organizations need to develop adaptive strategies that can respond swiftly to unforeseen changes in demand without overcommitting resources to safety stock.
9. Inventory Turnover and Aging
A challenge often overlooked is the potential impact of safety stock on overall inventory turnover and aging. High levels of safety stock can slow down inventory turnover, resulting in cash flow constraints and potential write-offs due to expired or obsolete products. Companies must strike a balance between safeguarding against disruptions and ensuring their inventory remains fresh and saleable.
10. Multi-Echelon Supply Chains
In complex supply chains with multiple tiers or echelons, managing safety stock becomes more intricate. Each tier may have its own safety stock requirements and lead time variations. Coordinating safety stock levels throughout the supply chain to optimize overall performance can be challenging due to information asymmetry, communication barriers, and conflicting interests. Collaboration and data-sharing among supply chain partners are essential to addressing this challenge effectively.
Managing this stock in inventory management is a multifaceted task that involves optimizing costs, accurately forecasting demand, navigating lead time variability, and addressing issues related to storage space, supplier reliability, and the EOQ model. A well-thought-out approach to these challenges is essential for ensuring efficient inventory management and sustaining customer satisfaction.
Conclusion
Safety stock is a critical component of inventory management, serving as a buffer against unexpected fluctuations in demand or supply chain disruptions. It acts as an insurance policy to ensure businesses can meet customer demands even during unpredictable scenarios. By maintaining an optimal safety inventory level, companies can strike a balance between cost efficiency and customer satisfaction.
In conclusion, understanding and effectively managing this stock is paramount for businesses aiming to optimize their inventory control processes. Now, if you’re looking for a comprehensive solution to streamline your inventory management and calculate the right stock levels, Qodenext offers cutting-edge software and expertise. Click here to schedule a demo and take your inventory management to the next level with Qodenext. Don’t miss the chance to enhance your operational efficiency and customer service today!
Frequently Asked Questions (FAQ’s)
1. What do you mean by safety stock?
Safety stock is extra inventory kept to prevent running out if demand is higher than expected or if supplies are delayed.
2. What is the maximum stock level?
There is no term “safety stock EOQ.” EOQ is the best order size to minimize costs, and safety stock is extra stock for emergencies—they are separate but related concepts.
3. What is the safety stock EOQ?
“Safe stock” is just another way to say safety stock—extra inventory to avoid shortages.
4. What is meant by safe stock?
Safety stock = (Maximum daily usage × Maximum lead time) – (Average daily usage × Average lead time)
5. What is the formula for safety stock?
ROP (Reorder Point): The inventory level at which you should order more to avoid running out.
EOQ (Economic Order Quantity): The best order size to minimize total inventory costs.
6. What is ROP and EOQ?
ROP = (Average daily demand × Lead time) + Safety stock
7. What is the ROP formula?
EOQ = √[(2 × Annual demand × Order cost) ÷ Holding cost per unit per year]
8. What is the formula for EOQ?
Maximum stock level is the most you should ever have in stock. Formula: Maximum stock level = Reorder point + Reorder quantity – (Minimum demand × Minimum lead time)
(Or, simply: the highest amount you allow before it becomes wasteful or costly.)