Capacity planning in operations management is a critical facet of optimizing organizational efficiency. It involves forecasting, managing, and aligning an entity’s production capabilities with demand, ensuring resources are utilized optimally. In this blog, we delve into the intricacies of capacity planning, shedding light on its significance in maintaining a competitive edge.
We explore strategies encompassing demand forecasting, resource allocation, and technology integration. From the intricacies of lean production to the versatility of outsourcing, we will dissect various approaches to enhance capacity planning. In an ever-evolving business landscape, mastering capacity planning is paramount for businesses seeking to stay agile and thrive.

What Is Capacity Training in Operations Management?
Capacity training in operations management is all about giving people, teams, and companies the right skills and know-how to run their production or service operations better. This helps ensure that a company’s resources, like its people, machines, and technology, are used well to meet customer needs, save money, and uphold quality standards. Now, let’s look at the main aspects of capacity training more closely:
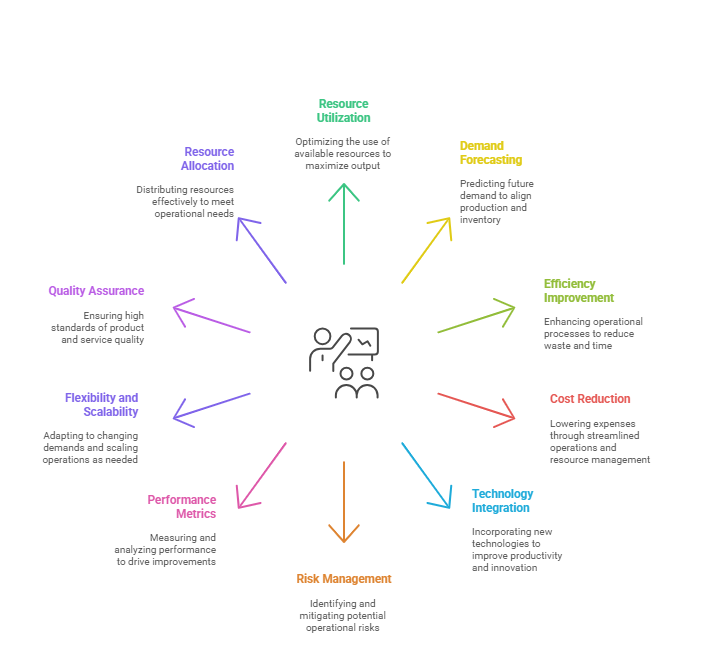
1. Resource Utilization
Resource optimization is about ensuring that personnel, machinery, and facilities are used efficiently. It involves methods like scheduling, load balancing, and cross-training to make the most of available resources.
2. Demand Forecasting
This feature involves using historical data and market analysis to predict customer demand accurately. Demand forecasting allows businesses to adjust their capacity plans to meet future requirements, reducing the risk of overproduction or shortages.
3. Efficiency Improvement
Efficiency improvement entails examining and optimizing every step in a process. Techniques such as Lean Six Sigma are often taught in capacity training to eliminate waste, reduce cycle times, and enhance process flow.
4. Cost Reduction
Cost reduction involves identifying areas where resources can be conserved without compromising quality. This may include reducing energy consumption, minimizing material waste, or optimizing labor utilization.
5. Technology Integration
Capacity training covers the integration of technology solutions like Enterprise Resource Planning (ERP) systems, automation, and IoT devices to enhance production processes, monitor capacity in real-time, and improve decision-making.
6. Risk Management
In-depth risk management training teaches organizations to identify potential capacity-related risks, such as supply chain disruptions or sudden spikes in demand, and develop contingency plans to mitigate these risks.
7. Performance Metrics
Performance metrics, like Overall Equipment Effectiveness (OEE) and Capacity Utilization Rate, are introduced to track the efficiency and effectiveness of capacity utilization. These metrics provide valuable insights for continuous improvement.
8. Flexibility and Scalability
Capacity training emphasizes the need for adaptable capacity plans. This means having the ability to scale up or down in response to changing market conditions, allowing organizations to meet customer demand while avoiding overinvestment in fixed assets.
9. Quality Assurance
Ensuring consistent quality is crucial. Capacity training often includes quality control methodologies like Total Quality Management (TQM) to maintain high standards during capacity utilization.
10. Resource Allocation
Effective resource allocation involves aligning resources with strategic goals. Capacity training helps organizations prioritize resource allocation decisions based on factors such as customer demand, product/service profitability, and market trends.
By mastering these features through capacity training, organizations can achieve better control over their operations, respond swiftly to market dynamics, and ultimately enhance their competitiveness in the ever-evolving business landscape.
Steps in Capacity Planning in Operations
Capacity planning is a crucial aspect of operations management that involves optimizing an organization’s ability to produce goods or provide services efficiently to meet customer demand. The process of capacity planning typically involves several key steps:
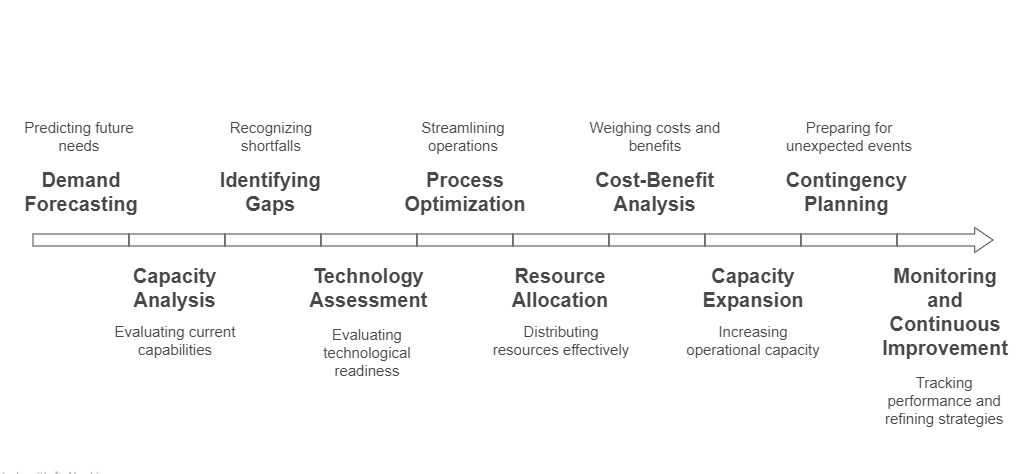
1. Demand Forecasting
Demand forecasting involves meticulous analysis of historical data, market trends, customer behavior, and other relevant factors. Various forecasting methods, such as quantitative and qualitative, are employed to predict future demand accurately. This step helps organizations understand when and how much capacity they need to fulfil customer orders.
2. Capacity Analysis
Capacity analysis comprehensively examines an organization’s current resources and capabilities. This includes evaluating the workforce’s production machinery, equipment, facilities, and skills. It also involves assessing the capacity utilization rates to understand how efficiently resources are utilized.
3. Identifying Gaps
Comparing the forecasted demand with the existing capacity helps pinpoint gaps in capability. An excess capacity gap indicates underutilization, meaning resources need to be fully optimized, which can lead to increased costs. Conversely, an insufficient capacity gap signifies overutilization, where the existing capacity cannot meet the forecasted demand, potentially resulting in missed opportunities and dissatisfied customers.
4. Technology Assessment
Assessing the technology is critical. Organizations must determine if their current technology can efficiently support the forecasted demand. This involves evaluating the machinery and equipment’s age, maintenance requirements, and capabilities. If technology needs to be updated or improved, investing in upgrades or new equipment may be necessary to align with capacity needs.
5. Process Optimization
Process optimization focuses on improving the efficiency of existing operations. This step involves analyzing each stage of production or service delivery to identify bottlenecks, redundancies, and areas for improvement. Organizations can maximize their existing capacity without significant capital investments by streamlining processes and eliminating inefficiencies.
6. Resource Allocation
Organizations must allocate resources strategically once capacity gaps are identified. This may involve redistributing labor, adjusting work schedules, or reallocating equipment to balance capacity with demand. Effective resource allocation ensures that available power is utilized efficiently.
7. Cost-Benefit Analysis
This analysis helps organizations evaluate the financial implications of various capacity adjustments, such as expanding facilities, hiring additional staff, or investing in technology upgrades. It ensures that capacity decisions align with budget constraints and long-term profitability goals.
8. Capacity Expansion
Organizations may need to consider capacity expansion if the demand forecast indicates a sustained and significant capacity shortfall. This can involve building new facilities, purchasing additional machinery, or scaling up operations. Expansion decisions should be based on a thorough analysis of the forecasted demand and cost considerations.
9. Contingency Planning
Capacity planning should also account for unexpected events, such as fluctuations in demand or equipment breakdowns. Contingency plans should be developed to address these contingencies, ensuring operations can continue smoothly even in adverse circumstances.
10. Monitoring and Continuous Improvement
Capacity planning is an ongoing process. Organizations should continuously monitor demand, capacity utilization, and the effectiveness of capacity adjustments. Regular reviews and adjustments allow agility in responding to changing market conditions and customer demands. Continuous improvement efforts help optimize capacity planning processes over time.
Incorporating these steps into capacity planning enables organizations to effectively align their resources with demand, optimize operations, and maintain competitiveness in the market.
Types of Capacity Planning in Manufacturing Industry
Capacity planning is a crucial aspect of operations in the manufacturing industry, as it involves determining the optimal level of production capability to meet current and future demands efficiently. Capacity planning encompasses a variety of approaches and techniques, each tailored to specific needs and circumstances. Here, we delve into the top types of capacity planning in the manufacturing industry:
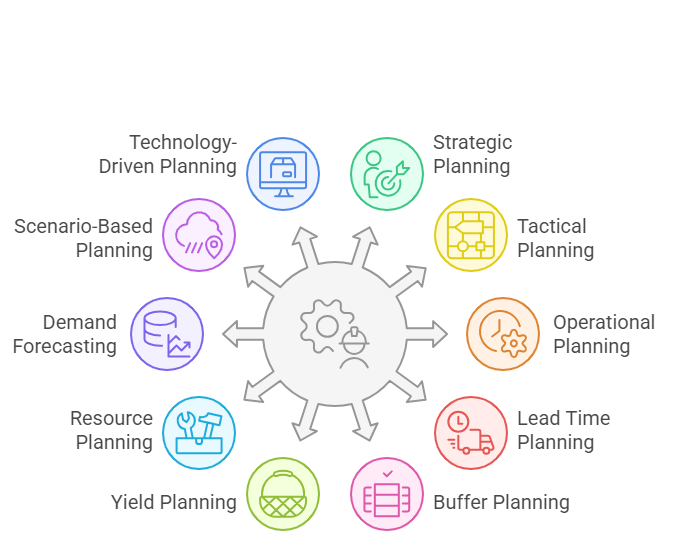
1. Strategic Capacity Planning
Strategic capacity planning involves long-term decisions regarding expanding or contracting production facilities. It considers market growth, competitive positioning, and overall business strategy. This type of planning might involve constructing new factories, acquiring additional equipment, or investing in research and development to increase production capabilities. The goal is to align the organization’s capacity with anticipated future demand while minimizing long-term risks and maximizing profitability.
2. Tactical Capacity Planning
Capacity planning deals with medium-term decisions to balance capacity with changing demand patterns. Manufacturers often use strategies like hiring temporary workers, adjusting shifts, or outsourcing production to adapt to fluctuations in demand. This approach enables companies to maintain a competitive edge by quickly responding to market dynamics without significant long-term commitments.
3. Operational Capacity Planning
Operational capacity planning addresses managing resources, including machinery, labor, and materials. It focuses on optimizing production schedules, minimizing downtime, and ensuring daily production targets are met efficiently. This type of planning is critical for maintaining a smooth workflow and delivering products on time.
4. Lead Time Capacity Planning
Lead time capacity planning emphasizes reducing the time it takes to transform raw materials into finished products. Manufacturers achieve this by streamlining processes, minimizing bottlenecks, and improving production efficiency. Shorter lead times enhance customer satisfaction and allow companies to respond more effectively to changing market conditions.
5. Buffer Capacity Planning
Buffer capacity planning involves creating a cushion of extra capacity to handle unforeseen disruptions or demand spikes. Manufacturers may maintain reserve equipment, cross-train workers, or establish backup suppliers to ensure continuity in production even when faced with unexpected challenges, such as equipment breakdowns or supply chain disruptions.
6. Yield Capacity Planning
Yield capacity planning maximizes output while minimizing waste and defects. This involves process improvements, quality control measures, and lean manufacturing techniques to increase the number of usable products produced with existing resources. Higher yields contribute to cost savings and improved overall production efficiency.
7. Resource Capacity Planning
Resource capacity planning involves optimizing the allocation of resources, including machinery, labor, and materials, to ensure that production runs smoothly. This entails monitoring resource utilization, adjusting production schedules, and identifying resource-sharing or consolidation opportunities to minimize underutilization or overuse.
8. Demand Forecasting Capacity Planning
Demand forecasting capacity planning relies on accurate sales predictions to align capacity with anticipated customer orders. Manufacturers use historical data, market trends, and statistical models to estimate future demand. This approach helps prevent overproduction or underproduction, reducing excess inventory or missed sales opportunities.
9. Scenario-Based Capacity Planning
Scenario-based capacity planning involves creating contingency plans for various market conditions and uncertainties. Manufacturers analyze different scenarios, such as economic downturns or supply chain disruptions, to develop flexible capacity strategies that adapt to changing circumstances.
10. Technology-Driven Capacity Planning
Modern manufacturing capacity planning has evolved by integrating cutting-edge technologies like IoT sensors, AI algorithms, and advanced data analytics. These innovative tools have revolutionized the industry by enabling real-time production data monitoring, allowing manufacturers to optimize their capacity continually. This flexibility will help them to swiftly adjust production processes, schedules, and resource allocation in response to dynamic conditions, ultimately leading to heightened efficiency and substantial cost savings.
Each of these capacity planning approaches plays a pivotal role in ensuring manufacturing operations’ ongoing competitiveness, adaptability, and responsiveness within an ever-evolving industry landscape. When combined, these strategic methodologies empower manufacturers to delicately balance efficiency, flexibility, and cost-effectiveness delicately, propelling them to thrive in the modern manufacturing ecosystem.
Advantages of Capacity Planning in Operations Management
Capacity planning is a critical component of operations management, playing a pivotal role in optimizing a company’s performance and ensuring its ability to meet customer demands effectively. By strategically assessing and managing resources, capacity planning enables businesses to maximize their efficiency and profitability.
The advantages of capacity planning are multifaceted, encompassing enhanced resource allocation, improved cost control, and increased customer satisfaction. Now, let’s delve deeper into the top five types of capacity planning:
1. Lead Capacity Planning
This approach involves increasing production capacity proactively, ahead of anticipated demand spikes. It ensures that a company can readily meet customer needs, even during peak periods, minimizing the risk of stockouts or long lead times.
2. Lag Capacity Planning
Lag capacity planning focuses on adjusting capacity levels after recognizing demand fluctuations. While it may entail higher costs during peak times, it can be a more cost-effective strategy when demand is stable, as it avoids overinvestment in resources.
3. Match Capacity Planning
This method aims to align capacity closely with actual demand, balancing lead and lag strategies. It involves flexible production schedules and adapting quickly to changing market conditions.
4. Strategic Capacity Planning
Strategic capacity planning takes a long-term perspective, considering factors such as market growth, technology advancements, and competitive positioning. It guides significant investments in infrastructure and facilities.
5. Operational Capacity Planning
This type deals with day-to-day resource allocation, ensuring that resources are utilized efficiently in the short term. It helps maintain smooth operations and prevents underutilization or overuse of resources.
Incorporating these various types of capacity planning into operations management enables businesses to optimize their resource utilization, respond effectively to market dynamics, and ultimately enhance their competitiveness and customer satisfaction.
Conclusion
Capacity planning in operations management is essential for aligning resources with demand efficiently. It involves forecasting, resource allocation, and strategic decision-making to meet customer needs while optimizing costs. Effective capacity planning ensures smooth operations and customer satisfaction.
To streamline this complex process, Qodenext offers advanced operations management software. Real-time data analysis and forecasting tools empower businesses to make informed decisions, helping them optimize capacity planning. Qodenext is the key to maintaining operational excellence, ensuring organizations are prepared for dynamic market challenges and positioned for sustainable success.
FAQ’s
1. What are the five steps of capacity planning?
The five main steps of capacity planning typically include: forecasting future demand, assessing current capacity, identifying capacity gaps, developing solutions to address those gaps, and monitoring and adjusting the plan as needed. These steps ensure that organizations can meet anticipated demand by balancing available resources with projected needs, allowing for proactive management of workforce, equipment, and facilities.
2. What is the main objective of capacity planning?
The main objective of capacity planning is to ensure that an organization has the right amount of resources such as labor, machinery, and materials available at the right time to meet future demand. This helps businesses operate efficiently, minimize costs, avoid shortages or excesses, and maintain high service levels for customers.
3. What is a capacity planning example?
An example of capacity planning is a manufacturing company that forecasts increased demand for its products during the holiday season. The company analyzes its current production capabilities, identifies a gap between expected demand and current capacity, and then decides to hire temporary workers and run extra shifts to meet the surge in orders. This ensures that customer demand is met without overburdening existing resources.
4. What are the three types of capacity planning?
The three main types of capacity planning are lead strategy, lag strategy, and match strategy. Lead strategy involves increasing capacity in anticipation of higher demand. Lag strategy means increasing capacity only after demand has risen. Match strategy is a balanced approach, where capacity is adjusted incrementally based on actual demand and forecasts.
5. What is meant by capacity planning?
Capacity planning is the process of determining how much production or service capacity an organization needs to meet future demand. It involves analyzing current resources, forecasting future needs, and making adjustments to ensure that the right resources are available at the right time to support business operations and customer requirements.
6. What is the formula for capacity planning?
While there is no single universal formula for capacity planning, a commonly used calculation is:Required Capacity=Forecasted Demand×TimeRequired Capacity=Forecasted Demand×TimeThese
formulas help organizations estimate how much capacity is needed to meet expected demand within a specific period. Actual formulas may vary depending on the context and specific business needs.
7. How does capacity planning impact business profitability?
Effective capacity planning helps businesses optimize resource utilization, reduce waste, and meet customer demand without incurring unnecessary costs. By aligning production capacity with forecasted demand, companies can prevent overproduction, minimize inventory holding costs, and avoid lost sales due to stockouts—all of which directly contribute to higher profitability.
8. What are the common challenges in capacity planning?
Common challenges include inaccurate demand forecasting, sudden changes in market conditions, supply chain disruptions, lack of real-time data, and resource constraints. Overcoming these challenges often requires using advanced analytics, maintaining flexible operations, and having contingency plans in place.
9. How often should capacity planning be done?
Capacity planning should be reviewed regularly—often quarterly or annually—depending on the industry and demand volatility. Businesses in fast-changing markets may need to review their capacity plans more frequently to stay aligned with market trends and operational requirements.
10. What tools or software are used for capacity planning?
Popular tools for capacity planning include Microsoft Excel (for smaller operations), ERP systems like SAP and Oracle NetSuite, and specialized capacity planning software such as Capacity Planning Tool by Smartsheet, Kinaxis, and Anaplan. These tools help automate data collection, forecast demand more accurately, and simulate different scenarios to support decision-making.