Automation is on top of the mind for every manufacturer today. Given the challenges they are facing on a day-to-day basis on the shop floor, in their warehouses, and across their supply chains, automation delivers several promises in terms of error (and effort) reduction and efficiency improvements. But adoption of the best technology is not going to guarantee the best results; in fact, automation technology adoption cannot, and should not, be the starting point of the automation journey in manufacturing.
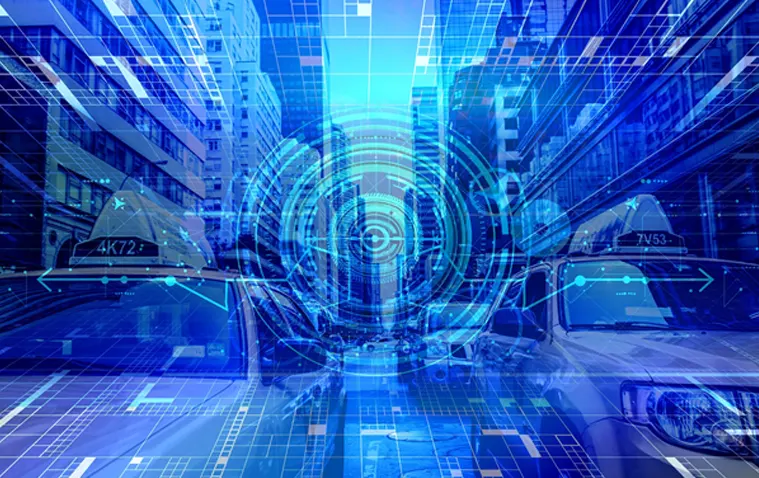
Here's how you can ensure successful automation in manufacturing
Ensuring successful automation in manufacturing tops the bucket list of every manufacturer today. Unfortunately, there is no single answer or solution to this. At the same time, it is extremely critical to note that just procuring the best automation technology is certainly not the answer. Although investing in the right automation technology plays a huge role in implementation success, there are numerous other factors to keep in mind while embarking on the journey.
Here are 8 questions you need to ask yourself before you kick-start your manufacturing automation journey:
1. Do you have a strong business case for automation?
Automation has now become a global phenomenon, with companies big and small embracing technology to improve production and distribution efficiency. But just because everyone has begun their automation journey doesn’t mean you have to, too. You need to embrace the technology only if it makes sense for your business. Do you have a strong business case for automation? Is your workforce spending too much time procuring raw materials? Are you facing too many errors in invoice processing? Is inventory management becoming a big nuisance for your business?
2. Is the process being automated stable?
When you embrace automation, you need to ensure the process you’ve chosen is suited for automation. Since manufacturing processes have too many unpredictable factors associated with them, to achieve maximum productivity through automation, you must make your processes as stable and predictable as possible. Also, it makes sense to start automating in phases, rather than take a Big Bang approach, and focus on automating manageable tasks – to witness a substantial increase in your turnover.
3. Do you have the buy-in from the leadership team and other relevant stakeholders?
Wanting to embrace automation is one thing; having the required approvals and budgets is a completely different ball game. In addition to having a strong business case for automation, you also need to have the required buy-in from the leadership team as well as other relevant stakeholders. Such support not only ensures you have the required budget for procuring and implementing modern tools and platforms; it also helps in receiving leadership oversight if at all, your automation project runs into problems.
4. Do you have a plan to upskill and reskill the workforce?
Doesn’t end at implementing modern technology; you also need skilled resources to drive innovation and growth. To ensure you get maximum returns from your automation investment, you need to have a robust plan in place for upskilling and/or reskilling your existing workforce and make sure your workforce has the skills and capabilities to work their way around these new tools and systems. Educating and upskilling your employees on how to work alongside the technology can lead to a perfect balance between the capabilities of your workforce and those that are brought about by automation.
5. What is your change management plan?
Automation is bound to bring about several changes in how your manufacturing business operates. To cope with all these changes, you need to have a robust change management plan in place and be equipped to successfully and seamlessly deploy the technology to drive transformation. Demonstrating the benefits of the technology and listing out all the possible changes that will be brought about by automation will aid in aligning your departments, while also ensuring your workforce knows how to deal with all the disruptions.
6. Do you have the right team and supplier to support the automation implementation?
The success of your automation strategy also depends largely on the team in charge of the implementation. Since the technology requires a deep understanding of the technology, challenges to avoid, and best practices to embrace, setting up a qualified team of experts is critical to success. And if you think you lack the skillset needed, you must engage with a qualified and competent partner with years of experience in successfully carrying out similar automation projects.
7. Have you defined the KPIs to monitor?
Additionally, you also need to define the KPIs that can help you monitor and measure the progress and success of your automation project and evaluate how seamlessly it realises larger goals and objectives. Since you cannot manage what you do not measure, collecting and measuring data via KPIs lies at the heart of every automation project. Such measurement can not only throw light on the benefits you are realising from the technology; it can also help you stick to project deadlines and costs and mitigate risks in time while ensuring the quality of deliverables.
8. Do you have sufficient budgets allocated for supporting components?
Another critical aspect that you need to keep in mind when you begin your manufacturing automation journey is to have the required budget for the project. Since any automation budget doesn’t just comprise the cost of the automation tool, but also supporting components like sensors, conveyors, electric actuators, and software solutions as well as costs of maintaining, supporting, and managing the project or the costs of an automation partner, it is important you have necessary investments in place for a successful expedition.
In the world of manufacturing, automation enables companies to not only save time and improve accuracy but also achieve more with less, drive efforts in their strategic initiatives, and focus on more complex and meaningful work – than be bogged down by the mundaneness of repetitive tasks. But just implementing the latest or best automation technology does not guarantee success. You need to have a comprehensive and holistic approach to automation – instead of a point solution approach – to deliver rich results and returns.